Continuity and reliability are essential advantages a plant or system can have. So, in this case, failures should be predicted and also you have to prepare a swift solution or actions for such a situation.
Today we are going to have a simple common situation that is presented in most plants that contain some critical conveyors that cannot be stopped for any reason.
Explaining Conveyor Operation
Here we have a very simple conveyor that is a part of a whole system.
The main problem is if this conveyor stopped the whole factory and the system operation will stop, that means increasing system downtime, and by its role that would cost you a lot of money.
To avoid such a situation, we are using a backup motor for some critical conveyors in some plants, all we need a backup motor that is connected with the same motion axe of the conveyor motor. As shown in Fig. (1)
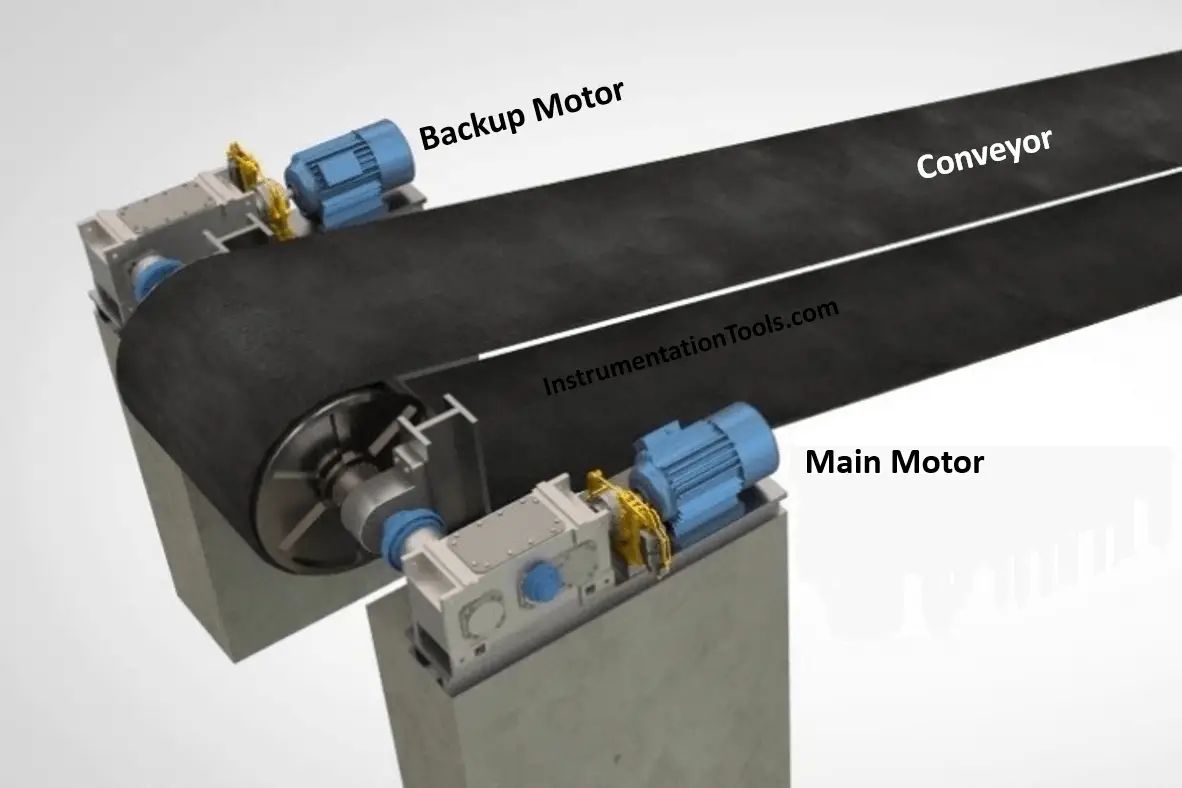
In case of failure of the main motor, the backup motor will work instead of it.
Register Siemens PLC Course: Click Here
PLC Ladder Diagram using Siemens TIA Portal
We discussed the PLC ladder logic networks designed in the Siemens Tia portal.
Network 1: Controlling the Main Motor
Here we have the first network that is shown in Fig. (2) as we can see by clicking on (I0.0) we can start the main motor.
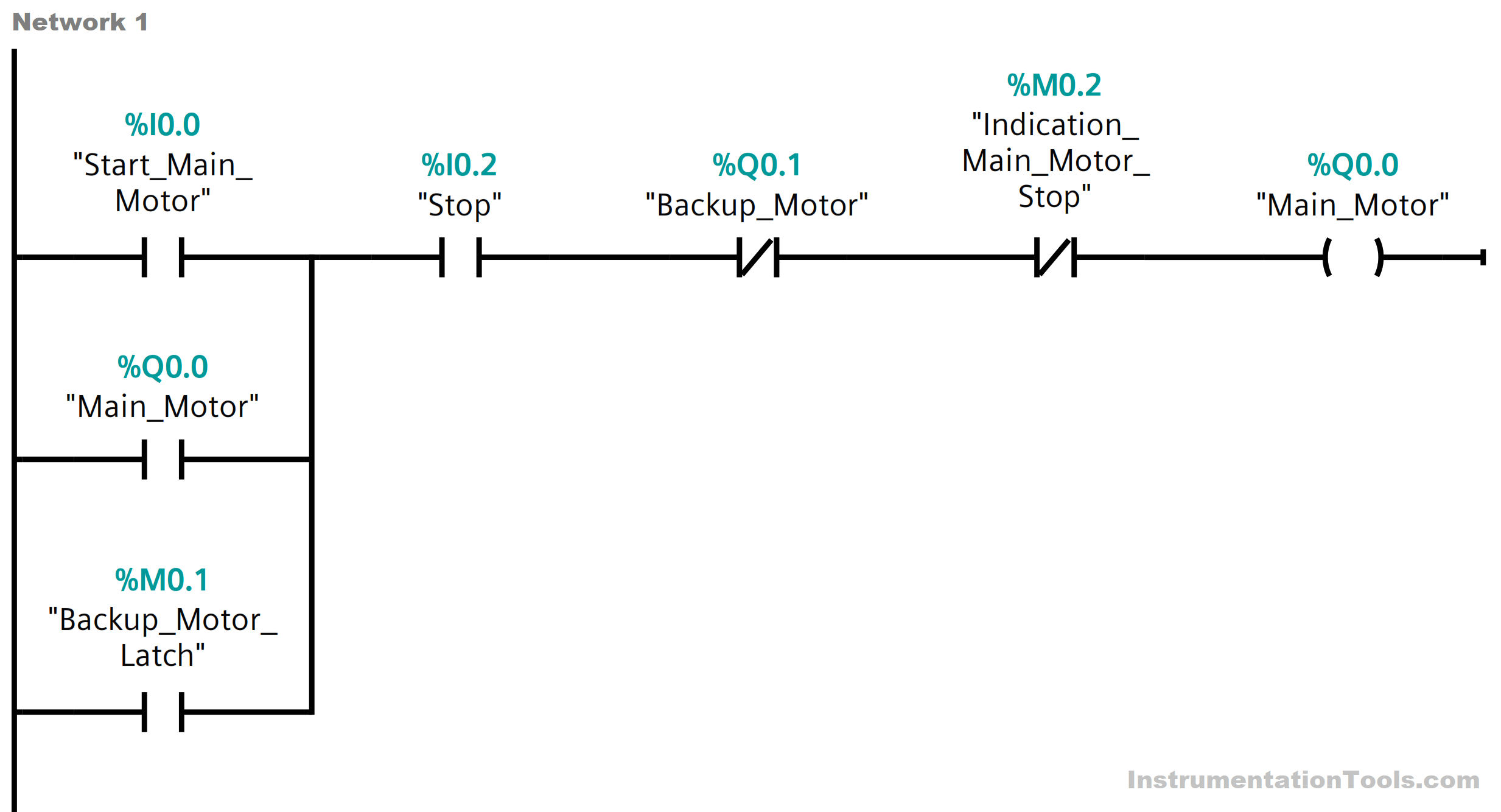
Notice that (I0.2) is the stop push button and it is already NC.
Also, we have an electrical interlock from the backup motor presented in (NC from Q0.1). to prevent the two motors from working together.
If the motor stops the bit (M0.2) would indicate that and it will stop the order of running that is presented on the digital outputs of the PLC signals.
Network 2: Controlling the Backup Motor
Then we have the second network that is shown in Fig. (3) as we can see by clicking on (I0.1) we can start the main motor.
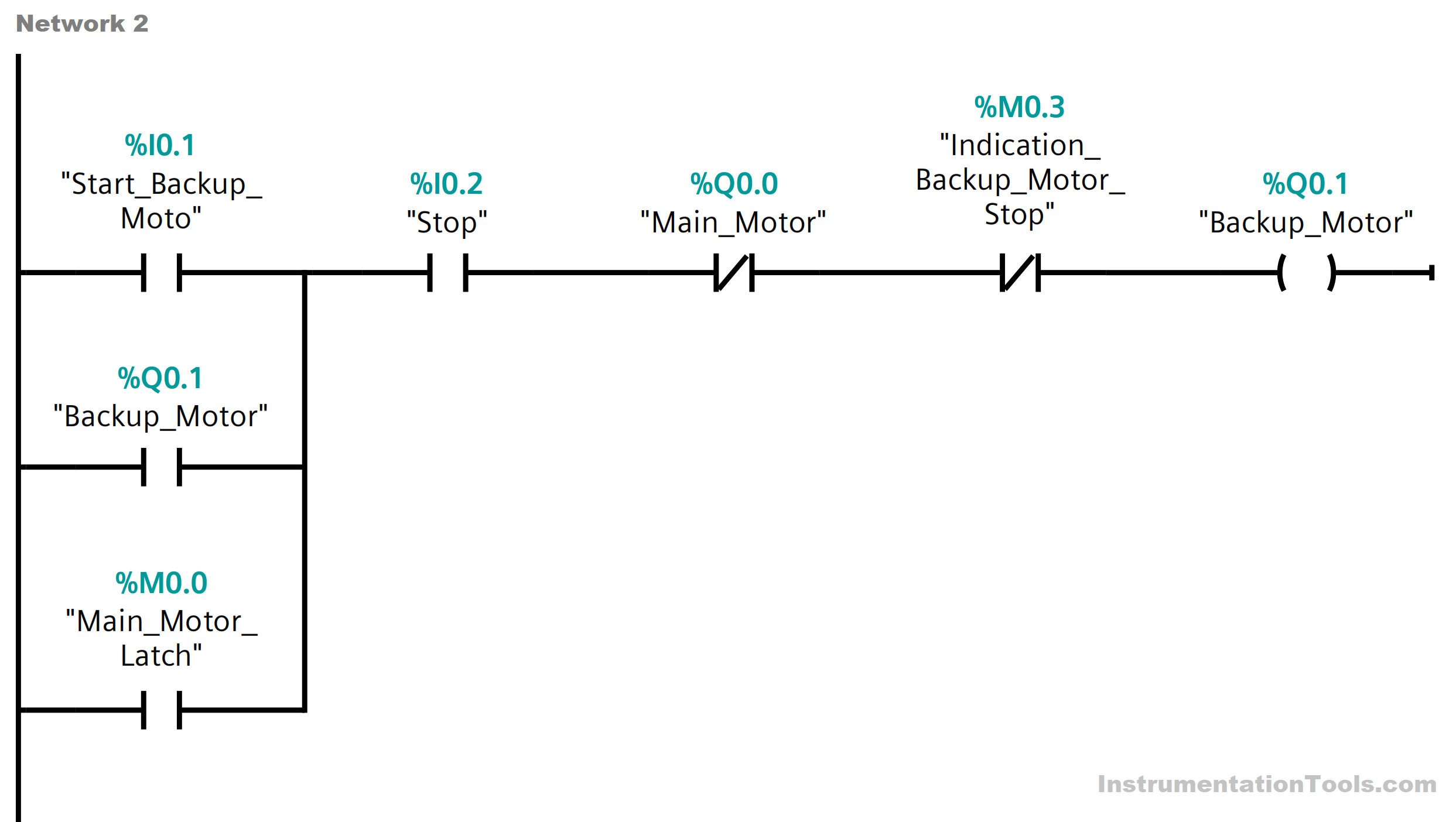
Beside the motor latch (Q0.1) we can see a bit (M0.0) that also can operate the backup motor in case of failure.
Also, we have an electrical interlock from the backup motor presented in (NC from Q0.1). to prevent the two motors from working together.
If the backup motor stops the bit (M0.3) would indicate that and it will stop the order of running that is presented on the digital outputs of the PLC signals.
Network 3: Main Motor Latch
For this network that is presented in Fig. (4) we can see that if any failure (Motor Stoppage) is indicated on the main motor by this bit (M0.2), the bit of (the main motor latch “M0.0”) will be energized.
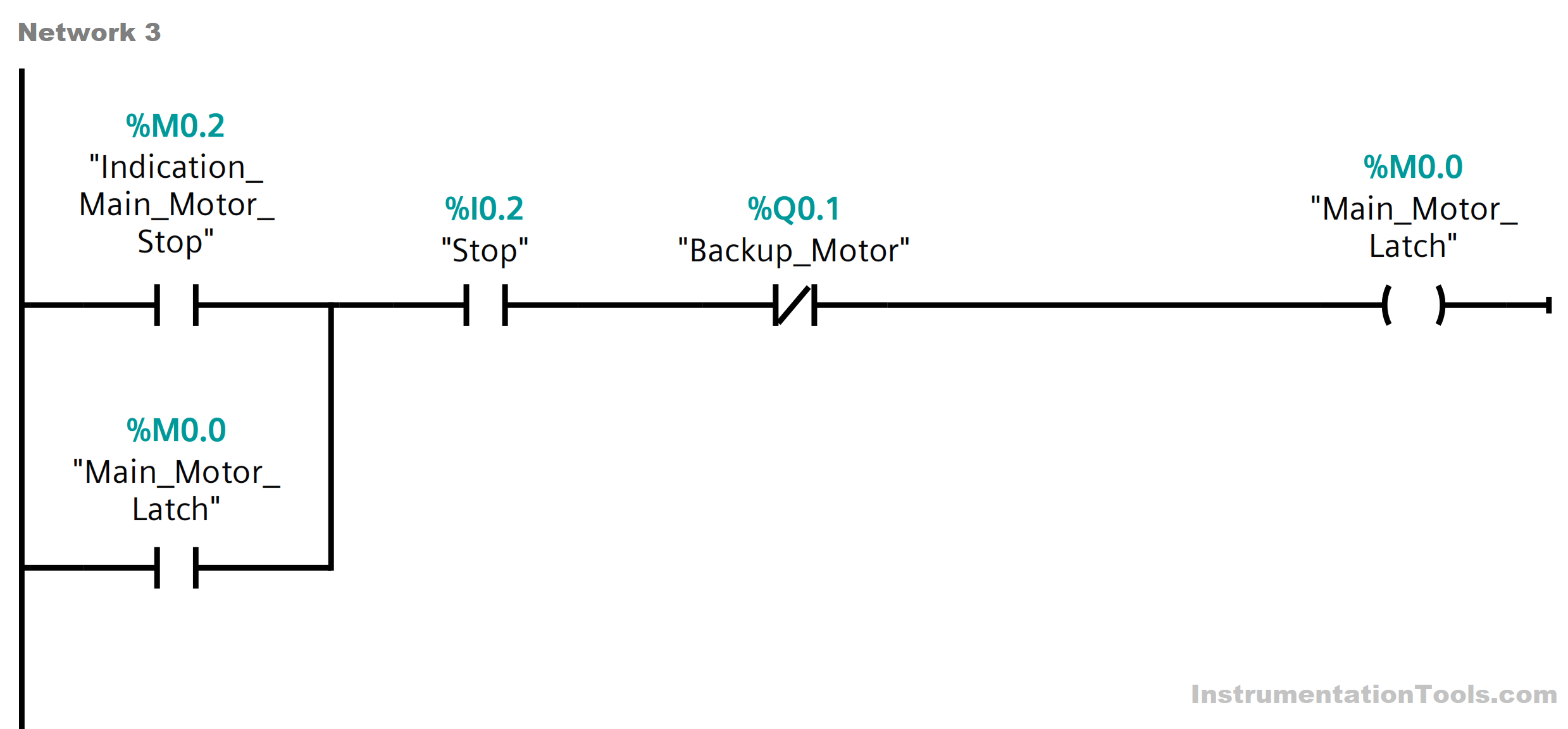
Then as you can see in Fig. (3) this bit will operate the backup motor then when the backup motor is on (by its role) it will de-energize the main motor latch (M0.0) again.
Network 4: Backup Motor Latch
Here we have the last network presented in Fig. (5) we can see that if any failure (Motor Stoppage) is indicated on the backup motor by this bit (M0.3), this bit (the backup motor latch “M0.1”) will be energized.
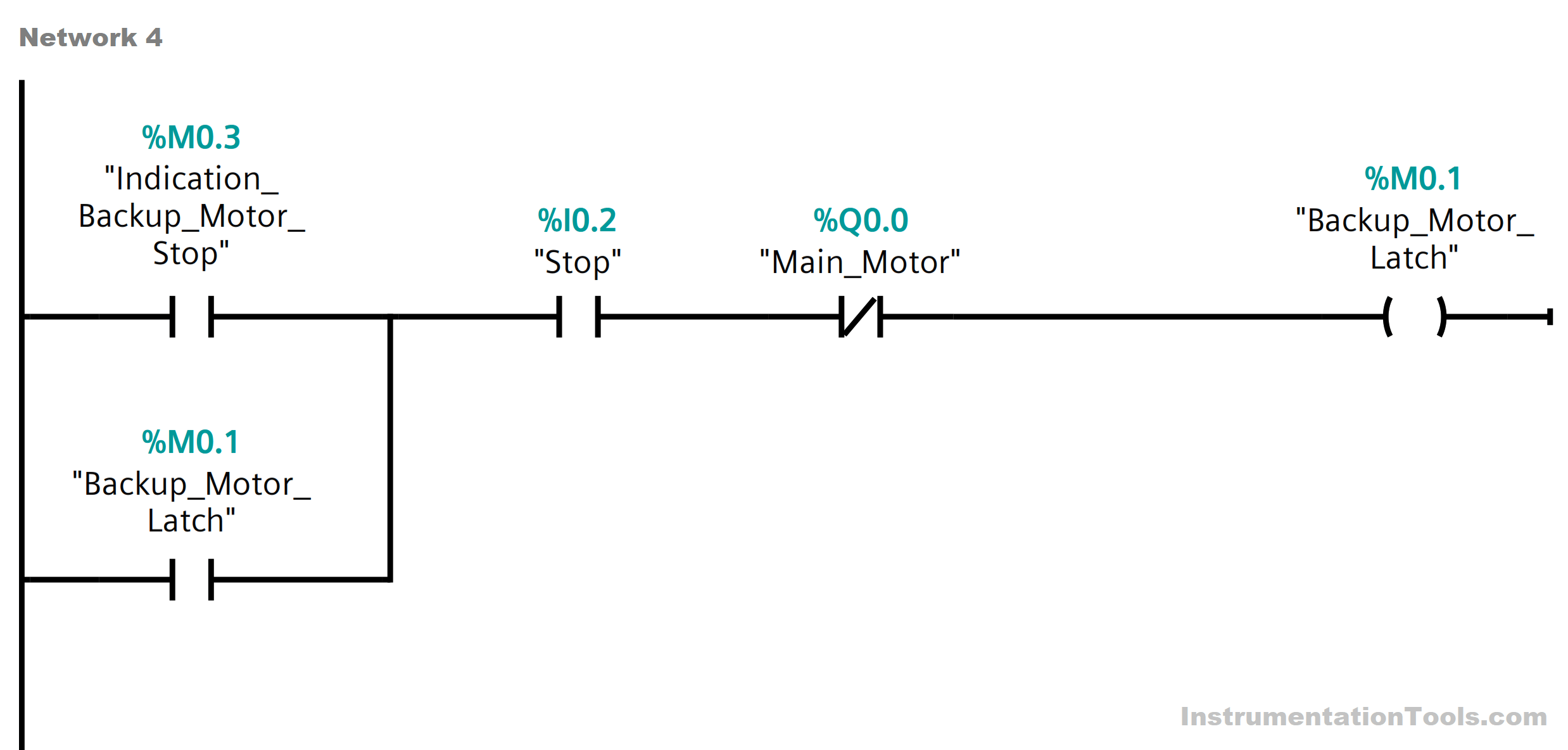
Then as you can see in Fig. (2) this bit will operate the main motor back again then when the main motor is on (by its role) it will de-energize the backup motor latch (M0.1) again.
If you liked this article, then please subscribe to our YouTube Channel for Instrumentation, Electrical, PLC, and SCADA video tutorials.
You can also follow us on Facebook and Twitter to receive daily updates.
Read Next:
- Scan Cycle in SIEMENS PLC
- Cloud-Based SCADA Projects
- PLC-based Gas Detection System
- Create New Project in Studio 5000
- Rockwell Allen Bradley PLC Projects