In industrial automation, VFD is a very important device used in electrical panels. Variable frequency drives are used widely for varying the speed of the motor according to the process requirements. This helps to control a process according to your needs.
VFD thus plays a crucial role in controlling a process smoothly. But, it too has its share of advantages and disadvantages. In this post, we will see the pros and cons of a VFD.
What is a VFD?
VFD stands for variable frequency drive. As the name implies, VFD is an electronic device that varies the speed of the motor by varying the output frequency. If the frequency is low, then the speed is low and if the frequency is high, then the speed is high.
So, the motor speed varies based on the frequency it receives from VFD. The frequency is varied by the most commonly used method – pulse width modulation.
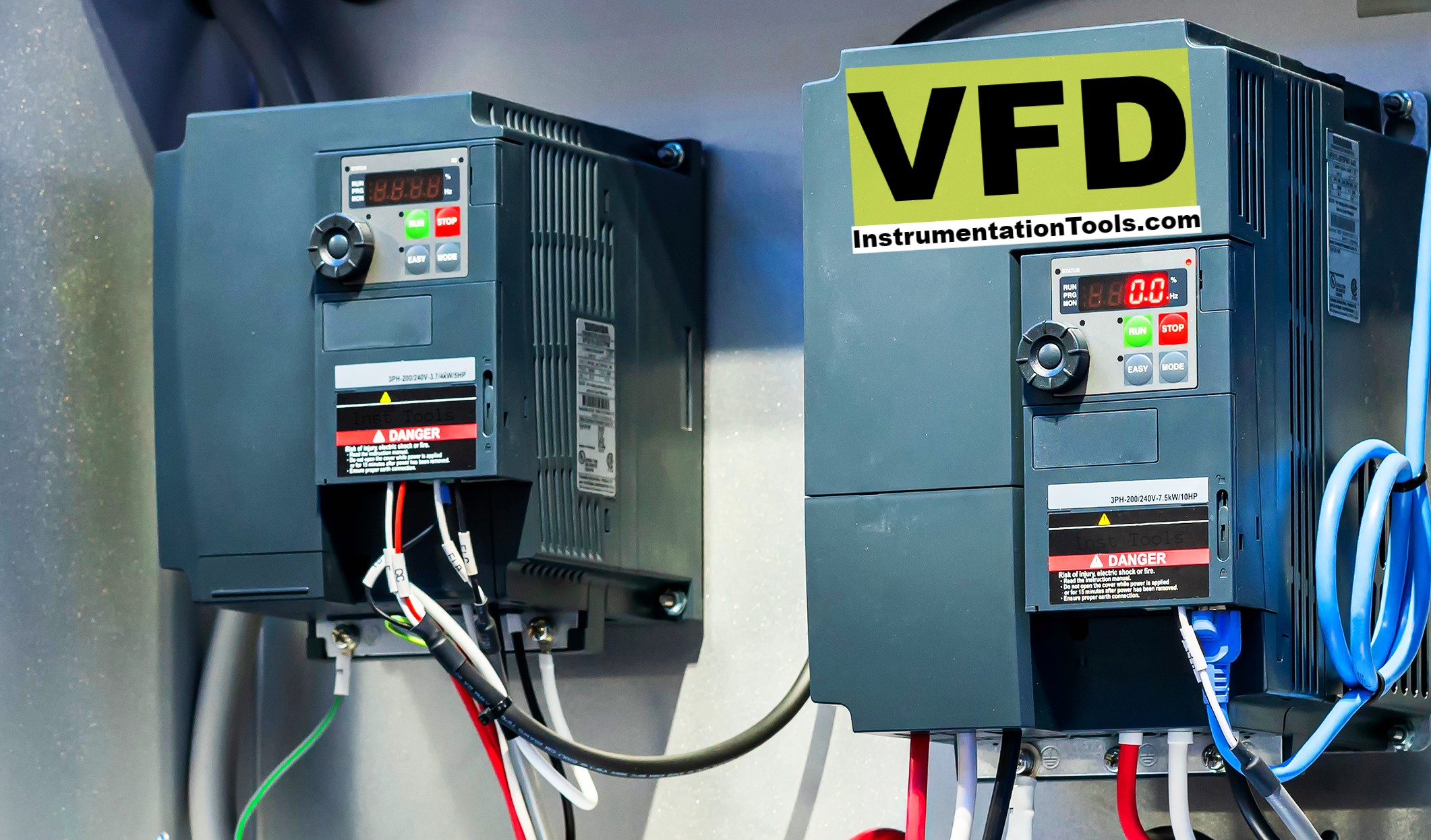
There is a main semiconductor component – IGBT, which plays a major role in modulating the pulses. The input waveform in AC form is converted to DC form inside and then converted back to AC form by IGBT which modulates the pulse width of the waveform. Based on the width, the frequency varies. And when the frequency varies, the motor speed varies.
The frequency reference is given by an external control signal, which can be 4-20mA, 0-10 V, or a communication protocol. Based on this control signal, the internal circuit captures it and decides how much to vary the width of the pulses. This means, the user demands his requirement by sending it on the same in the control signal and then varying the speed of the motor.
Generally, there are two frequencies used worldwide – 0 to 50 Hz and 0 to 60 Hz. Based on the input frequency received, the output frequency varies accordingly in that range.
If you are interested in learning the PLC programming for controlling the VFD drive, then watch the below video.
VFD Pros
The very first advantage is its speed variation capability. To date, there is no electronic device that can vary the speed of the motor.
As you have control over speed, the power consumption too reduced to a great extent. Instead of running the motor at full speed unnecessarily, just run it at the desired speed. Energy efficiency is increased and power consumption decreases by using VFD.
Motor ramp-up and ramp-down time varies through VFD. This allows a smooth start and stop of the motor and avoids excess current draw or load on the motor during this phase. Motor life is extended a lot due to this.
VFD comes with many adjustable parameters, but one such parameter that stands out is the ability to tune speed through PID. It takes feedback and based on it, varies the speed of the motor. So, there is no need for a controller like PLC to do this job. VFD does it for you.
VFD has a wide range of fault protection in it. This protects the motor from any type of damage. For example, if any single input phase out of the three phases fails, then the VFD immediately detects it and stops the motor by generating an alarm. Due to this, the motor is protected from any type of damage, be it minor or major.
Frequent switching on or off a motor does not affect its performance when a VFD is used.
You also get the option to vary the motor torque smoothly. This aligns the motor performance with the actual amount of load connected. So, the motor life increases to a great extent.
They come with many in-built communication protocols like Ethernet, Modbus, etc. which help to share data with any controller. Data exchange becomes smooth as you get abundant idea of what’s happening inside the motor and VFD.
VFD Cons
VFD is a very costly equipment. Yes, it cannot be replaced by any other device due to its variable speed property. But choose it only if there is a dire need for varying speed. Otherwise, VFD proves a costly initial investment.
VFD programming is difficult if it has many menus and sub-menus. This can sometimes confuse the operator.
Due to its sinusoidal three-phase output which is in true RMS value, they produce a large number of harmonics, voltage transients, and spikes sometimes and this can disturb the other electrical equipment present near it.
Heat dissipation is more when VFD is in use, so it requires proper cooling methods to keep the panel heat under control.
If you liked this article, then please subscribe to our YouTube Channel for PLC and SCADA video tutorials.
You can also follow us on Facebook and Twitter to receive daily updates.
Read Next:
- Motor Feedback PLC Logic
- Steps in PLC System Design
- SCADA System Vulnerabilities
- Delta PLC and VFD with Modbus
- Industrial Automation Documents