Variable area flow meters operate at a constant delta pressure (Δp) and the area changes with the flow rate. The area will increase as the flow rate through the meter increases to preserve a constant Delta Pressure (Δp).
Variable Area Flow Meters
The most common design of variable area meters is the cone-and-float type, which is also known as a rotameter. The basic design of a variable area meter is a tapered tube (usually glass) containing a self-centering float that is pushed up by the flow and pulled down by gravity.
At higher flow rates the float rises to increase the area between the tube and the float and maintain a constant Δp.
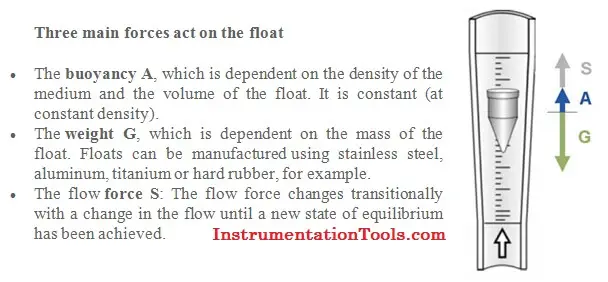
The flow rate is determined by how far the float has risen up the tube: there are graduations on the side of the tube. Variable area meters are widely used for metering gas but different types are available for a variety of different fluids. A buoyancy correction term is required for liquids and dense fluids.
Variable area flowmeters are very simple yet versatile flow measurement devices for use on all types of liquids, gases, and steam. They operate on the variable area principle, whereby a flowing fluid changes the position of a float, piston, or vane to open a larger area for the passage of the fluid. The position of the float, piston, or vane is used to give a direct visual indication of the flow rate.
Rotameters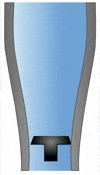
The rotameter is an industrial flowmeter used to measure the flow rate of liquids and gases. Its operation is based on the variable area principle: fluid flow raises a float in a tapered tube, increasing the area for the passage of the fluid. The greater the flow, the higher the float is raised.
The height of the float is directly proportional to the flow rate. With liquids, the float is raised by a combination of the buoyancy of the liquid and the velocity head of the fluid.
With gases, buoyancy is negligible, and the float responds to the velocity head alone. The float moves up or down in the tube in proportion to the fluid flow rate and the annular area between the float and the tube wall.
The float reaches a stable position in the tube when the upward force exerted by the flowing fluid equals the downward gravitational force exerted by the weight of the float.
A change in flow rate upsets this balance of forces. The float then moves up or down, changing the annular area until it again reaches a position where the forces are in equilibrium.
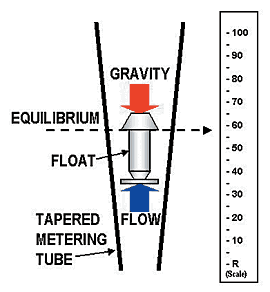
To satisfy the force equation, the rotameter float assumes a distinct position for every constant flow rate. However, it is important to note that because the float position is gravity-dependent, rotameters must be vertically oriented and mounted.
The tapered tube’s gradually increasing diameter provides a related increase in the annular area around the float, and is designed in accordance with the basic equation for volumetric flow rate:

where:
Q = volumetric flow rate, e.g., gallons per minute
k = a constant
A = annular area between the float and the tube wall
g = force of gravity
h = pressure drop (head) across the float
With h being constant in a VA meter, we have A as a direct function of flow rate Q. Thus, the rotameter designer can determine the tube taper so that the height of the float in the tube is a measure of flow rate.
Variable area flowmeters are used primarily to set flow rates. The operator observes the meter and adjusts the valve to bring the process flow to the proper flow rate.
The meter’s ability to repeat or reproduce this flow rate is of primary importance. Rotameters are repeatable up to ±1 ⁄4% of the instantaneous flow rate. This feature enables the operator to reset or adjust the flow with confidence.
Advantages of Variable Area Flow Meters
- The rotameter is popular because it has a linear scale, a relatively long measurement range, and a low-pressure drop.
- It is simple to install and maintain.
- It can be manufactured in a variety of construction materials and designed to cover a wide range of pressures and temperatures.
- The rotameter can easily be sized or converted from one kind of service to another. In general, it owes its wide use to its versatility in construction and applications.
- Because of its functional advantages, the rotameter is an exceptionally practical flow measurement device.
- The pressure drop across the float is low and remains essentially constant as the flow rate changes. Float response to flow rate changes is linear, and a 10-to-1 flow range or turndown is standard.
- Variable area flowmeters are commonly used to provide cost-effective local indication of small liquid or gas flows
Disadvantages of Variable Area Flow Meters
- Low accuracy – uncertainty on volumetric flowrate is ~2% of reading
- Generally small turndown
- Tendency of float to ‘stick’ at low flows
- Requirement for buoyancy correction in liquids
- Application Cautions for Variable Area Flowmeters
Do not apply variable area flowmeters to fluids that are opaque, dirty, or prone to coat the metering tube or float, because these may render the flowmeter inoperable.
Be sure to install variable area flowmeters with floats in the vertical orientation because their operation is dependent upon gravity. Variable area flowmeters that require upward flow may not be suitable in many applications where the fluid flows using only gravity.
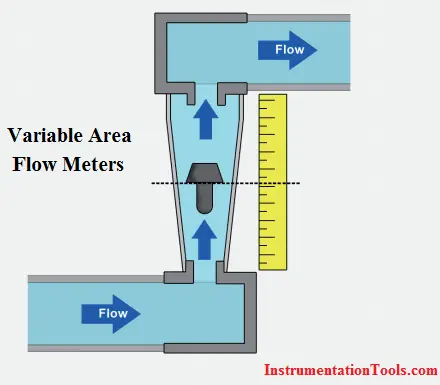
A potential safety hazard can be created if a glass metering tube breaks, especially when dangerous fluids are present in the flowmeter. Be careful to install variable area flowmeters with glass metering tubes in locations where the glass cannot be damaged.
Also, the float can get stuck when the flow turns on suddenly or when high flow rates cause the float to reach its highest mechanical position.
If you liked this article, then please subscribe to our YouTube Channel for Instrumentation, Electrical, PLC, and SCADA video tutorials.
You can also follow us on Facebook and Twitter to receive daily updates.
Read Next:
- Types of Level Measurement
- Level Measurement Systems
- Types of Variable Area Flow Meters
- Velocity-based Flow Meter
- How to Select a Rotameter?
Whether Rotameter Flow Transmitter output can control VFD motors?
Based on the formula the flow rate is independent of the actual pressure, but is proportional to the differential pressure. Is this true at very low pressures? If we are working with a system pressure of 20mbar absolute and the air coming in is restricted. Is there a correction based on absolute pressure in the system?