Reliability centered maintenance (RCM) is a tool used to identify potential problems and designed to optimize maintenance programs.
RCM is a process used to improve the maintenance tasks in an efficient manner, cost-effective, reliable and safe strategy.
Reliability Centered Maintenance (RCM) requires a complete mindset shift from the traditional maintenance management approach of doing PM (preventive maintenance) to everything, everywhere in the hope of preventing all failures.
Reliability Centered Maintenance
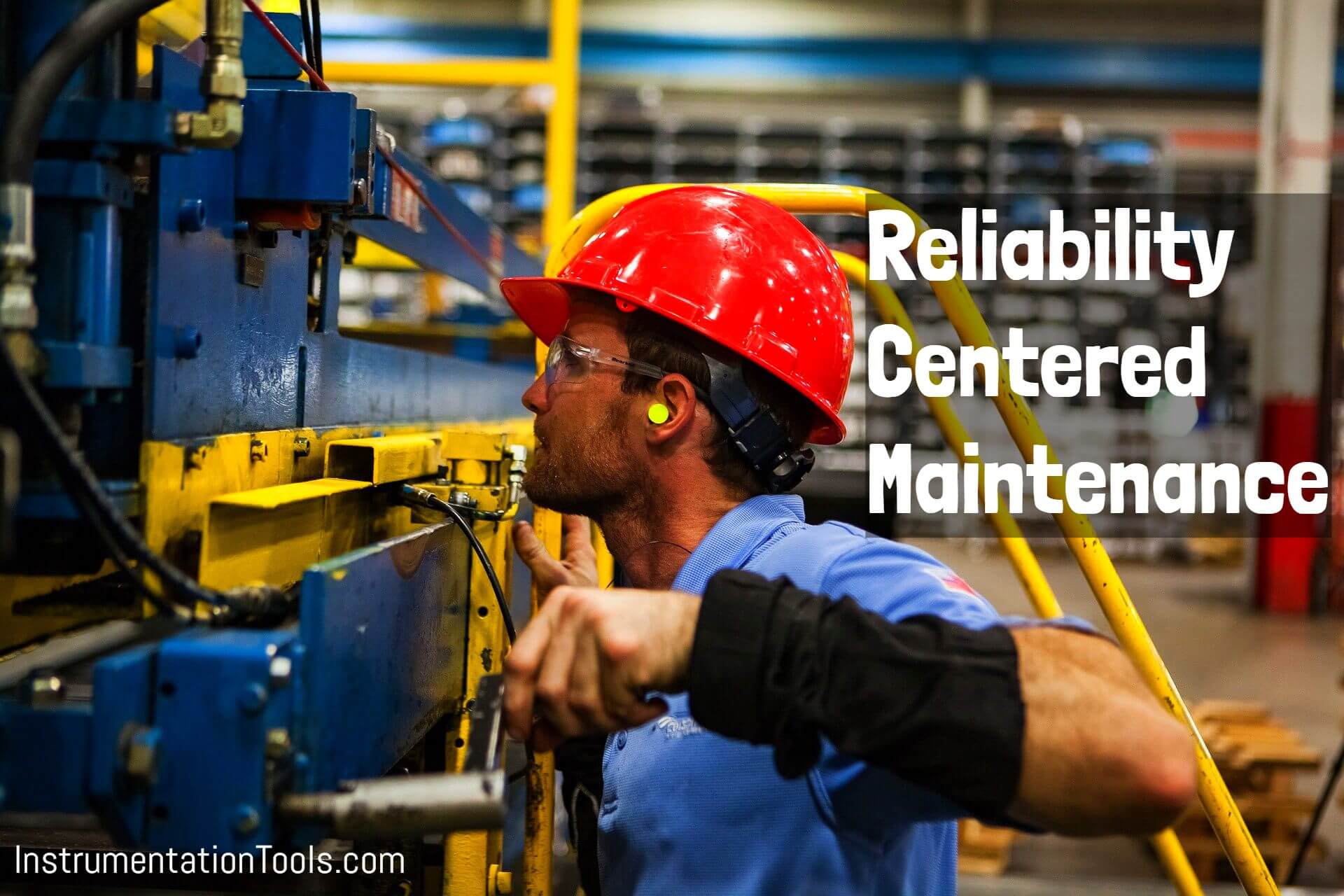
RCM is a systematic process to determine what must be done to keep assets doing.
What operators need them to do in their current operational context.
The RCM process requires a multidisciplinary team to answer the below few questions about the asset being assessed:
Functions
What are the functions and associated desired standards of performance of the asset in its present operating context?.
In other words, what do operations want the asset to do versus what the asset can do at its peak performance level?
Functional Failures
In what ways can it fail to fulfill its functions?
We need to define which failures to perform the defined functions are relevant and worthy of in-depth analysis.
Failure Modes
What causes each functional failure?.
We brainstorm on all possible failure events and their causes.
Failure Effects
What happens when each failure occurs?.
We must determine each “failure”s impact by describing the sequence of events happening when each failure mode occurs.
Failure Outcomes
In what way does each failure matter?.
How is safety, environment, production, or maintenance cost impacted?.
Was the failure a result of a faulty protection device?
- Proactive tasks and task intervals: What action is needed to predict or prevent each failure?.
We must determine whether any form of proactive maintenance, that is, what condition or time base tasks, can be applied to avoid each failure.
- Default actions: What should be done if a suitable proactive task cannot be found?.
In the case that proactive tasks are not technically or economically viable, the team has to determine the most appropriate course of action for failure management.
At this stage, we must decide whether we can let the failure happen or whether redesign or some other one-time change is needed to avoid the failure or its consequences.
RCM is a process, that is also capable of delivering many other benefits as well as just improving reliability.
RCM Analysis and Implementation of Changes
Based on the results of RCM analysis, start to implement changes by
- Reactive maintenance
- Preventive maintenance
- Predictive maintenance
Reactive Maintenance
It is a process of normalizing the equipment as it fails. This type of maintenance tends to be the most costly, but never avoidable.
Preventive Maintenance
Preventive maintenance is performed while the equipment is still in working condition to avoid unexpected breakdowns.
Predictive Maintenance
Determine the condition of the equipment while it is in use through software and hardware designed to measure functionality or abnormalities also called “ condition monitoring”.
The returns are gained by knowing the exact way when the services are needed.
Advantages of RCM
The following are the advantages of Reliability Centered Maintenance:
Improves the equipment availability.
Reduces maintenance costs.
Reduces resource costs.
Disadvantages of RCM
RCM does not put into account costs related to the maintenance of an asset.
Conclusion
RCM is recognized as one of the most powerful tools a company can use to obtain more value from its physical assets.
It is the cornerstone of highly successful maintenance programs to ensure that machines help operations to deliver as required, yielding or exceeding the anticipated financial outcome required by stakeholders.
It is a means to optimize reliability and maintainability performance to achieve greater uptime.
Reference: Reliability Centered Maintenance by John Moubray
Read Next:
As early as the 1970s, post-mortem maintenance (BM) prevailed in the field of equipment management. After entering the 1970s, with the transformation of management thinking, the preventive maintenance model (PM) has been expanded worldwide.
During this period, the former Soviet Union prevailed in some Western countries, the aviation sector usually adopted the state model (CBM), and more often used the state-based maintenance model;With the application of computer technology and the development of testing technology and instruments in the 1980s, some developed countries began to adopt the predictive maintenance model (PDM);
in the 1990s, the world economy gradually moved towards integration, and fierce market competition led to some innovative enterprises. Stand out, they widely adopt Active Maintenance Mode (PAM);In recent years, some developed countries have introduced the concept of economy in the PAM practice process, and further developed a reliability-centric maintenance (RCM) model, which is based on the active maintenance (PAM) model.
The combination of improved maintenance, it reasonably distinguishes key parts, based on reliability as the premise, and based on the principle of economical applicability, it classifies the types of faults, maintenance methods, and whether to undergo transformation.
It focuses on dynamic management to give full play to the failure Disintegration detection and non-disintegration maintenance technology expertise, and constantly guide users to take measures to improve weak parts in a timely manner, so that the maintenance work can obtain the greatest economic benefits
Wide-plus Transmitter