This article discusses the PLC program to control Crane movement using the Schneider PLC in the Ecostruxure Machine Expert-Basic software. The Crane Machine has a Trolley that can move Left or Right and a Hoist that can move Up or Down. This PLC system uses a Proximity Sensor to limit the range of Left or Right movement of the Trolley and Upward movement of the Hoist Crane. This system has an Emergency button to Stop all Crane movements without turning Off the system.
PLC Hoist Crane Programming
This PLC program has 7 buttons:
- START SYSTEM (I0.0) button is used to turn ON the system.
- The STOP SYSTEM (I0.1) button is used to turn OFF the system.
- UP_BUTTON (I0.5) is used to move the Hoist Crane UP. When this button is Pressed, the Output OUT_UP (Q0.3) will be ON.
- DOWN_BUTTON (I0.4) button is used to move the Hoist Crane DOWN. When this button is Pressed, the output OUT_DOWN (Q0.2) will be ON.
- LEFT_BUTTON (I0.2) is used to move the Crane to the LEFT. When this button is Pressed, the output OUT_LEFT (Q0.0) will be ON.
- The RIGHT_BUTTON (I0.3) button is used to move the Crane to the RIGHT. When this button is Pressed, then the output OUT_RIGHT (Q0.1) will be ON.
- EMERGENCY (I0.6) button is used to Stop all Crane movement without turning OFF the system.
This Crane system uses a Proximity Sensor as a safety measure to prevent the Crane from moving beyond the safety limit.
- SENS_UP (I0.7) is used to limit the Highest position of the Hoist Crane, preventing the Hoist Crane from hitting the Hoist Motor.
- SENS_LEFT (I0.8) is used to limit the crane’s range when moving to the LEFT.
- SENS_RIGHT (I0.9) is used to limit the crane’s range when moving to the RIGHT.
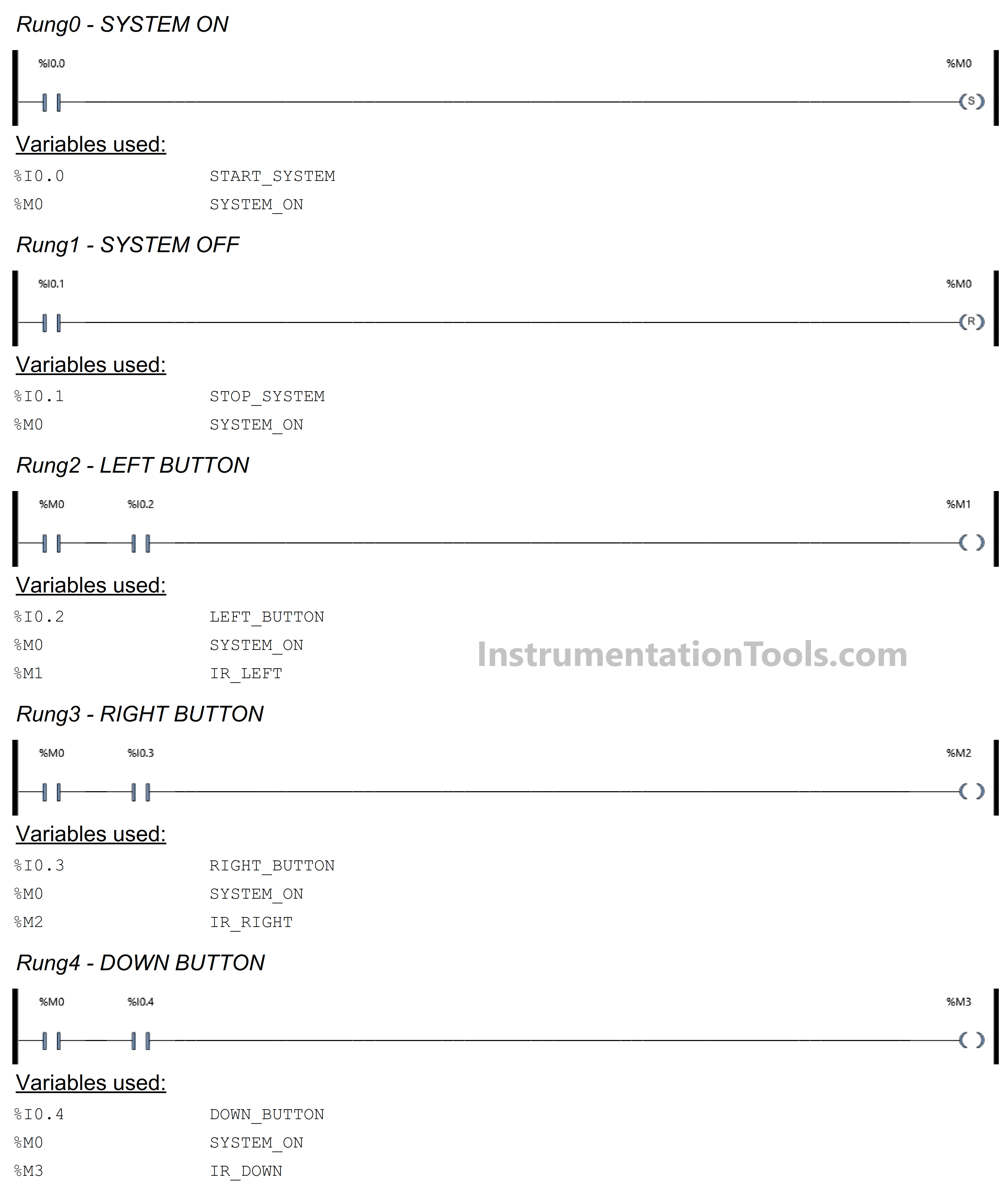
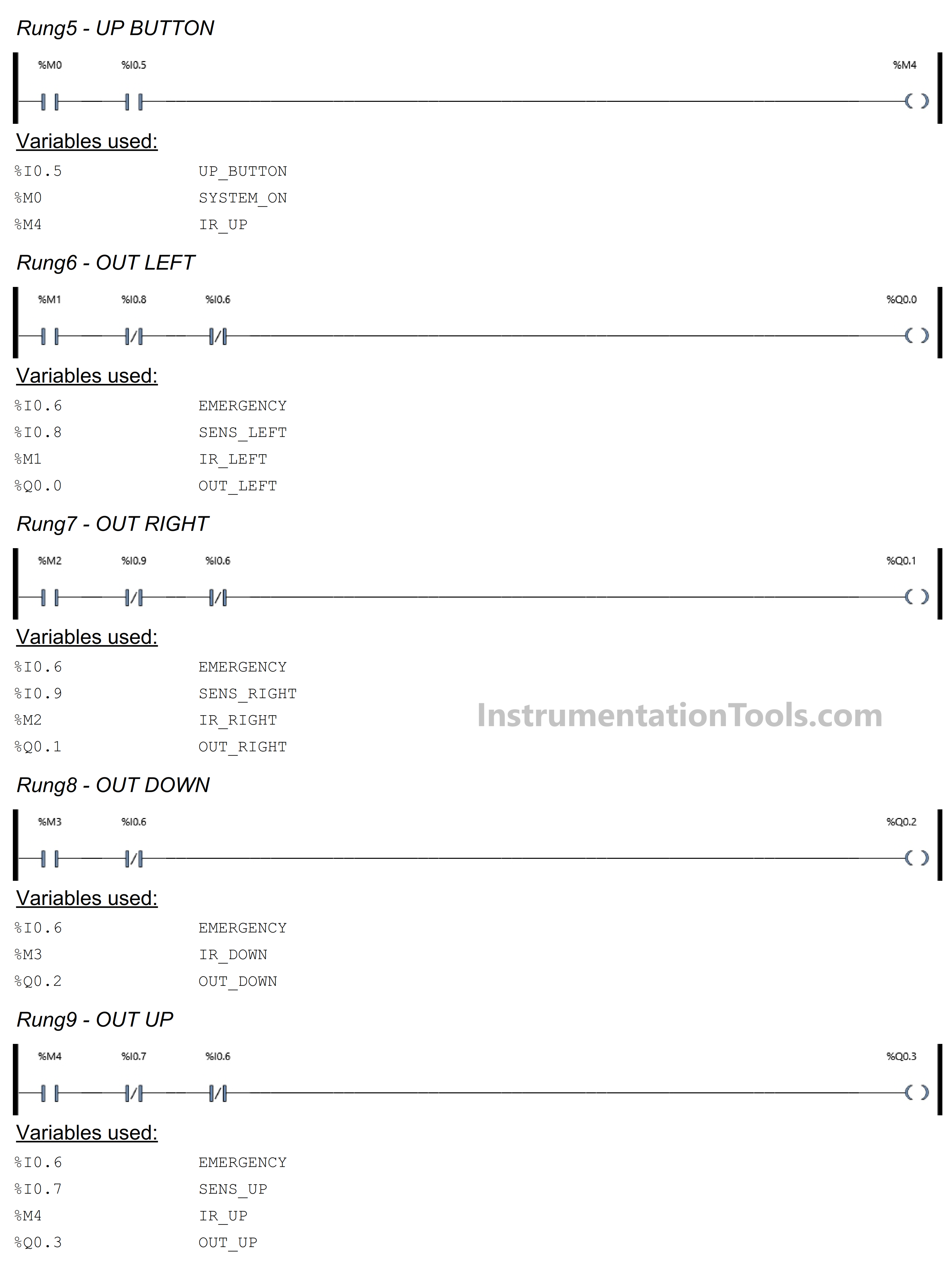
I/O Addressing
Comment | Input (I) | Output(Q) | Memory Bits |
START_SYSTEM | I0.0 | Â | Â |
STOP_SYSTEM | I0.1 | Â | Â |
LEFT_BUTTON | I0.2 | Â | Â |
RIGHT_BUTTON | I0.3 | Â | Â |
DOWN_BUTTON | I0.4 | Â | Â |
UP_BUTTON | I0.5 | Â | Â |
EMERGENCY | I0.6 | Â | Â |
SENS_LEFT | I0.8 | Â | Â |
SENS_RIGHT | I0.9 | Â | Â |
SENS_UP | I0.7 | Â | Â |
OUT_LEFT | Â | Q0.0 | Â |
OUT_RIGHT | Â | Q0.1 | Â |
OUT_DOWN | Â | Q0.2 | Â |
OUT_UP | Â | Q0.3 | Â |
SYSTEM_ON | Â | Â | M0 |
IR_LEFT | Â | Â | M1 |
IR_RIGHT | Â | Â | M2 |
IR_DOWN | Â | Â | M3 |
IR_UP | Â | Â | M4 |
Schneider Programming of PLC
In this Rung, the memory bit SYSTEM_ON (M0) will be in the HIGH state if the START_SYSTEM (I0.0) button is Pressed. Because it uses the SET Coil Instruction, the memory bit SYSTEM_ON (M0) remains in the HIGH state even though the START_SYSTEM (I0.0) button has been Released.
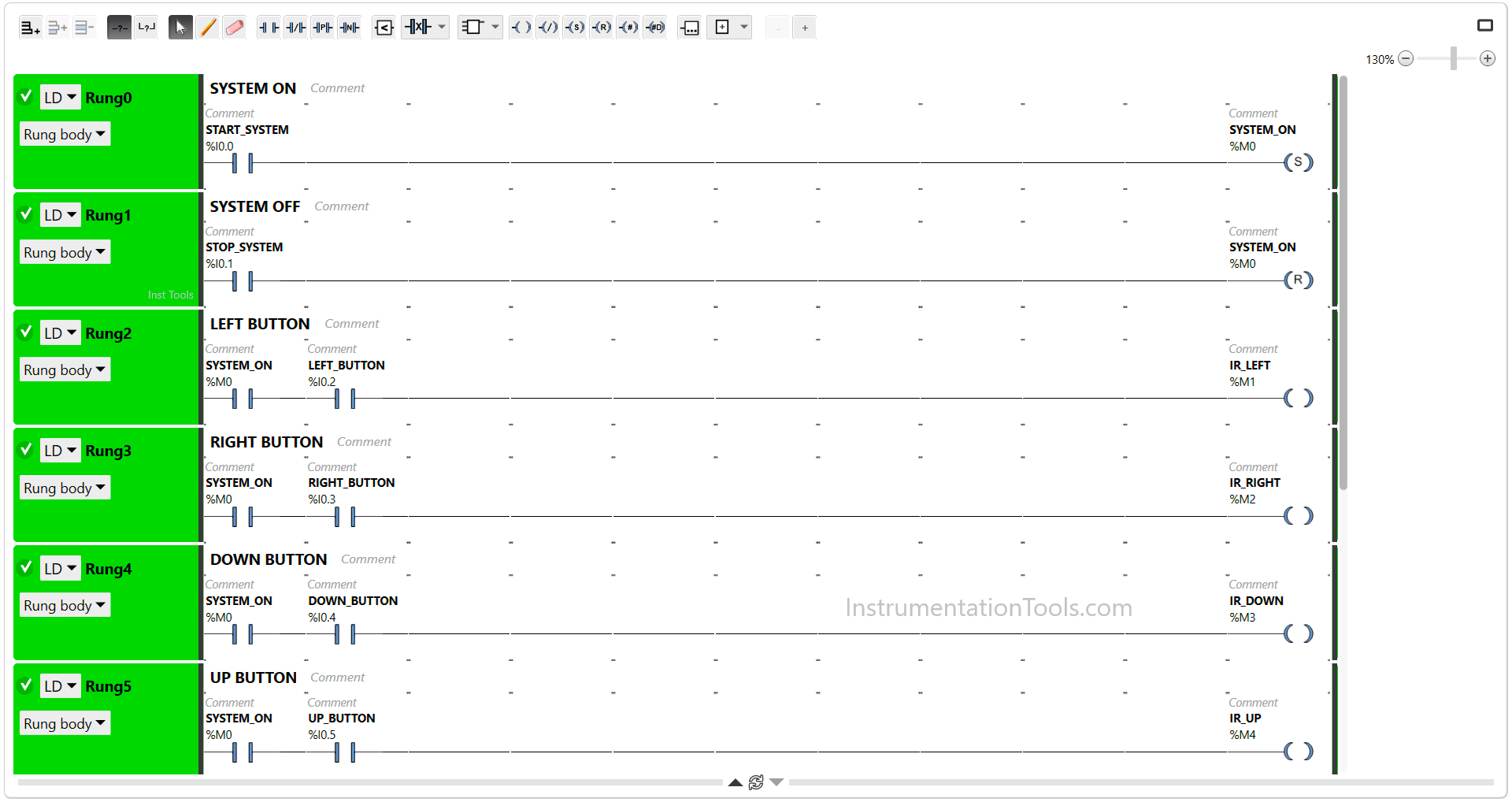
RUNG 1 (SYSTEM OFF)
In this Rung, the memory bit SYSTEM_ON (M0) will become LOW state if the STOP_SYSTEM (I0.1) button is Pressed. Because it uses the RESET Coil Instruction.
RUNG 2 (LEFT BUTTON)
In this Rung, the memory bit IR_LEFT (M1) will be in the HIGH state if the NO contact of memory bit SYSTEM_ON (M0) in the HIGH state and the LEFT_BUTTON (I0.2) button is Pressed.
RUNG 3 (RIGHT BUTTON)
In this Rung, the memory bit IR_RIGHT (M2) will be in the HIGH state if the NO contact of memory bit SYSTEM_ON (M0) in the HIGH state and the RIGHT_BUTTON (I0.3) button is Pressed.
RUNG 4 (DOWN BUTTON)
In this Rung, the memory bit IR_DOWN (M3) will be in the HIGH state if the NO contact of memory bit SYSTEM_ON (M0) in the HIGH state and the DOWN_BUTTON (I0.4) button is Pressed.
RUNG 5 (UP BUTTON)
In this Rung, the memory bit IR_UP (M4) will be in the HIGH state if the NO contact of memory bit SYSTEM_ON (M0) in the HIGH state and the UP_BUTTON (I0.5) button is Pressed.
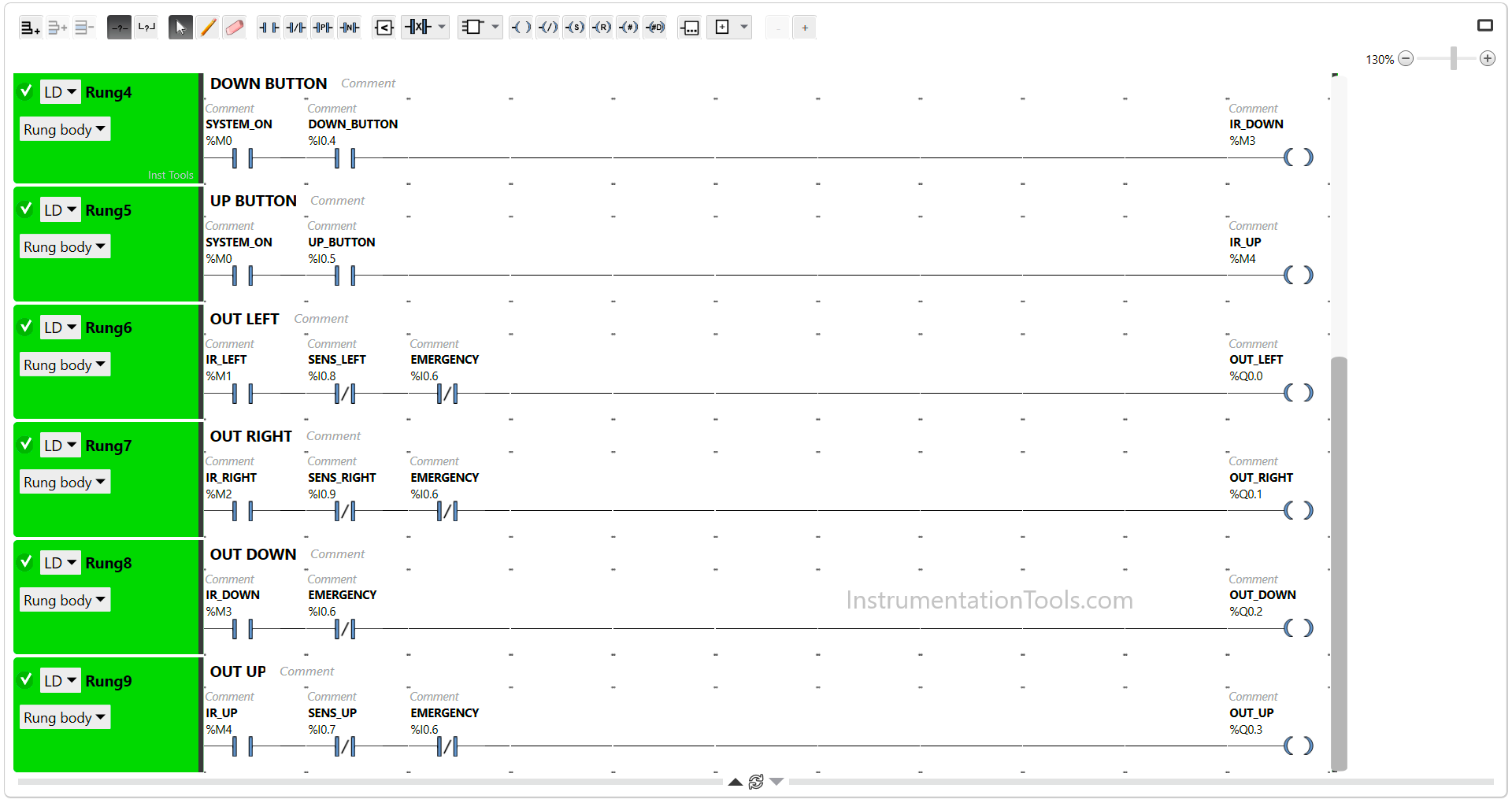
RUNG 6 (OUT LEFT)
In this Rung, when the NO contact of memory bit IR_LEFT (M1) in the HIGH state, the Output OUT_LEFT (Q0.0) will be ON.
The OUT_LEFT (Q0.0) output will be OFF if the EMERGENCY (I0.6) button is Pressed or if the NC contact of Proximity Sensor SENS_LEFT (I0.8) in the HIGH state.
RUNG 7 (OUT RIGHT)
In this Rung, when the NO contact of memory bit IR_RIGHT (M2) in the HIGH state, the Output OUT_RIGHT (Q0.1) will be ON.
The OUT_RIGHT (Q0.1) output will be OFF if the EMERGENCY (I0.6) button is Pressed or if the NC contact of Proximity Sensor SENS_RIGHT (I0.9) in the HIGH state.
RUNG 8 (OUT DOWN)
In this Rung, when the memory bit IR_DOWN (M3) in the HIGH state, the Output OUT_DOWN (Q0.2) will be ON.
The OUT_DOWN (Q0.2) output will be OFF if the EMERGENCY (I0.6) button is Pressed.
RUNG 9 (OUT UP)
In this Rung, when the NO contact of memory bit IR_UP (M4) in the HIGH state, the Output OUT_UP (Q0.3) will be ON.
The OUT_UP (Q0.3) output will be OFF if the EMERGENCY (I0.6) button is Pressed or if the NC contact of Proximity Sensor SENS_UP (I0.7) in the HIGH state.
Read Next:
- Conveyor Sorting with Color Detection
- Difference Between PLC and CNC Machine
- PLC Programming Clothes Washing System
- PLC Example for Traffic Light FBD Program
- PLC Program for Password Management