The overall effectiveness of any grounding system will be determined by the individual components that are used to construct the system and the manner in which the components are connected. The purpose of this article will be to review the selection of these components and the methods by which they should be interconnected.
Great care must be exercised in selecting all of the following grounding components:
- The Grounding Conductors
- The Grounding Electrodes
- The Connectors
Grounding Components
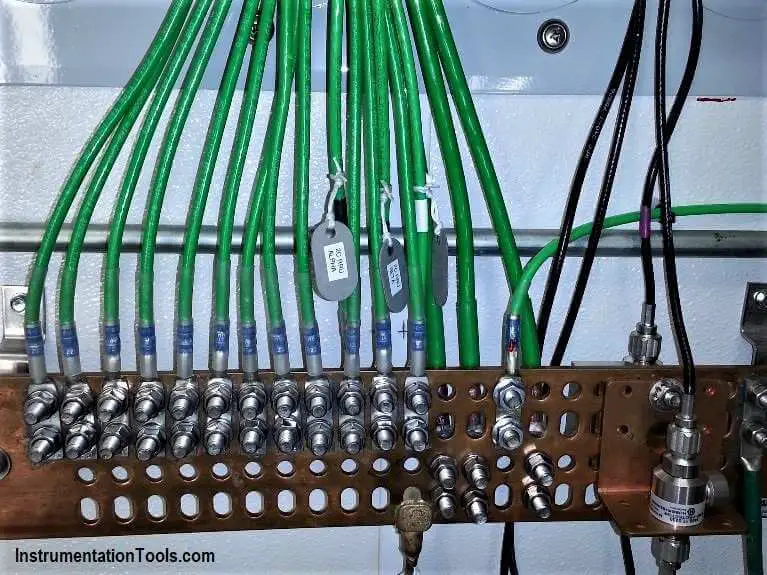
The Grounding Conductors
The NEC contains requirements for both the equipment grounding conductors (EGC) and the grounding electrode conductor (GEC).
Recall that the EGC is used to connect the noncurrent-carrying metal parts of equipment, enclosures, raceways, etc., to the system grounded conductor and/or the grounding electrode conductor at the service or source of a separately derived system. The GEC, on the other hand, is used to connect the grounding electrode to the EGC and/or grounded conductor at the service or source of a separately derived system.
Equipment Grounding Conductors
Materials:
Section 250-91 (b) lists 11 components which are permitted to serve as the equipment grounding conductor for both branch-circuits and feeders. The permissible items are a copper or other corrosion-resistant conductor.
EGC’s are permitted to be either solid or stranded; insulated, covered, or bare; and in the form of a wire or a busbar of any shape, rigid metal conduit, intermediate metal conduit, electrical metallic tubing, flexible metal conduit where both the conduit and fittings are listed for grounding, armor of Type AC cable, the copper sheath of mineral-insulated, metal-sheathed cable, the metallic sheath or the combined metallic sheath and grounding conductors of Type MC cable, cable trays as permitted in Sections 318-3(c) and 318-7 of the NEC, cablebus framework as permitted in Section 365-2(a) of the NEC, other electrically continuous metal raceways listed for grounding.
Installation:
No matter what type of EGC is selected, the NEC requires in Section 300-3 (b) that in general, all conductors of the circuit, including the EGC must be contained within the same raceway, cable tray, trench, cable or cord.
The purpose of this requirement is to ensure the impedance of the EGC remains at the lowest possible value. When the circuit conductors are run in parallel, as permitted by Section 310- 4 of the NEC, the equipment grounding conductors are also required to be run in parallel. In these parallel installations the EGC must be a full sized conductor based on the ampere rating of the overcurrent protective device protecting the circuit conductors.
The NEC further requires in Section 250-92 (c) that the EGC shall be installed with all of the applicable provisions in the Code for the type of EGC which is selected. In other words, if rigid metal conduit (RMC) is used as the EGC, as permitted in Section 250-91 (b) (2), the RMC must be installed in a manner that meets all of the requirements for RMC contained in Article 346 of the NEC.
Installers of electrical systems should understand that when they install a raceway system, such as RMC, and it is used as an EGC, each length of conduit is part of the overall equipment grounding system. For this reason, any terminations at boxes or couplings must be made up wrenchtight to ensure a low impedance ground path.
Size:
When the equipment grounding conductor is a separate conductor, as permitted by 250-91 (b) (1), the size of the EGC is determined by the rating or the setting of the overcurrent protective device (fuse or circuit breaker) which is ahead of the equipment, conduit, etc.
Table 250-95 of the NEC contains the minimum size for aluminum, copper-clad aluminum and copper equipment grounding conductors. The table includes sizes for circuits from 15- amperes up to 6000-amperes. The values listed in the table are based on a maximum circuit conductor length of 100 feet.
For conductor lengths longer than 100 ft, an adjustment in the EGC size may be necessary. Section 250- 95 requires that where the circuit ungrounded conductors are increased in size to allow for voltage drop, the circuit equipment grounding conductors must be adjusted proportionately as well.
Grounding Electrode Conductors
Materials:
The grounding electrode conductor is permitted to be constructed of copper, aluminum, or copper-clad aluminum. Copper-clad aluminum is constructed of a minimum of 10% copper which is metallurgically bonded to the aluminum core.
The GEC is permitted to be a solid or stranded conductor and it can be an insulated, covered or bare conductor. Solid conductors provide less surface area to corrode and subsequently are used when installed in corrosive locations. However, stranded conductors in general are easier to work with so they are used more frequently.
With stranded conductors of a given size, the greater the number of strands, the smaller each strand is and the conductor is more flexible. Copper is by far the most common choice for grounding electrode conductors but copper-clad aluminum may be used to reduce the likelihood of repeated theft of the copper GEC.
The major disadvantage to using aluminum is the installation restriction in damp or wet locations. See installation provisions below.
Installation:
In general, grounding electrode conductors are required to be installed in one continuous length, without splices or joints. As noted above however, the GEC can be spliced by means of irreversible compression-type connectors listed for the use or by means of the exothermic welding process (CADWELD).
Also as noted above, the GEC can be installed directly on a building structure, if a No. 6 AWG or larger, and not subject to physical damage. If the GEC is going to be subject to physical damage it should be installed in a raceway or cable armor for protection.
Section 250-92 (a) prohibits the use of aluminum or copper-clad aluminum grounding electrode conductors when they are installed in direct contact with masonry, the earth, or where they are subject to corrosive conditions.
Another important restriction for aluminum or copper-clad aluminum GEC’s is the prohibition against their use outdoors within 18 inches of the earth. This requirement effectively precludes the use of aluminum or copper-clad aluminum for connection to “made” electrodes installed outdoors.
Size:
The size of the grounding electrode conductor is based on the size of the largest service-entrance conductor that supplies the building or structure. When the service conductors are installed in parallel, the size of the GEC is based on the size of the equivalent area of a single conductor.
For example, if a 3-phase, 4-wire service consists of two, 500 kcmil conductors per phase, in parallel, the size of the GEC would be based on the equivalent area of a single phase,1,000kcmil,( 500kcmil x 2 conductors). Table 250-94 of the NEC contains the minimum size for aluminum, copper-clad aluminum and copper grounding electrode conductors.
The table includes sizes for circuits from No. 2 AWG copper and No. 1/0 AWG aluminum up to 1100 kcmil copper and 1750 kcmil aluminum or copperclad aluminum. Designers and installers of electrical systems should note that no matter what the size of the service, the GEC is never required to be larger than a 3/0 AWG copper or a 250 kcmil aluminum or copper-clad aluminum conductor.
The reason for this limitation is that the grounding electrode is unable to dissipate any more current into the earth than can be carried by these conductors. So even if the conductor size were increased, the effectiveness of the grounding electrode system would not be improved.
There may be particular applications where design personnel oversize the grounding electrode conductor because of the size of the facility or the nature of the equipment which may be used in the facility. For large facilities where outdoor equipment and exposed conductors are used, available fault current and maximum clearing times must be considered. IEEE Std 80 gives guidance for choosing conductor size and material.
The Grounding Electrode
Many different types of grounding electrodes are available, some “natural” and some “made”. The natural types include metal underground water pipe, the metal frame of the building (if effectively grounded), copper wire or reinforcing bar in concrete foundations or underground structures.
“Made” electrodes are specifically installed to improve the system grounding or earthing. Made electrodes include rods or pipe driven into the earth, metallic plates buried in the earth or a copper wire ring encircling the structure. Note that underground gas piping is not permitted to be used as a grounding electrode. Likewise, aluminum electrodes are prohibited by the NEC.
Other rules for the above electrodes also may apply. Those in effect at the time of this writing include:
Rule #1
All water pipe electrodes must be in contact with the earth for at least 10 feet and must be supplemented by an additional electrode as listed above. (If the water pipe happens to be disconnected or if a section of plastic pipe is installed at a later date, the supplemental electrode would still be effective.)
Rule #2
The copper conductor in the concrete foundation or footer must be #4 AWG or larger and must be at least 20 feet if it is to be used as a grounding electrode. If rebars are used, they must be 1/2 inch (#4) or larger, bare or coated with an electrically conductive material and at least 20 feet long. The foundation must be in direct contact with the earth.
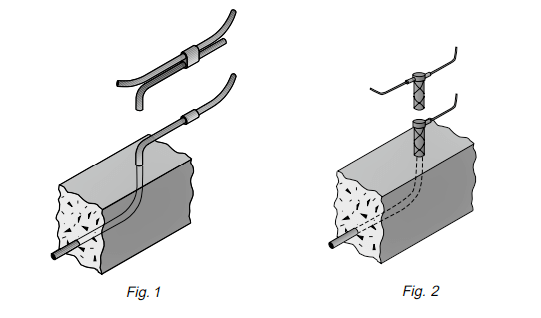
This type of electrode is commonly called a “Ufer Ground”. (A plastic sheet must not be used to separate the concrete from the earth.) Figure 1 shows a #4 AWG or larger copper wire imbedded in the concrete foundation. Figure 2 shows a #4 (1/2”) or larger rebar imbedded in the concrete foundation. CADWELD Connections are used to make permanent connections to either the copper wire or the rebar.
Rule #3
The copper wire ground ring encircling a building or structure must be #2 AWG or larger, at least 20 feet (6 m) long and buried at least 2 1/2 feet (.76m) in the earth.
Rule #4
Rod or pipe electrodes shall be at least 8 ft long with a minimum of 8 feet in contact with the earth, installed vertically except where rock is encountered, in which case they may be driven at a 45o angle or buried in a trench 2 1/2 feet deep. The upper end of the rod or pipe must be flush or below grade unless the top end and the connector are protected from damage.
Pipe electrodes shall be 3/4 inch trade size or larger and shall have their outer surface galvanized or another metal coating for corrosion protection. Rod electrodes shall be 5/8 inch diameter if of iron or steel. Stainless steel rods less than 5/8 inch and nonferrous rods, including copper clad steel rods, shall be listed and not less than 1/2 inch diameter.
Rule #5
Plate electrodes must be at least 1 square foot (0.093 square meter) and 1/4 inch (6.3 mm) thick if steel or 0.06 inch (1.5 mm) thick if nonferrous. Note the plate thickness required by the NEC is different than that required for lightning protection. Burial depth is not specified by code. If used, we suggest that to get the best performance, it be installed on edge and with the top at least 18 inch (460 mm) below grade. Plate electrodes, however, are not as efficient as most other types of electrodes and are usually used only in special conditions where other types of electrodes cannot be used.
Recommended practice is to install the electrodes and interconnecting conductors 18 inches (460 mm) beyond the roof drip line. This provides additional moisture to reduce resistance.
The electrodes used to ground lightning protection systems shall not be the same ones used for the electrical system ground electrodes but the electrodes from both systems must be bonded together. Not only required by the NEC but also required for safety of all who may come in contact with the electrical system, all grounding electrodes must be interconnected.
Separate and isolated ground systems are dangerous and are not permitted! While separate and isolated ground systems were once specified for many electronic systems, this practice has been shown to corrupt the data, damage the equipment and in addition can be extremely dangerous.
Ground Rods
Ground rods are commonly available as copperbonded steel and galvanized steel. Solid stainless steel, solid copper and occasionally plain steel are also utilized. Rods are also available with a factory welded pigtail (Fig. 3). While copper bonded steel rods have a slightly lower electrical resistance than galvanized or plain steel rods, they are not chosen for their lower electrical resistance but rather for their resistance to corrosion.
Copper is a more noble metal than steel and will therefore resist corrosion much better than steel, or even galvanized steel in most soils. (Fig. 3)
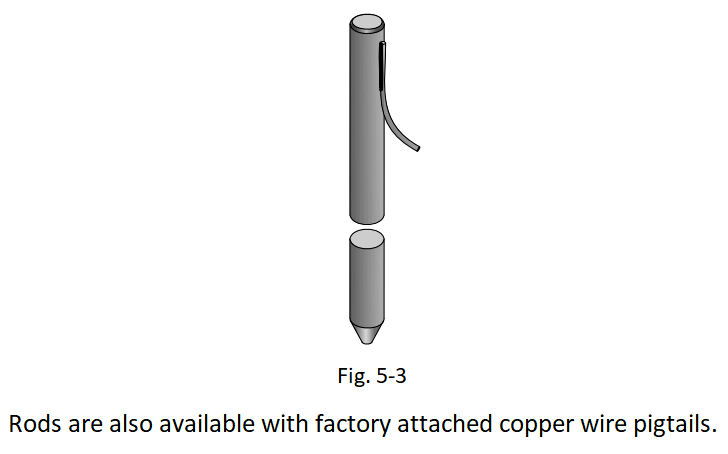
However, when copper is interconnected electrically to steel in the presence of an electrolyte, the steel will corrode to protect the copper. Since the ratio of steel to copper in the grounding system is usually large, the amount of steel corrosion is usually so small it can be neglected.
However, in cases where the steel to copper ratio is small, the corrosion aspect must be considered, for example as in a pole having both a ground rod and a guy anchor. These may be electrically connected. If the guy anchor is steel and the electrode is a copperbonded rod, an insulator in the guy wire should be used to break the electrical interconnection. Otherwise, galvanic corrosion on the guy anchor may occur.
If the soil resistivity is very high, a backfill material is used around the ground rod to lower the system resistance. Care must be considered in choosing the material used. It should be of a material compatible with the ground rod, conductor and connection material.
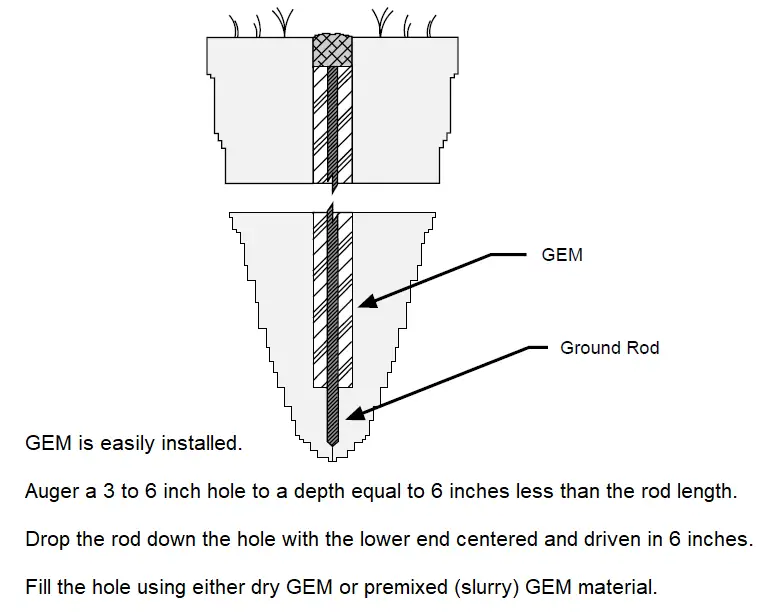
Fig: 4
Often, one ground rod will not provide the ground resistance required for the particular installation. The NEC requires the ground resistance with one rod, pipe or plate electrode to be 25 ohms or less. If it is over 25 ohms, a second electrode is required, connected to the first electrode and separated by 6 feet or more. The resistance of the two electrodes does not have to meet the 25 ohm maximum resistance requirement.
More often, a maximum resistance is called out in the job specifications. This may be 5 ohms or sometimes as low as 1 ohm. Depending on the earth resistivity at the site, a low resistance may be difficult to acquire.
There are several ways to lower system ground resistance:
Use multiple rods
Unless the surface layer of soil (top 8 to 10 feet) is of a relatively low resistance, the use of multiple rods may not be effective. Multiple rods should be separated 8 to 10 feet for maximum efficiency and economy requiring a larger area which may not be available.
Use deep driven rods
Many high resistance sites have a high resistivity soil in the upper levels (for example a rocky surface) but a lower resistivity at lower levels. Deep driven rods will reach this low resistivity layer.
Sometimes it is necessary to drive 100 to 150 feet to reach this low resistivity layer. Since a continuous rod cannot be installed, the method of splicing the rod sections must be carefully examined. The methods available are threaded couplers, compression (threadless) type and welded type.
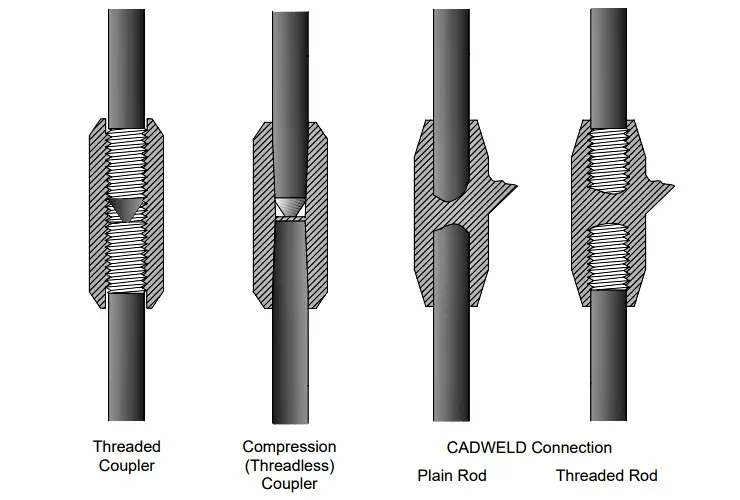
Fig: 5
Although the welded type are more expensive, they assure that the couplings will not become a high resistance member in the current path over the life of the system. One loose coupling will render all of the lower rod sections useless.
Also available is a connection which is a combination of a screw coupling and a welded coupling. After the screw coupling is installed, two CADWELD connections are made to weld the coupling to both the top and bottom rods. (Fig. 6)
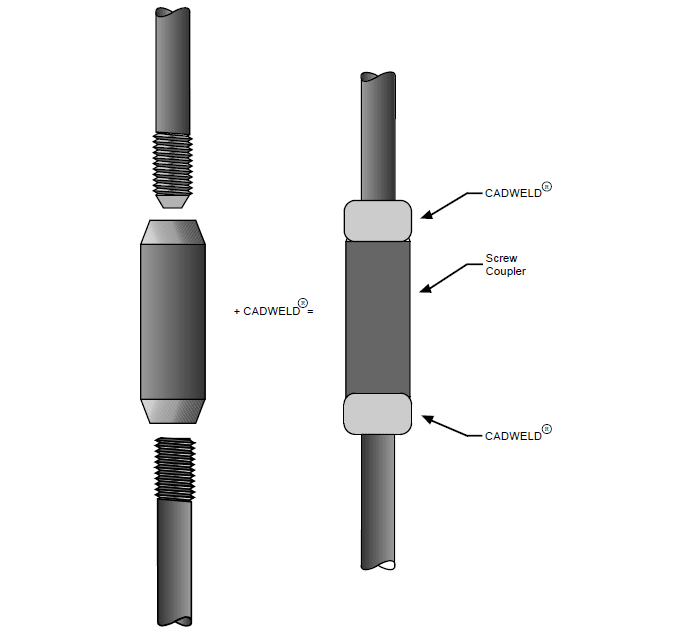
Fig: 6
When using deep driven rods to reach soils of low resistance, tests have shown that the rods do not have to be separated more than 10 feet for maximum efficiency. This is probably due to the fact that only the lower 10 feet of rod is in the lower resistance soil.
Use a Ground Enhancement Material
Several materials are available to lower the resistance of the installed rod electrode. They are placed around the rod which has been installed in an augured hole. Although they have a resistivity higher than the metal rod, their resistivity is lower than the surrounding soil. This, in effect, increases the diameter of the rod.
Following are some of the materials commonly used as ground enhancement materials along with their resistivities;
- concrete : 3000 to 9000 ohm-cm (30 -90 ohm-m)
- bentonite (clay) : 250 ohm-cm. (2.5 ohm-m) (Shrinks and looses contact with both rod and earth when it dries)
- GEM™ : 12 ohm-cm (0.12 ohm-m) or less. (Permanent, sets up like concrete and does not shrink or leach into soil)
Use a Chemical Type of Grounding Electrode
Several makes of chemical types of ground electrodes are available. They are essentially a copper pipe with holes in it. The pipe is filled with a salt, such as magnesium sulfate. The salt slowly leaches from the holes in the pipe infiltrating the soil. The salts must be periodically replaced for the electrode to remain effective. Also, the Environmental Protection Agency (EPA) may object to adding salts to the soil.
Use a Salt Around the Rod
Adding salt to a trench around the ground rod is an inexpensive method to add salts to the soil. The salts must be periodically renewed. The EPA may also object to this method. Some salts may corrode the grounding conductors. This approach to lowering the ground resistance is not recommended.
Connections
The connections to the ground rod can be as important as the rod itself. (Connectors are discussed further in the following section.) Often, a large conductor is connected to one or two ground rods. In many cases, this is a mismatch since the rod cannot carry as much current as the conductor.
Table -1 lists the equivalent copper conductor size for various rod sizes based on fusing formulas.
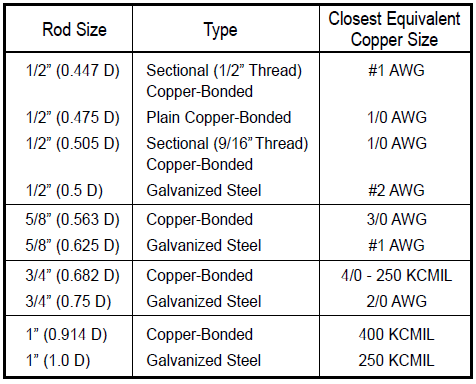
Table: 1
One must also consider the current flow into the rods. If the current heats the surrounding soil to 100o C or higher, the moisture evaporates and the soil resistivity increases. The maximum one second fault current for a 5/8” x10’ ground rod in 100 ohm-meter soil is 27 amperes to limit the temperature to 60o C. (Ref IEEE Std 80-1986)
In areas where the amount of available land is limited and the soil resistivity is high, the use of multiple rods with interconnecting conductors will lower the system resistance. When this is not sufficient, using GEM around either the rods or the conductors, or both, should be considered. (Fig. 4)
Connectors
For most connector applications there is a choice of good – better – best. This choice depends on required life, expected corrosion, expected level of current (lightning and faults) and total installed cost. Grounding connections carry little or no current until a fault occurs. Then, the currents can be very high and the likelihood of detecting a damaged connector is low since many of them are concealed.
The result is system degradation or failure. For connectors hidden behind walls or in the ground, there is no way to determine if something has degraded. Failure of even one connection point in a grounding network may be dangerous, yet go undetected for years.
Connectors are listed in Table -2 showing relative cost, installation time, applicable tests and codes, and recommendations where they should not, in the author’s opinion, be used. The final decision is up to the designer!
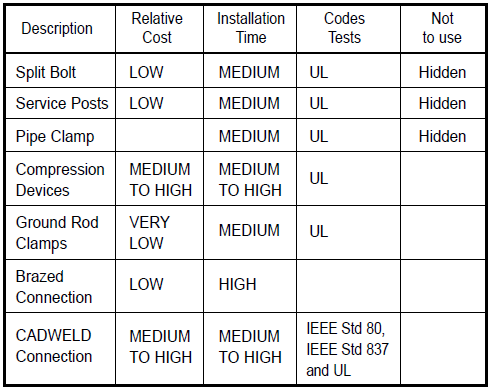
Table: 2
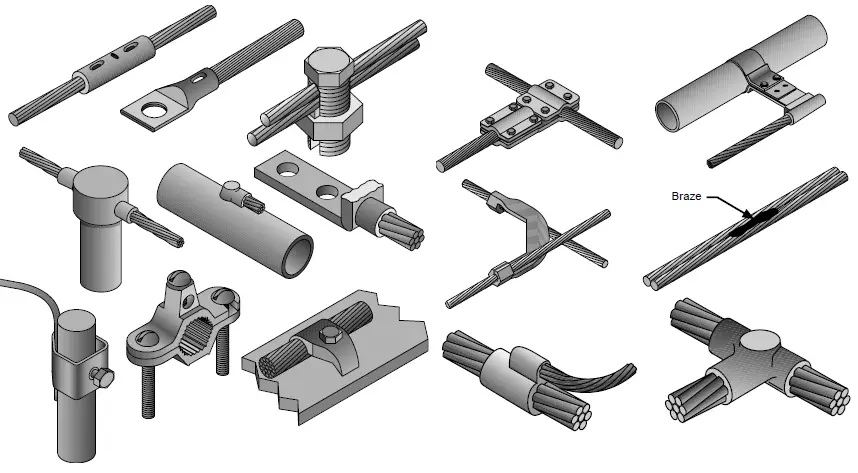
Fig: 7
Do you face any problems with grounding? Share with us.
Reference: erico
Read Next:
- Grounding Electronic Equipment
- Floating Versus Grounded Voltage
- How to Avoid Bad Grounds?
- Measurement of Earth Resistance
- Types of Instrument Earthing