An Allen-Bradley SLC500 programmable logic controller (PLC) uses a 16-bit analog-to-digital converter ( in its model 1746-NI4 ) in analog input card to convert 4-20 mA signals into digital number values ranging from 3277 (at 4 mA) to 16384 (at 20 mA).
However, these raw numbers from the PLC’s analog card must be mathematically scaled inside the PLC to represent real-world units of measurement, in this case 0 to 700 GPM of flow.
PLC Analog Input Scaling
Formulate a scaling equation to program into the PLC so that 4 mA of current registers as 0 GPM, and 20 mA of current registers as 700 GPM.
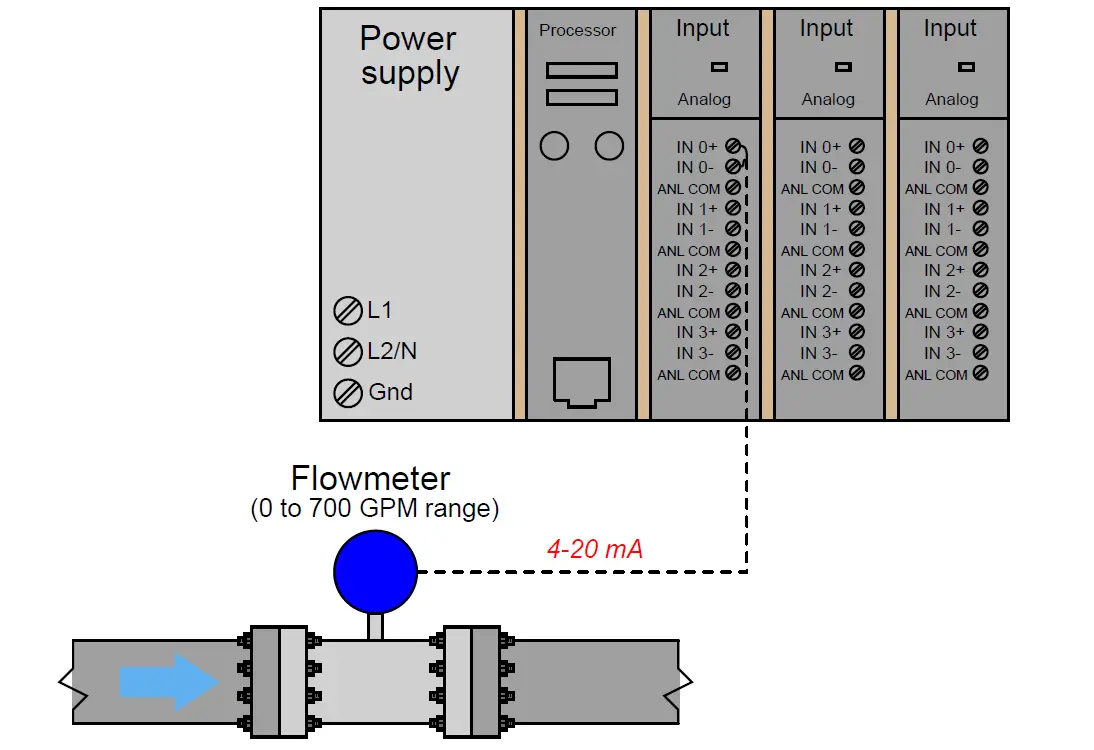
We are already given the raw number values from the analog card’s analog-to-digital converter (ADC) circuit for 4 mA and 20 mA: 3277 and 16384, respectively.
These values define the domain of our linear graph:
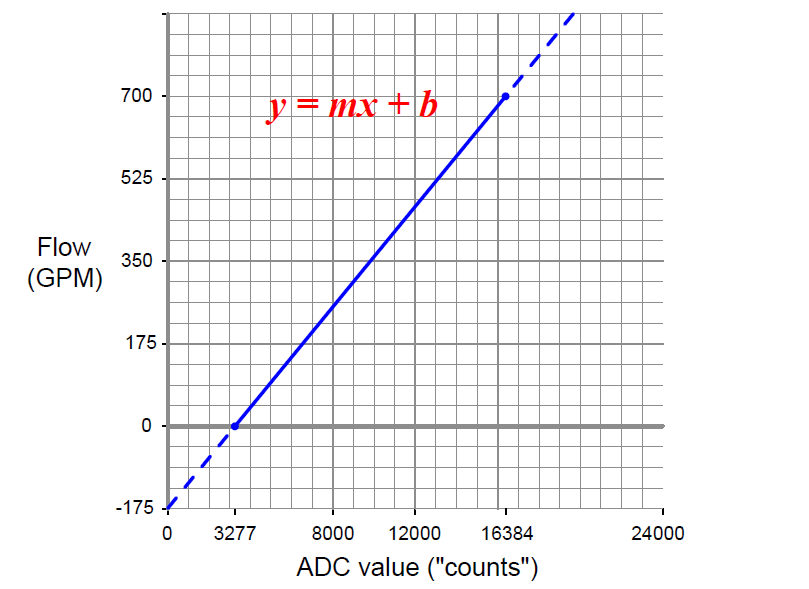
Calculating and substituting the slope (m) value for this equation, using the full rise-over-run of the linear function:
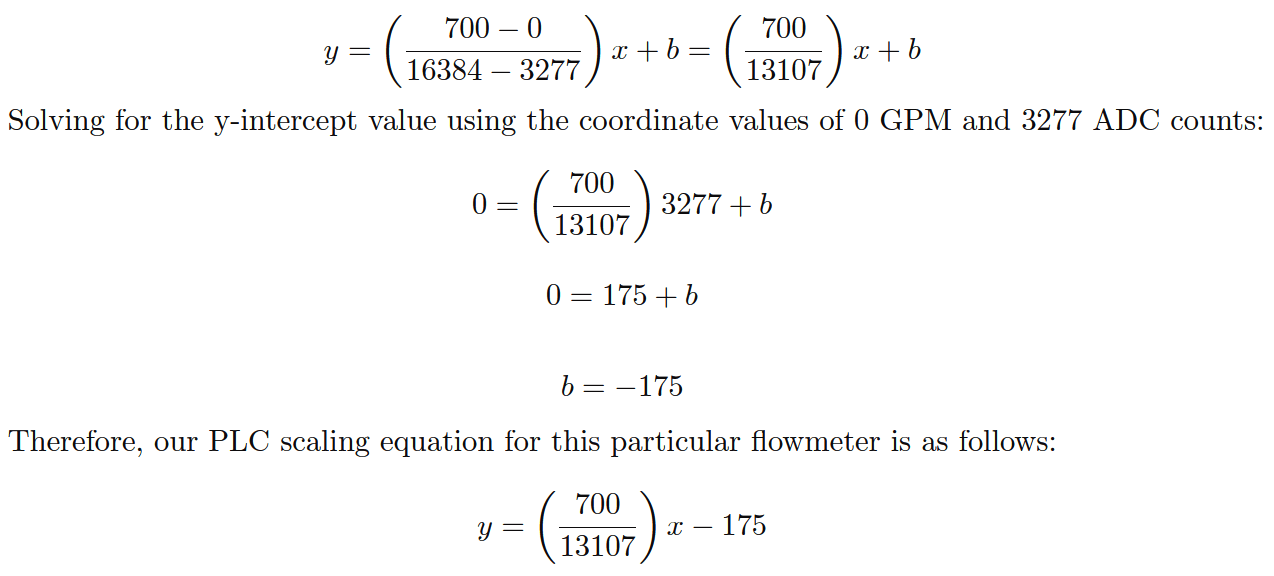
Also Read : PLC Raw Count Calculation
This type of scaling calculation is so common in PLC applications that Allen-Bradley has provided a special SCL (“scale”) instruction just for this purpose.
Instead of “slope” (m) and “intercept” (b), the instruction prompts the human programmer to enter “rate” and “offset” values, respectively.
Furthermore, the rate in Allen-Bradley’s SCL instruction is expressed as the numerator of a fraction where the denominator is fixed at 10000, allowing fractional (less than one) slope values to be specified using integer numbers.
Aside from these details, the concept is exactly the same. Expressing our slope of 700/13107 as a fraction with 10000 as the denominator is a simple matter of solving for the numerator using cross-multiplication and division:

Thus, the SCL instruction would be configured as follows
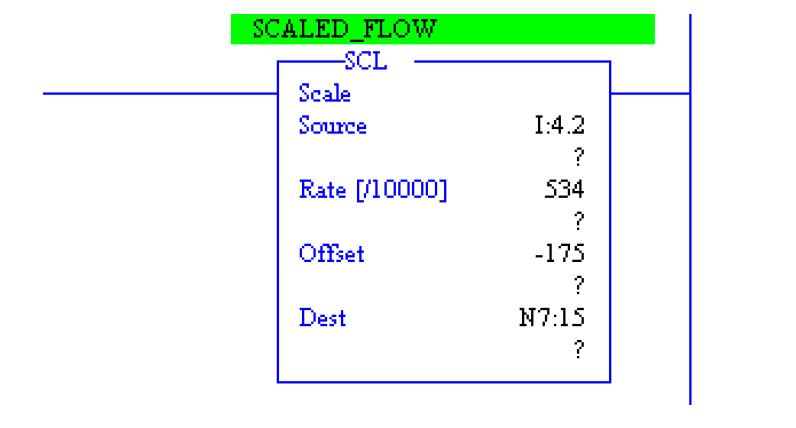
Also Read : 4-20mA Conversion Formulas
Credits : by Tony R. Kuphaldt – Creative Commons Attribution 4.0 License
PLC Tutorials :
What is Programmable Logic Controller ?
What is Ladder Diagram Programming ?
History of Programmable Logic Controllers
Mis-conceptions of PLC Ladder Logic
Contacts and coils in PLC
Digital Input and Output Modules
Analog I/O and Network I/O
PLC Input/Output Modules
Memory Mapping in PLC
Analog Input Scaling
PLC Example with Switches
Counter Instructions
Timer Instructions
Math instructions
Data Instructions
Ladder Logic Questions
If you liked this article, then please subscribe to our YouTube Channel for PLC and SCADA video tutorials.
You can also follow us on Facebook and Twitter to receive daily updates.
thank you
Please tell me 4-20 mA is analog input or analog output in plc /Scada system.
Thanks
Always see the signal from control systems point of view.
Example-
Field transmitters signal is Analog Input to PLC or DCS.
PLC or DCS signal to Control Valves is Analog Output.
Sir please injection moulding plc check
Wow what an information is shared in this platform. I am impressed thank you Inst Tools