In this article, you will learn the important factors for control valve selection and process design parameters in a nutshell.
Control Valve in Nutshell
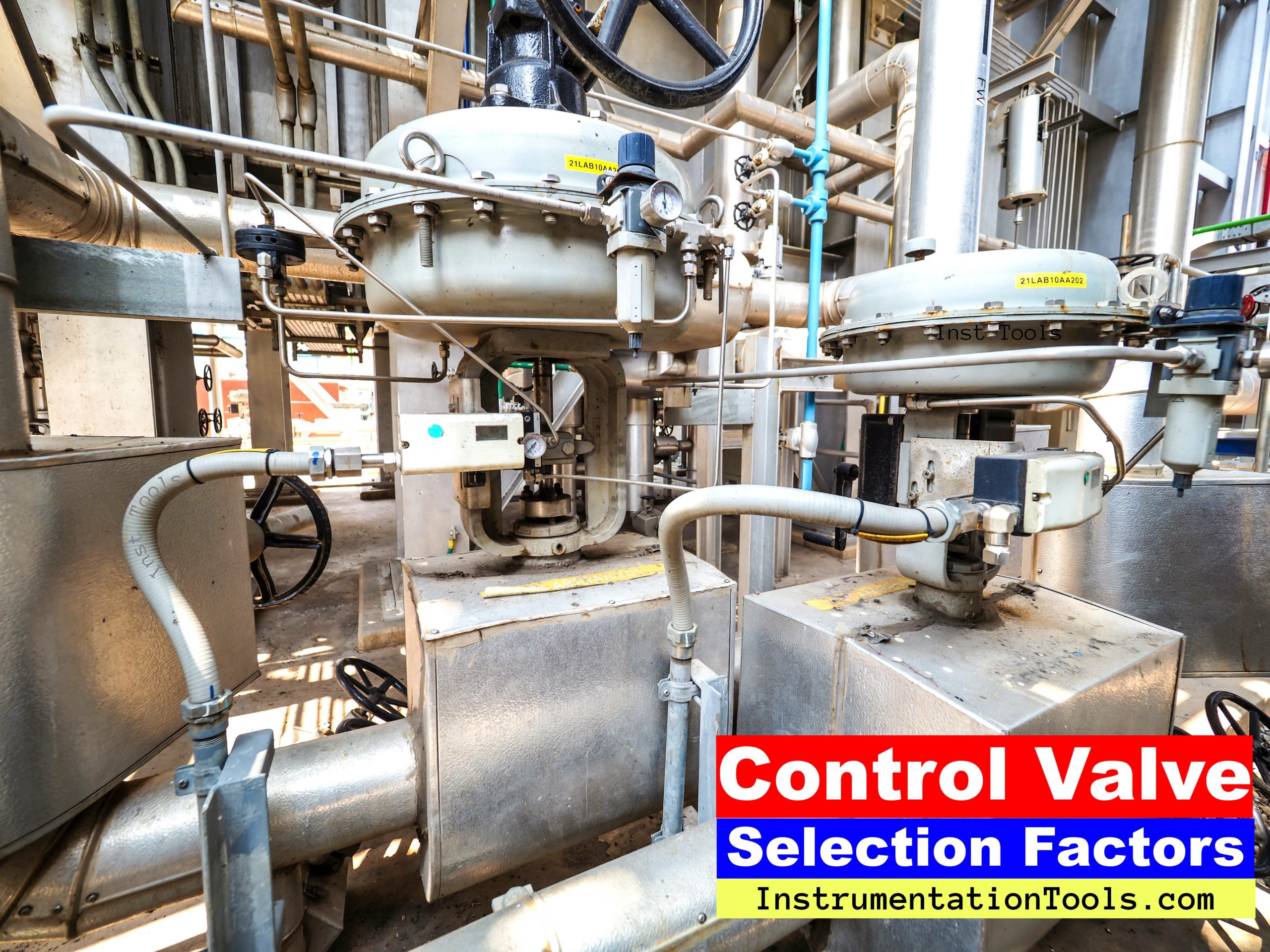
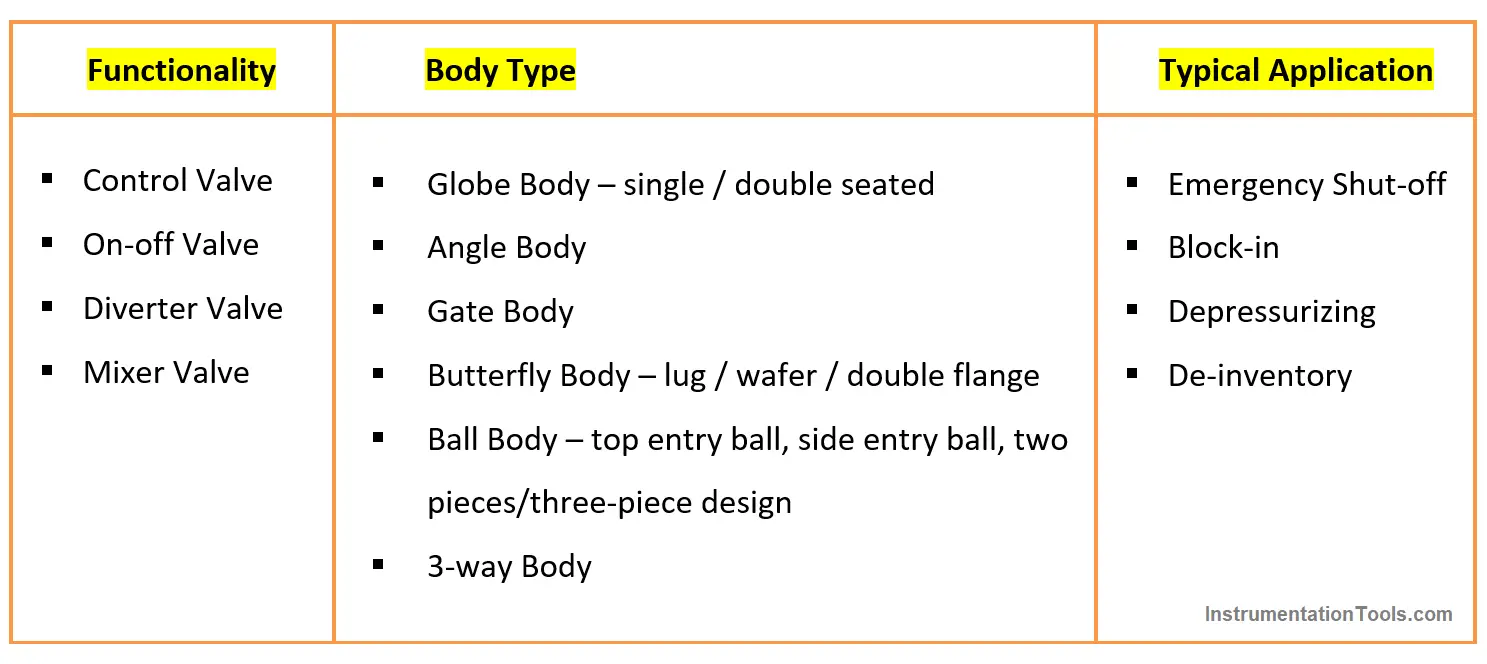
Valve Type | Valve Strength | Valve Weakness |
---|---|---|
Globe Valve | Best suitable for accurate control/throttling service | Permanent pressure drop reasonably high |
Butterfly Valve | Best choice for larger pipe size, low permanent pressure drop, Cv is quite high | Cavitation may happen at low-pressure drop Metal to metal seated type does not provide tight shutoff |
Ball Valve | Best choice for tight shutoff, low permanent pressure drop, Cv is quite higher. Best choice for Shutdown application Low cost | Poor in throttling application Temp limited by seating material for soft seated |
Gate Valve | High capacity, tight shutoff in low cost | Not suitable for throttling application, cavitation at low-pressure drop, slow acting, Bulky |
Angle Valve | Best suit for high-pressure drop application | Piping routing is a major concern i.e. 90° offset between inlet & outlet |
Valve Design Factors
Valve Sizing Concerns | Valve Countermeasures |
---|---|
Cavitation Anti-cavitation valves are Low-pressure recovery design | Globe or angle with hardened trim, specially designed multi-hole/path cavitation trim, or noise abatement trim) shall be used (17-4 pH, 440C, 420SST HT, COLMONOY 6, ALLOY 6). Select a valve with a higher liquid pressure recovery factor (FL) to install a restriction orifice directly downstream of the control valve install two (or more) control valves in series |
Flashing | Use Hard faced trim use harden trim (stellite, 440C, or Colmonoy® 6). Use erosion-resistance body material. Increase valve body size. Use angle valve. |
Noise The major reason for high noise in case of gas service is uncontrolled velocity. Noise in liquid application is mainly due to Cavitation/ flashing. | Source Treatment: Special trim; Larger valve size. Path Treatment: pipe Insulation, Silencers/diffusers |
Inputs and Outputs for Valve Sizing
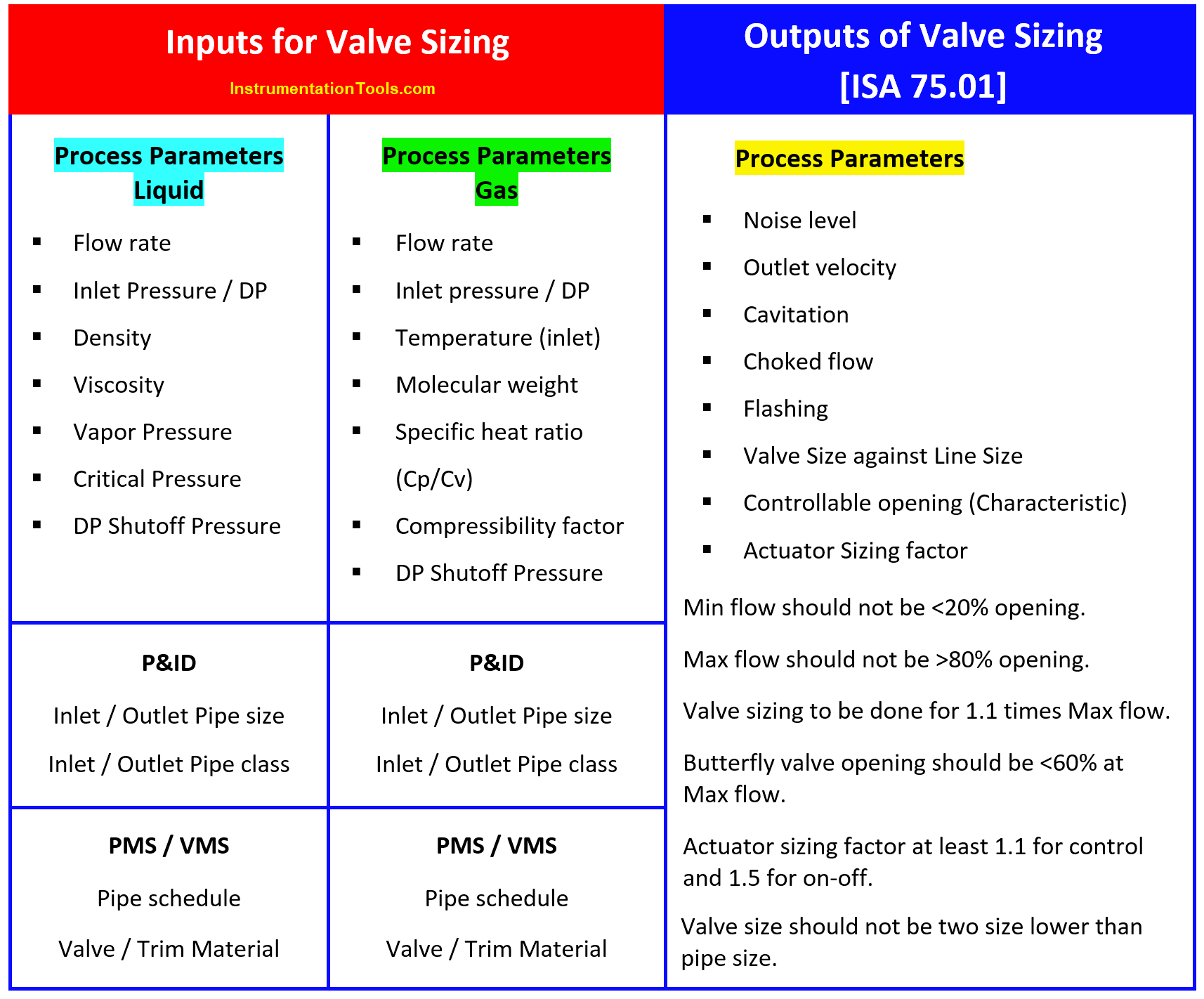
Valve Standards
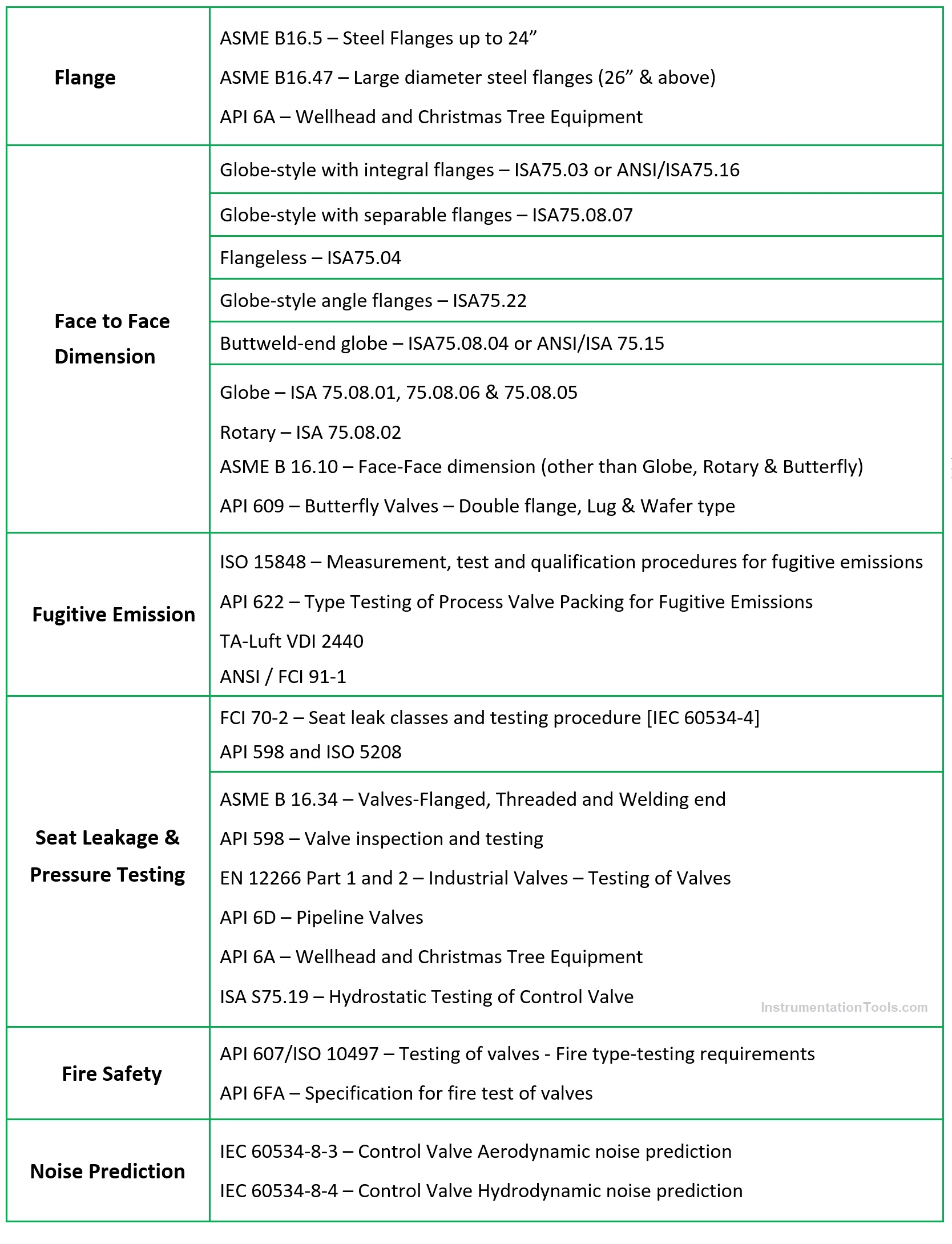
Valve Materials
Valve Body Material example | Carbon Steels – LCB, A216 Gr WCB, WCC, LCC. Alloy Steels – WC9, C5 & WC6. Stainless Steels – 316 SS, 316L SS, 304 SS. Monel is used in oxygen service |
Valve Trim Material Example | SS316, Stellited, SS410, SS420, SS 440, Hardening Treated material |
Valve Hardened Trim Applications
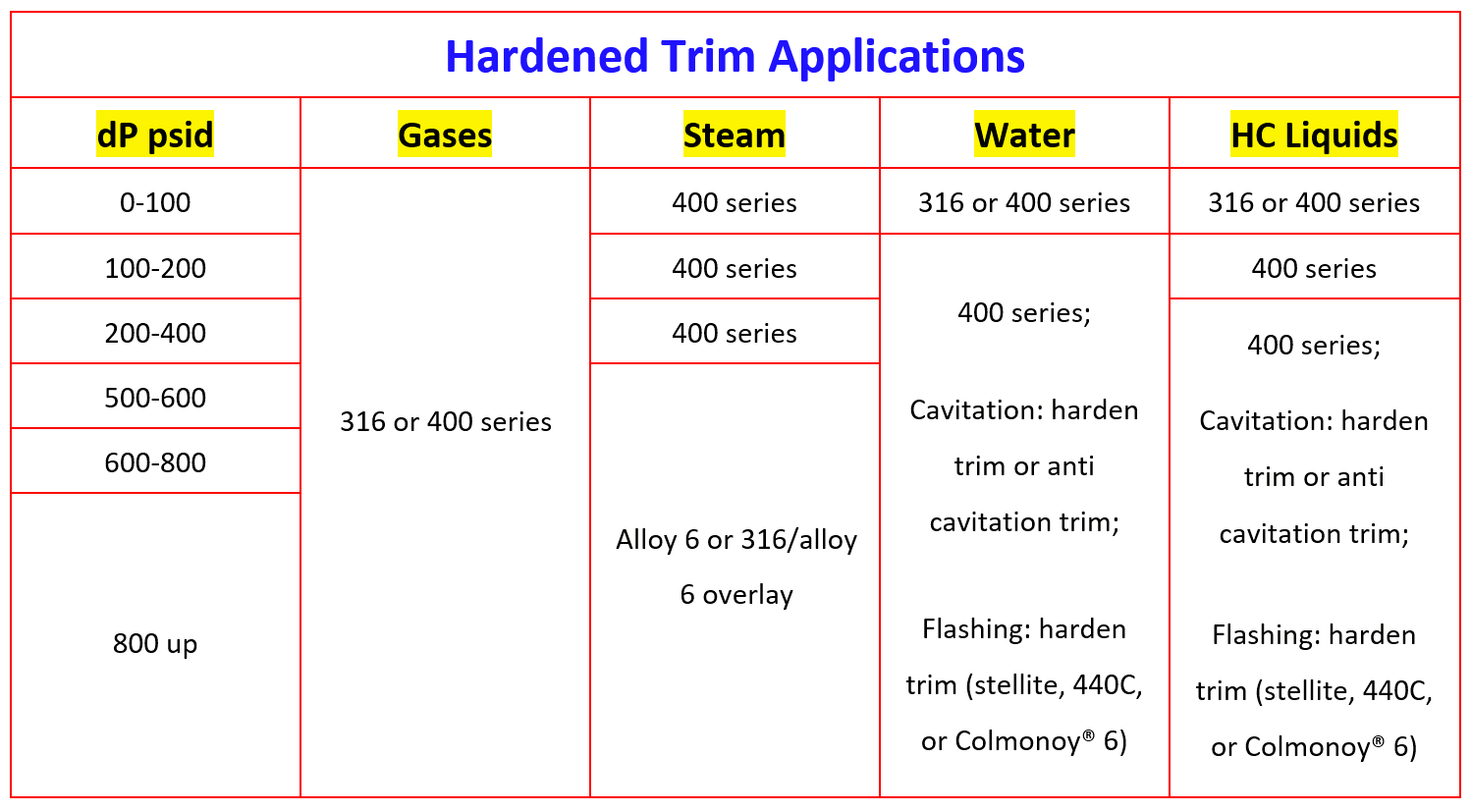
Valve Severe Service Classification
High Turndown | Qmax/Qmin >10 |
High Power Conversion Pa = kg⋅m−1⋅s−2 Flow = m3⋅s−1 Watt= kg⋅m2⋅s−3 | dP(Pa) x Q(m3/sec) >100 kW |
High Noise | >85 dB |
Flashing – Only for liquid | P2<Pv |
Cavitation – Only for liquid | dp/(p1-pv) > 0.38 |
High-pressure drop ratio (choked flow) | dp/p1 > 0.6 |
Body Outlet Velocity Criteria for Valve Sizing
Gas, vapor, and steam | < 0.3 Mach |
emergency depressurizing services Services for which the control valve is closed for more than 4 hours during an 8-hour shift, | < 0.4 Mach |
water service | < 5 m/s |
liquid services other than water | < 10 m/s |
erosive fluid | < 5 m/s |
FL: Rated liquid pressure recovery factor (dimensionless) Globe-style valves generally have low-pressure recovery capability (means FL is higher). The chance of cavitation is low. Butterfly valves generally have high-pressure recovery capability (means FL is lower). The chance of cavitation is high. |
xT Rated pressure drop ratio factor (dimensionless) Globe valve has a higher xT value Ball and Butterfly have lower xT Value Valves with a high xT value can cope with greater differential pressures than ball or butterfly valves. |
FP: Piping geometry factor (dimensionless), should be >0.5. Fp equals unity for the case of valve size equal to line size. The pipe size is, for different reasons, frequently bigger than the nominal size of the control valve. The control valve is installed with reducers and expanders. The reducer will increase pressure drop. If DP increases, we can have less Cv which is due to the reducer effect. To compensate for this, Cv values are further increased by the Fp factor. |
Expansion factor Y: Expansion factor (ratio of flow coefficient for gas to that for a liquid at the same Reynolds number). This factor accounts for the reduction in flow rate that occurs when the Differential pressure ratio (∆p/p1) increases. The typical value is between 0.67 to 1 |
Fd Valve style modifier (dimensionless): depends exclusively on the trim type and the shape of the throttling area. Fd value of 1.0 can be used for valves with one single flow passage. Fd value of 0.7 can be used for valves with two flow passages, such as double port globe valves and butterfly valves. |
Valve Selection Factors
For liquid sizing calculations with given process data and calculated Cv, if the viscosity of the liquid is increased (keeping other parameters constant), the Cv will increase.
For a given sizing calculations with given process data and calculated Cv, if now DP across the valve is increased (keeping other parameters constant), the Cv will decrease.
The angle type is best suited for the very high-pressure drop.
Ball valves are generally used for tight shutoff.
Control valve leakage classes are defined as per ANSI/FCI70.2.
During the “Chocked flow” condition, the further increase in pressure drop will not result in an increase in flow.
Flashing can NOT be eliminated by suitable trim design. Cavitation can be isolated/eliminated
Anti-cavitation valves are Low-pressure recovery designs.
The higher value of the “Liquid Pressure Recovery factor” means Low-pressure recovery.
Valves with noise-reducing trims are inherently having the linear characteristic.
Equal percentage plugs shall normally be used when there are large variations in valve pressure drop whereas Linear characteristic plugs are selected for small variations in valve pressure drop.
Piston actuators are preferred for fast stroking.
Fail Locked (FL) position of control valve with double acting actuator does not require volume tank.
Fail Open / Fail Closed position of control valve with double acting actuator requires volume tank.
17-4 PH material is stainless steel.
Stellite Hard Facing (HF) is a Cobalt-Chromium alloy.
In general, during minimum operating conditions flow is low and DP is high whereas under max operating conditions flow is high and DP is low.
Valve trim seating to meet the classification “TSO” shall be class V or VI
Toxic / Volatile Organic Compounds (VOCs), H2S, and H2 service valve requires special low emission valve packing (Class AH) and/or bellows sealing. Class AH packing is more stringent than Class CH packing.
Minimum acceptable hardness in case of stellited or hardened trim shall be of the order of RC38 (BHN 352) to RC45 (BHN 429).
Generally, valve packing shall be Teflon for temperatures below 200 deg C and graphite for steam services and temperatures above 200 deg C. Graphite-based packing system shall be used for fire-safe applications.
Valve Size shall be limited to no less than half the piping line size.
The use of globe design of valve for valve size more than 12” is not economical. it is preferred to have butterfly valve size of 4” as a minimum.
Kv =0.865 Cv or Cv = 1.156 Kv
Valve Cost Calculator Points
Fireproofing requirement |
Partial Stroke testing requirements |
Local panels for field operation |
Minimum stroke time requirement e.g. anti-surge |
Mechanical stopper |
Fugitive emission packing requirement |
Special accessories like volume booster, airlock, Volume tank, Safety valve |
Special Valve Testing requirements such as Bend test, Magnetic particle test, Positive material inspection, NACE, Helium leak test, Radiography, PWHT, Impact testing, Dye penetration testing, Dead-band / Hysteresis testing Cryogenic Test, Seismic test, Proof of design/type test |
Special Valve Painting requirements |
Special Valve Services such as Anti-surge control (Compressor) Turbine Bypass (Power) Slide Valves, diverter valves (FCC) Double Guillotine Valves / Goggle Valve (FCC) Hot gas bypass (SRU) HIPPS Choke Valves of well fluids CEP, BFP Recirculation Flow (Power) Speed control – Turbine governing valve (Power) HP/LP Bypass Spray (Power) Oxygen service, Vacuum, low-temperature Cryogenic valves, HF, H2S, Steam, H2 services |
Disclaimer: The information shared is intended only for informational & educational purposes. All content mentioned does not constitute professional advice and is not guaranteed to be accurate, complete, reliable, up-to-date, or error-free.
Nice information on Control valve sizing,application,features and on cost also