In this article, we will learn about what is Robot and Robotics, Laws of Robotics, classification and components of robots.
Robot
An industrial robot is a general purpose, programmable machine which are able to do anthropomorphic or human like characteristics. It is designed for the case of multifunctional operations to move materials, parts, tools or special devices through variable programmed motions for the performance of a variety of tasks.
In general, robots are designed and meant to be controlled by a computer or similar device. The motions of the robots are controlled by the controller under the supervision of computer with the help of programs.
Thus, the programming feature allows robots to be used for a variety of industrial operations.
Robotics
Robotics is an interdisciplinary field that deals with mechanical engineering, electrical and electronics engineering, computer science, cognitive sciences, nano technology, biology and many other disciplines.
It is an art, knowledge base and also skill of designing, applying and using robots in human workplaces. Robotic systems consist of not just robots, but also other devices and systems used together with robots.
Nowadays, robots are used in applications of manufacturing environments, medical field, marine technology and even in defense sectors.
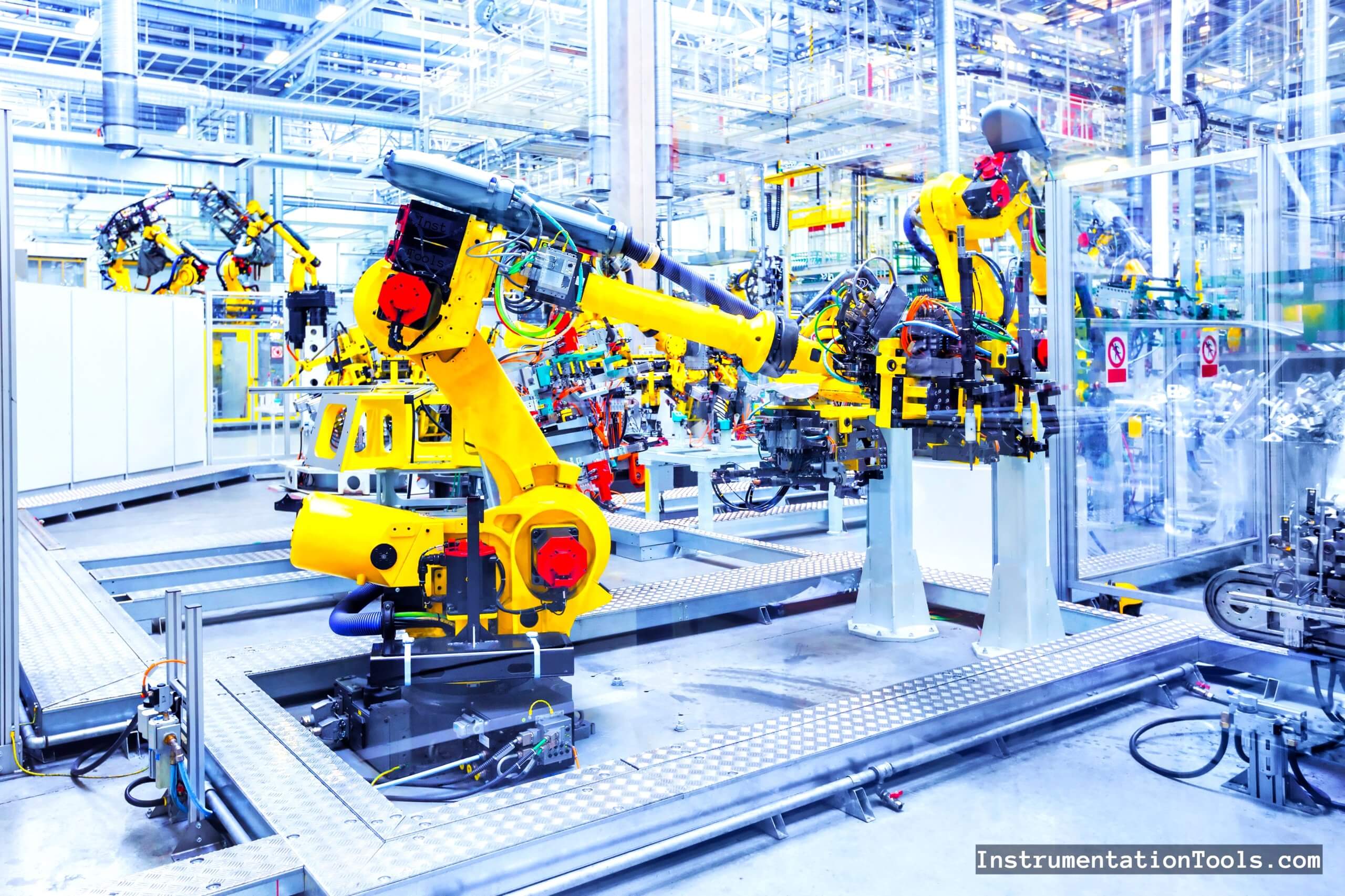
Laws of Robotics
A robot that appears in workplace want to be well designed, fail-safe machine that performs according to three principles.
These principles were called the Three Law of Robotics and they are:
- A robot may not injure a human being or through inaction, allow a human to be harmed.
- A robot must obey orders given by human except when that conflicts with the first law
- A robot must protect its own existence unless that conflicts with first or second law.
Classification of Robots
According to the Japanese Industrial Robot Association, robots are classified into six classes.
They are:
Class 1 – Manual Handling Robot
Manual Handling Robot has multiple degrees of freedom, actuated by an operator.
Class 2 – Fixed Sequence Robot
A bot that performs the continuous task according to the situation and condition applied on it. It uses a constant sequence which is hard to modify.
Class 3 – Variable Sequence Robot
Variable Sequence Robot also performs continuous tasks as situation applied but one main difference is it can be modified as it is used for a variety of sequences.
Class 4 – Playback Robot
This category of robot records the tasks performed by the human before and stores the tasks and motions for later playback. The robots will repeat the task and motions according to the recorded information.
Class 5 – Numerical Control Robot
The operator supplies the robot with a movement program rather than teaching it manually.
Class 6 – Intelligent Robot
A robot that can able to understand its work environment and the ability to successfully complete a task though there is a change in the surrounding conditions under which is it to be performed. This type of robot will easily absorb the changes in its work area and work regarding that.
Components of Robot
A robot as a whole consists of the following elements which are integrated together to form a whole.
- Manipulator
- End effector
- Actuators
- Sensors
- Controller
- Processor
- Software
Manipulator
The manipulator is the main body of the robot which consists of the links, the joints, and other structural elements of the robot.
Simply a manipulator is a structure where all other important parts are fixed. Without any other elements manipulator alone is not considered as a robot.
End Effector
This part is connected to the last joint (Hand) of a manipulator that generally handle objects, lift parts, makes connections to other machines, or performs the required tasks.
Generally, the hand of a robot has provisions for connecting speciality end effectors specially designed for a purpose. The end effector is not to be same for all applications, depends on the need designs of end effectors may get vary.
A welding torch, paint spray gun, glue laying device, parts handlers are some of the end effectors used in robots.
Actuators
Actuators are known as the muscles of the manipulators. Robot joints, and links are moved by the actuators only through the signals received from the controllers.
Servomotors, Stepper motors, Pneumatic actuators, and Hydraulic actuators are some common types of actuators used in robots.
Mainly Actuators are under the control of the controller only.
Sensors
Sensors are used to collect information about the internal state of the robot or to communicate with outside environment.
The robot controller needs to know the location of joints or needs to move the actuators depends on the input signal, mainly the input signals were given by the sensors.
These sensors are integrated with robots every part where the actuations need to be done depends on the signal, feedback or process.
Every action for outside environment is by the signal of the sensors only. It may be touch, tactile, vision and so on.
Mostly these sensors will get information and sends that to controller that will make required process to do.
Controller
Controller is like human cerebellum; it does not have the power of brain but it controls all the motions. Through controller only all the motions of the robot were processed.
This controller gets the necessary inputs from all sensory items do the motions of the coordination, actuator or joints links. Without controller, we cannot do the exact robot operations.
For example, we want to move a robot arm for picking and placing an object from one place to other in that we need to change the motion of the arm from 90⁰ to 45⁰, controller sends the signal to actuator for rotation of 45⁰ after reaching the point it picks the object as the sensor sends the feedback signal to the controller so again it will move to home position of 90⁰. Like this controller makes every action in the robots.
Processor
Processor is considered as the brain of robots. It calculates all the motion, it calculates how much speed was needed for moving to the destination point, checks the coordination points for the function.
The processor is generally a computer which is specially made for the desired robots. It requires operating system, monitor and other peripheral for controlling the operation.
In some systems both controller and processor were integrated as one but in some systems, they will be separated. Depends on the user requirement the processor is chosen.
Software
Mainly three group of software are used in robots. They are Operating system, robotics software and applications-oriented programs. Operating system is used to operate the processor.
Robotic software is used to calculate the necessary motion of each joint based on the kinematic, inverse kinematic equations of the robot. This information is sent to the controller.
This robotic software has different levels from machine level language to high level language used by high tech robots.
Last application-oriented programs were developed for the specific routine work or tasks like assembly, machine handling, pick and place and vision systems.
Advantages of Robots
- Robots can work in hazardous environments such as radiation, darkness, hot and cold areas even in ocean bottoms without life support, comfort.
- Robot usage can increase productivity, safety, efficiency, quality and consistency of products.
- Robots need no environmental comforts like lighting, air conditioning, ventilation and noise protection.
- Robots can work continuously without tiring or boredom
- Robot have repeatable precisions at all times.
- They can work more accurate than humans in every environment.
- Robots can perform multiple tasks at a time but human can perform single task at a time.
Disadvantages of Robots
- Though it is more accurate than humans but it lacks the capability in responding to emergency situations
- Inappropriate or wrong responses may cause several loss to the work environment.
- The replacement of human workers with robots may cause economic hardship in the society
- Its initial installation, training, and other peripherals were very costly.
- Only trained personnel were able to operate this.
- Robots have very limited capability in real-time response because they will work with the stored programs it can’t work beyond that.