In this post, we will see the concept of Electro deionization (EDI) in a water treatment plant.
Water treatment plants are used to convert bad wastewater into drinkable or usable water. The quality of the water coming out of these plants need to be maintained for proper human use.
Such plants are used in almost every industry; as quality water demand is a must for the personnel to use or machines to operate.
The water content is monitored by various types of sensors, which help in maintaining the final output. Without them, it is impossible to operate the plant.
Many components are used in a water treatment plant to treat bad water. One such component is EDI (Electro deionization).
In this post, we will see the concept of EDI used in water treatment plants. It is one of the most essential components used in these types of plants.
Why EDI is required?
Conductivity means the ability of water to conduct current. It is one of the important criteria in determining water quality. Low conductivity means lower the ability of water to conduct electricity and such water is of pure quality.
This is because, in contrast, if water has ions from dissolved salts and other inorganic materials like chlorides, sulfides, carbon compounds, etc. (means dissolved impurities), it will conduct current due to the large presence of ions.
So, higher conductivity means higher the ability of water to conduct electricity and such water is of poor quality.
To minimize the effect of conductivity, EDI is used. EDI is used after the RO process for polishing demineralized water to obtain low levels of conductivity and silica.
What is Electro deionization?
As the name implies, EDI (Electro deionization) means to remove ions from the water through electrical means.
It uses electricity, ion exchange membranes, and resins to remove ions and other charged species from water; like salts and organic acids.
It is the best alternative to a conventional mixed bed polisher. EDI is a continuous process with no downtime required, due to electrochemical regeneration.
Working of EDI
Refer to the above image. EDI is nothing but a chamber of membranes. The light blue and orange color lines represent semipermeable cationic exchange and anionic exchange membranes.
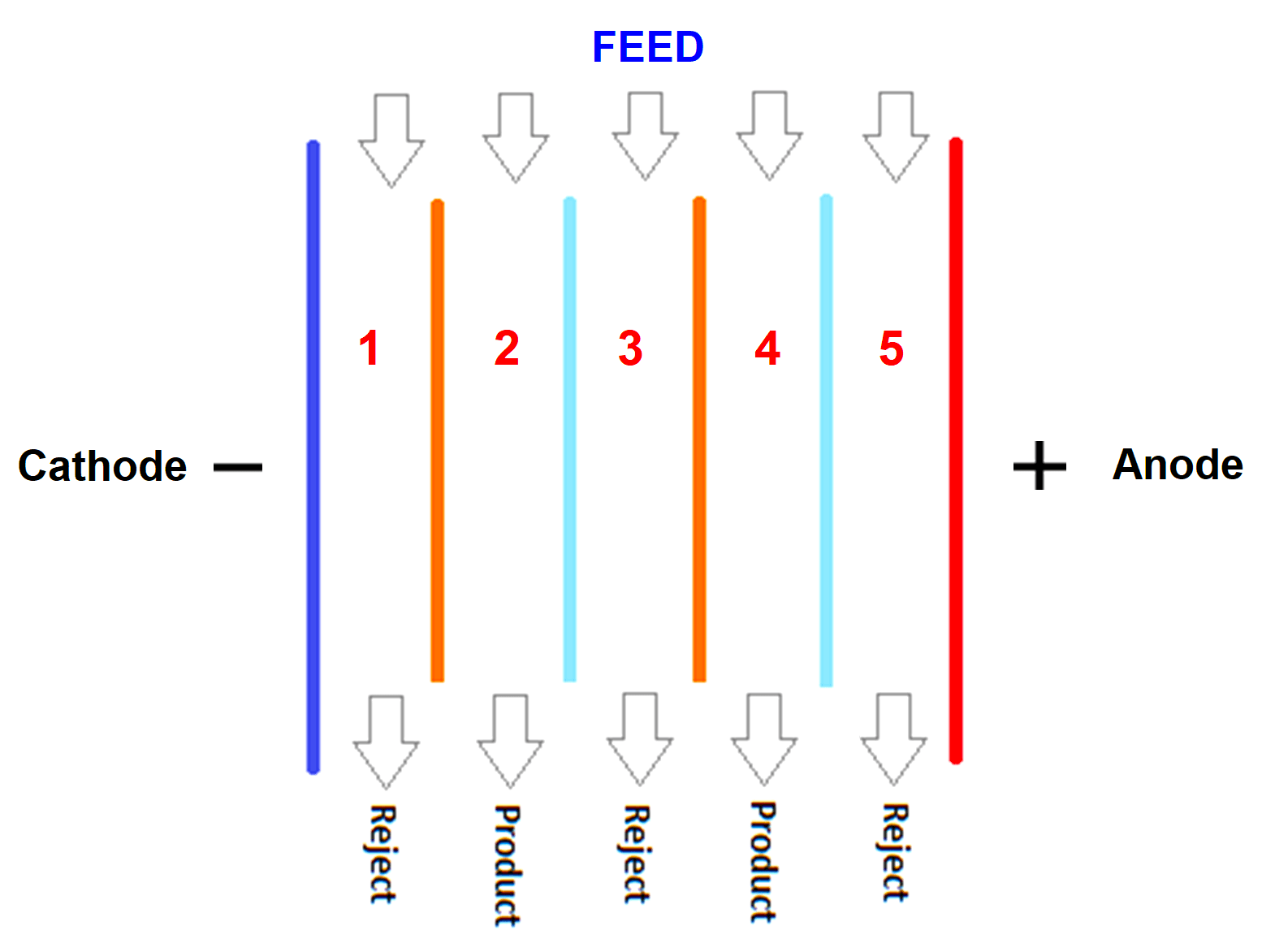
One special feature of this membrane is that only ions can pass through it, and not water. Between these membranes, water flows from the feed line to either reject line or the product line through the resins between membranes.
A DC electrical field is applied by an external power source using electrodes at the end of membranes.
Now, let us start the control flow. Consider that you have applied electrical power to the electrodes. You have also started the flow of impure water from the feed. This water will contain both the negative charged and positive charged ions.
Let us start with the first line. Negative ions will flow through this line as it is and positive ions will also flow through this line as it is (because it will be attracted to negative electrodes).
In the second line, positive ions will be flowing towards the first line and the negative ions will be flowing towards the third line. In the third line, ions will flow as it is to the outlet.
In the fourth line, positive ions will be flowing towards the third line and negative ions will be flowing towards the fifth line.
In the last line, positive ions will flow as it is and negative ions will also flow through it as it is (because they will be attracted to positive electrodes).
Now, you must be wondering how come the ions flow as it is through the third line without being attracted towards any electrode. Here comes the main fundamental of the membranes.
As discussed before, the membranes are cationic exchange and anionic exchange. Cationic exchange membranes in the figure are the orange ones which allow only positive ions to flow. Anionic exchange membranes are the light blue ones that allow only negative ions to flow.
Now, let us go back to the third line. As per electrical attraction, positive ions must have flown to the second line. But, to flow to it, they have to pass through blue lines and the blue membranes are anionic ones that allow only negative ions to flow.
Similarly, negative ions must have flown to the fourth line. But, to flow to it, they have to pass through orange lines and the orange membranes are anionic ones that allow only positive ions to flow.
So, the respective charged particles flow as it is through the third line. These membranes are thus, the special feature of EDI.
So, now, all the concentrated ions are flowing to the reject line and the product line has water with a minimal amount of ions. This means the drain water containing charges has flown towards the reject line.
How is EDI used in Industrial Automation Control?
PLCs are used in water treatment plants and EDI is connected to the PLC through a digital output; for turning it on or off depending upon the control logic. It is also interfaced with the analog output of PLC.
This analog output will apply a variable voltage to the EDI rectifier unit in the control panel, which in turn provides the option of a variable DC voltage from it to the EDI connected in the field.
Through these rectifiers, the PLC can also read the current, voltage, and ampere of the EDI through analog inputs.
In the process scenario, EDI comes after the RO unit. EDI unit is turned on only when the feed water-supplying pump is on. You cannot run the EDI as dry, otherwise, it will damage it.
So, EDI is interlocked with the feed water pump. After EDI, a conductivity sensor is installed to measure the output of EDI; as to what amount of electric charges have been removed from the water.
If the conductivity is still higher, then a diverter valve installed after the sensor will divert the water back to the recirculation line; rather than diverting the water to the product line.
In this way, we saw the concept of EDI in water treatment plants.
If you liked this article, then please subscribe to our YouTube Channel for Instrumentation, Electrical, PLC, and SCADA video tutorials.
You can also follow us on Facebook and Twitter to receive daily updates.
Read Next:
- Process Air Compressor Overhauls
- Heat Exchanger Root Cause Analysis
- Malfunctioning Inlet Check Valves
- Refrigeration Compressor Turbine RCA
- Erratic Stroking Control Valves RCA