A SCADA system refer to a system consisting of a number of remote terminal units (or RTUs) collecting field data connected back to a master station via a communications system.
The master station displays the acquired data and also allows the operator to perform remote control tasks. The accurate and timely data (normally real-time) allows for optimization of the operation of the plant and process.
A further benefit is more efficient, reliable and most importantly, safer operations. This all results in a lower cost of operation compared to earlier non-automated systems. A successful SCADA installation depends on utilizing proven and reliable technology, with adequate and comprehensive training of all personnel in the operation of the system.
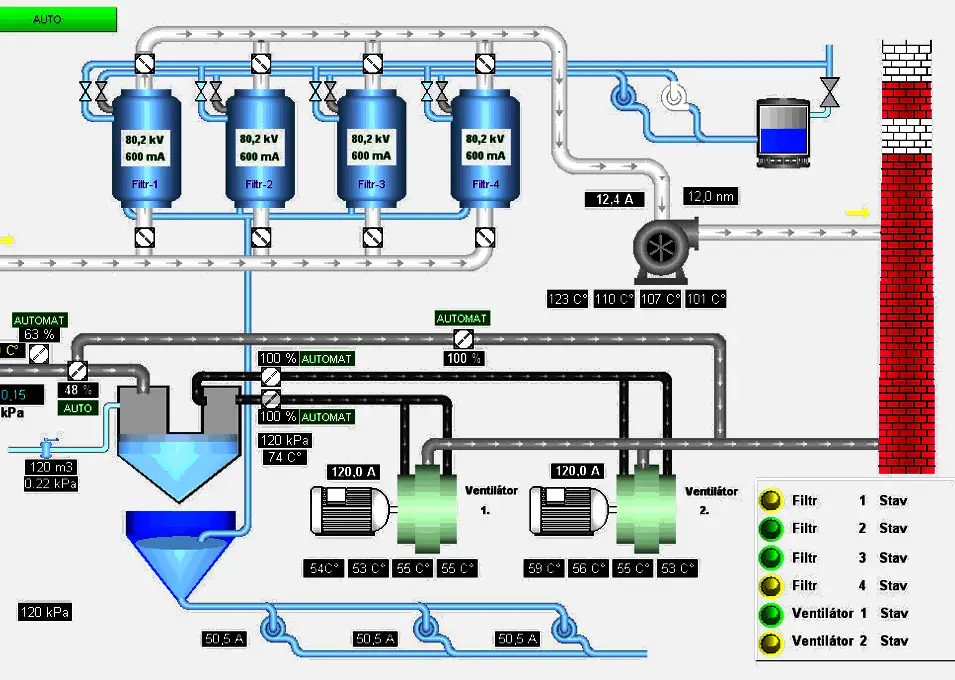
Image courtesy : promotic
There is a history of unsuccessful SCADA systems – contributing factors to these systems includes inadequate integration of the various components of the system, unnecessary complexity in the system, unreliable hardware and unproven software.
Today hardware reliability is less of a problem, but the increasing software complexity is producing new challenges. It should be noted in passing that many operators judge a SCADA system not only by the smooth performance of the RTUs, communication links and the master station (all falling under the umbrella of SCADA system) but also the field devices (both transducers and control devices). The field devices however fall outside the scope of SCADA in this manual and will not be discussed further.
The RTU provides an interface to the field analog and digital signals situated at each remote site. The communications system provides the pathway for communications between the master station and the remote sites. This communication system can be radio, telephone line, microwave and possibly even satellite.
Specific protocols and error detection philosophies are used for efficient and optimum transfer of data. The master station (and sub-masters) gather data from the various RTUs and generally provide an operator interface for display of information and control of the remote sites. In large telemetry systems, sub-master sites gather information from remote sites and act as a relay back to the control master station.
NOTE : In olden days, we call the SCADA system as complete control system with hardware and software to monitor and control the equipment in industries. whereas in modern days we have individual advanced systems like PLC, DCS as control systems and use SCADA for operator interface or called as Human Machine Interface (HMI) or simply as graphical user interface. so do not confuse about the terminology of “SCADA” between olden days and modern days. Below we discuss about the SCADA systems in terms of olden days i.e. as complete control system.
SCADA technology has existed since the early sixties and there are now two other competing approaches possible – distributed control system (DCS) and programmable logic controller (PLC). In addition there has been a growing trend to use smart instruments as a key component in all these systems.
Distributed control system (DCS), is another variant of SCADA where data acquisition and control functions are performed by a number of distributed microprocessor-based units situated near to the devices being controlled or the instrument from which data is being gathered. DCS systems have evolved into systems providing very sophisticated analog (e.g. loop) control capability. A closely integrated set of operator interfaces (or man machine interfaces) is provided to allow for easy system configurations and operator control. The data highway is normally capable of fairly high speeds.
Another variant of SCADA components widely used is the Programmable Logic Controller (PLC). PLCs have replaced hardwired relays with a combination of ladder– logic software and solid state electronic input and output modules. They are often used in the implementation of a SCADA RTU as they offer a standard hardware solution, which is very economically priced.
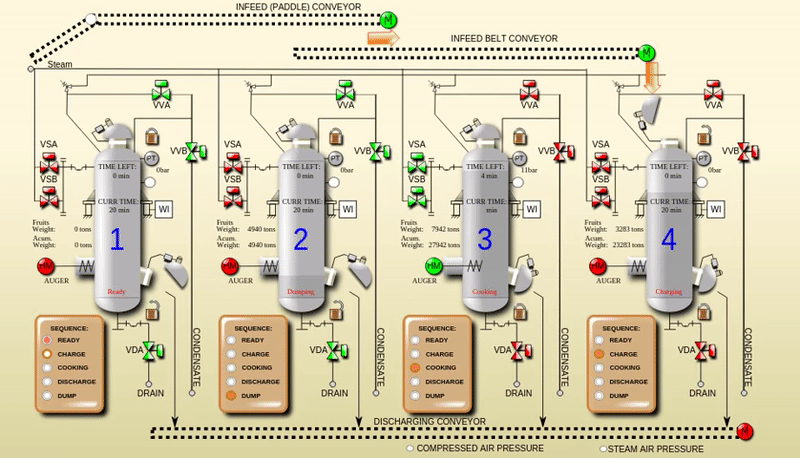
Evolution of SCADA
- 1890’s Remote Control and Remote Indication
- 1920’s Tele-command and control
- 1930’s Check Before Operate (CEO)Systems, Based on Electro Mechanical Technology
- 1960’s Supervisory Control Systems (Remote Control & Status Indication)
- 1960’s Data Acquisitions gaming Popularity (DAS) SCADA came into being.
- 1980’s Load Dispatch Centre and Control
- 1990’s Energy Control Centre
- 2000’s Energy Management Systems
Objectives of SCADA
The important objectives of SCADA are to listed below:
- Monitoring : Continuous monitoring of the parameters of voltage , current, etc..
- Measurement: Measurement of variables for processing.
- Data Acquisition: Frequent acquisition of data from RTUs and Data Loggers / Phasor data Concentrators (PDC).
- Data Communication: Transmission andreceiving of large amounts of data from field to control centre’s.
- Control: Online real time control for closed loop and open loop processes.
- Automation:: Automatic tasks of switching of transmission lines, CBs, etc.
Benefits of SCADA
The important benefits can be addresses as the following functions:
- Continuous monitoring of process.
- Real time control.
- Automation and Protection.
- Remote control and operation.
Elements of the system
The structure of a SCADA system has the following basic components (Figure 1):
- Central monitoring control station: is one or more central servers ( central host computer server ).
- Intermediate data acquisition station: are input blocks of RTU remote terminal ( Remote Terminal Units ) or PLC ( Programmable Logic Controllers ) programmable control blocks with delivery function relay with actuators (field level sensors, switchgear control boxes and actuator valves …).
- Communication system: including industrial communication networks, telecommunications equipment and multiplex switching devices with field-level data transfer functions to control units and servers
- Human interface – HMI machine ( Human – Machine Interface ): is the device that displays the data processing process for the operator to control the operation process of the system.
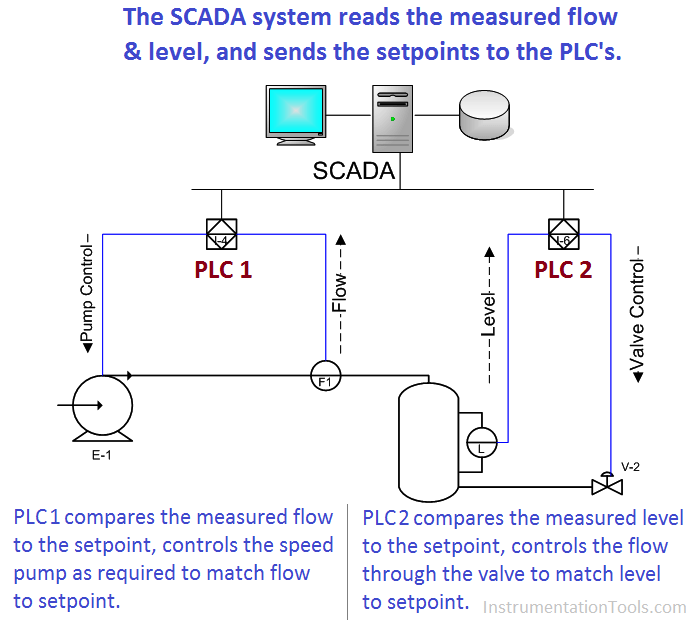
In the SCADA system, the data collection process is performed first in the process of scanning the RTU information obtained from the devices attached to them. The time to execute this task is called the internal scan time. Servers scan RTUs to collect data from these RTUs. To control, the server sends the required signal to the RTUs, thereby allowing the RTUs to send control signals directly to the executing devices.
Data transmitted in the SCADA system can be continuous (analog ), digital ( digital ) or pulse ( pulse ).
Data transmission in SCADA system is shown only in digital form called data field. This digital data is formed from logic signals (on / off), analog / current signals, high-speed pulse signals, ….
The basic interface for operating at the terminal is a GUI ( Graphical User Interface ) screen that is used to display the entire monitoring system or devices in the system. At one point, the data is displayed as a static image, when the data changes, the image also changes.
In case the system data changes continuously over time, the SCADA system often displays the process of changing this data on the graphical interface (GUI) screen in the form of graphs.
A great advantage of SCADA system is the ability to handle errors very successfully when the system occurs. In general, when there is a problem the SCADA system can choose one of the following ways:
Using data stored in RTUs: In SCADA systems, there are RTUs with large memory capacity, when the system operates stably the data will be backed up in the RTU’s memory. Therefore, when the system fails, the RTUs will use this data temporarily until the system becomes normal again.
Use of system redundant hardware: most SCADA systems are designed with additional spare parts, such as two-way communication system, dual RTUs or two servers … thus, These spare parts will be put to use when the SCADA system crashes or works offline (possibly for maintenance, repair, testing, etc.).
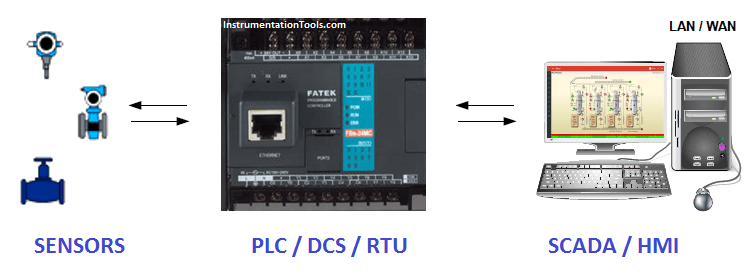
Functions of SCADA
The important functions of an SCADA are listed below.
- Data Acquisition
- Information Display
- Supervisory Control
- Alarm Processing
- Information Storage and Reports
- Sequence of Event Acquisition
- Data Calculation
- Special RTU Processing/Control
Usage of SCADA
SCADA can be used to manage any kind of equipment. Typically, SCADA systems are used to automate complex industrial processes where human control is difficult.
For example in systems where there are more control factors unable to be managed by operators in a control center.
SCADA systems are widely used for control in the following domains
1. Electric power generation, transmission and distribution: Electric utilities use SCADA systems to detect current flow and line voltage, to monitor the operation of circuit breakers, and to take sections of the power grid online or offline.
2. Water and sewage: State and municipal water utilities use SCADA to monitor and regulate water flow, reservoir levels, pipe pressure and other factors.
3. Buildings, facilities and environments: Facility managers use SCADA to control HVAC, refrigeration units, lighting and entry systems.
4. Manufacturing: SCADA systems manage parts inventories for just-in-time manufacturing, regulate industrial automation and robots, and monitor process and quality control.
5. Mass transit: Transit authorities use SCADA to regulate electricity to subways, trams and trolley buses; to automate traffic signals for rail systems; to track and locate trains and buses; and to control railroad crossing gates.
6. Traffic signals: SCADA regulates traffic lights, controls traffic flow and detects out-of-order signals.
Real-Time Monitoring and Control using SCADA
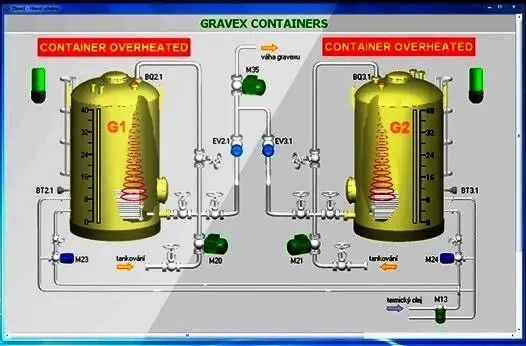
The following are the important features of a SCADA from an control point of view. SCADA is capable of the following
- Acquire quantitative measurements immediately and over time
- Detect, Diagnose and correct problems as soon as they arise
- Measure trends over time and prepare reports and charts
- Discover and eliminate bottlenecks over time and improve efficiency
- Ability to Control large and complex processes with a few specialized staff.
SCADA provides the facility to fine-tune the operators experiential knowledge in to the system. Sensors can be placed at every critical point in the process to be managed and controlled. As SCADA technology improves, more sensors can be placed to improve efficiency.
SCADA has the ability to view the operation of large power process in real time through software. GIS (Geographical Information System) is one such software widely used in electric power applications. With such am=n ability it is possible to correct errors and diagnostics.
So even for very complex manufacturing processes, large electrical plants, etc., you can have an eagle-eye view of every event while it’s happening — and that means you have a knowledge base from which to correct errors and improve efficiency. With SCADA, you can do more, at less cost, providing a direct increase in profitability.
If you liked this article, then please subscribe to our YouTube Channel for PLC and SCADA video tutorials.
You can also follow us on Facebook and Twitter to receive daily updates.
Read Next:
- SCADA Multiple Choice Questions
- PLC do the Scaling for a Sensor
- Cyber Attacks on Control Systems
- Difference Between SCADA and HMI
- Distributed Control System MCQ
Highly educative information
Wonderful
Instruments tools very important sites it is use ower working field area