SCADA software is the most important aspect which runs on the hardware. Earlier SCADA was mostly hardware and less on software. Presently, SCADA is 85% software and 15 % hardware. SCADA software can be divided into two types, proprietary or open.
The important SCADA protocols can be classified into the following
- DNP3 (Distributed Network Protocol)
- IEC (International Electro Technical Commission) 60870
ISO Model
The working these protocols are based on the ISO or open systems interconnection model (OSI) are shown below.
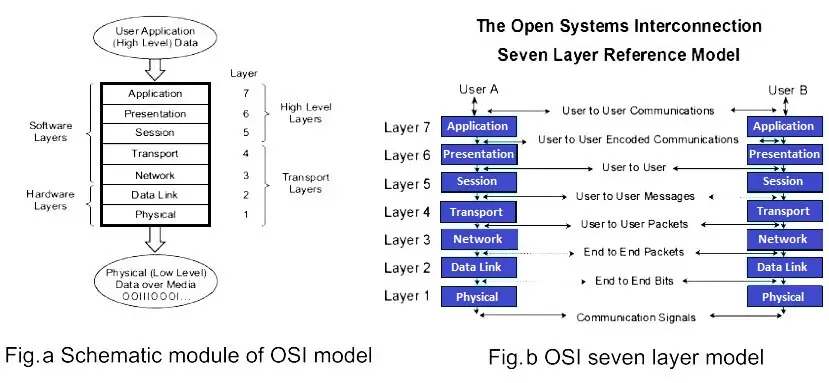
The OSI Reference model has seven layers, the details of which are given below. The different layers are categorized based on the functions they perform
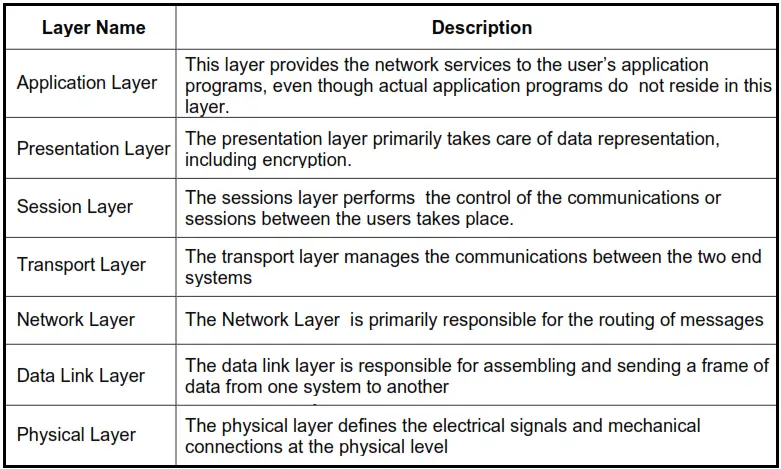
DNP3 Protocol
DNP3 stands for distributed network protocol and it consist of a set of communication protocols used between components which are used in process automation systems like electric utility, chemical process plants, etc.
The purpose of DNP3 is to accomplish communication between various types of monitoring, data acquisition systems and control equipment. This protocol forms an integral part in SCADA systems while interconnecting the RTUs and IEDs named as the Inter –Control Center Communications (ICCP) protocol. ICCP is a part of IEC 60870 and is widely used in inter- master station communications.
IEC 60870 was primarily design to allow important reliable communication between in electric utility automation systems under situations of information distortion and transmission. Security of these protocols is an important aspect to be considered.
DNP3 protocols were not designed to be secure from hackers and threats. There was a need to introduce security authentication to the DNP3 protocol. Presently it is in complaint with IEC 62315-5 and is regarded as a a set of best practices for implementing SCADA-RTU master station communications.
Important Features of DNP3
1. DNP3 protocol is characterised by important features that makes it inter-operable with related protocols like MODBUS, etc. This makes it more efficient and efficient for communicating between components in SCADA systems.
2. DNP3, with reference to the widely used OSI model for communicating networks, corresponds to layer 2, which provides multiplexing of various features like error checking, link control, data fragmentation, etc.
3. DNP3 provides a transport function (layer 4) and Application layer (Layer 7) corresponding to SCADA applications.
4. DNP3 has improved bandwidth efficiency which is accomplished through event oriented data reporting.
5. DNP3 has good ability to handle error detection.
The DNP Protocol performs time synchronization with RTU, where time stamped variants of all data point objects are reconstructed through a sequence of events.
The DNP3 protocol has the added advantage of supporting RTUs of different nature and complexity through four levels of subsets of the protocols for RTU compliance. However this protocol tends to become more complex with increased number of RTUs and interconnection.
IEC60870 Protocol
IEC standard 60870 is widely used for controlling electric power transmission grids and other process plants. This standard can be used for interoperating various equipment from different suppliers through standardized protocols.
IEC standard 60870 has six parts, defining general information related to the standard, operating conditions, electrical interfaces, performance requirements, and data transmission protocols.
IEC 60870 provides a communication profile for tele-control messages between two directly connected systems. This protocols provides tele-control and tele-protection of electric power systems through associated tele-communication.
IEC 60870-5 has five parts:
IEC 60870-5-1: Transmission Frame Formats
IEC 60870-5-2: Data Link Transmission Services
IEC 60870-5-3; General Structure of Application Data
IEC 60870-5-4; Definition and Coding of Information Elements
IEC 60870-5-5; Basic Application Functions
The two widely used protocols for SCADA Applications are
- HDLC (High Level Data Link Control)
- MODBUS
HDLC
HDLC (High Level Data Link Control) is a bit oriented code transparent synchronous data link layer protocol developed by ISO. HDLC provides connection – oriented and connection – less service.
Though HDLC can be used for point to point multi point connections, but is preferable to use one to one connections, known as asynchronous balanced mode (ABM). It forms the basis for all modern protocols.
Modbus
MODBUS is a serial communications protocol originally published by MODICON in 1979 for use with its programmable logic controllers. MODBUS protocol is simple and robust which has become a widely used standard communication protocol for connecting industrial electronic devices.
The advantages of MODBUS protocol from an industry point of view are
1. Industry centric.
2. Open Source
3. Easy to use and deploy
4. Vendor independent
MODBUS allows communication between several devices connected to the network through RTUs in SCADA. In this protocol, the master may initiate a MODBUS command to activate the connected element / device.
The command contains the MODBUS address of the device. Only the indented device will act on receiving the command though other devices receive them. The MODBUS command ensures that the command is received unchanged through an inbuilt checking information.
No standard way exists for a node to find the description of a data object, there is no way for a field device to “report by exception” Modbus is restricted to addressing 247 devices on one data link, which limits the number of field devices that may be connected to a master station Modbus transmissions must be contiguous which limits the types of remote communications devices to those that can buffer data to avoid gaps in the transmission. Modbus protocol provides no security against unauthorized commands or interception of data.
Companies develop proprietary software to communicate to their hardware. These systems are sold as ‘turn key’ solutions. The main problem with this system is the overwhelming reliance on the supplier of the system.
Open software systems have gained popularity because of the inter-operability they bring to the system. Interoperability is the ability to mix different manufacturers’ equipment on the same system.
The widely used open software for SCADA systems are Citect and Wonderware.
Key features of SCADA Software are
- User interfaces
- Graphics displays
- Alarms
- Trends
- RTU (and PLC) interface
- Scalability
- Access to data
- Database
- Networking
- Fault tolerance and redundancy
- Client/server distributed processing
If you liked this article, then please subscribe to our YouTube Channel for PLC and SCADA video tutorials.
You can also follow us on Facebook and Twitter to receive daily updates.
Read Next:
- What is IEC 61508?
- Modbus versus DNP3 Protocols
- OSI Layers of Communication
- Networking Interview Questions
- Basics of SCADA Hardware