15 MW Centrifugal Compressor 3-monthly 10-days outage reduced to 1½ days
Synthesis Gas (75% H2 + 25% N2 gas mix) spill from a broken instrument process lead ignited into a huge fireball near the Synthesis Gas Compressor (K-601) third or High Pressure barrel (HPB).
The plant’s 2 professional fire fighters and volunteer trained fire fighters heroically fought and put out the fire. The HP barrel (HPB) discharge head (DH) leaked two months after plant restart and increased progressively.
Centrifugal Compressor Outage Reduced
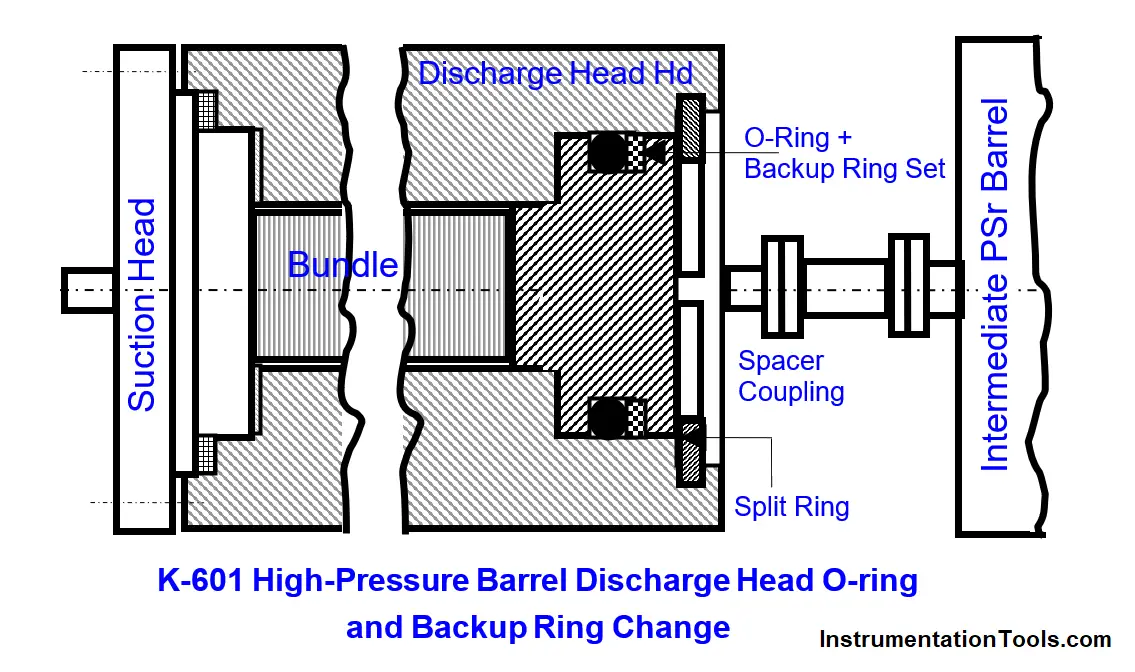
The crew installed steam ring diluted the synthesis gas (75% H2, 25% N2) leaks to prevent fire repeat; on the environs combustibles content reaching 90% of limit, the lab crew monitored the combustibles content 2-hourly instead of 8‑hrly.
The operation engineer started the SD preparations and the rotating machine crew changed the HPB DH O‑ring backup ring set (ORBRS).
Thus, the HPB DH ORBRS set changed, a ten days SD task repeated at 3-monthly intervals. Besides, huge maintenance efforts, costs, the 40*650 = 26000 Tons yearly ammonia production loss, and the front end 40 days, 30% load operation and venting the produced Reformed Gas wastefully crippled the company financially.
Front end SDs and restarts stress the equipment thermally and reduce their lives by years. Hence, plants continue operating the front end at as low load as practical – 30% in this plant’s case – during ammonia plant SDs.
Why the ORBRS Change Takes 10 days?
The Rotating Machine Crew’s (RMC) below given ORBRS procedure is the reason for 10-days SD:
- The RMC somehow wrongly believed no room to shift the DH towards the IP barrel; hence, they chose to position the IP barrel ½ meter away from the 30 T weight 3rd barrel, as the only rentable very old and crane stretching to its limit could just lift the 20 T weight IP barrel (IPB).
- IPB shifting involves:
- Unbolt the IPB foundation bolts
- Dissemble 10” suction and discharge 1500 # RTJ flanges – a heavy task
- Cut few ¾” and 1” gas and oil lines to move the IPB
- Uncouple IPB from left LPB and right HPB i.e., two couplings dissemble and to heavy machines alignments to the IPB
- Lift and position the IPB ½ m away using the crane
- Unlock HPB split rings, and pull the DH using the chain pulley block arranged before the SD
- Change the Discharge Head ORBRS
- Assemble back the DH
- Position the IPB using the crane
- Align IPB to HPB and LPB
These numerous heavy jobs led to them each time 10-days SD.
The Author’s 1½ – Shutdown Method
The author then the instrument engineer felt uneasy of an instrument lead starting these high-cost tasks and 40-days yearly on-stream days loss.
Hence, he wanted to help reduce the shutdown (SD) days; by eye judgment, he was certain that the 600 mm long spacer couplings between machines provide enough room to move the DH towards the IPB left in position.
Hence, he took few measurements during the RMCs tea breaks to avoid the feeling of interfering in others’ work. It convinced him that ORBRS change with IPB in-situ in 1½-2 days SD was possible, without hiring the heavy crane.
He talked to the RMC leader about this and offered to work with him during the next ORBRS change. The unbelievable 8½ days of time-saving each time and so many other benefits seemed too good to be true to the mindset RMC.
They ridiculed the author; and influenced the electrical graduate maintenance manager not to approve trying the new method. Hence, the 10‑days routine continued for 3 more years!
Job done in < 36 hours
The author became Maintenance Manager three years later. The rotating machine crew under his guidance and using the author’s procedure changed the ORBRS in < 36 hours, as under.
The author accepted the RMC leader request to position the crane as insurance, in case reverting to the old method was necessary to respect their views and to gain their whole hearted cooperation while doing the job by his method.
- The RMC dissembled the IPB to HPB 600 mm long spacer coupling
- As usual they removed the DH securing split rings
- They pulled the DH towards the IPB using the before SD arranged chain pulley block; the DH came clear out of the HPB
- The crew replaced the ORBRS and boxed the HPB
- They did the task in 1½ days
The New Method’s Benefits
The new procedure benefits are:
No IPB shift and hence,
- No poor condition crane positioning in the pipe rack obstructing difficult to maneuver area
- The absence of managers’ and crews’ extreme stress from the IPB lift start to its placing back in position, because of the crane’s very old condition and the crane driver and owner confidence lack
- No high pressure large sized suction and discharge flanges breaking, making and new gaskets use
- No anxieties of likely flange leaks, likely fires and making joints again and new gaskets use costs
- No difficult complex and time taking IPB to HPB and IPB to LPB thermal growth compensating alignment
- No 10-days wasteful and exorbitant crane rent payment for just few hours use
- No living with the hazardous leaks until the crane availability
- Most important: 4*8½=34 days less plant outage yearly, 85% less wasteful RFG venting during the SD and its enormous financial savings
- Last but not the least 17% yearly higher ammonia, urea and NPK fertilizers production year after year
- No wasteful RFG wasteful venting during the 40-days ammonia plant SDs
- The money value of all these would be close to ¼ to 3/8 billion rupees annually.
This Case Study Take outs
Below are these Case Study Take outs:
- Consider alternative methods when the developed procedure involves expensive resources use and very high total plant downtimes
- Don’t reject other disciplines persons suggestions; for that matter from anybody right away; consider these showing genuine interest, mindset and prejudice free and encourage them; in case their suggestions posed few practical difficulties discuss and iron out; even mock trials are worthwhile
Author: S. Raghava Chari
Do you face any similar issues? Share with us through the below comments section.
If you liked this article, then please subscribe to our YouTube Channel for Instrumentation, Electrical, PLC, and SCADA video tutorials.
You can also follow us on Facebook and Twitter to receive daily updates.
Read Next:
- CO2 Stripper Collapsed Internals
- Roof Hot Spots eliminated forever
- Absorber Corroded Wall Thickness
- Rotary Drier Shell to Split Gear drive
- RFG main Hot Spots threaten Outage