What is Scan Time?
Every control system will take some time to execute its operation. Likewise, PLCs also takes time to perform a task. In simple terms, PLCs mainly has 3 parts which are input modules, output modules, and processor (CPU).
The input modules will read the status of switches, transmitters, and gives the data to the processor. The processor will execute the logic as per the user program. The processor will give the command to the output modules. The output modules are connected with final control elements like control valves, motor control feeders, etc.
The inputs and outputs may be in the form of NO, NC, 4-20mA, or a Bit/Pulse. So, the above all mentioned steps require some time in PLC which means for reading inputs, solve the logic, and write output, each step required some time which is nothing but the PLC scan time.
Definition of PLC Scan Time
Time taken by the PLC to read the inputs, solve the Logic, and to write the output is called a PLC Scan Time.
These functions work in the loop it may vary its time taken for execution from 0ms to 150ms to a large till 1000ms.
The variation in scan time depends on the following factors:
- Number of inputs
- Length of logic/Loops in program
- Number of Outputs
Let’s get clear the concept by the following example;
In PLC, we have an analog input card, these analog signals need to be converted in digital format so that the processor can read it and perform an action.
Say If 1 channel generally needs a 3ms time so, if we used a 4 channel to PLC then the scan time will be 4 X 3=12ms.
Why the Scan time Important?
Suppose we have a PLC whose scan time is 5ms, and we need to assign an input for an encoder which generates a pulse every 1ms time. Refer below figure (a).

Figure: a
In the graph below, as you can see the PLC takes a 0.3ms time to read input, 0.3ms time to write output, and 4.4ms time to executive logic. I.e. total 5ms scan time is required by PLC.
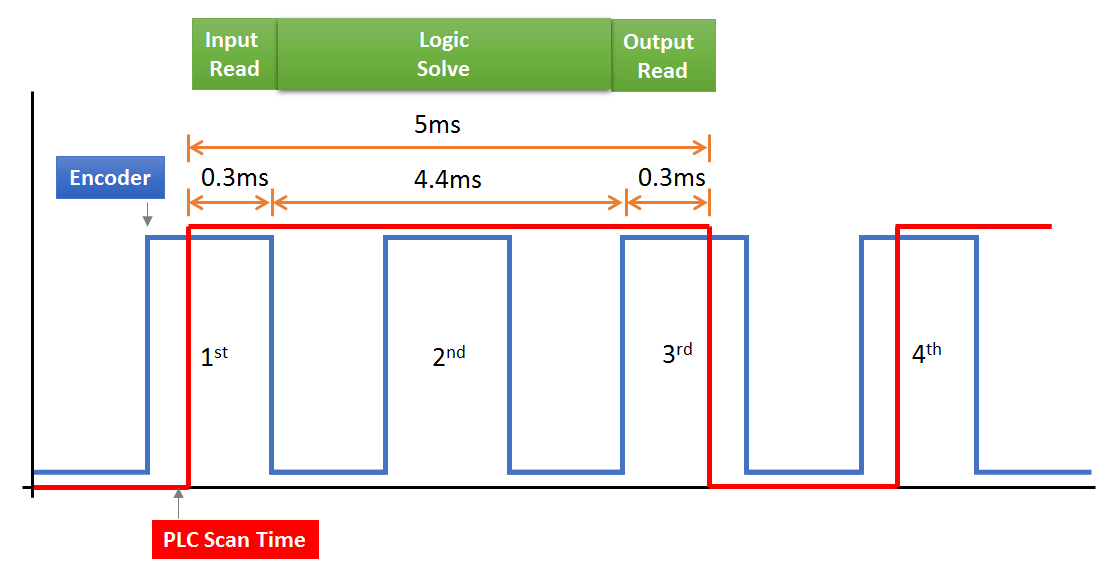
Figure: b
As we can see the encoder pulse start after 0.5ms and PLC scan time starts with 0ms. The PLC will read the first pulse of the encoder which is at 0.5ms but after the first pulse as soon as the second pulse which will be at 1ms, the PLC will not be able to read this input because the PLC input read scan time is 0.3ms only.
So at each new scan time, the PLC will read only the first pulse of the encoder and other pulses will be neglected by PLC because PLC scan time is Greater than Encoder time. These are a serious issue for the process.
What if I have already a PLC whose scan time is greater than an encoder?
In the PLC software there is Instruction, by which you can avoid the above problem they are as followed;
- Immediate Instruction – Input Immediate, Output Immediate
- Interrupts instruction.
These instructions are mainly seen in Siemens Old PLC’s.
The Instruction works such that the input immediate will pause the logic execution step and read the Inputs again and again and then continue the logic step, same the other Instruction also works respectively.
Author: Jadhav Amit R
If you liked this article, then please subscribe to our YouTube Channel for PLC and SCADA video tutorials.
You can also follow us on Facebook and Twitter to receive daily updates.
Read Next:
- FB Block in Siemens PLC
- PLC Input Output Modules
- One-Shot Rising PLC Program
- Midline Instruction in Siemens
- Choose Right Fuse for a Panel
Good example. Whether there are such logics in a DCS ?
Yes, usually the design of DCS scan time starts from 0.5ms to greater upto 500ms these are adjustable according to process.
Verry important information necessary for Instrumentation and plc selection
Is scanning time a clock?
Isn’t it symmetrical? duty cycle greater than 50%?
During level 0 it do nothing?
The scan time is generally synchronous?
If I use a bit memory contact NC on series with a coil, I get de scan time?
Thanks!