In this post, we will see various types of industrial automation controls used in the HVAC domain.
HVAC stands for Heating, Ventilation, and Air Conditioning. It is a type of automation system which is used for handling air quality and thermal comfort given to the human environment for survival. It is based on thermodynamics, fluid mechanics, and heat transfer. Just like different types of automation systems, HVAC to is one type of automation system.
It is one of the most important parts required when setting up a high-rise building, commercial complex, industrial unit, hospital, parking unit, hotels, etc. where air quality and thermal parameters need to be maintained so that the personnel around can live properly.
Traditional HVAC systems worked without PLCs; but nowadays, almost all of them have PLCs installed for better and more accurate control.
HVAC Automation
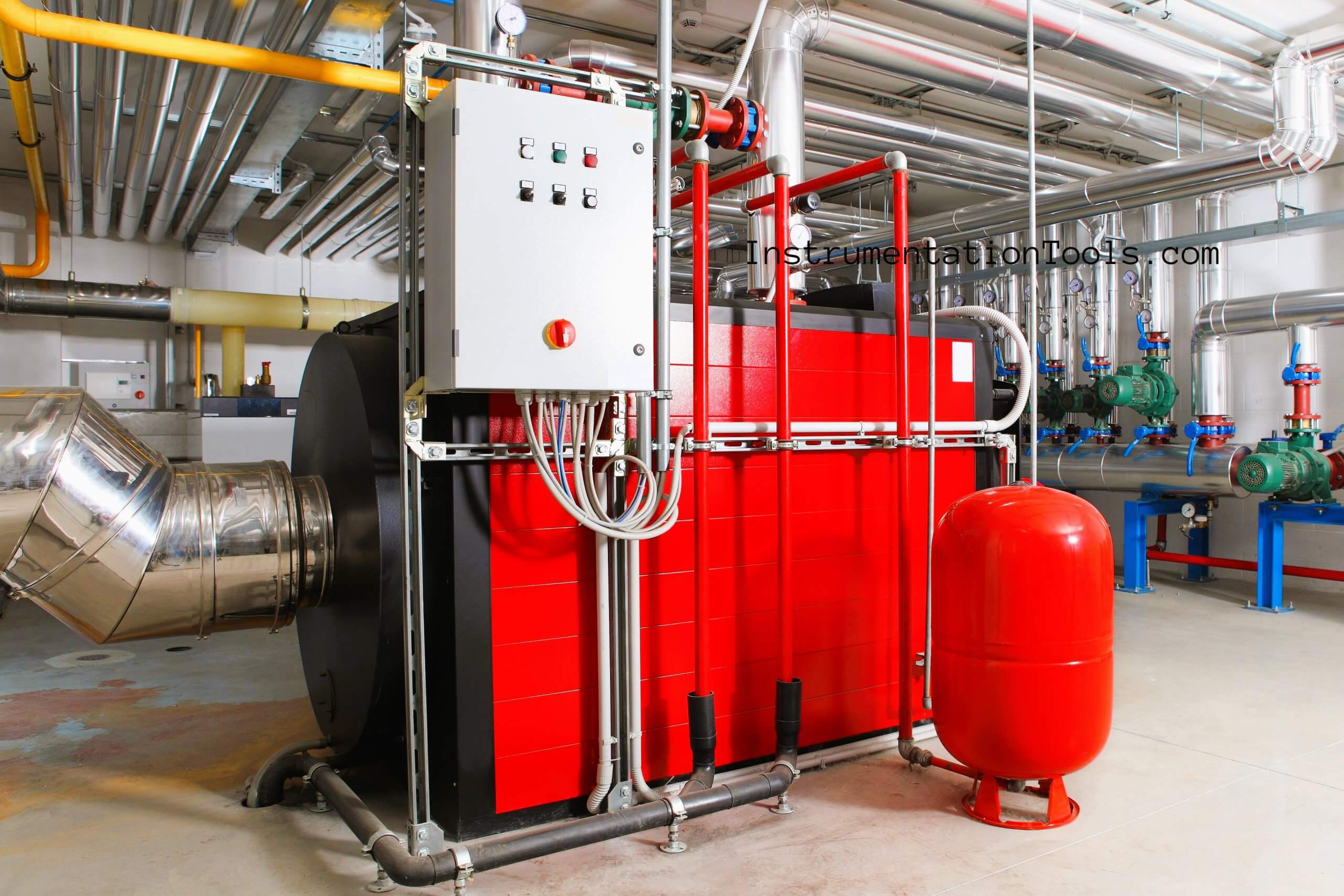
There are numerous types of controls in HVAC automation. Basically, temperature, humidity, and pressure are to be maintained.
But, apart from it, it is also to be taken care that the devices which are controlling the automation like compressors, valves, pumps, sensors, etc.; need to be maintained for long life.
So, there are various types of automation logic used in HVAC for maintaining the whole system. Let us have a look at the various types of controls.
Night Mode
Consider a hospital area. Basically, a lab is fully occupied during the day or during general shift hours. When there are very few personnel present in the area, then it is a waste of energy to provide fully loaded cool air in the room.
So, a night mode provision is generally provided in the PLC program. Suppose there are three compressors in the system and they all run in the daytime to provide a cool set temperature.
During the nighttime, as fewer people are there, a slightly higher temperature is acceptable in the area. So, as soon as night time arrives, the set temperature in the PLC increases; which will run less number of compressors.
The blower speed will reduce automatically. The chilled water valve will close to a higher percentage; so, if less water is passed through the valve, then the chiller passing water will automatically run in less demand and thus improve power consumption.
This improves energy efficiency by reducing power consumption; and also provides less load on all the corresponding devices like motors, valves, and compressors.
The same condition goes for hot air and water. The devices used in control will also run in night mode or according to demand. This will help reduce energy consumption.
Temperature Control Strategy
As temperature control is an important part of HVAC, there are numerous sub-systems in PLC logic to control the temperature. It is used to modulate heating coils, cooling coils, dampers, and fans to control the return line temperature. If the return media is controlled, then the purpose of control is automatically achieved.
Controlling is done mostly by PID logic; because PID accurately modulates the output according to the input received.
Blower speed is controlled according to flow or sometimes, it runs at a set speed; to maintain the CFM in the area. If CFM is not maintained, then the temperature will also not be controlled.
Alarm Management
As multiple compressors, blowers and pumps run in an HVAC system, it is necessary to detect its alarms and accordingly control the system.
Suppose three compressors are installed in the system; with two working and one standby. When a compressor trips or any fault occurs in it, then the standby compressor is automatically turned on to maintain the temperature.
A compressor can have various alarms like motor overload, emergency stop, oil pressure fail, discharge and suction pressure fail, and other related types. So, it is necessary to control all the alarms and indirectly, manage the whole system.
Running hours and Availability Management
If multiple motors are running, then it is necessary that they equally load the share between them.
They can be prioritized by running hours or device alarms. Running hours can be classified as least running hours, FIFO sequence (First In First Out), and LIFO (Last In First Out).
Depending on that, a device running hours are shared equally between them. In terms of availability, it means whether there is an alarm in the device or whether it is enabled/disabled for operation.
Depending on that, the devices are run for proper load sharing. PLCs consider both the running hours and their availability to properly optimize the device operation.
Coefficient of Performance (COP) Calculation
This programming helps in calculating the COP based on thermal power (in KW) and electrical power (KW).
This helps the engineers in reading the efficiency of the heating and cooling machines; and shows whether they are providing proper performance or not.
Refrigerant Pressure Control
The internal pressure of the refrigerant and outdoor air temperature is monitored and controlled in tandem to modulate condenser fan air pressure.
Basically, the idea is to provide appropriate pressure to the chilling devices; so that the temperature and pressure of the media are maintained.
Apart from these, it is important to note that PID is a very useful library used to modulate the devices. The core idea is to control temperature, pressure, humidity, and flow so that the whole HVAC operation works properly.
Read Next:
- Types of HVAC Chillers
- HVAC Heat Transfer Loops
- Automation used in HVAC
- HVAC Objective Questions
- Valves in HVAC System