The operation of a control valve involves positioning its movable part (the plug, ball or vane) relative to the stationary seat of the valve. The purpose of the valve actuator is to accurately locate the valve plug in a position dictated by the control signal.
The actuator accepts a signal from the control system and, in response, moves the valve to a fully-open or fully-closed position, or a more open or a more closed position (depending on whether ‘on/off’ or ‘continuous’ control action is used).
There are several ways of providing this actuation.
- Pneumatic.
- Electric.
Other significant actuators include the hydraulic and the direct acting types.
Pneumatic Control Valve Actuators
- piston actuators
- diaphragm actuators
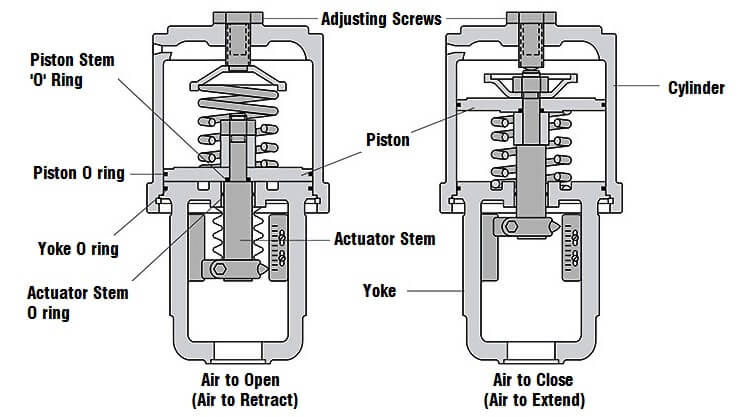
Piston actuators
Piston actuators are generally used where the stroke of a diaphragm actuator would be too short or the thrust is too small. The compressed air is applied to a solid piston contained within a solid cylinder.
Piston actuators can be single acting or double acting, can withstand higher input pressures and can offer smaller cylinder volumes, which can act at high speed.
Diaphragm actuators
Diaphragm actuators have compressed air applied to a flexible membrane called the diaphragm. The below Figure shows a rolling diaphragm where the effective diaphragm area is virtually constant throughout the actuator stroke.
These types of actuators are single acting, in that air is only supplied to one side of the diaphragm, and they can be either direct acting (spring-to-retract) or reverse acting (spring-to-extend).
Reverse acting (spring-to-extend)
The operating force is derived from compressed air pressure, which is applied to a flexible diaphragm. The actuator is designed so that the force resulting from the air pressure, multiplied by the area of the diaphragm, overcomes the force exerted (in the opposite direction) by the spring(s).
The diaphragm (Above Figure) is pushed upwards, pulling the spindle up, and if the spindle is connected to a direct acting valve, the plug is opened. The actuator is designed so that with a specific change of air pressure, the spindle will move sufficiently to move the valve through its complete stroke from fully-closed to fully-open.
As the air pressure decreases, the spring(s) moves the spindle in the opposite direction. The range of air pressure is equal to the stated actuator spring rating, for example 0.2 – 1 bar.
With a larger valve and/or a higher differential pressure to work against, more force is needed to obtain full valve movement.
To create more force, a larger diaphragm area or higher spring range is needed. This is why controls manufacturers offer a range of pneumatic actuators to match a range of valves – comprising increasing diaphragm areas, and a choice of spring ranges to create different forces.
The diagrams in Below Figure show the components of a basic pneumatic actuator and the direction of spindle movement with increasing air pressure.
Direct acting actuator (spring-to-retract)
The direct acting actuator is designed with the spring below the diaphragm, having air supplied to the space above the diaphragm. The result, with increasing air pressure, is spindle movement in the opposite direction to the reverse acting actuator.
The effect of this movement on the valve opening depends on the design and type of valve used, and is illustrated in Above Figure.
There is however, an alternative, which is shown in Below Figure. A direct acting pneumatic actuator is coupled to a control valve with a reverse acting plug (sometimes called a ‘hanging plug’).
The choice between direct acting and reverse acting pneumatic controls depends on what position the valve should revert to in the event of failure of the compressed air supply. Should the valve close or be wide-open?
This choice depends upon the nature of the application and safety requirements. It makes sense for steam valves to close on air failure, and cooling valves to open on air failure.
The combination of actuator and valve type must be considered.
The below Figures sow the net effect of the various combinations.
Article Source :Â spirax sarco
fantastic explanation
sir please explain the working of Reverse Air Bag House
Perfect tex!, excellent explanation of the operation control valve and its main accessory. Congratulations
Thanks a lot
Nice information sir