Cables and Cable Glands Questions
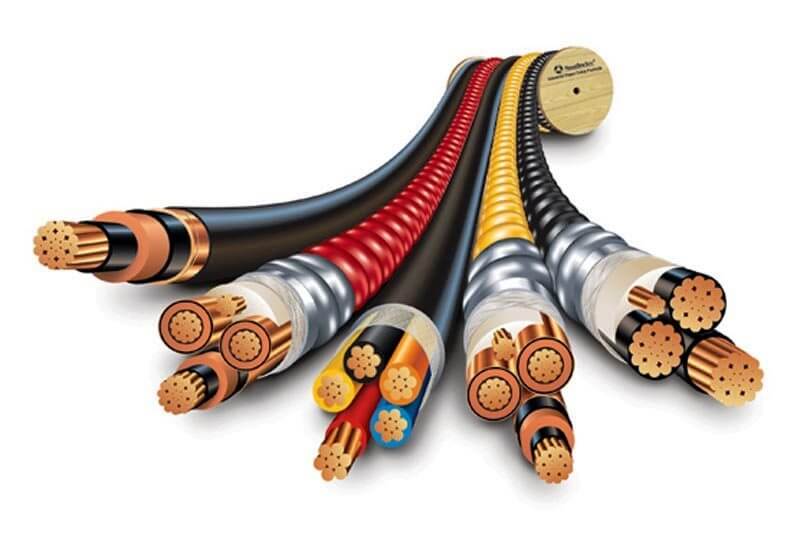
What are different elements of a Cable? Basic about cable components & constructional details
Conductor
Conductor is a current carrying element made up of Aluminium or Copper with a specific cross section for the assigned rating, having resistance / km within certain specified limits.
Electrical Insulation (dielectric)
Insulation is provided over the conductors to electrically isolate them from one another. Various types of insulating materials used are : PVC, XLPE (Cross Linked Polyethylene), Rubber, etc.
An insulated conductor is termed as Core. A cable may have one or more cores. In a multiple core cable , the cores are helically stranded together.
In twin, three & multi-core cables, the cores are laid up together with a suitable lay; the outer most layer has right-hand lay and the successive layers are laid with opposite lay direction.
Inner sheath (bedding)
Cables with stranded cores are provided with Inner Sheath applied either by extrusion or by wrapping.
It is ensured that the shape is as circular as possible. Inner Sheath is so applied that it fits closely on the laid up cores & it should be possible to remove it without damage to the insulation.
Thickness of Inner Sheath is specified in relevant standard and is based on calculated diameter over laid-up cores.
Armour
A wire, strip or a tape applied helically over the cable, to protect the cable from penetration by sharp objects, crushing forces, and damage from rodents or boring insects, is termed as Armour.
Armour is applied over the insulation in case of single core cables & over inner sheath in case of twin, three & multi core cables.
Outer Sheath
Outer sheath /Jacket is usually an extruded plastic cover over the laid-up or armoured core. PVC is a common sheathing material.
Outer sheath provides mechanical, thermal, chemical and environmental protection.
No electrical function is assigned to Outer sheath. The colour of outer sheath is normally black.
What are different cable types and categories?
Cables can be divided into large number of types based on a combination of classifications as follows:
- Based on the voltage ratings as low voltage, high voltage, extra high voltage cables, etc.
- Based on the conductor material, Copper conductor or Aluminium conductor.
- Based on the insulating material as PVC insulated, Rubber insulated, XLPE insulated, etc.
- Armoured or Unarmoured cables
- Based on the sheathing material, as PVC Sheathed, Rubber Sheathed, Lead Sheathed, Aluminium Sheathed, etc.
- Based on the number of cores as single core, two core, three core, three-and-a-half core, four core, multicore, etc.
- Based on the cross-section of the conductor.
- Based on the type of conductor, solid, stranded, sector shaped, etc.
From above it is evident that the types of cables will differ widely depending upon various factors involved.
To facilitate identification and description of the type of cable it is general practice to adopt some form of type designations.
With these designations it becomes easier to convey in a few words the right type of cable.
Also Read : Selection Guidelines for Cable Glands
Comparison of XLPE cables with PVC cables
The important difference is the extra toughness of insulation and, in particular, the ability to withstand much high temperature without deformation due to mechanical pressure.
The better physical properties of XLPE enable the insulation thickness to be reduced and hence overall size of the cable.
The continuous temperature rating is increased from 70°C to 90°C and the temperature for short circuit ratings for the cable from 160°C to 250°C.
In general, XLPE insulated cables are competitive alternative to PVC cables for industrial use and Paper insulated cables for public supply systems.
What is screening in cable and why it is required?
Electrical Screening is necessary only for cables with phase voltage > 1 kv and fulfills the following functions.
- Potential grading and limiting of electrical fields
- Conduction of charge and discharge currents
To satisfy these functions, the screening normally comprises a combination of conducting layers with metallic elements.
The magnitude of electric stress and the degree of sensitivity of the insulation material against partial discharge govern the type of screening of the insulation with conducting layers.
Above certain voltages, as a means of containing the electrical field within the insulation, semiconducting screens are applied over the conductor & insulation.
Screens are provided to achieve symmetrical dielectric fields within the cable structure & carry current during short circuit. By this it is possible to eliminate any electrical discharges arising from air gaps adjacent to the insulation.
The coefficient of expansion of polyethylene & EPR is approximately ten times greater than that of either Copper or Aluminium, and when the conductor is at its maximum operating temperature of 90°C a sufficiently large gap is formed between the insulation and the surface of the conductor to enable electrical discharge to occur.
This discharge site & any others which are formed around a conductor when conductor is bent can be eliminated by applying a semiconducting layer over the conductor.
Similarly, any discharges arising from air gaps between laid-up cores can be nullified by the use of a screen over the insulation.
During the early 1960s semiconducting tapes were applied the conductor but these have since been superseded by an extruded layer.
This has the advantage of providing both a smoother finish and, as it fills the interstices between the wires, a circular envelop around the conductor.
By reducing the concentration of the flux lines around the individual wires, the electrical stress around conductor is reduced by between 10% to 15%.
The semiconducting layer is compatible with, and bonds to, the insulation and a nominal thickness of 0.7 mm is typical.
What is FRLS H cable?
Flame Retardant Low Smoke and Low Halogen cables have improved flame resistant characteristics and emit lower smoke and toxic gases.
Special features
- Reduced flame propagation
- Low smoke emission
- Low acid gas generation
Formulation for the FRLS compounds, which are mainly for the sheathing materials, require special ingredients.
These cables may have insulation of PVC or XLPE, but sheath is PVC based, suitably compounded to meet FRLS H requirements.
What are the general Packing practices followed?
Cables are generally received on wooden/steel drum. There is an arrow painted on the flanges of the drum which indicate the direction in which the drum should be rolled.
The cable will unwind and become loose if the drum is rolled in the opposite direction.
All drums should be stored in such a manner as to leave sufficient space between them for air circulation.
In no case should the drums be stored ‘ on the flat’ i.e. with flange horizontal.
What are the different Conductor materials used as conductor?
Conductor is a current carrying element made up of Aluminium or Copper with a specific cross section for the assigned rating, having resistance / km within certain specified limits.
Also Read : Cable Screen shall not be Grounded at Field Device ?
What is the criterion for selecting particular type of conductor?
Conductor selection depends on various parameters like current carrying capacity , system voltage, voltage drop, flexibility, shape, and economics.
The most commonly used metals are Copper and Aluminium.
Resistance (R) of a conductor is inversely proportional to the area of cross section and is given by :
R= þ x l / A
Where
þ= Resistivity of the conductor material.
l= Length of conductor.
A = cross sectional area of conductor.
What are the different types of conductor?
Conductors are divided into different classes , the flexibility of the conductor increases with the class number.
These are as follows:
- Cables for fixed installations: classes 1 and 2
- The flexibles: classes 5 and 6
Solid Conductor (Class 1)
The conductor consists of single wire of plain or tinned annealed Copper and its cross-section is circular.
Solid Aluminium conductor of sizes 1.5 mm2 , up to and including 16 mm2 is of circular cross-section. Sizes 25 mm2 and above may be either circular or shaped cross-section.
Stranded Circular Non-Compacted Conductors ( Class 2 )
The conductor consists of plain or tinned annealed Copper or plain Aluminium.
The number of wires in the conductor are not less than the appropriate minimum number as specified in the standards.
Stranded Compacted Circular Conductors and Shaped Conductors (Class 2)
The conductor consists of plain or tinned annealed Copper or plain Aluminium.
The number of wires in the conductor are not less than the appropriate minimum number as specified in the standards.
Flexible Conductors(Classes 5 and 6 )
Conductor consists of plain or tinned annealed Copper.
The diameter of the wires in any conductor does not exceed the appropriate maximum value as given in the standards.
What are different types of insulating material?
List the important properties of cable insulation.
What are thermoplastic and thermoset materials?
Insulation is provided to electrically isolate the individual cores from one another.
The applied insulation must perform adequately in the specified temperature range, and its dielectric strength should be sufficient to sustain the electrical stresses.
Cable insulation should have:
- High Dielectric Strength
- Low dielectric constant
- Good Mechanical properties
- Resistance to Ageing
- High temperature withstandability
Insulating materials are classified as thermoplastic or thermoset. Thermoplastic materials lose their form upon heating. Thermoset materials maintain their form in spite of heating.
Various types of insulating materials used are : PVC, XLPE, Rubber, Impregnated Paper, etc.
Polyvinyl Chloride (PVC)
Polyvinyl chloride (PVC or vinyl) is a thermoplastic. PVC compound is the standard insulation for cables rated at 11000 volts or less & sheathing of entire range of cables.
PVC compound is a mixture of PVC resin, plasticizer, fillers, stabilizers, lubricant, pigment. The quantity and type of each ingredient determines the properties.
A broad range of electrical, physical and chemical properties is possible.
PVC has good electrical properties. It is tough and resistant to flame, moisture, and abrasion. Resistance to ozone, acids, alkalis, alcohol, and most solvents is also adequate.
PVC can be made resistant to oils and gasoline.
PVC has the disadvantage of having a high dielectric constant and dissipation factor.
Also plasticizer loss can cause hardening and cracking.
Crosslinked Polyethylene
Crosslinked polyethylene (XLPE) is a thermoset. It is produced by compounding PE (polyethylene) with a crosslinking agent, like organic peroxide.
The molecules of polyethylene are “crosslinked”, forming an interconnected network. The terms “cured” and “vulcanised” are also used for “crosslinked“.
Elastomer
Elastomeric material are used for insulation and for sheaths. They are applied mainly where the product has to be particular flexible.
A wide range of elastomers is nowadays available to the cable industry.
This makes possible the manufacture of compounds with specific properties, such as abrasion and oil resistance, weather and heat resistance and flame resistance, combined with good overall electrical and mechanical charateristics.
The classical elastomeric material, natural rubber, has declined in significance in recent years.
In its place, the synthetic elastomers produced by the co-polymerisation of ethylene and propylene, are constantly finding new areas of application in cable engineering. This co-polymers, are generally known as EPR.
Rubber was the first insulant to be used in Electric cable manufacture but gave way to other insulants like paper, PVC, XLPE etc.
Rubber is still considered the preferred insulation for flexible cables and cables where very small bending diameter is desired.
Paper
Paper tapes of specific thickness and suitable widths are lapped around the conductor. The thickness of built up insulation depends on the rated voltage of the cable. Paper insulated cores are dried and impregnated using mass impregnating non-draining compound.
Also Read : Difference Between RS232 and RS485
What is the function of Conductor / Insulation Screen and material used?
Function of Conductor / Insulation Screen
The conductor shield is a layer of semi-conducting material. Semi-conducting materials do not conduct electricity well enough to be a conductor but will not hold back voltage.
It “smoothes” out the surface irregularities of the conductor. The conductor shield makes the voltage on the inside of the insulation the same. Industry specifications define the performance of conductor shield. Good insulation shields are extruded in tandem with the insulation.
The insulation shield consists of two components. These components are the extruded (auxiliary) shield and the metallic (primary) shield.
The extruded shield consist of a semi-conducting layer similar to the conductor shield. It makes the voltage on the outside of the insulation the same.
The primary shield can consist of metal tape, drain wires or concentric neutral (CN) wires. Grounding the primary shield makes the voltage on the outside of the insulation ground. The Copper of the shield is usually bare, but may be coated with lead or tin.
Some primary shields consists of drain wires and tape. Aluminium and lead can also be used as the shield.
Concentric neutral wires serve a two-fold purpose. They function as the metallic component of the insulation shield and as a conductor for the neutral return current. Their cross sectional area must be sized in order to function as the neutral conductor.
Cables with PVC Insulation
The inner conducting layer consists of PVC compound having high carbon black content.
For the outer conducting layer, a cover of conducting tapes is preferred.
Cables with PE or XLPE Insulation
Because of higher sensistivity to partial discharge the reliable well adhesive gap and cavity free bonding to conducting layers is of greatest significance.
The inner conducting layer consists of polymer compound made conductive by adding carbon black.
And the outer conducting layer is formed by semi-conducting compound along with semi-conducting tapes.
Cable Glands Questions
What is Cable Gland?
A device designed to permit the entry of cable in to electrical equipment which provides sealing, retention and ear thing, bonding, grounding, insulation, strain relief or combination of all these.
Gland should maintain overall integrity of enclosure in to which it is to be fitted.
How to select the Cable Gland?
Gland should be selected on following Points
- Type of Cable
- Gland Size
- Entry Type/Thread Specification of application
- Ingress Protection required.
- Material
What are the type of Cable and how the Gland to be used?
Unarmored: Unarmored Cable will require outer seal within Gland to not only Provide ingress protection but also degree of retention.
Armored: Gland that required clamping mechanism to terminate the armored both mechanically and electrically.
The Gland will usually be required to provide ingress protection by sealing outer sheath and retention by clamping amour.
what are the types of Gland?
- Brass Indoor Type Gland
- Brass Outdoor Type Gland
- Brass Straitening Unarmored Cable Gland
- Brass Weather Proof Gland
- PG Threaded Gland:
- Industrial Type Gland
Describe the types of Gland?
Brass Indoor Type Gland
- This Gland is quite handy in use with various types of cable whether plastic, rubberized, metal or any other.
- Application: Dry indoor, for use with all type of SWA cables, plastic or rubber sheathed cable.
- Brass indoor gland suitable for single wire armored, plastic or rubber sheathed cable. Recommended to use with shroud for additional ingress protection.
- Cable Type: Steel Wire Amour.
- Amour Clamping: Two Part Amour Lock.
Brass Outdoor Type Gland
This come in stunning high quality material for use in outdoor or indoor application with various types of cables sheathed or unsheathed.
- Brass indoor and outdoor gland popularly used with single wire armored.
- Plastic or rubber sheathed cable. Terminates and secure cable armoring and outer seal grips sheath of cable thus ensuring mechanical strength and earth continuity.
- CW brass glands are also supplied with integral earth facilities.
- Recommended to use PVC shroud for additional ingress protection
Application:
a) Outdoor or indoor, for use with all type of SWA cables, plastic or rubber sheathed cable.
b) Most suitable for SWA, plastic of rubber (Elastomeric) sheathed cables.
c) Used in dry indoor conditions.
d) No loose parts and easy to install.
e)Save times & money.
- Gland size: 20 mm to 75 mm (S & L)
- Accessories :Earth Tag, PVC Shroud, Neo prime Rubber & LSF Rubber, PVC Washer, Brass Lock Nut.
- Cable Type: Wire Braid Armor.
- Armor Clamping: Three Parts (With Lock Nut).
Also Read : Generator Action in a Motor
Brass Straitening Unarmored Cable Gland
- Nickel plated or natural brass A2 type cable glands are used with variety of unarmored or rubber sheathed cables.
- Brass indoor and outdoor cable gland suitable for all types of unarmored cables, plastic or rubber sheathed cables.
Application:
- For use with unarmored elastomeric and plastic insulated cables.
- Indoor & Outdoor whenever it is required to provide sealing on cable outer sheath.
- Size : Metric – 20mm to 75mm (S/L)
- Accessories: Earth Tag, PVC Shroud, Neo prime Rubber & LSF Rubber, PVC Washer, Brass Lock Nut.
- Cable Type : Unarmored
Brass Weather Proof Gland
Unlike other types of cable glands, This type cable gland is used precisely with single armored various types of swa cables whether plastic or rubber sheathed ones.
This type cable gland is known for its uninterrupted services once the gland is fixed to the desired wires and wire components.
- Suitable for SWA or rubber sheathed cables.
- Outer seal grips bedding layer of cable for use in most climatic conditions.
- Weather proof and water proof.
- Design has separate armor lock rings. Can be supplied with integral earth facility.
- Gland size: 20 mm to 75 mm (S & L)
Application
- Outdoor or indoor, for use with single armored, all type of SWA cable, plastic or rubber sheathed cable.
- E1W Gland is Weatherproof & Waterproof Cable Gland
- Cable Type : Steel Wire Armour
- Armour Clamping: Three Part Armour Lock
- Sealing Technique: Compression & Displacement Type
- Sealing Area(s): Inner & Outer Sheath
PG Threaded Gland:
Nickel chrome plated PG threaded cable gland is a custom made threaded gland to meet the needs from the meet industries.
Apart from the round headed PG threaded cable gland, also available hexagonal gland or any other like spherical rectangular or any other dimensional PG threaded cable gland as per the specification of the customer.
Industrial Cable Gland
Brass gland suitable for wire braid armored, plastic or rubber sheathed cable.
Terminates and secure cable armoring and outer seal grips sheath of cable thus ensuring mechanical strength and earth continuity.
- Recommended to use PVC shroud for additional ingress protection
- Cable Type: Wire Braid Armour
- Armour Clamping : Three Part (With Lock Nut)
- Sealing Technique: Compression Type.
- Brass gland suitable for steel tape armored, plastic or rubber sheathed cables. Terminates and secure cable armoring and outer seal grips sheath of cable thus ensuring mechanical strength and earth continuity.
- Recommended to use PVC shroud for additional ingress protection
- Cable Type : Steel Tape Armour
- Armour Clamping : Three Part (With Lock Nut)
- Sealing Technique: Compression Type.
What is difference between Single Compression and Double Compression?
- Double compression glands provide extra support to the heavy armored cables entering or exiting the panel while single compression glands are used for light armored cables.
- Normal Cable Gland is also called Single Compression Cable Gland. As the name suggests, while you tighten the gland, the grip or compression is effected only at one p [lace (i.e.) at the cable armour only. There is scope for moisture and corrosive vapour to enter the gland and thus into the cable.
- Whereas in Double-Compression Gland, the compression happens both at the cable armour as well as at the inner sheath. This is sort of two sealing. Hence, chances of moisture or vapour entry are minimized. Hence these glands are also known as Weather-proof cable glands or Flame-proof cable glands.
- The basic difference between single and double compression is in Single comp there no cone and cone ring.
The mechanical support for the cable is only Neoprene rubber seal, When you tighten the cable. - In double camp gland the mechanical support to the cable only cone and cone ring. When we are doing glanding the cable armor sits on the cone and cone ring act as a lock for armor.
- Single compression and double compression glands are used on the basis of area classification. Those who are affiliated with oil and gas sector they will easily understand about area classification.
- In zone 0 where the presence of hydrocarbon is obvious (IIC) double compression gland is used because the flame path in case of double compression gland is much more than in case of single compression gland.
- The logic behind this is that if there is any explosion inside the terminal box of the motor no flame should be able to come out through the cable gland in order to prevent fire hazards but where there is no presence of hydrocarbons i.e. no danger of fire hazards (IIA/ IIB) single compression glands are used.
- It has nothing to do with mechanical strength. Even in case of lighting fixtures used in IIC zone double compression glands are used.
what are the parts of Double compression Gland?
Parts of Double compression gland –
- Gland body
- Gland body Nut
- Cone
- Cone Ring
- Neoprene Rubber seal
- Rubber Washer
- Check Nut
what are the parts of Single compression Gland?
Single Comp Parts
- Gland body
- Gland body Nut
- Neoprene Rubber seal
- Rubber Washer
- Check Nut
- Flat washer
Also Read : 4-wire Transmitters Current Loops
can a neutral screen conductor be joined with different type of conductor