In Industrial process control, we need different types of interlock logic to achieve the desired control and trip functions as per the requirements.
The PLC interlock logic is used to provide priority to the input first operated to avoid any damage to the equipment and machines or to avoid any undesired interruption.
One of the logic is interlock with first input priority. Say we have a machine that can do 5 different types of functions. We have 5 different types of inputs available to control the machine operation but the machine will do only one function at a time as per the selected input.
If input 1 is selected then the machine will do function 1. Similarly, if input 2 is given to the machine then the machine will do function 2 and so on. Be careful that the machine may be damaged if two or more inputs are given at the same time.
Here in this case we need to write a PLC interlock logic such that whatever the first selected input has high priority. Meanwhile, if any other input is given to the machine then it has to disregard the other input until the present operation completes.
PLC Interlock Example
Consider a motor that can operate in two directions as per the operator selection.
The motor can rotate in the forward direction or in the reverse direction. But the motor can rotate in only one direction at a time.
If we give both forward or reverse commands at the same time then the motor will be damaged.
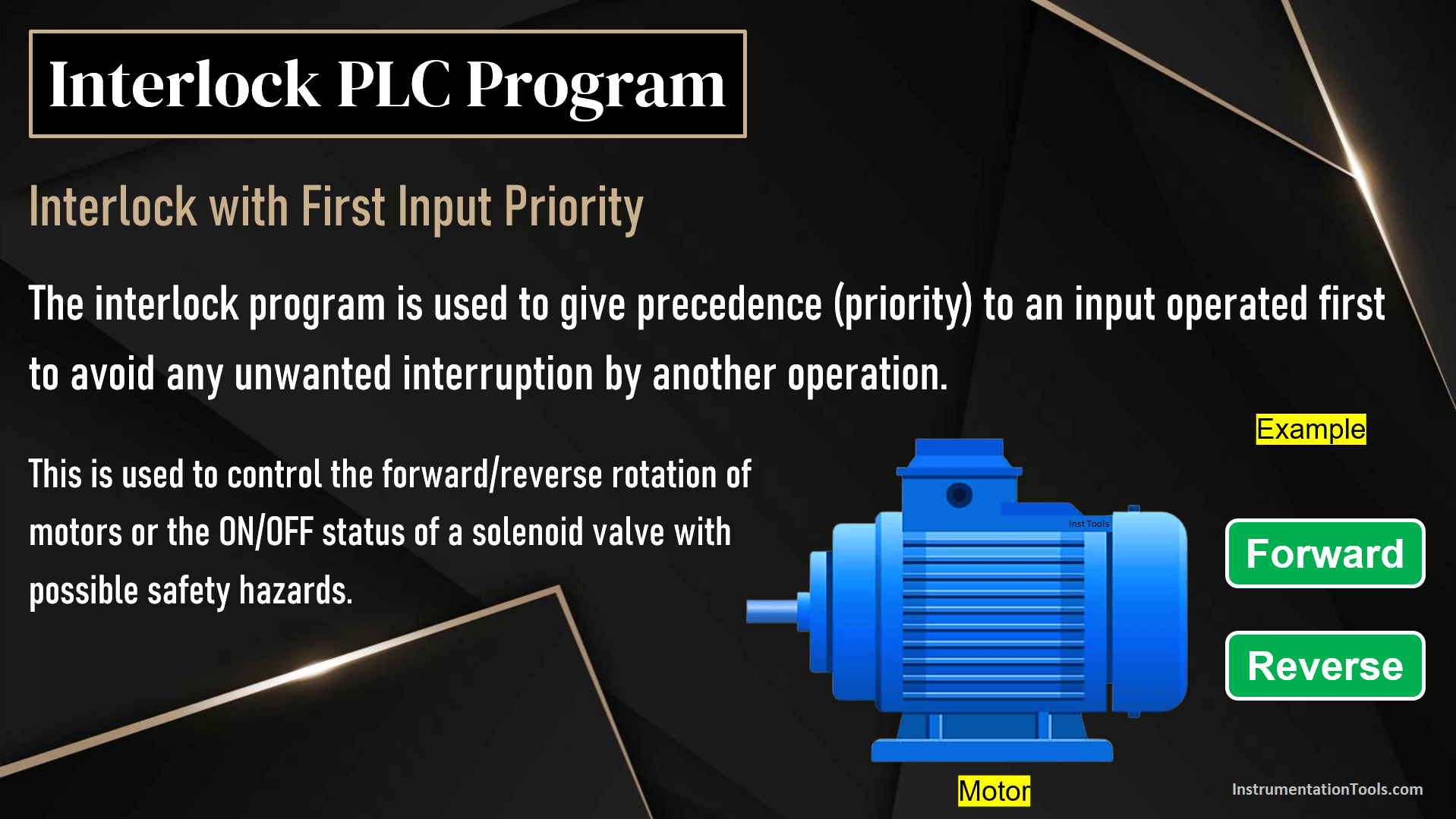
The operator can start the motor in the forward direction using a Forward selector switch and similarly, the operator can start the motor in the reverse direction using a Reverse selector switch.
Motor Forward and Reverse PLC Logic without Interlock
In general, the motor logics are equipped with many safety functions and other motor-related pushbuttons like start, stop, and emergency stop.
Here in this article, we are just focusing on simple forward and reverse logic for understanding the interlock program.
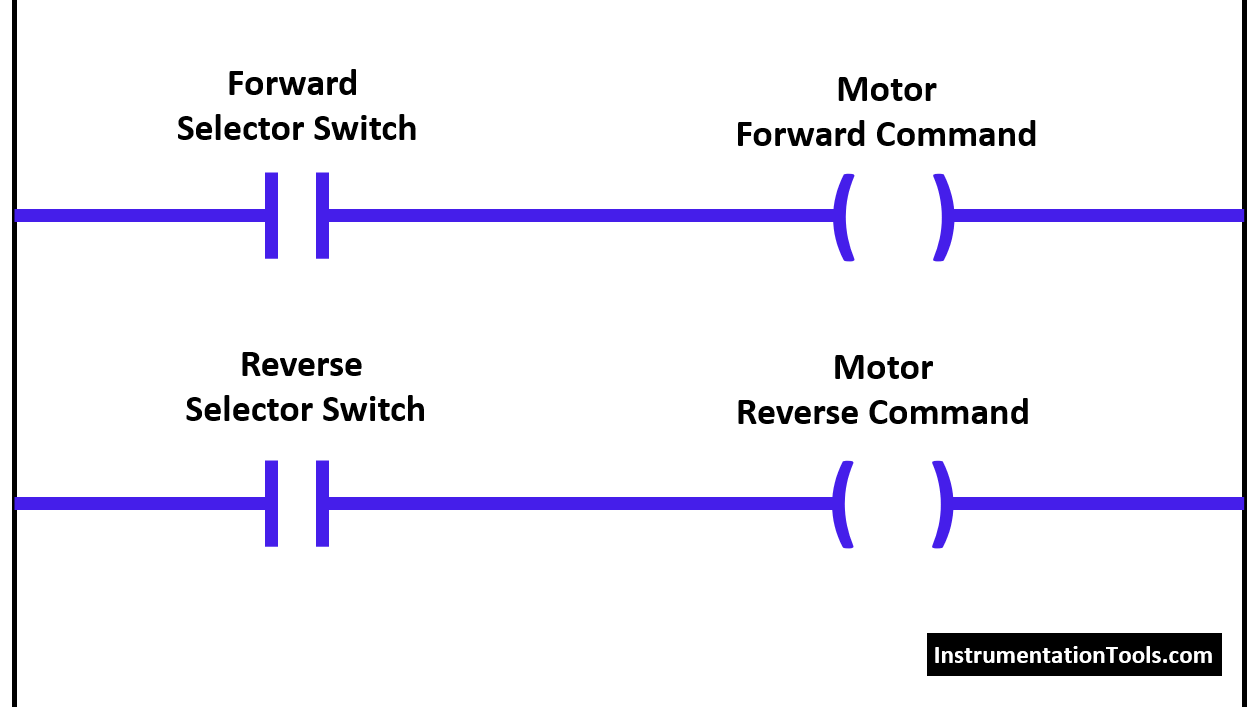
In the above PLC logic, when the forward selector switch is ON then the motor forward command will be initiated. Similarly, if the reverse selector switch is ON then the motor reverse command will be initiated.
In this logic, if both forward selector switch and reverse selector switch are ON at the same time then both forward and reverse commands will be initiated and these types of logic/situations damage the motors or any other machines.
Interlock Logic with First Input Priority
Now we can avoid these problems with help of an interlock program. This program is called Interlock with the first input priority.
We have to insert the Normally-Close (N.C.) status of motor output commands in the input side to implement this interlock logic.
Insert N.C. status of motor reverse command with the motor forward selector switch as shown in the below figure.
Again insert N.C. status of motor reverse command with the motor reverse selection switch as shown in the below figure.
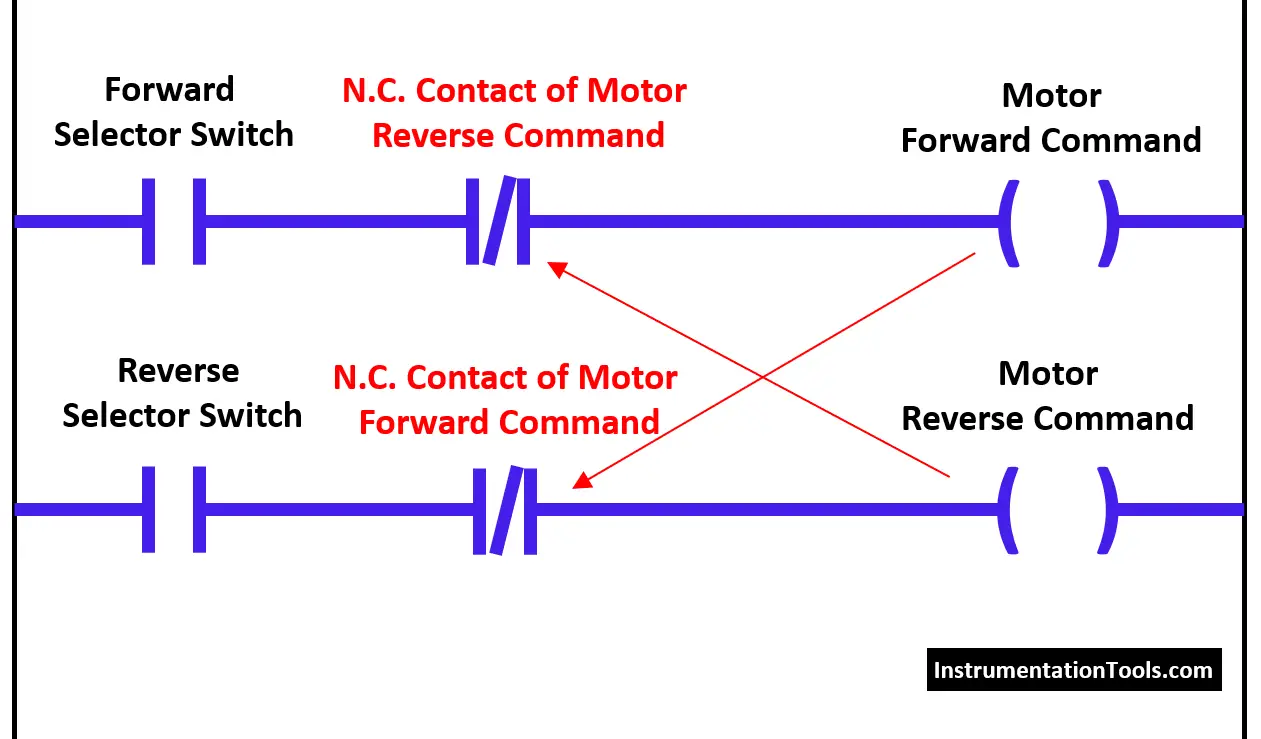
Initially, the motor will be in an OFF state so both N.C. contacts are in a close state.
Motor Forward Direction
Say if the operator started the motor in a forward direction then the N.C. contact of the motor forward command will be open in the second rung.
During this time, even if the operator activates the reverse selector switch then this command will not be initiated because N.C. contact is activated and it is open when the motor running in the forward direction.
Motor Reverse Direction
Similarly, if the operator started the motor in a reverse direction then the N.C. contact of the motor reverse command will be open in the first rung.
During this time, even if the operator activates the forward selector switch then this command will not be initiated because N.C. contact is activated and it is open when the motor running in reverse direction.
PLC Interlock Video Tutorial
In this video, I explained the importance of interlock logic with the first input priority.
If you liked this article, then please subscribe to our YouTube Channel for PLC and SCADA video tutorials.
You can also follow us on Facebook and Twitter to receive daily updates.
Read Next