Write the PLC program to control multiple pumps using programmable logic controllers. We have two input pumps used to fill a tank. Make sure pumps operate in an equal amount of time over their lifetime.
Multiple Pumps Control using PLC
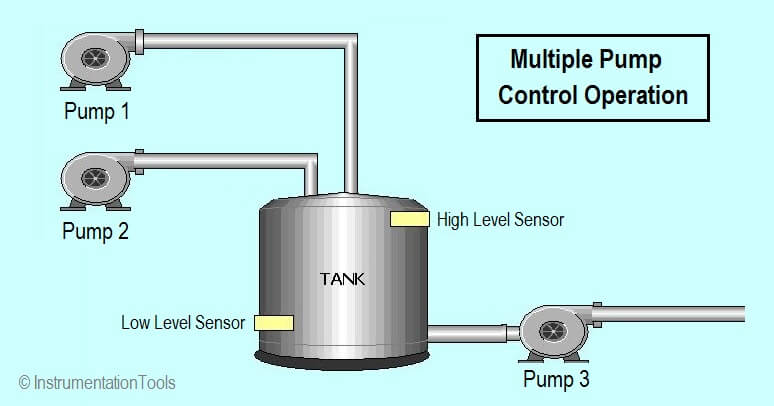
Program Logic:
Develop ladder logic program according to the logic given below,
- The start/stop push button is provided for control of the two input pump motors P1 and P2.
- The Start/Stop pushbutton station is operated to control pump P1.
- When the tank is full drain pump motor P3 is started automatically and runs until the low-level sensor is actuated.
- After 3 fillings of the tank by pump P1 control automatically shifts to pump P2.
- The operation of the start/stop pushbutton now controls pump P2.
- After 3 fillings of the tank by pump P2, the sequence is repeated.
PLC Program:
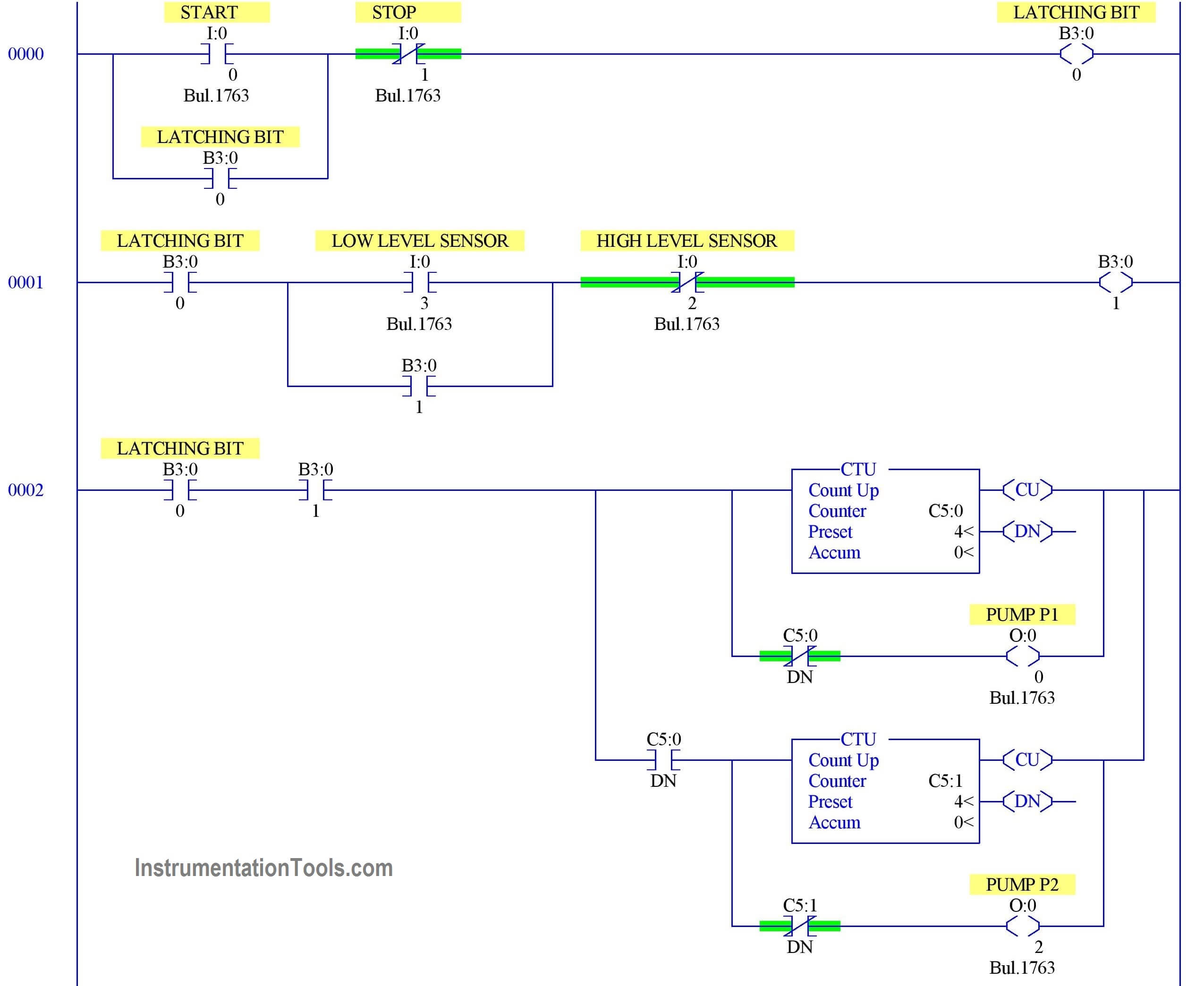
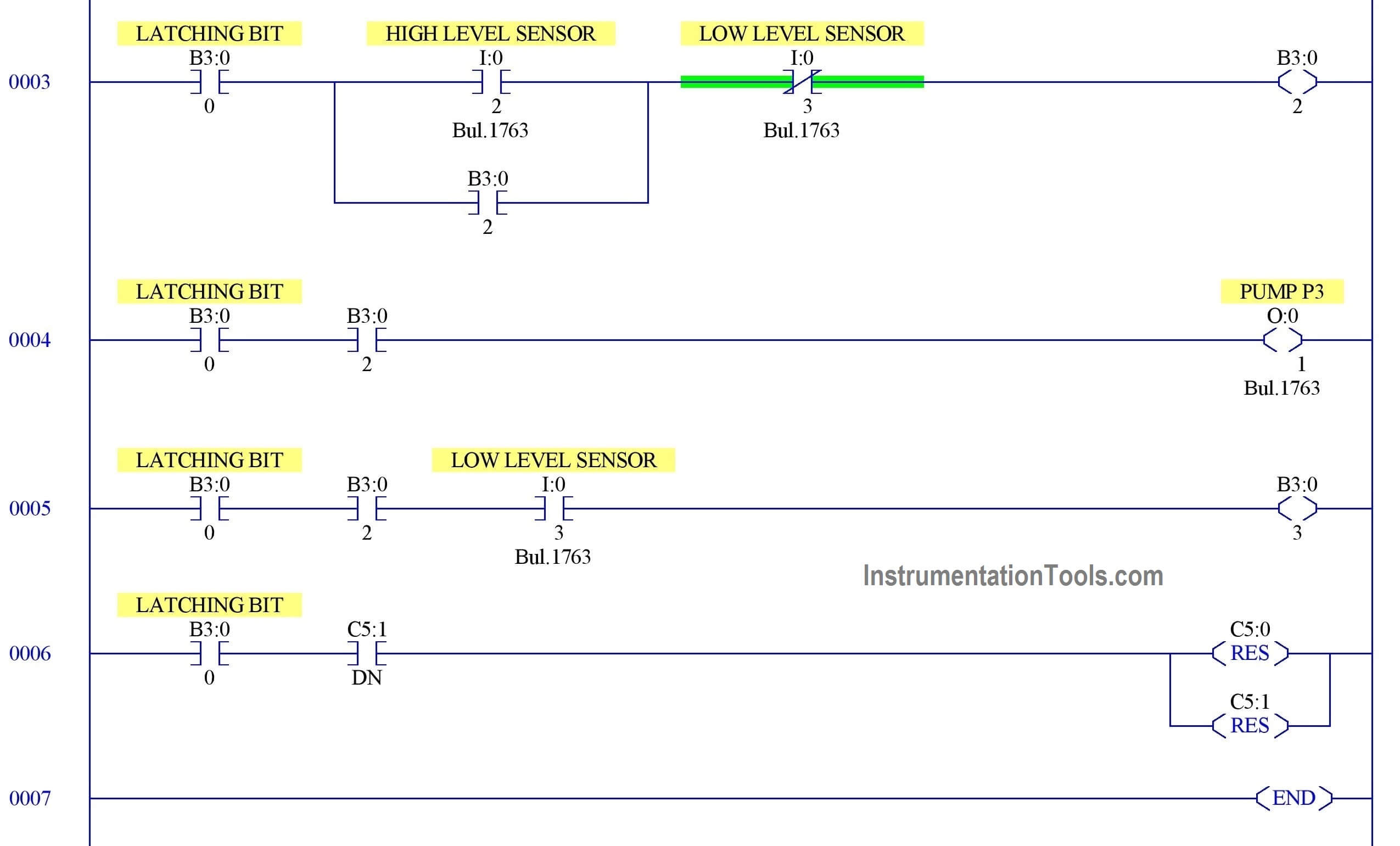
Program Description:
Rung 0000:
Start/Stop PB latched with memory B3:0/0.
Rung 0001:
B3:0/0 enabled to turn on B3:0/1 which is to turn ON PUMP P1 (O:0/0) when low-level sensor(I:0/3) turn ON and High-level sensor (I:0/2) is in off condition.B3:0/1 is latched with low-level sensor because pump p1 should not go off once water started rising.
Rung 0002:
Memory contacts used to turn on PUMP P1 (O: 0/0) with counter (C5:0).
Since we are going to shift pump operation from P1 to P2, two counters are used to shift between Pl and P2.
Counter C5:1 is used to turn on PUMP P2(O:0/2).
Rung 0003 & 0004:
B3:0/0 enabled to turn on B3:0/2 which is to turn on PUMP P3(O:0/1) when high-level sensor(I:0/2) turn ON and low-level sensor (I:0/3) is in off condition.B3:0/2 is latched with high-level sensor because pump p3 should not go off once water started reducing.
Rung 0005:
When Pump 3 (O: 0/1) is running, the low-level sensor turns on will make Pump p3 off and pump P1(O:0/0) ON.
Rung 0006:
Both Counter reset is done once the second counter (C5:1) done bit turns ON.
Conclusion:
We can use this example to understand the programming logic in AB PLC.
Author: Hema Sundaresan
If you liked this article, then please subscribe to our YouTube Channel for PLC and SCADA video tutorials.
You can also follow us on Facebook and Twitter to receive daily updates.
Read Next:
- PLC Example with Timers
- Traffic Light Control using PLC
- One-Shot Rising Instruction in PLC
- Count Running Hours of Pumps
- Communication between PLC & Energy Meter