The main difference between DCS and PLC is the business model which we discussed with comparison of DCS Versus PLC Architecture.
DCS versus PLC Architecture
The DCS business model can be said to be based on a monolithic integrated system by a single manufacturer.
DCS Architecture
For a DCS the controller, I/O-subsystem, database server software, engineering software, and operator software are all a single monolithic unit designed together and only work with each other.
It is not possible to use components from a third-party. It is not possible to use any of these components on some other system.
A DCS uses I/O-subsystem network and control network based on standard Ethernet, but with a proprietary application protocol, and typically only with a particular approved model of Ethernet switches.
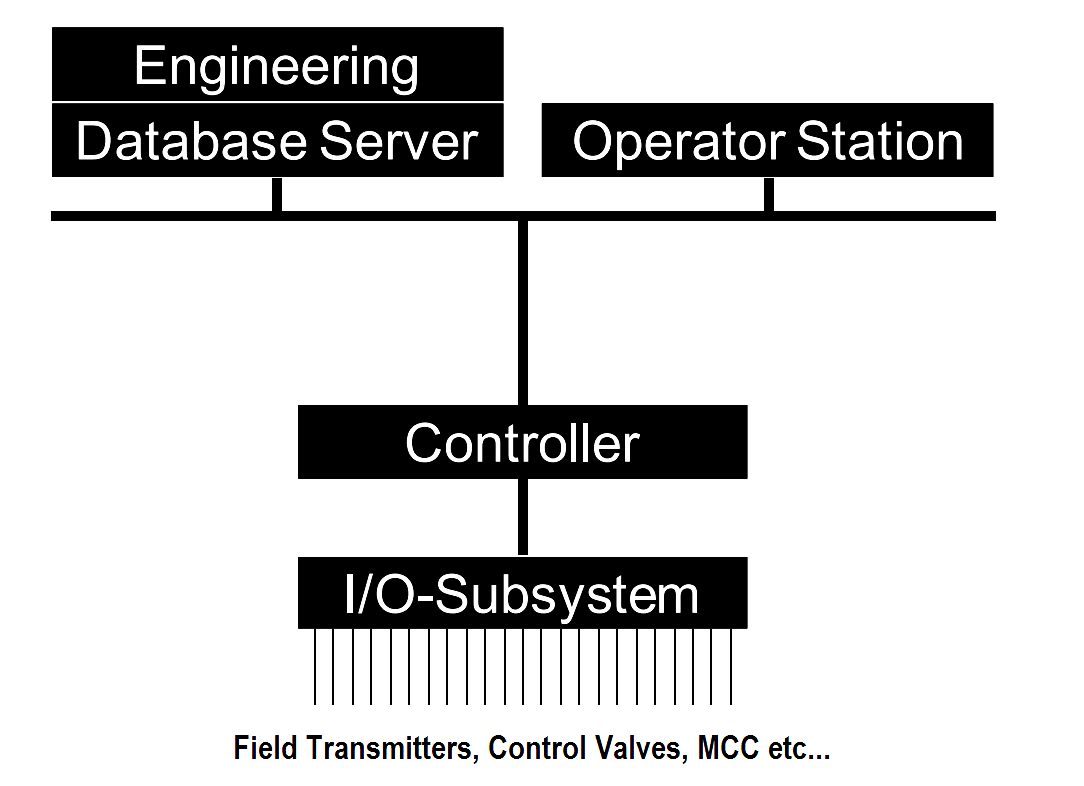
Figure 1 In a DCS all components come from the same single manufacturer
Only a specific version of Windows is permitted and only on one type of approved computer shipped from the DCS manufacturer.
These restrictions enable the DCS manufacturer to test everything together very thoroughly, on a very large scale, heavily loaded, with many controllers and work stations.
Applications like batch control, advanced control, and auto-tuning etc. are also tested together. This ensures there are no compatibility conflicts and unforeseen dependencies.
Thorough large-scale testing is possible because there is essentially only one type of each component so only one or very few combinations.
Third-party software is only permitted on separate “application stations” where it cannot conflict the native DCS applications and must be tested and approved by the DCS manufacturer; white-listed.
A DCS is monolithic using the same brand I/O subsystem, controller, and software, and single computer and operating system platform. This has been thoroughly tested on very large scale.
DCS Long Term Support
Systems typically remain operational for 15 years or more. During this time there will be several Windows versions, service packs, hot fixes, lots of virus definition updates, and computer hardware will need to be replaced too.
Typically DCS only support a single type of anti-virus software and whenever there is a new virus definition or when there is a Windows operating system service pack or hot fix, the entire monolithic suite of all hardware and software are tested together again by the system vendor prior to release ensuring the virus definition and service pack can be deployed without any compatibility conflicts.
DCS Upgrade
DCS versions are also upgraded as a single monolithic unit of all hardware and software such as I/O card firmware, controller firmware, server software, engineering station software, operator station software, as well as any other software are all upgraded together.
Any time there is a new system version all these components have been thoroughly tested together on a large scale by the system manufacturer in advance ensuring they are all compatible with each other.
Moreover, the online hotcutover process from earlier version to the new version has been thoroughly tested on a large scale ensuring smooth deployment at site.
It is this reassurance that thorough and large-scale testing provides which makes DCS very popular with large installations like petrochemical complexes. Such testing is made practical by the few combinations in a monolithic system.
PLC Architecture / Business Model
The PLC business model can be said to be based on flexible architecture by a system integrator (SI).
PLC Architecture
The PLC architecture is very flexible where each component can be freely selected from any of many suppliers. The PLC is the CPU with configuration software and IO-subsystem.
Sometimes the I/O-subsystem may come from a third-party. Even I/O cards that plug into the backplane may come from third-parties.
The HMI software is typically from a third-party. A native OPC server from the PLC manufacturer is typically best, but third-party OPC servers are sometimes used.
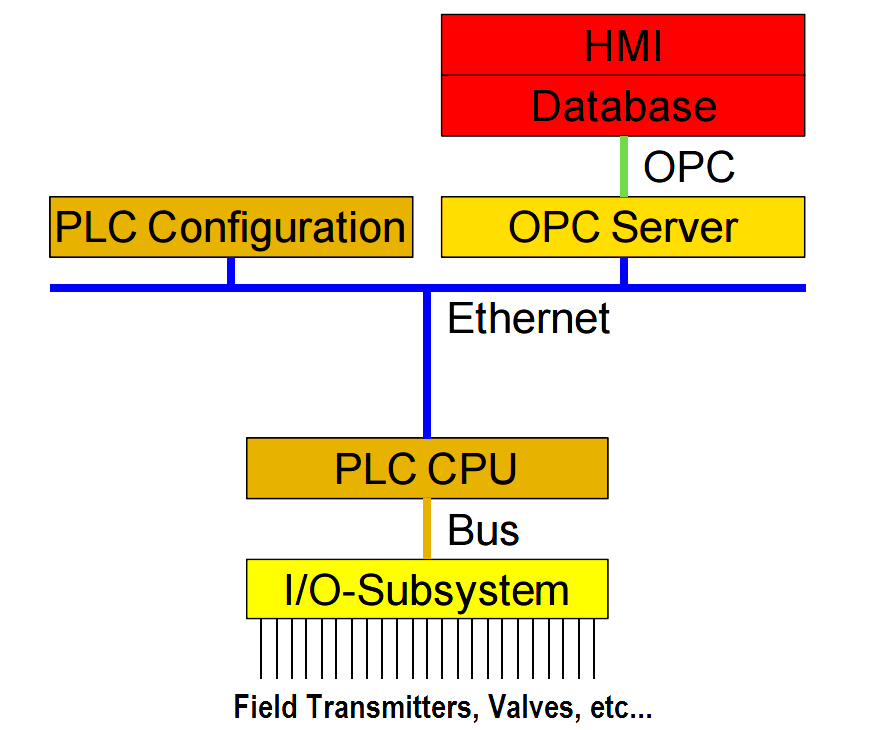
Figure 2 For a PLC components from different manufacturers are integrated
Basically any PLC works with any I/O-subsystem, OPC server, and HMI software because standard protocols like PROFIBUS-DP, PROFINET, Modbus/RTU, Modbus/TCP, DeviceNet, and EtherNet/IP as well as OPC etc. are used.
Networking gear, computers, and Windows version can be selected freely. Some components found not working are blacklisted.
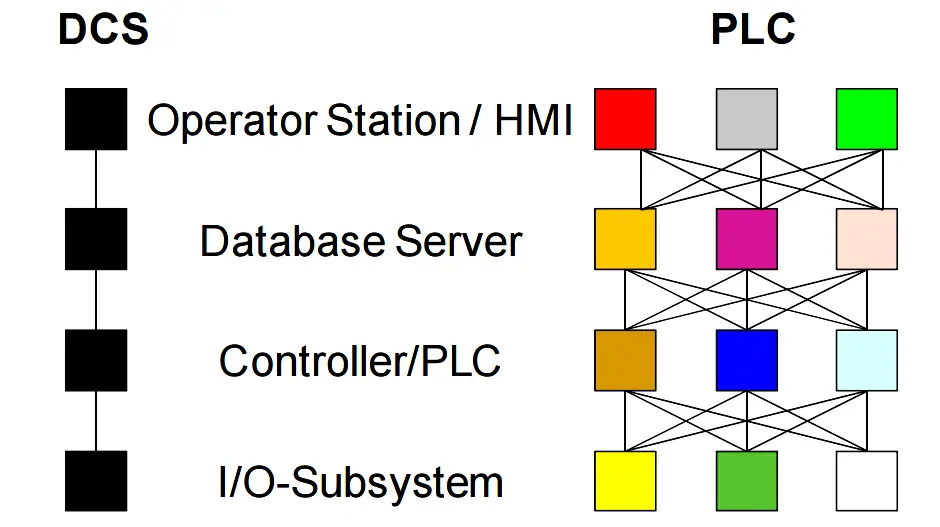
Figure 3 DCS uses a single supplier while PLC solutions combines multiple suppliers resulting in a large number of combinations
Note: Now-a-days single PLC package supplier also available
This flexibility enables hundreds of combinations of hardware and software making it impossible for these manufacturers to get together to test every possible combination of their hardware and software on each version of Windows before a plant decides to purchase.
Some combinations may be tested by the manufacturers involved, but it may or may not be on large scale with heavy loading.
A PLC permits any combination of I/O subsystem, CPU, and HMI/SCADA software, on a wide verity of computer and operating system platforms. Every combination cannot be tested.
The PLC manufacturer may supply all hardware and software components, all from the same manufacturer as many PLC manufacturers have acquired HMI companies. If so, this particular combination may have been tested more thoroughly than the other combinations tested.
Auxiliary third-party applications like batch control, advanced control, and auto-tuning etc. are generally not tested together as it results in an even greater number of combinations.
PLC uses proprietary configuration software just like DCS. That is, you cannot use third-party configuration software for your PLC, just like a DCS.
A native OPC server for the PLC is better than a third-party OPC server because the PLC configuration software generally automatically configures the address space for the OPC server.
PLC Long Term Support
During the 15 years or more of typical system operation there will be several Windows versions, service packs, hot fixes, lots of virus definition updates, and computer hardware will need to be replaced too.
Typically PLC has no restriction on anti-virus software or Windows operating system version so again the number of combinations of virus definitions, service packs, and hot fixes becomes too vast and impractical for these manufacturers to get together to test every possible new combination before a deployment in plants to ensure there will be no compatibility conflicts when deployed on the large number of combinations of hardware and software.
The PLC manufacturer may limit to a single anti-virus software and Windows version. If so, this particular combination may have been tested more thoroughly than the other combinations they test.
PLC Upgrade
For a PLC, hardware and software components are upgraded individually. That is, I/O-subsystem firmware, CPU firmware and configuration software, OPC server, HMI software, as well as any other software are all upgraded independent of each other.
Taking different versions for each option of components into account, the number of combinations becomes orders of magnitude larger.
This flexibility makes it impractical for these manufacturers to get together to test every possible combination of new versions before deployment in plants.
Testing the hot-cutover of one combination of versions to another combination of versions becomes nearly impossible.
The PLC manufacturer may supply all hardware and software components, limit to a single antivirus software and Windows version which are tested before deployment, and limit to single I/O-Subsystem Database Server Controller/PLC Operator Station / HMI, DCS, PLC system-wide version upgrades, and test hot-cutover before deployment.
This way the flexibility of the PLC would be abandoned to achieve the robustness of a DCS.
Article Source: eddl.org
If you liked this article, then please subscribe to our YouTube Channel for PLC and SCADA video tutorials.
You can also follow us on Facebook and Twitter to receive daily updates.
Read Next:
PLC Training Software Download
Sir ,
I have some information about PLC n dcs. I want to share it.
What is the procedure?
Great. You can mail me : [email protected] Thanks
Kunal mail me
can you mail me also, pls. [email protected]
@ Kunal please mail me as well. Thanks.
please mail me
Please send your updates to my mail: [email protected]
Hi, Please Subscribe to Newsletter : CLICK HERE
mr.kunal ,please mail my email [email protected]
It is very useful guide line for instrumentation.
Mr Kunal , please mail me , mail ID : [email protected]
Pl. share to Me also Mail Id:- [email protected]