A Wedge Flow Meter is preferably applied in difficult-to-meter line fluids, like air-entrained liquids, particular entrained liquids, high viscous liquids, or slurry liquids, which are abrasive or fibrous.
It is also applicable for clean liquids, gas/air, and steam. It consists of a measurement pipe with pressure taps in front and behind the flow element, a wedge restriction being welded into the measurement pipe from the top side.
Wedge Flow Meter
The pressure is measured in front of the wedge (high or dynamic pressure side) and behind the wedge (static or low-pressure side).
By determining the difference between these two measurements, which is called the differential pressure, the volume flow of the fluid can be calculated, as all other characteristics of the measuring points are constant.
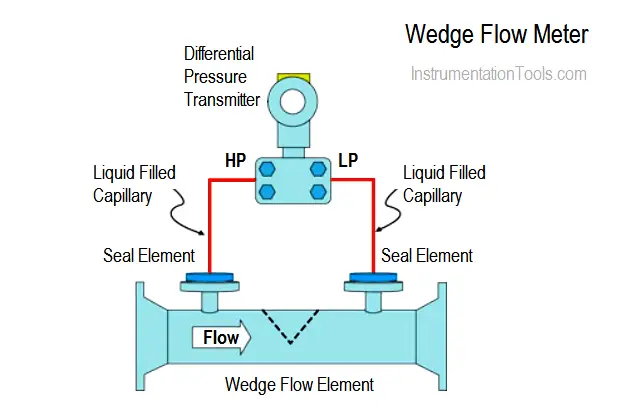
As the wedge has the profile of an isosceles triangle, the form is the same from both sides. So the measurement is possible in both directions.
The line fluid is forced downward similar to a segmental orifice plate, but is guided along a slopping “wedge” shape rather than a sharp edge. The pressure taps are located upstream and downstream of the wedge and in all cases are equipped with sealed sensors.
The differential pressure produced by the device is a function of the wedge segment opening (H) and the diameter of the body, “D” values as shown in the below figure.
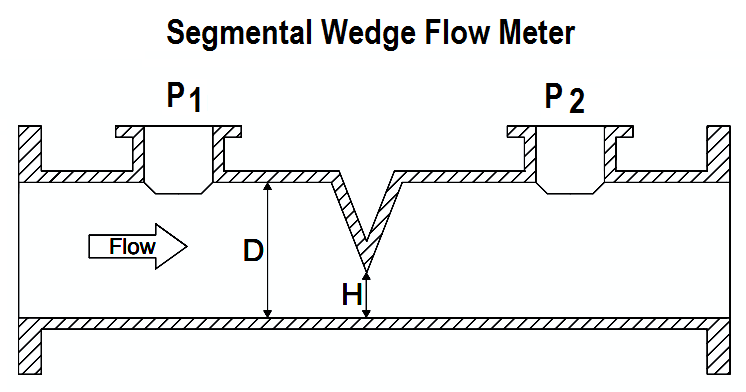
The calculations for compressible flow are similar but must take account to temperature and adiabatic expansion and compressibility factors.
Solids and other debris easily pass under the restriction of the wedge meter. The inherent ruggedness of the restriction resists damage to its measuring edge.
If you liked this article, then please subscribe to our YouTube Channel for Instrumentation, Electrical, PLC, and SCADA video tutorials.
You can also follow us on Facebook and Twitter to receive daily updates.
If you liked this article, then please subscribe to our YouTube Channel for Instrumentation, Electrical, PLC, and SCADA video tutorials.
You can also follow us on Facebook and Twitter to receive daily updates.
Read Next:
- DP Transmitter Interface Level
- Types of Vortex Flow Sensors
- Field Instrumentation Questions
- 3-15 psi to 4-20mA Conversion
- Why Turndown Ratio is important
Hello
I would like to add some information regarding the wedge flow meter. As most flow meters using differential pressure share a common flow equation, in principle, they are all created equal. Why you would select one geometry over another has to do with a couple of considerations.
1. What is the Reynolds Number of the process at flowing conditions? The wedge meter has a very stable discharge coefficient down to an Re# of 500. This is one reason the wedge meter is well suited in viscous or low-velocity applications. The discharge coefficient is a factor for all flow primaries that corrects the common theoretical flow equation for the manufacturing tolerances, tap location, fluid profile, and turbulence associated to the installed geometry.
2. The stability of the geometry under flowing conditions. The wedge meter is a very robust design that is well suited for withstanding impact and erosive forces. Therefore, the wedge meter is found often in slurry applications. However, it should be noted that a slurry flow application with a minimum Re# over 10000 could be measured by using a venturi as well with less permanent pressure loss.
I would like to make a point regarding the orientation of the process taps. In almost all cases the preferred installation is to have the instrument taps at 90 degrees on the pipe rather than at the top of the pipe. With the tap and wedge aligned at the 90-degree position, solids can still easily pass along the bottom of the pipe.
What we avoid is collecting entrained gas in the o-lets and impulse lines. Any amount of trapped gas will lead to error as the gas is compressible and will vary in amount as flow rates change and process conditions vary.