Pipeline project management is a vast subject, this article focuses on poorly executed front end loading (FEL) steps in midstream activities.
With growing clamour for clean energy globally, the midstream industry becomes crucial for any hydrocarbon exporting country. To have an effective midstream network, would mean construction & production costs also have a role to play in ensuring globally competitive & affordable prices of oil & gas products.
One could argue that short term and long term barrel prices apart from supply and demand is a motivating factor for operators to invest in hydrocarbon projects, but it can also be equally said, that despite what the global price or supply & demand is, effective project management & execution also determines the economic success for all project stakeholders.
Pipeline Project Management
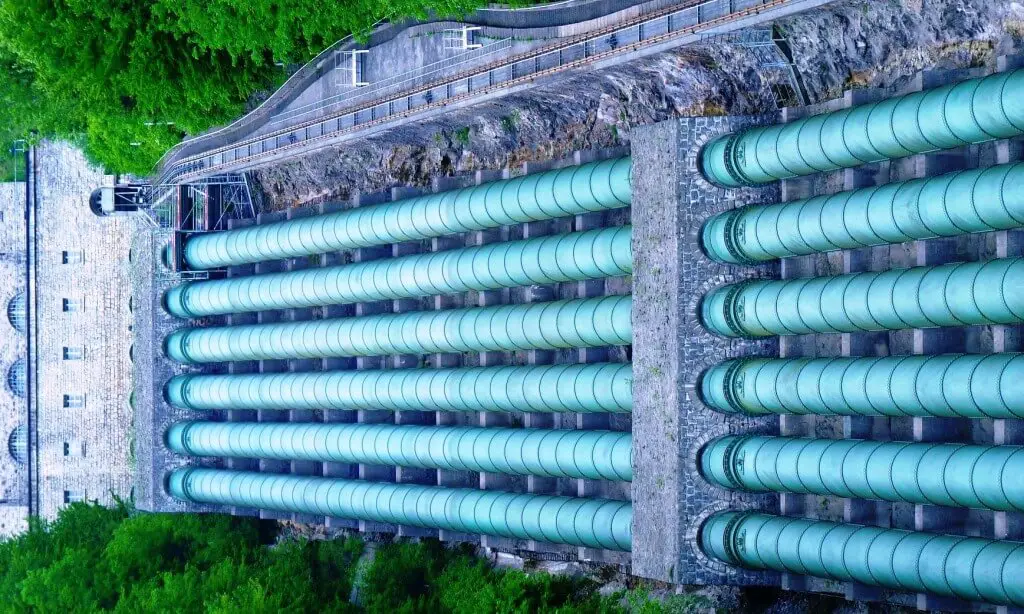
A key stage in midstream project management is Front End Loading (FEL) where strategic information that addresses internal and external risks, resource availability, allocation, and commitment is made before sanctioning or making a final investment decision (FID) on the project.
Simply put, the more homework you do in the early stages of a project decides how much success can be achieved.
This article focuses on some of the repercussions of poorly executed front end loading (FEL) steps in midstream activities.
Front End Engineering (FEED)
1.  Choosing Pipeline Sizes:
The starting point to design any oil & gas pipelines is the well production, pressure & temperature profile in addition to the composition of the contents that the pipeline will carry. Production profiles are needed to estimate the peak flow rates which the pipeline experiences and in turn determine the pipeline size, whereas the pressure and temperature profiles determine the pipeline wall thickness.
When your reservoir engineer and production technologist are indecisive about the Stock Tank Oil in place (STOIP), how much & at what rate the recoverable volumes from the wells are going to be extracted, chances are that you are going to underestimate/over-estimate the pipeline sizes.
In the case of multiphase flow, whether 2 or 3 phases, the pipeline sizes significantly affect your flow regimes and carry the risk of slug formation. The slug volumes decide the size of your slug catcher & underestimating its size can cause equipment failure. Hence work it out with your subsurface team to arrive at a conclusive and accurate production profile prior to performing pipeline FEED.
2.  Material Costs Overrun:
Nothing can be more disastrous than realizing as the project progresses that your pipeline actually costs more because of underestimating the pipeline’s wall thickness. Wall thickness is a key value that depends on the design pressure & eventually determines the pipeline weight.
Since pipeline weight is proportional to the square of the outer diameter (OD), for every millimeter increase, so does the weight increase. When the parabolic increase per unit pipeline weight is multiplied with the total kilometers of pipeline length, the pipeline material costs are going to probably overrun the project budget.
Therefore, it is not just the engineering standard chosen, but following this crucial step as part of a checklist prior to finalizing the pipeline sizes is a must.
3.  Pipeline Corrosion:
Various Engineering design practices offer solutions as to what should be the corrosion allowance for a given pipeline application. Produced water and Hydrogen sulfide (H2S) are the popular enemies that contribute to pipeline corrosion. In addition to pipeline contents, sand from well fluids that escape sand traps, hydrate particles and fluid flow rates exacerbate metal erosion. However, engineers sometimes fail to account for the effect of external forces.
In offshore pipelines, sea waves and sand underneath the soil act upon the pipeline components such as risers thereby inducing stress. Human error also needs to be taken into account where, when ships collide with platforms, it can cause dents from where corrosion propagates.
Pigging operations and depressurization to dislodge hydrates can also contribute to pipeline corrosion simply because pigs can cause dents when their velocities are not regulated properly resulting in the pig getting stuck. When hydrates get dislodged during a depressurization, there are good chances that a high-velocity column of hydrate can collide with pipeline bends thereby cracking and exposing the metal to corrosion effects.
Therefore, a key step during FEED is for engineering teams to take time out and allocate resources to do a pipeline stress analysis, on-bottom stability analysis, a basic corrosion management plan covering pipeline coatings & cathodic protection, a risk assessment report and Pipeline Integrity Management (PIM) report to ensure that the wall thicknesses & supporting structures chosen are adequate to meet all internal and external risks that the pipeline can experience.
If one argues that this is a far fetched vision during early FEED, wait till you see blame game that starts during the detailed engineering stage because of material cost overruns.
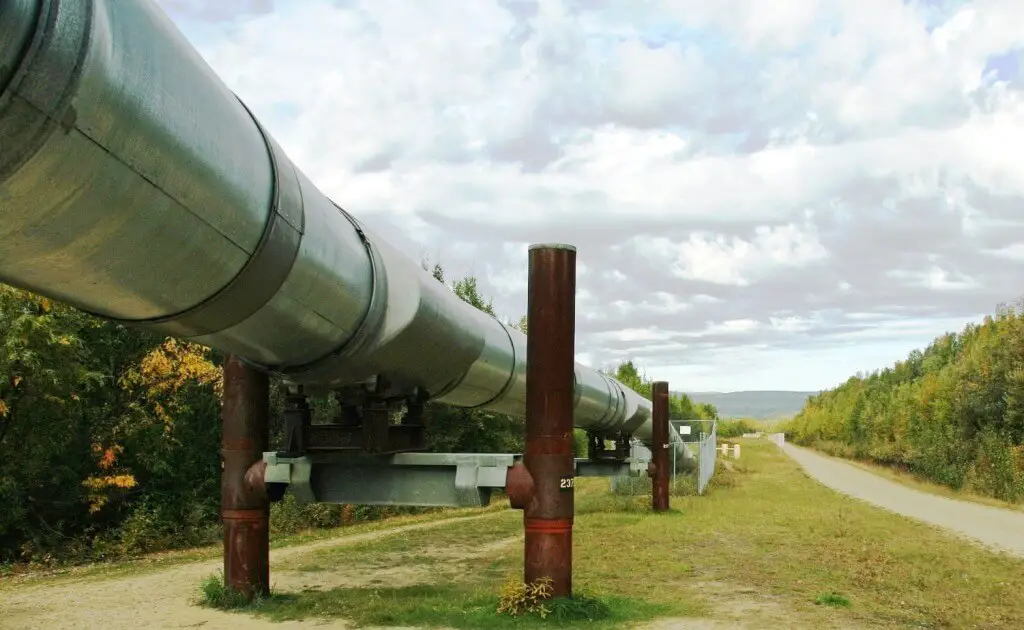
Contract Management
1.  Vendor Contracts:
As much as the top management works on the terms and conditions of a production sharing contract (PSC), taxation, governmental regulations, etc. that shows its effects on the company’s balance sheets, so must the procurement department spend time due diligently to ensure that the right vendors are available to deliver material and equipment which affects project schedule and costs.
A classic case of project cost overrun is when the procurement department realizes that there is only one particular vendor to meet your project requirements after the project has been sanctioned. If a procurement strategy and supply chain are not in place, it can leave the project to the mercy of the sole vendor.
Hence ITT (Invitation to Tender) documents must be prepared at the earliest to receive competing offers from various bidders which in turn allows project managers to prepare realistic schedules and costs incurred.
2.  Interface Management:
Project management also includes interface management. In midstream projects when facilities such as booster compressors, sectionalizing valves & burn pit lines are vendor items, it is important for contractors to keep a constant open line of communication with vendors to ensure that the engineering & hook-up drawings and datasheets have been followed to meet project specifications prior to execution.
There is nothing more upsetting for project managers to watch their tables pile up with Change Orders (CO). When equipment that is already manufactured & delivered to the site but does not conform to the project specifications because of poor communication with the vendor, it is the homework of developing a contracting strategy, regular project review by engineering teams at the early stages which can minimize the damages to the project’s cost & schedule. Otherwise even your legal department might be left out in the open to dry under the sun.
3.  Man-hours Billing & LSTK:
Between Projects awarded on man-hour billing vs. Lump sum Turn key (LSTK) contracts, in reality, it depends on factors such as – how well the project owner defines the scope & shares the project vision.
During FEL stage of long term projects, if project charters that have requirements changing dynamically and frequently, chances are that the engineering contractor would hesitate to engage with the project owner on LSTK basis (unless the contractor is desperate for the money to keep his company afloat).
Basically, if the project requirements are not expected to change much during the course of the project, the project owner can negotiate to put the budget and schedule risks on the contractor on LSTK terms.
But to be practical, there is no project, where complete clarity is always available prior to Sanctioning/FID. Hence it is prudent for project owners to keep their options open to enter into a mixed contract where both man-hour billing and LSTK methods provide flexibility, transparency, accountability, and ease of management to the project.
Typically FEED follows a man-hour billing cycle & Detailing work follows LSTK terms. For such mixed contracts, the onus is on the engineering contractor to prove transparency and accountability during and after the man-hour based FEED by maintaining clear open book records on the project progress & work delivered.
This is important for the project owner to assess, if the scope of work (SoW), quality and execution schedule has been met to satisfaction and avoid feeling like cab passengers who constantly suspect if the cab meter is functioning correctly. This also allows project owners to assess if re-work through change orders will become a habit during the detailing phase of engineering.
4.  Under/Over Quoting:
When contractors lack experience with similar projects in the past to determine what it takes to execute a project, he either ends up working for free on all that ‘extra’ SoW or losing the E&C contract to a brighter guy. Therefore if you are a small contractor, start small.
5.  Take Benchmarking Seriously:
High FEL projects or projects that have clear vision, clarity, and scope are expected to have shorter schedules, predictable costs, and completion in all respects.
Benchmarking with similar projects that had sound contracts with reputed suppliers gives a good idea where your project is heading towards, quicker and confident final investment decisions (FID) and also aids in eliminating uncertainties that warrant excess contingencies.
6.  Project Economics & Standardization:
When projects run on low-profit margins, instead of cutting corners and getting into trouble, it is more sensible to first understand how project economic factors such as direct & indirect costs, revenue, margin, overheads, taxation, etc affect the project’s profitability.
Contracts made with vendors who employ Product Standardization, maintain sound balance sheets, the ready availability of credit better bet to ensure your project’s vendor items are delivered on time to meet project schedules and quality.
Therefore, it is preferable during FEL for procurement teams to refer back to previously approved contractors who meet the project owner’s business objectives because they better understand the Project Owner’s requirements.
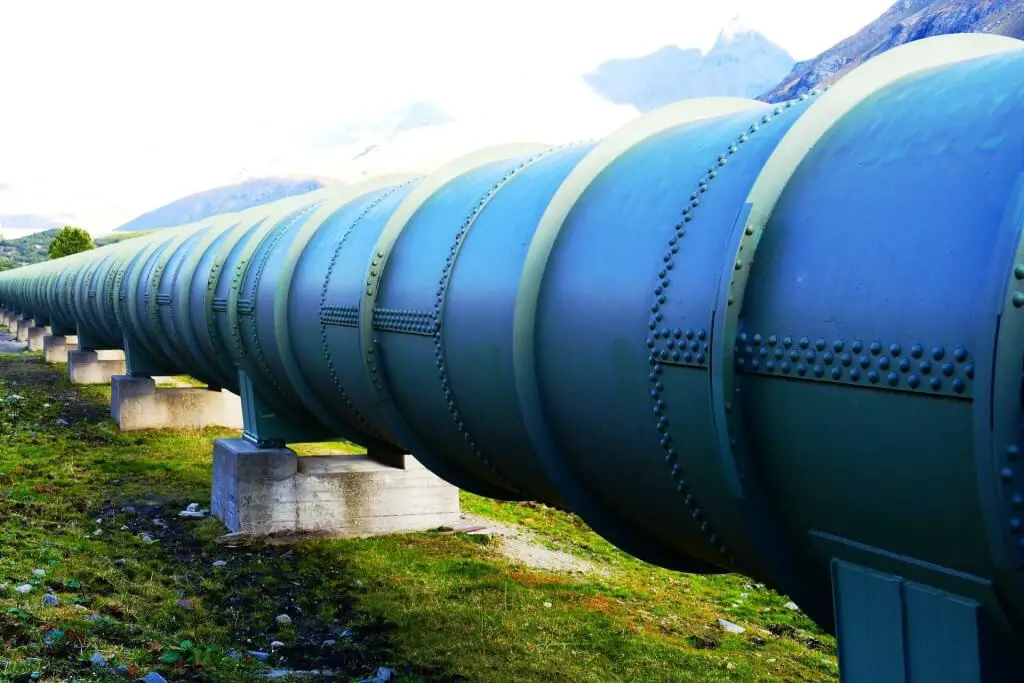
Local Laws & Regulations
1.  Pipeline Location Markers:
It is no doubt a momentous joy in meeting project requirements, executing, completing, running a guarantee test, handing over the keys of the facilities to the project owner & closing the business deal.
But if a buried natural gas pipeline that runs through large localities of human occupation without any pipeline location markers & the local government body in-charge of laying roads & electrical cables hit the gas pipeline while digging up, in all likelihood the incident will hit the tabloids when there is an explosion.
Hence always have an emergency response plan of action as part of the project plan with constant communication with local civic authorities.
2.  Right of Way (ROW):
Project Owners, Project Managers, project engineers, and all relevant stakeholders have the duty to follow all local laws and meet environmental regulations. When project owners skip such an early FEL step & Engineers are busy proving their caliber laying an above-ground gas pipeline laden with high H2S content through a forest area with no cognizance of the local habitat or environmental regulations, one wouldn’t want to see an elephant stepping on it.
When the pipeline ruptures, with all that hydrogen sulfide laden gas spewing out killing the surrounding habitat due to poisoning & explosions, the project owner can be sure to become the next subject of a Hollywood movie or a Greenpeace Activist’s Documentary.
In protected habitats, the ROW of local flora & fauna gains first priority over Project Owner’s ROW. Therefore, project managers have the mandatory task of keeping track of Local environmental regulations from the earliest stage of Front End Loading.
3. Planning ROW Path:
Not all projects are expected to receive the kind of budgets to build oil & gas facilities in one go and hence projects are implemented in phases. Sometimes, though budgets are sanctioned, projects are not implemented considering unforeseeable poor market demand.
In the event where the project is expected to go through a later stage expansion or when an underestimation of market demand causes downsizing the infrastructure but market demand increases at a later stage, the existing pipeline capacity becomes insufficient to transport.
In such cases, it is prudent to plan early during the FEL stage to acquire and accommodate additional ROW for future pipeline expansions. However, to do so, local landowners and governmental authorities must be consulted early to acquire the requisite land and approvals for gaining ROW rights.
References: [1]
Author:
Vijay Sarathy holds a Master’s Degree in Chemical Engineering from Birla Institute of Technology & Science (BITS), Pilani, India and is a Chartered Engineer from the Institution of Chemical Engineers, UK. His expertise over 10 years of professional experience covers Front End Engineering, Process Dynamic Simulation and Subsea/Onshore pipeline flow assurance in the Oil and Gas industry. Vijay has worked as an Upstream Process Engineer with major conglomerates of General Electric, ENI Saipem and Shell.
Read Next:
- Pre-commissioning Activities
- Project Planning & Implementation
- Fire Alarm System Commissioning
- P&ID Guide for Pressure Safety Valves
- Documents for CommissioningÂ