In our professional career, it is mostly required to do some things as per planning and efficient checking. A proper approach to this gives a very reliable and error-free output. So, people who work by planning always get to see proper outputs in their work. One term which is not known to many, but is very useful is PDCA.
PDCA is widely used in businesses and industries to get proper changes in processes, functions, services, and products. As industries have various sectors in it, one such sector where PDCA is very useful is maintenance. In this post, we will see the concept of PDCA in industrial maintenance.
What is PDCA?
First of all, let us understand the meaning of PDCA. PDCA stands for plan, do, check, and act. As the meaning says, it is all about planning things before executing a work.
In a simple sense, if you imagine a world in a big industry with improper planning, then you know how damaging it can be to a business. Be it a big or small industry, planning is of utmost importance.
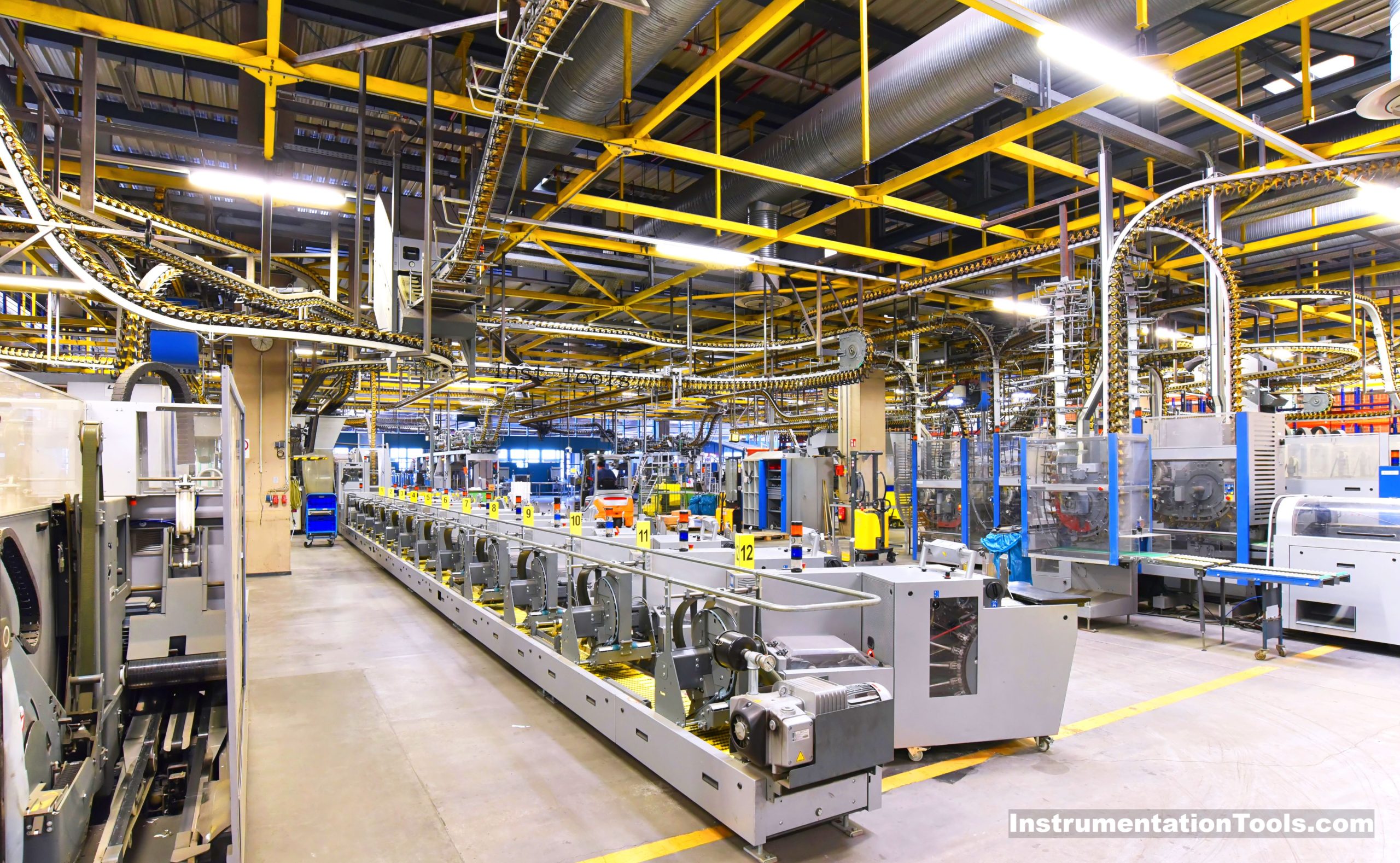
But generally, people just assume that planning things will automatically do work for them. Mere planning is not required, as the next step will be to do it properly and check if it is working properly or not. If working then it is not an in issue; but if not working, then it needs to be acted upon and corrected. So, after planning, the work needs to be executed properly with testing and troubleshooting.
The main goal of this is to avoid repetitive works. Because, once tested, you will not face issues in working on the system again and again. It is like you have once designed a prototype, there is no need to design on that system again.
It is just about execution then. The PDCA cycle thus helps to increase productivity, reduce errors, get a structured approach, solve problems quickly, standardize functions, and enhance continuous outputs with improvements.
As discussed with keeping our scope in mind, PDCA is a very important phase in industrial maintenance. Let us first understand all the four basic aspects one by one.
Plan
This is the first step in the action. As the name implies, you first need to plan the work. If you go out to work and do not know what to do, then how will the work happen? So, planning helps in identifying past issues, improving quality steps for that, resource allotment, setting goals after that, and defining objectives.
Do
The next stage comes for execution. Once you have planned everything, then you need to ensure that the work is done according to that only. For that, you need to read the plans properly and work according to that only. It is thus essential that the planning is proper, so that the execution happens properly.
Check
Once you execution is completed or under process, you have to check whether you have got the desired output or not. This will be on continuous basis or on some frequency basis. So, testing and checking the system during or after execution is a very important part of the process.
Act
Once you identify the issues or get to know what was wrong during testing, you have to act accordingly and implement it. The implementation must be done in such a way that the bugs get resolved and does not occur again during next implementation. It means that a new approach will now be taken to execute the system from start to end once again. Results are not important; process is important. Once your process is set, results will become good automatically.
PDCA in the Industrial Maintenance
Now that we are clear with what PDCA is, let us see how it works in industrial maintenance.
As maintenance deals with maintaining systems or troubleshooting issues when found, the first step lies in identifying issues. During maintenance, you are required to do a fixed set of goals; but when you find that some regular issues occur during maintenance or above all, if you find some new problem, that needs to be addressed. This is the first step before starting PDCA, because if you do not know what is the problem, then there is no use of planning and executing it.
Once the issues have been highlighted, the next step is to plan the action for the same. Apart from regular maintenance, you now have to address new problems found. So, a team that is set must be able to solve everything. This planning must be communicated to them in a systematic manner.
Now that you have the plan ready, it’s time for execution. All the maintenance tasks must be carried on time and schedule, because maintenance work does not come daily. And the most important thing is to stick to the plan that has been scripted for doing the job. As maintenance works deal in stringent time, proper discipline and sticking to adheres is a must.
Once the work has been completed, you have to check now whether everything is working fine or not as per the desired plan. This can be done by measuring things like how much time it took, and how effectively the system is working.
If any issues are still found, then it needs to be resolved immediately; because once the production starts, you won’t get time to maintain or check the system immediately. This act will then start to fine tune the system and once done, your system is ready to be given to production team once again.
If you liked this article, then please subscribe to our YouTube Channel for PLC and SCADA video tutorials.
You can also follow us on Facebook and Twitter to receive daily updates.
Read Next:
- Shutdown Maintenance
- Motor Maintenance Guide
- DCS System Maintenance
- Pressure Gauge Maintenance
- Maintenance of Electrical Drive