Shutdown maintenance is a routine procedure for many work environments, ranging from industrial plants and laboratories to virtually all other production facilities operating within the manufacturing industry.
Unlike routine maintenance checklists, the purpose of shutdown maintenance is generally to service larger machines, equipment, or electrical systems that are usually always powered on in order for your plant to operate.
As a result, shutdown maintenance procedures are scheduled at routine intervals and with the assistance of a licensed electrician in order for the procedures to be completed safely and with minimal unforeseen disruptions to plant productivity.
Shutdown Maintenance
There are 5 phases of the shutdown maintenance procedure that must be followed in order for maintenance to be completed adequately and efficiently.
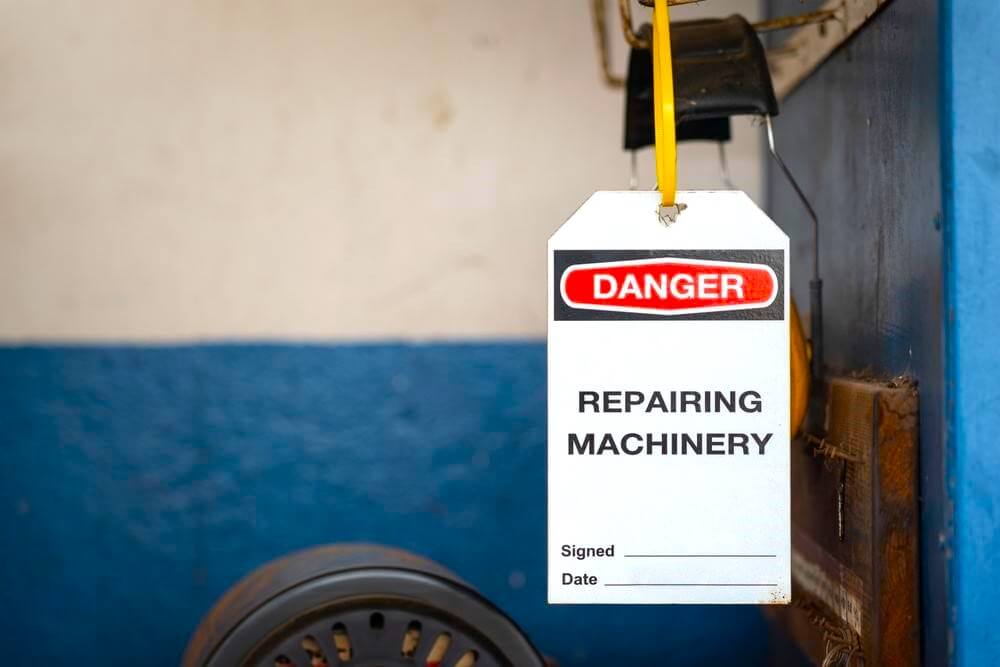
Weāll be outlining each of these five phases below.
- Initiation
- Planning
- Scheduling
- Execution
- Evaluation
1. Initiation
The first stage of conducting shutdown maintenance naturally involves determining what tasks need to be performed once your facility has been shut down. In other words, this preliminary initiation phase should involve developing a maintenance checklist for your staff to follow.
Alongside preparing your shutdown maintenance checklist, the initiation phase should ideally also include organizing maintenance objectives and developing log-keeping procedures to adequately track any deviations that may occur when meeting these objectives.
Some examples of maintenance objectives include shutdown maintenance occurs:
- within a consistent timeframe to reduce impacts on productivity,
- within a consistent budget to reduce cost efficiency,
- with minimal disruptions and hazards to staff.
Log-keeping should also outline the dates that maintenance was conducted, the duration of each shutdown period, all of the equipment that was inspected, the tasks that were performed, the contact information of any third-party assistance used to conduct maintenance, and the name of the supervisor on shift at that time.
2. Planning
Once youāve outlined what tasks must be completed during your upcoming scheduled shutdown maintenance, youāll want to ensure that you and your staff have access to guidelines that must be followed when conducting that maintenance.
Planning out your scheduled maintenance will involve allocating staff members to each maintenance task and ensuring that all staff is equipped with the necessary tools and equipment in order for that maintenance to be conducted smoothly and efficiently.
The planning phase of your shutdown maintenance should also involve making considerations for pre-shutdown and post-shutdown processes, alongside overseeing maintenance tasks as they happen. Having clear and concise protocols in place throughout your scheduled shutdown maintenance will undoubtedly reduce the risks of failing to complete any necessary maintenance tasks during the shutdown, and the likelihood of experiencing a workplace incident as a result of poor planning.
3. Scheduling
Continuing on from planning the logistics of your shutdown maintenance procedure, maintenance supervisors should also ensure that theyāve finalized the schedule for maintenance at least one week to four weeks in advance (depending on the size of your facility and workforce) in order to provide their staff with plenty of notice.
This notice period is essential for ensuring that all staff members who are required to conduct or oversee maintenance will be available at the time that maintenance is scheduled to occur, and that no time-sensitive production tasks are scheduled to occur simultaneously with your shutdown maintenance.
Scheduling your shutdown maintenance should also take into account the availability of any third-party professionals like electricians or engineers who are expected to be on-site to facilitate, oversee, and sign off on any specialized maintenance tasks that have been planned to occur. Be sure to contact these independent specialists or technicians a few weeks in advance to reduce the risks of scheduling conflicts.
A dedicated shutdown scheduler position can be assigned to a supervisor in your workforce to ensure that specialists are contacted as promptly as possible and that on-site staff receives clear notice that shutdown maintenance is scheduled to occur.
Itās also worth developing a contingency plan for your shutdown maintenance if any necessary people are absent from scheduled maintenance processes due to unforeseen circumstances. Are there other site supervisors who may be able to be on-call during scheduled maintenance?
And will there be multiple electricians, engineers, or other specialists available on-site or on your business premises if theyāre required? Having answers to these questions can play a vital role in making sure that your scheduled shutdown maintenance can be conducted without a hitch.
4. Execution
Now with all the planning out of the way, itās finally time to go ahead with your scheduled maintenance and commence with shutting down all the machinery and equipment on your plant and premises. Any assigned maintenance supervisors will be in control during the shutdown process, and as such is responsible for ensuring that all machines and equipment are powered down safely and with expert handling.
If there are any unforeseen problems like potential interferences to scheduled maintenance tasks, the maintenance supervisors should detail these issues to scheduling supervisors alongside adding records to maintenance logs. Keeping a record of these interferences can help reduce the risk of these interferences occurring in the future, as rectifying these issues can be included in preparation processes for future scheduled maintenance.
Remember that although these 5 phases are a universal guide for conducting shutdown maintenance, all maintenance processes managed by industrial plants and other highly technical workspaces are usually always tailored to fit that working environment. You should feel comfortable amending your processes to align with records of past maintenance logs.
5. Evaluation
Finally, once all machinery and equipment have been powered back on and maintenance logs have been finalized, all thatās left to do is review recordings gathered by your maintenance supervisors and all other technicians that may have been enlisted to complete specialized maintenance tasks.
The evaluation phase of your shutdown maintenance procedure is essentially where site supervisors can assess the efficiency of any scheduled maintenance, and amend procedures to further streamline maintenance processes.
Simply put, taking time to adequately evaluate the completion of your maintenance tasks alongside the overarching timeline of scheduled maintenance, can help site workers identify any barriers to the efficiency of your maintenance, and work to remove those barriers.
Removing those barriers will naturally allow your scheduled maintenance to occur in a smaller time frame, further minimizing the impact of scheduled maintenance on plant productivity and profitability.
Conclusion
With all five phases of the shutdown maintenance process now complete, all thatās left to do is prepare for your next round of scheduled maintenance. Be sure to utilize any information gathered from your maintenance logs and make space for any introduced machinery or equipment in order to keep your maintenance processes clear and concise, yet consistently adaptable.