Oil burners basically may be divided into two groups. Those used in conjunction with domestic heating systems and those used in industrial heating systems.
This article focuses mainly on popular industrial oil burners.
Oil Burners
The purpose of the burner is to mix the fuel with enough air to cause heat release from the fuel. This act requires the combustion of the fuel, but the combustion takes place outside the burner, that is at the tip.
The performance of the burner is achieved by proper air-fuel mixing. The good burner mixes well and liberates a maximum amount of heat from the fuel. A poor burner does not accomplish this task well at all.
Oil burners for industrial use are usually classified according to the method used for atomizing the oil.
Types
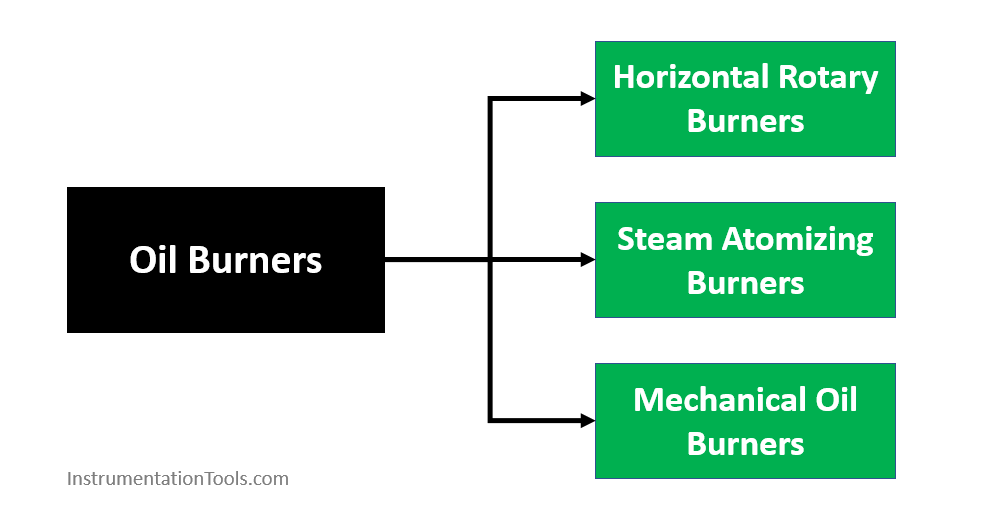
We discuss three popular burners used in industries.
They are
- Horizontal rotary
- Steam atomizing burners
- Mechanical oil Burners.
Horizontal Rotary Burner
This type of burner enters the boiler or furnace on a horizontal plane, and prepares oil for combustion by centrifugal force.
Fuel is atomized by a horizontal rotary burner by a combined action of the atomizing cup and the primary air stream.
Burner Controls
There are three types of control systems that can be used with the horizontal rotary oil burner:
- Manual
- Semi-automatic
- Automatic
Manual Control
It requires the presence of an operator to start and shut down the burner and to regulate the firing rate while it is in operation.
The flow of oil, primary air, and secondary air can be adjusted separately, or arrangements can be made to adjust them simultaneously.
Semi-automatic Control
 It is necessary that the presence of an operator to start or shut down the burner but is equipped with controls that automatically regulate the rate of firing while the burner is in operation.
Automatic Control
In this control, the burner starts automatically, ignites the oil, and regulates the firing rate to follow the load while it is in operation.
The burner can be automatically controlled in many ways.
Method 1
The oil flow is adjusted by the pressure or temperature controller.
If the required rate of firing is below the minimum rate of the burner the burner shuts down and the controls reset so that the burner will operate at its maximum rate of firing when it is relighted.
Method 2
The rate of adding the oil is controlled by regulating the supply of primary and secondary air.
Method 3
It is similar to the first one described except that the controls are set to start the burner at its minimum rate of operation.
This is accomplished by means of a small electric motor or a regulator actuated by oil pressure.
Steam Atomizing Burners
The fuel oil enters a steam atomizer at relatively low pressure and is atomized by a jet of steam.
Combustion air is supplied by forced draft blowers.
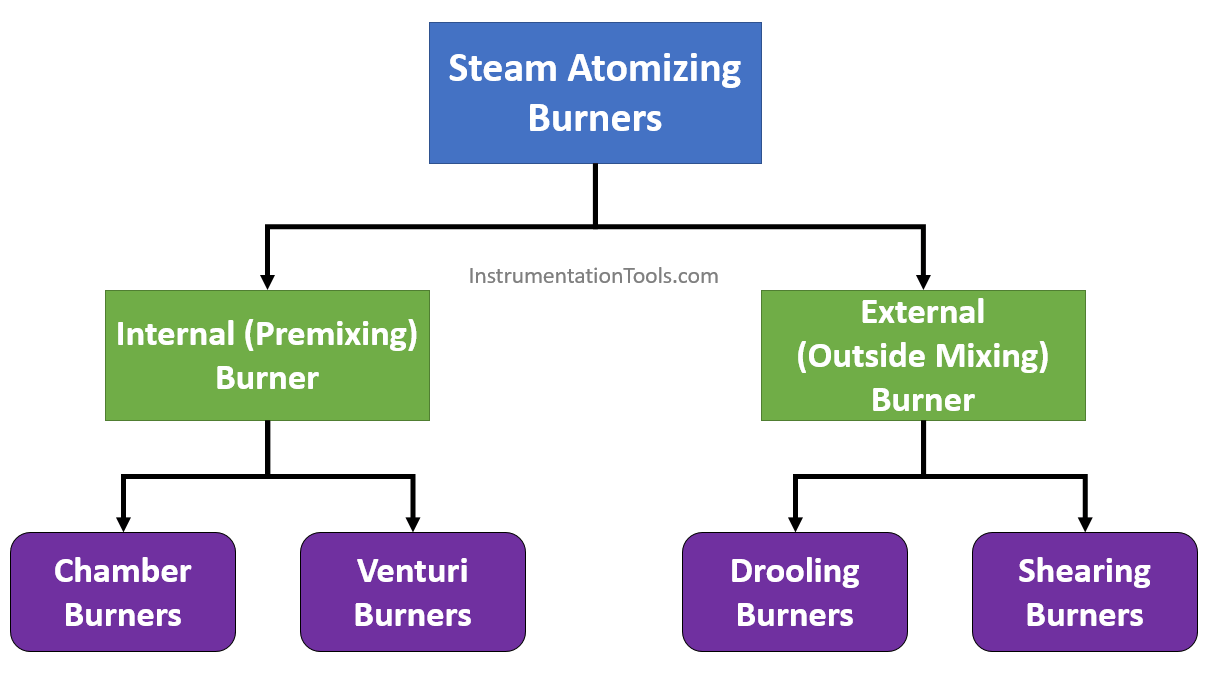
Steam atomization burners are further divided into two categories.
- Internal (Premixing)
- External (Outside mixing)
Internal (Premixing)
In the internal or premix in the unit, the oil and steam mix within the burner body.
Internal mixing burners may be divided into two categories.
- Chamber burners
- Venturi burners
Chamber burners
Comprises a chamber in which a preliminary mixing of oil and steam takes place, resulting in better heating.
Better heating results in bringing down the oil viscosity and makes it easy for pulverization.
Venturi burners
In this type of oil burners, chambers are formed by built up from cones and tapering nozzles.Â
External (Outside Mixing)
Oil generally reaches the tip through a central passage. As the oil emerges from the corner tip, it is halted by a jet of steam which breaks up the oil into tiny droplets.
The external mixing burners which are of the old class generally have a somewhat higher steam consumption. These are less sensitive to the variation of steam pressures.
The outside burners may be divided into two categories
Drooling Burners
In this type of oil burners, oil falls slowly on to the steam jet.Â
Shearing Burners
In this type, the oil is forced onto the steam at right angles.
Mechanical Oil Burners
By using mechanical force, the oil is atomized in the burner, so the name mechanical oil burner.
These burners provide atomization of the fuel oil by discharging the oil, under the pressure up to 300 psi or higher through a small orifice.
Mechanical burners use a slotted disk, which imparts a whirling motion to the oil before it reaches the atomizing orifice. The whirling motion improves atomization.
Advantages of Oil Burners
- Rotary burners require a reliable and positive method of ignition for safe operation.
- Automatic safety devices are usually provided to shut off the oil supply in case of the loss of ignition, low water, or excessive temperature.
Applications
- Power plants,
- Chemical recovery boilers
Read Next:
Excellent information provided
Thank you
The burner has a main switch with ON and OFF positions. There is also a START push button. To start the burner, turn the main switch to the ON position and press the START button. Then the flue gas fan starts first. When the fan has developed a sufficient negative pressure (the contact of the pressure sensor closes), the oil burner starts. After the oil burner starts, the ignition current transformer turns on for 3 seconds.
Now (within 3 s) the flame guard must see the flame (closing contact) in order for the burner to stay on. If the flame guard does not see the flame, the oil burner stops, but the flue gas blower remains on. At the same time, the “BURNER FAILURE” warning light lights up. The warning light can be turned off when the main switch is turned to the OFF position; at the same time, the flue gas fan stops. Turning the main switch to the OFF position always stops all functions of the burner.
MAKE LADDER LOGIC FOR IT