We use a direct online starter and a star delta starter for starting the induction motor. An induction motor takes about 6 times the current of its full load current (FLC) when we start the motor on DOL.
Even the motor takes 3-4 times current when we start the motor on the star delta starter.
Soft Starter
The electrical system experiences heavy stress when we start a large rating motor on DOL or star delta. The driven equipment also experiences heavy mechanical stress.
To mitigate the above situation, a soft starter is used for the jerk-less starting and stopping of an induction motor.
Advantages of Soft Starter
The advantages of the use of a soft starter are as follows.
- Reduced mechanical stress on the motor and driven equipment
- Reduced electro-mechanical stress on the power system
- Increased life of the motor
Limitations of the soft starter
The soft starter can be used for starting and stopping the motor at a reduced voltage in order to reduce the starting current for jerk-less starting.
We can not use the soft starter for speed regulation purposes.
Working Principle of Soft Starter
The soft starter has anti-parallel SCR in each phase. The output voltage of each phase is controlled using the controlling firing angle. As the firing angle is reduced the output AC voltage increase.
At starting, the SCRs are fired at a maximum firing angle in order to get low output.
More importantly, the output of the soft starter at the reduced voltage has the same frequency. The soft starter does not change the frequency. The flux in the motor is proportional to the ratio of voltage and frequency.
The V/f ratio is low when the motor is started at low voltage. The starting torque of the motor is low when it is started with a soft starter.
Therefore, the soft starter is suitable for those applications where starting torque requirement is low. If the starting torque requirement is high, the soft starter will draw a large current and may trip with an overcurrent fault.
When the motor achieves its rated speed the bypass contactor is made to bypass the SCRs in order to supply a perfect sinusoidal voltage to the induction motor.
Variable Frequency Drive (VFD)
VFD does two functions.
- Soft starting and stopping of an induction motor
- Speed control of the motor as per process requirement
The speed of an induction motor is proportional to the frequency and inversely proportional to the number of poles.
Ns = 120f/p
The VFD has the following sections.
- Converter section
- DC Bus
- Inverter section
Three-phase AC voltage is first converted into DC voltage. The output of the rectifier is further filtered to remove the AC components in the DC. The DC voltage is again converted into AC by PWM technology.
The PWM inverter controls the width of the pulse and as a result, the output voltage gets varies with an increased frequency. Thus the V/f ratio of the inverter output is maintained constant.
The motor is capable to deliver the constant torque from minimum speed to base speed of the motor.
The VFD is popularly used in industries for fan and pump applications. The power drawn by the fan and pump is proportional to the cubic speed. Thus, at reduced speed, substantial power saving can be achieved.
Comparison between Soft Starter and VFD
The below comparison table shows the brief differences between the soft starter and VFD drives.
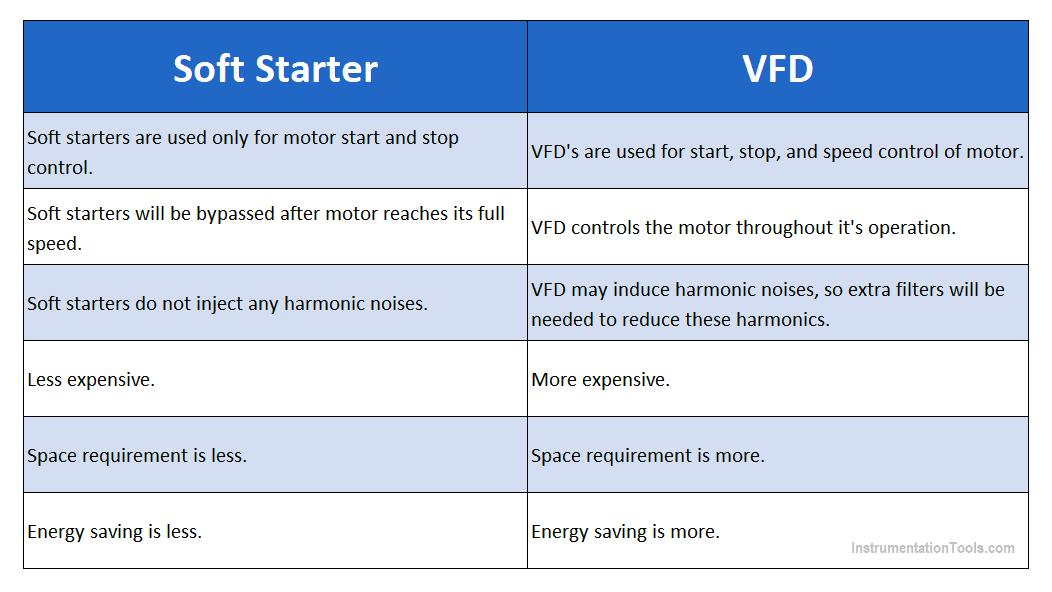
We have to use the VFD drives if the process application requires speed control of the motor as a soft starter does not have this capability.
Author: Satyadeo Vyas
If you liked this article, then please subscribe to our YouTube Channel for Instrumentation, Electrical, PLC, and SCADA video tutorials.
You can also follow us on Facebook and Twitter to receive daily updates.
Read Next:
Pictures of each would be good as they look similar but there are differences.
Three phase AC voltage is first converted into AC voltage. The output of the rectifier is further filtered to remove the AC components in the DC. The DC voltage is again converted into AC by PWM technology
…
Three phase AC voltage is first converted into DC *
Can you edit it please .
Thank you .