What is a Centrifugal Machine?
The machine in which the crystals in the massecuite are separated from the mother liquor is called molasses by the action of centrifugal force.
What is Automation?
The plant automation provides remote monitoring and controls of equipment for increasing productivity, in a safe working environment.
The purpose of automation is to reduce human efforts and increase plant efficiency.
In the sugar industry, the centrifugation process includes Continues type and Batch type centrifugation.
The batch type centrifugal operates using a set of sensors (proximity sensors and MTC), Solenoid Operated Valves, Feed Control valves, and Air Cylinders, Â
Proximity sensors:
These sensors sense or detect nearby objects without any physical contact.
Charging Sensor:Â
It is an electronic Sensor with ultrasonic technology.
Discharge Valve:
This valve is located at the bottom of the machine this arrangement consists of an air cylinder attached to the spindle and an SS Head to the Piston Rod.
 Instrument air:
The compressed air required to drive the pneumatic Valve is known as Instrument air. To drive the pneumatic valve the instrument’s air pressure must be 6 kg/cm2
Brake System:
The air-operated disk brake system is used as an emergency brake for shut down only.
The speed of the batch-type centrifugal machine is equipped with a 4-speed motor.
Typically 50, 200, 750, and 1480 RPM.
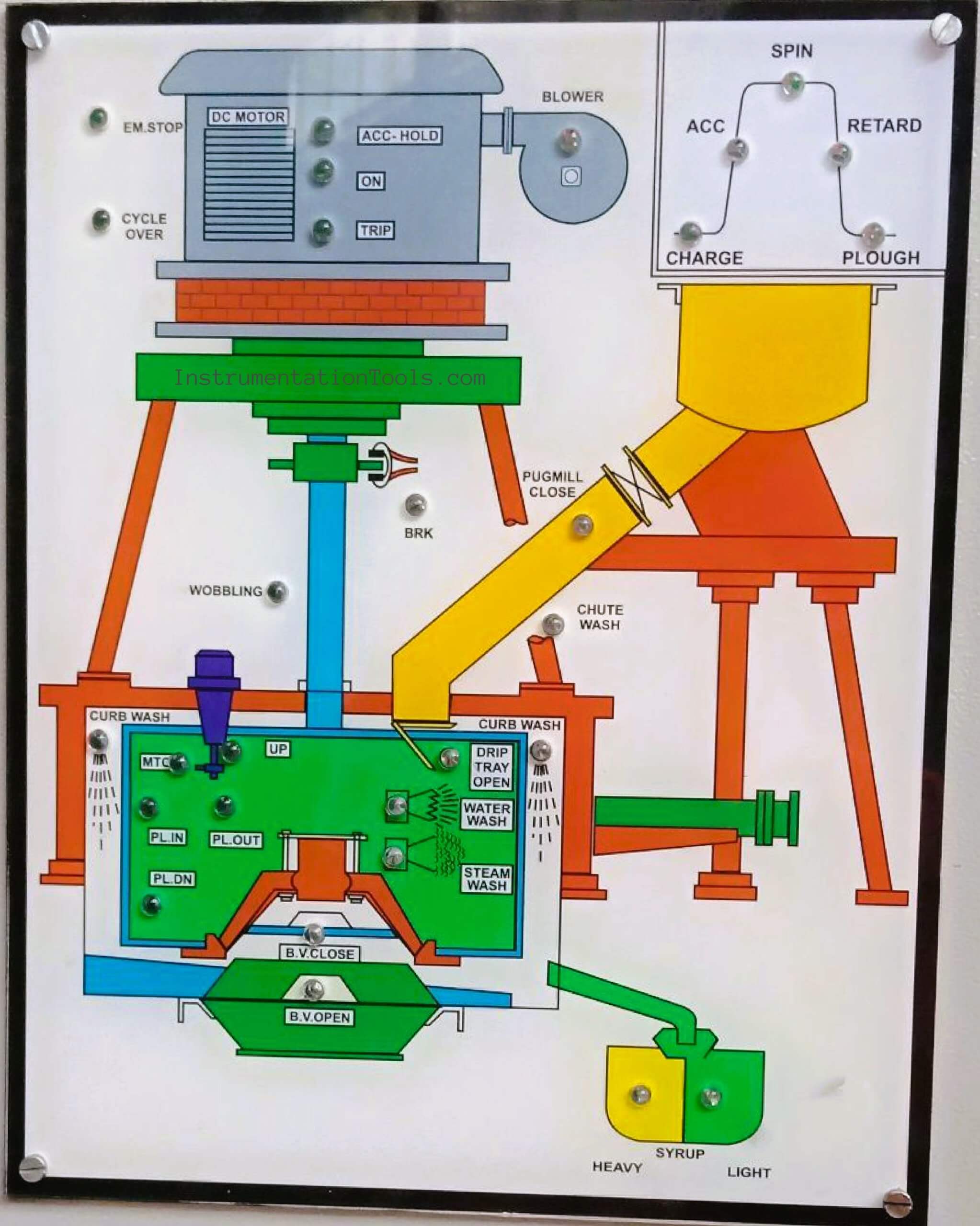
The table shows the details of solenoid valves used for the operation
SL | SOLENOID VALVE | SOV TYPE | SOV MAKE |
 1 | Brake | SC / SA | Rotex |
 2 | Steam Wash | SC / SA | Rotex |
 3 | Water Wash | SC / SA | Rotex |
 4 | Crub Wash | SC / SA | Rotex |
 5 | Chute Wash | SC / DA | Rotex |
 6 | Feed Valve – Ii | SC / DA | Rotex |
 7 | Syrup Separator | SC / DA | Rotex |
 8 | Pug Mill Gate [FV I] | DC / DA | Rotex |
 9 | Bottom Valve | DC / DA | Rotex |
 10 | MTC | SC / SA | Rotex |
 11 | Scrapper Up/Down | DC / DA | Rotex |
 12 | Scrapper In /Out | SC / DA | Energy Tech |
 13 | Lock | SC / SA | Energy Tech |
Batch Type Centrifugal Automation
The sequential operation of batch type Centrifugal Machine is as below:
- On pressing the ‘ON’ button the machine gets started to 50 to 200 RPM and the timer is operated. Similarly, the screenwash timer gets energized, and thus the screenwash is started.
- After the preset time of screenwash is over the monitor casing cover gets opened and charging of massecuite takes place simultaneously through a set of feed valves, and the charging timer starts.
- Upon reaching the predetermined level of massecuite charge in the basket. The pug mill gate is closed by an Electro-Pneumatic actuator.Â
- After closing the pug mill gate the machine gets accelerated to 750 RPM, and the first water wash delay timer gets energized. After this delay timer is over, the monitor casing flap closes and the first water wash duration starts.Â
- After the first water wash duration is over the second water wash delay timer gets energized. When this delay timer is over the second water wash duration starts.Â
- After the second water wash duration is over, the syrup separator switches to the light side.Â
- After the 200 to 750 timer is over, the machine again gets accelerated to the higher speed of 1480 RPM.
- After the present time of 750 to 1480 RPM, the machine runs at spinning speed i.e. 1440 RPM. The spinning time is about 60 to 100 sec. depending upon massecuite quality.
- Now the steam wash delay timer gets energized. And the steam wash timer starts at a steam pressure of 100 psi.
- When the preset time of spinning duration is over, the machine retards to 1480 to 750 RPM by regenerative braking.
- After the 750 to 200 RPM timer is over, mechanical brakes are applied to the machine to Retard to 50 RPM.
- Â Finally, the machine comes to zero RPM or stands still. Two seconds before the machine reaches a standstill, the bottom valve lifts and sugar crystals get discharged.
- After the bottom valve lifting timer duration is over, the bottom valve falls down and thus closes the opening of the bottom valve.
- After the closing of the bottom valve the existing cycle is completed and the next cycle starts automatically.
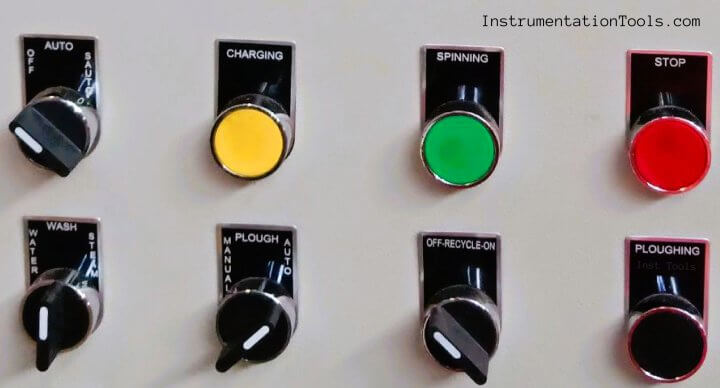
About the Centrifugal Machine
A Centrifugal machine consists of a basket revolving on the vertical shaft or axis called a spindle and is driven by an electrical motor of variable speed.
Proper Equilibrium of the basket is the most important factor to be considered for the smooth and safe operation of the centrifugal machine.
The upper end of the shaft rotates in the ball bearing mounted in a thick rubber baffle.
The basket is surrounded by a monitor casing that stores the separated Molasses and delivers it to a suitable outlet.
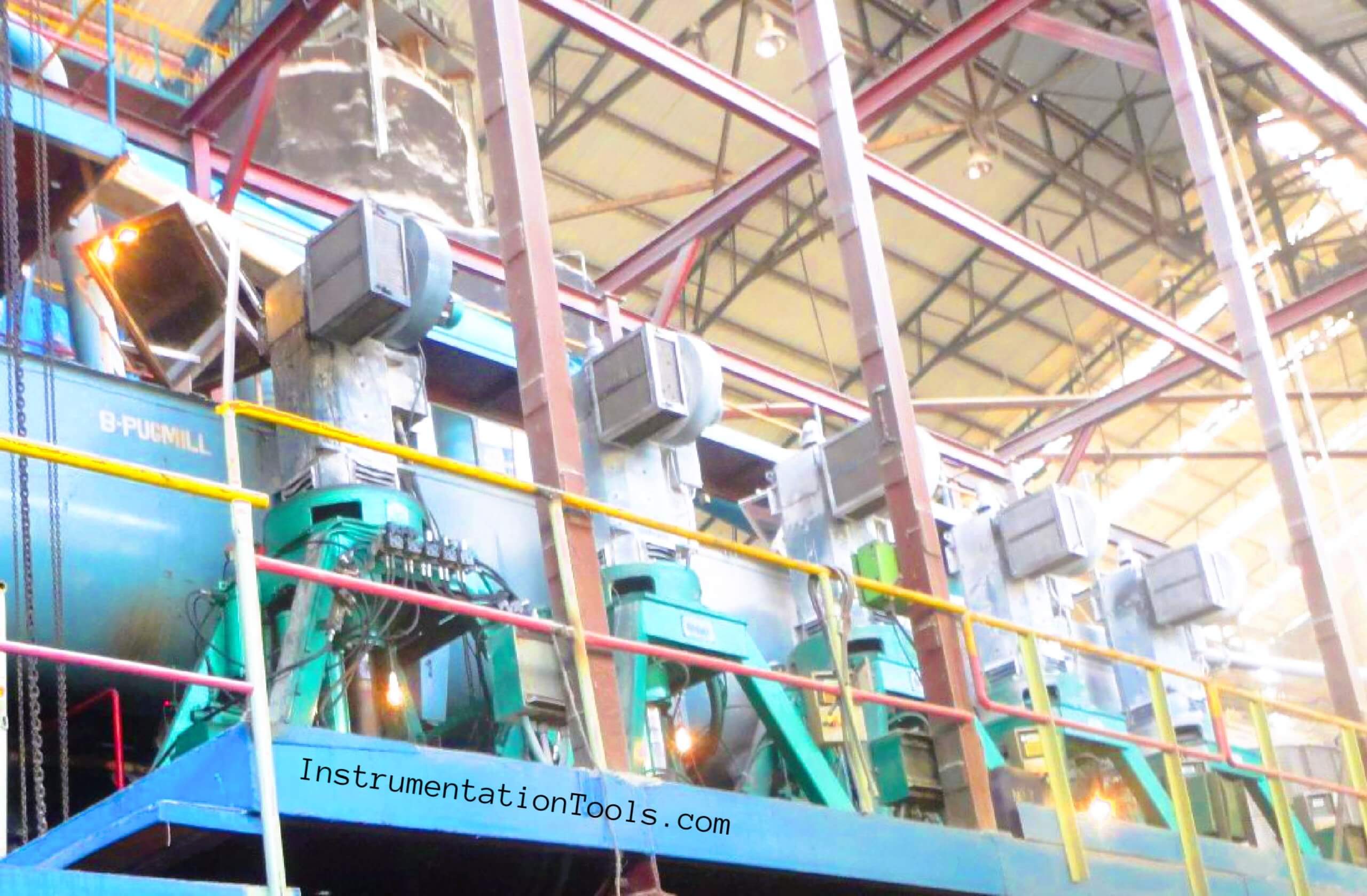
The bottom opening of the basket is generally closed when the machine is in operation by means of a conical cover/bottom cone of metal Sheet.
The massecuite is charged to a centrifugal machine from the pug mill through a set of feed valves.
During charging of the massecuite, the centrifugal machine revolves at a lower speed, so that the massecuite forms the vertical layer on the wall of the basket due to centrifugal force.
When the massecuite layer in the basket reaches the desired thickness feeding must be stopped, and the machine is accelerated to the operating speed of about 1440 RPM
Due to increased acceleration in the machine, the massecuite climbs up the outer wall of the basket during this period the mother liquor called molasses is expelled out, runs down towards the monitor casing, is collected at the bottom, and is then pumped to molasses receiving tank.
For better purging and drying of sugar, a super-heated water wash and steam wash at a suitable stage are introduced in the case of high-grade massecuite. The automatic separator is another process carried out to separate light molasses from heavy molasses, as all molasses expels out of the machine and the sugar is separated.
As the process cycle gets completed the centrifugal machine is now decelerated and stopped by the brake.
The wall of sugar in the basket collapses and the sugar crystal is discharged by means of a mechanical plough as soon as the bottom case lifts up.
After the sugar is discharged the existing cycle is terminated and the machine runs for the next cycle.
The capacity of a centrifugal machine is about 2.2 tons of massecuite per charge /cycle.
For purging the Gravity Factor of a centrifugal machine is 1050. The massecuite thickness in the basket must not exceed 230 mm or 23 cm or 10 inches of sugar crystal, having a crystal size of 0.4mm
The massecuite is charged at 200 RPM
Sugar crystals are discharged at 50 RPM
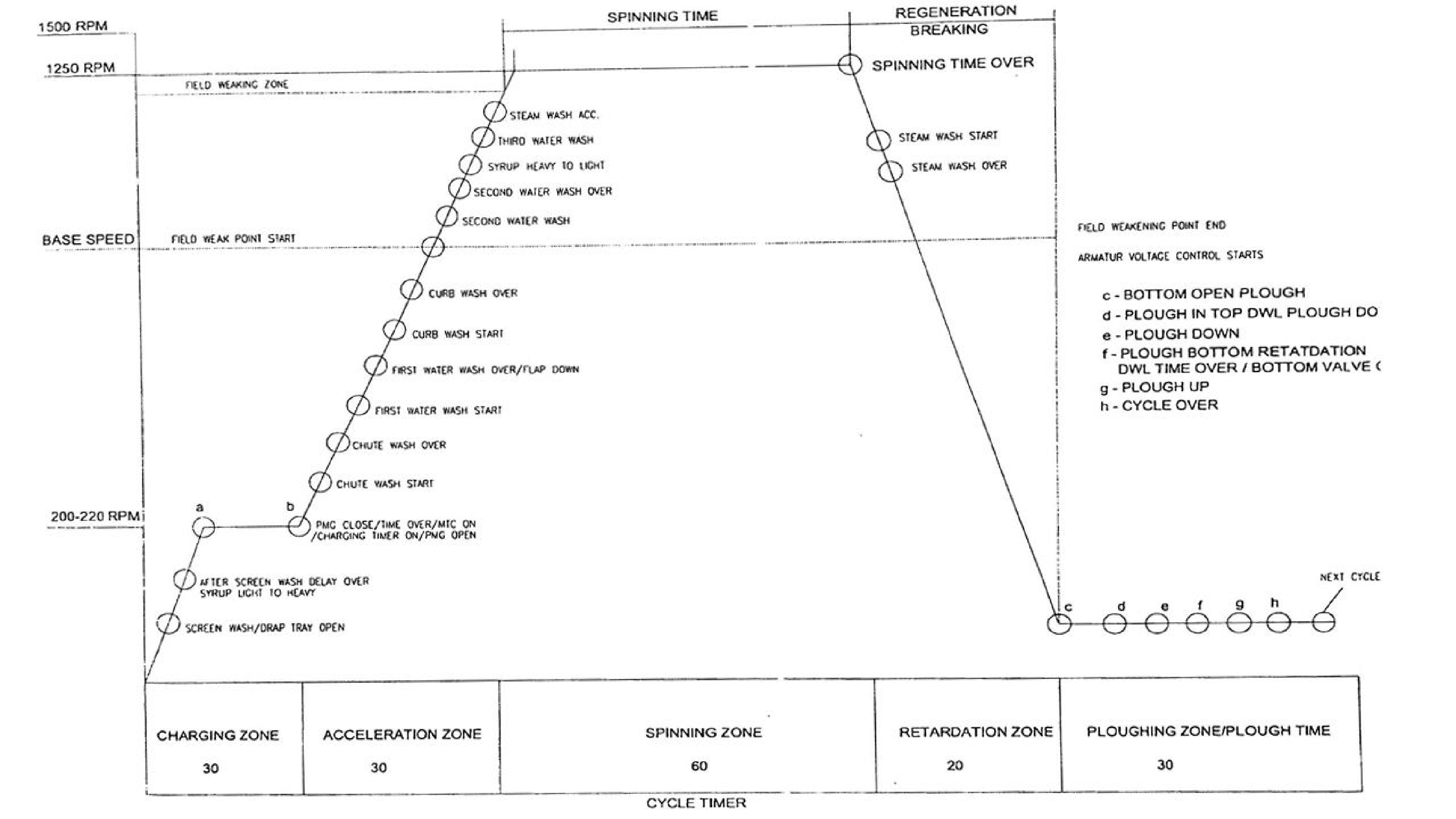
Note: The process parameters and ranges may vary depending on your plant design.