For a long time, machines and robots, in particular, have been the stars of engineering, primarily when they perform incredible acts of programming and speed. But how often do you pause to reflect on the timeless value of the simplest components of the engineering world? The surface plate is among the tools that have endured over the years and demonstrate the significance of technical precision.Â
In its simplest form, a surface plate is a rectangular plate with a completely flat surface. This tool, which can also be referred to as a true plane surface, is used to conduct accurate measurements in the field of engineering. Granite surface plates and iron surface plates are the most common surfaces face because they can provide a precise reference surface for design, checking, machining, and gaging.Â
Engineering Surface Plates
You can’t achieve reliable results without a stable baseline from which you measure anything. A surface plate could come in handy if you need to measure something.
Many workshops and labs will attach their various gaging devices to ensure the most accurate measurements to a surface plate. The measurement of something can then be determined from that point forward.
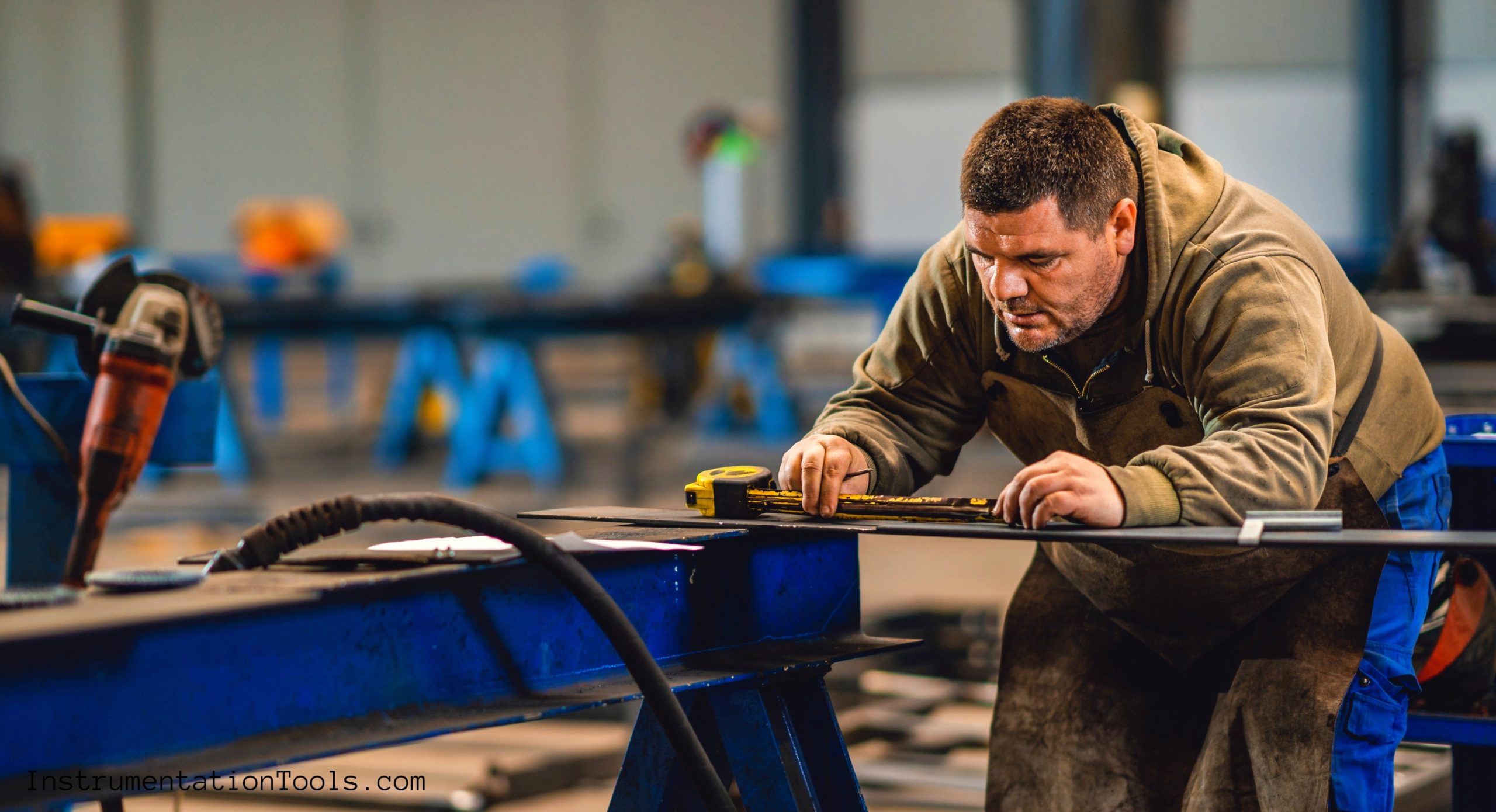
There are many grades of surface plates each with its precision. Some tasks call for a higher grade, while others can get by with a lower one. Surface plates with a grade of 0 are the most accurate ones.
Grade 1 plates are a step down in precision but still enough for most measurement purposes. You’ll likely find Grade 2 surface plates in a workshop where accuracy isn’t as important. Being the lowest grade, grade 3 is rarely used in mechanical engineering.Â
History
Henry Maudslay, who lived around the year 1800, is credited with being the first person to recognize the significance of the surface plate. Maudslay’s early career began as a blacksmith, where he demonstrated exceptional skill in forging delicate yet intricate pieces of metal.Â
After gaining acclaim, he found work with renowned locksmith Joseph Bramah. And it was during this period that Maudslay developed the specialized equipment and instruments that allowed him to produce such pieces. However, he saw an issue with mass manufacturing standardization. For all parts to be manufactured to the exact specifications, Maudslay established the true plane surface for measurement.Â
Maudslay came up with a procedure that involved scraping the plates, wiping blue paint across pairs of plates to identify faults, and making sets of three plates instead of matching concave and convex plates to guarantee that his surface plates were flat. This allowed for standardization, mass production of components and tools, and a solid foundation for the industrial revolution.
Iron was the standard material for surface plates at the time. However, different kinds of materials were tried out for making surface plates. Today, granite surface plates are the most common ones you’ll see. Unlike cast iron, granite is non-magnetic, non-conductive, and vibration-absorbing.
Calibration and Upkeep
Surface plates, whether they are new or have been resurfaced, need to be checked and calibrated often to make sure they comply with specific regulations. Even though surface plates are quite durable, it’d be foolish to think they can’t be damaged. With time and repeated usage, some parts may wear out more quickly than others.Â
Lapping or resurfacing is performed during calibration to ensure that measurements are consistent with grade requirements. During this process, an abrasive paste is used to polish the surface, removing any imperfections or flaws.
If possible, you can switch from one surface portion to another to maximize the time between calibrations. To prevent preference for one area of the plate over another, it’s best to rotate it between uses.Â
Furthermore, keeping your plate’s surface clear of anything that might get in the way will protect the flatness and quality of your container as well as the accuracy of your measurements. So, when you’re using the plate, nothing else must be placed on it.
It’s also possible to extend the period between calibrations with some preventative care. The surface plate should be cleaned frequently and after each use. Since granite easily picks up dust and dirt, you should always keep the surface plate covered when you’re not using it.Â
Then, regularly inspect the plate for signs of damage, keeping in mind that even minor flaws might significantly impact your measurements.
Conclusion: The Importance
While machines and robots have long been engineering’s shining stars—mainly when they perform astounding programming and speed—the importance of even the most basic engineering tools can’t be overstated. Part of engineering is ensuring that measurements are precise. To ensure that engineered parts meet specifications, surface plates are employed. This is the importance of a properly calibrated surface plate.