Metrology is the science of measurement and involves using tools (known as metrology tools) to measure objects. This principle is highly applicable in CNC machining throughout the production process due to its common use for parts with complex designs.
For example, metrology tools can calibrate the machine or workpiece can ensure that the CNC machined parts have size, shape, and tolerance according to the specifications and within the specified tolerances.
Every CNC machine shop has different types of metrology tools depending on their work and workloads. In turn, this will determine the capability of such shops. This article discusses the types of metrology tools in precision CNC machining, their benefits, and their applications.
Metrology Tools for CNC Machined Parts
There are many types of metrology tools each with unique functions for CNC machines and custom CNC machined parts.
Below are the common ones you can find in a CNC machine shop:
Coordinate Measuring Machines (CMM)
The coordinate measuring machine can measure the dimension of a workpiece or a CNC machine in the x, y, and z axes.
Aside from measuring, some CMM machines with the necessary feature can record the measured data and some are big enough to measure parts with a size of 10m or more.
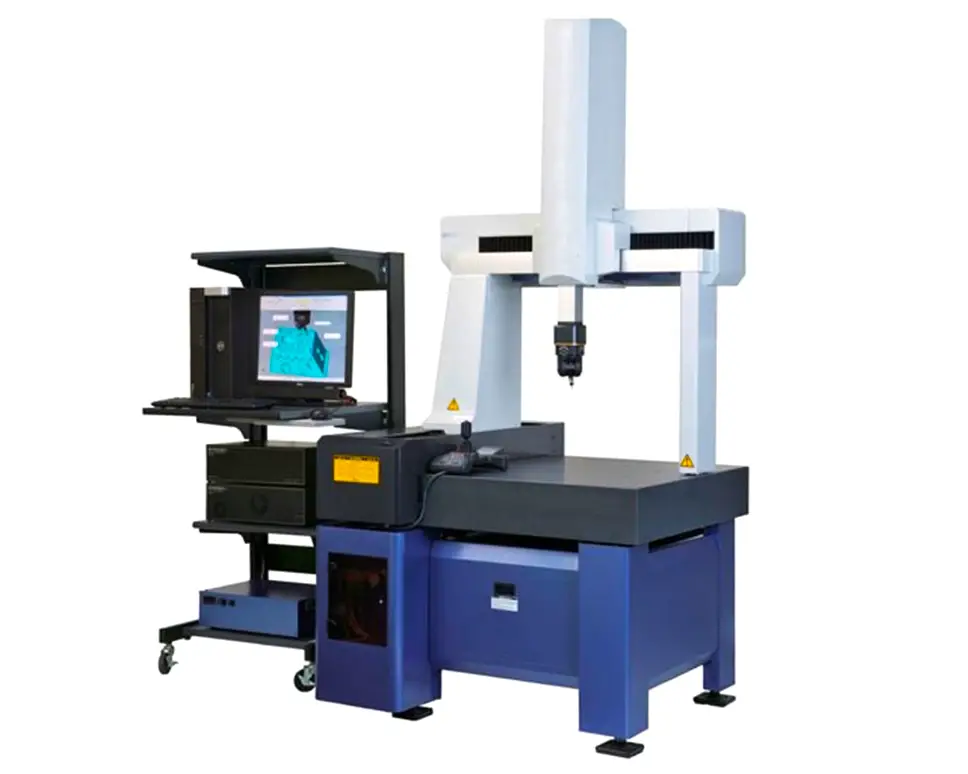
There are two ways by which a CMM machine takes measurements. One way is by using a touching probe to measure the workpiece or machine’s dimensions. The other method involves using a camera or laser beam.
To measure a part, the operator places the workpiece or CNC machine part on the CMM base. Above the CMM plate is a movable gantry containing the touching probe or the laser beam. The CMM machine then controls the probe or laser beam to touch the object along the x, y, and z axes
Using the touching probe as an example, on touching the object, it sends a signal which the computer uses to establish the coordinate system of the part. Afterward, the computer analyzes the coordinates.
Profile Projectors
Profile projectors or shadowgraph is an optical measuring instrument that works similarly to optical microscope.
Profile projector was initially an inspection tool for workpiece outlines.
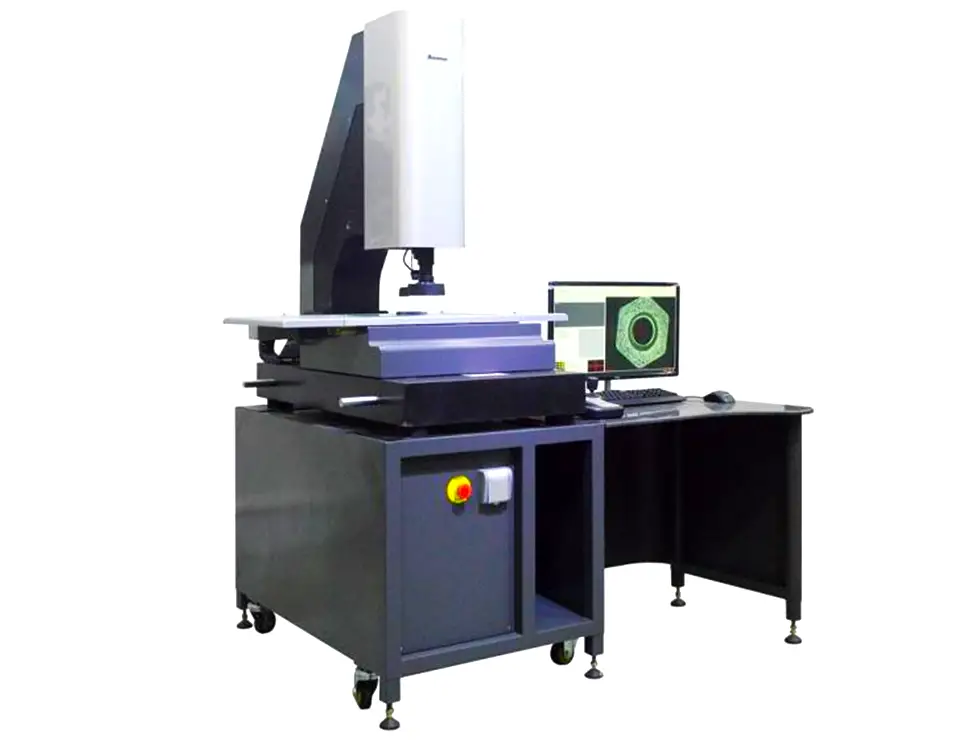
Profile Projector involves placing the target on the stage and shining light on it from the bottom to protect the target’s shadow on the screen. Afterward, the tool’s telecentric optical system then makes accurate measurements.
Profile projectors are metrology tools applicable in inspecting the outlines of workpieces. However, they have limitations based on the size of the workpiece.
Caliper
A caliper is a simple metrology tool applicable to measuring the distance between a workpiece or a CNC machine.
Calipers come in several shapes and sizes and are applicable depending on the size and shape of the part or machine. Furthermore, they can also be automated or manual which also affects their applications
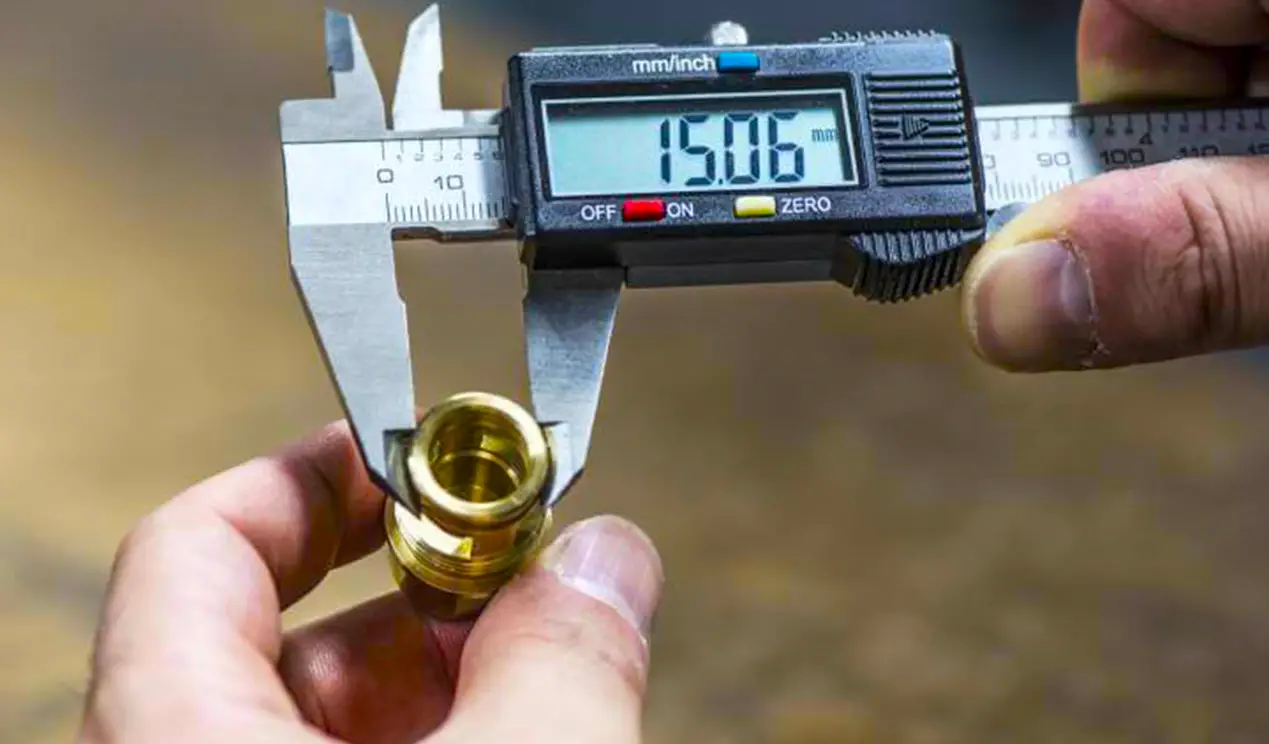
Height Gage
A height gauge is a metrology tool for CNC machining applicable to measuring the height of an object.
The height gauge is the better tool for measuring the height of large objects.Â
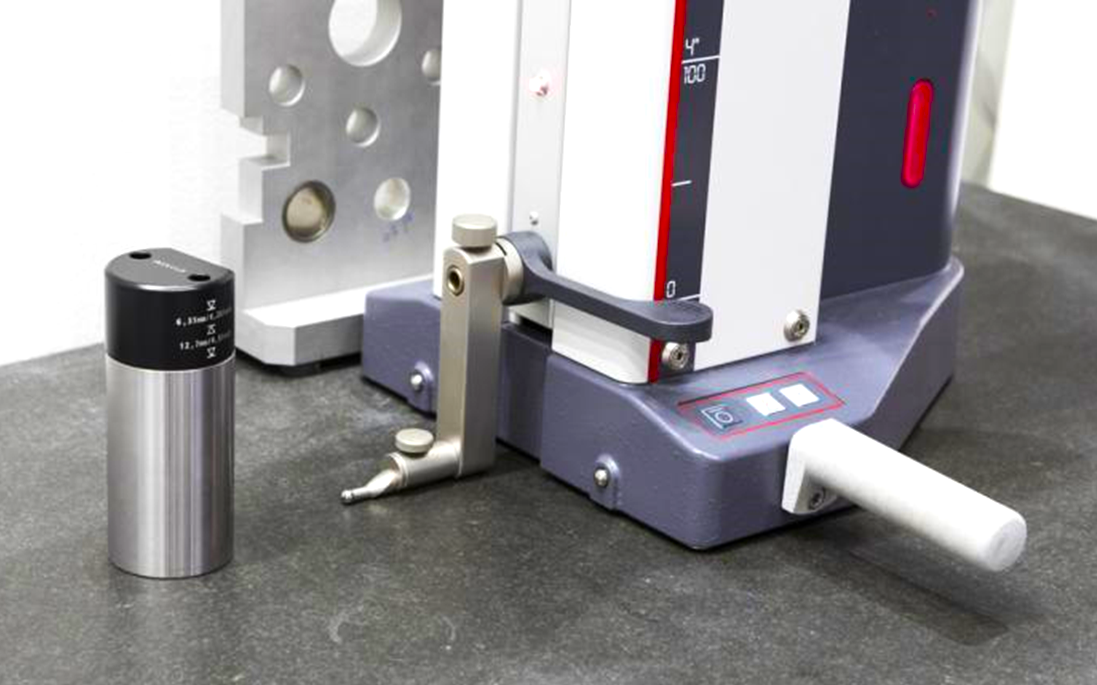
Surface Finish Testers
The surface finish tester is a metrology tool applicable in CNC machining for testing the roughness of a workpiece.
The surface finish tester measures the roughness depth (Rz) and the mean roughness value (Ra).
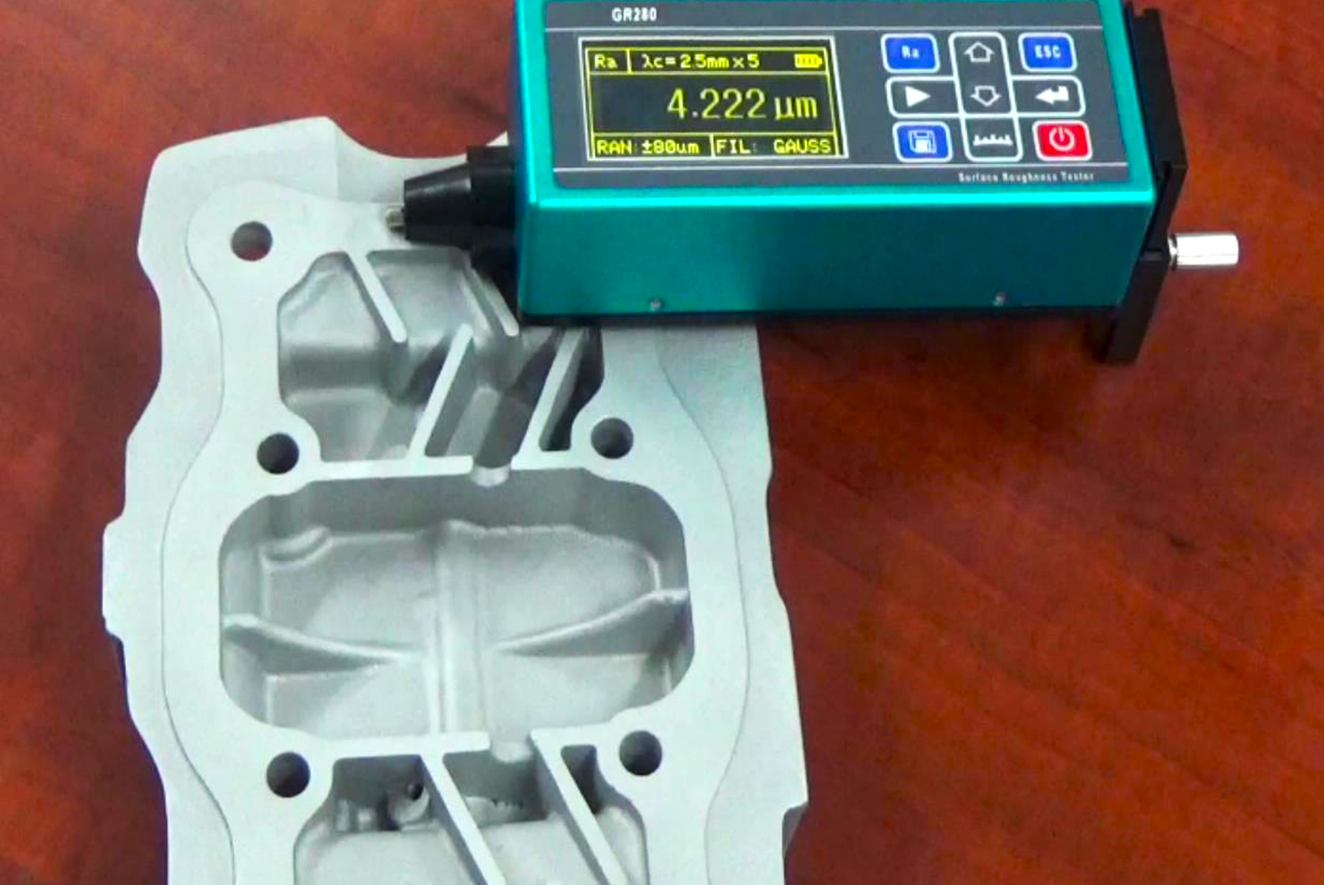
Using the surface finish tester, manufacturers can know the roughness which can help them judge the wear resistance, vulnerability to corrosion and cracks, and ease of adhesion.
Applications of Metrology Tools for CNC machining
Metrology tools are applicable in CNC machining in several ways.
Below are a few ways they apply
Quality Control in Manufacturing
Metrology in CNC machining allows manufacturers to enact quality control in the manufacturing process.
As a result, they can ensure machined parts are according to the specifications. Furthermore, quality control ensures the certainty of the functionality of the product.
Inspection of Prototype Parts
Metrology tools are an important part of prototyping as they allow designers to inspect prototypes and check for defects.
For example, the CMM machine can measure the dimension of the prototype in case of deviation from the specification. Generally, with metrology tools, it is easier to detect technical faults and fix them during the prototyping.Â
Tooling Verification
Metrology in CNC machining is also suitable for the verification of tools.
For example, measuring the dimension of the workpiece makes it possible to choose the tool that can machine such a workpiece effectively and efficiently. Therefore ensuring we can verify the suitability of the machine for a process and a product.
Calibration of CNC Machines
Aside from tooling verification, metrology tools are also applicable in the calibration of CNC machines. As a result, this ensures that the best tools are chosen for the product. This is very important due to the complexity of products machined using the process.Â
Advantages of Metrology Tools for CNC machined parts
Metrology tools for CNC machining have the following advantages
Improved Accuracy
Metrology tools allow the calibration of the CNC machine, hence, there is an improvement in the accuracy of the machine.
Furthermore, using computer-controlled metrology tools such as a CMM machine will reduce human personnel involvement which sometimes leads to operational errors that can lead to problems.
Increased Efficiency
With the tools, manufacturers can quickly measure parts and make quick adjustments. This will result in faster and more efficient production processes.
For example, coordinate measuring machines (CMMs) can perform automated measurements of parts, reducing the need for manual measurement and inspection.
Cost Reduction
Metrology in CNC machining also ensures that the precise amount of material is worked on. Therefore, there is a reduction in material wastage.
Aside from that, knowing about the measurement and tailoring the process for tight tolerance reduces operation time which reduces the cost.
Better Quality Control
Metrology tools such as the CMM machine can digitally measure and analyze your part while providing other services such as dimensional analysis, CAD comparison, tool certifications, and reverse engineers. This is all needed for quality assurance purposes.
Limitations of Metrology Tools
Although they have several benefits, using metrology tools in CNC machining also has a few limitations.
High Initial Cost
Metrology tools have a high initial cost of investment which can deter many businesses. Nevertheless, businesses can outsource CNC machining services with the infrastructure already in place
Technical Expertise Required
Some metrology tools require operators to have high technical expertise. As a result, this can increase the cost of operation. Aside from that, fielding an inexperienced operator will increase the chances of defects in production.
Soft Parts Could Lead to Defects
For parts that come from soft materials like rubbers and elastomers, using a probe can lead to the parts caving in. This will lead to error which is seen during digital analysis.
Time-Consuming
Manual measurement will take a little time. Nonetheless, a coordinate measuring machine (CMM), will also take longer due to the pre-measurement stage which requires programming the machine. As a result, this will slow down production processes and increase lead times.
Environmental Factors
Some metrology tools are susceptible to variables that include temperature, humidity, and pressure which can affect the measurement
As a result, this can lead to further tests and calibrations which makes the process more time-consuming. Aside from that, when such errors are not noticed, they can affect the quality of the end product.Â
Conclusion
Metrology tools such as CMM machines and calipers are vital in CNC machining due to the improved accuracy, efficient production process, cost reduction, etc. They are important in achieving quality assurance.
As a result, choosing a rapid prototyping service depends on them. At RapidDirect, we provide CNC machining services with quality assurance. We have a well-trained and experienced inspection team and suppliers and materials and machines go through thorough tests and inspections. Looking for quality custom CNC machined parts? Upload the CAD file on our online quotation platform to get an instant quotation and DfM report.