In various industrial processes, ranging from the chemical industry to food processing and monitoring greenhouse gas emissions, liquids and gases play pivotal roles.
Consequently, producers and consumers across diverse sectors rely on accurate measurement techniques. Furthermore, the adoption of hydrogen as an alternative energy source raises the demand for highly precise technical solutions.
Challenges in Gas and Liquid Measurement
Accurate measurement of liquids and gases demands a profound understanding of the underlying physical principles governing these processes.
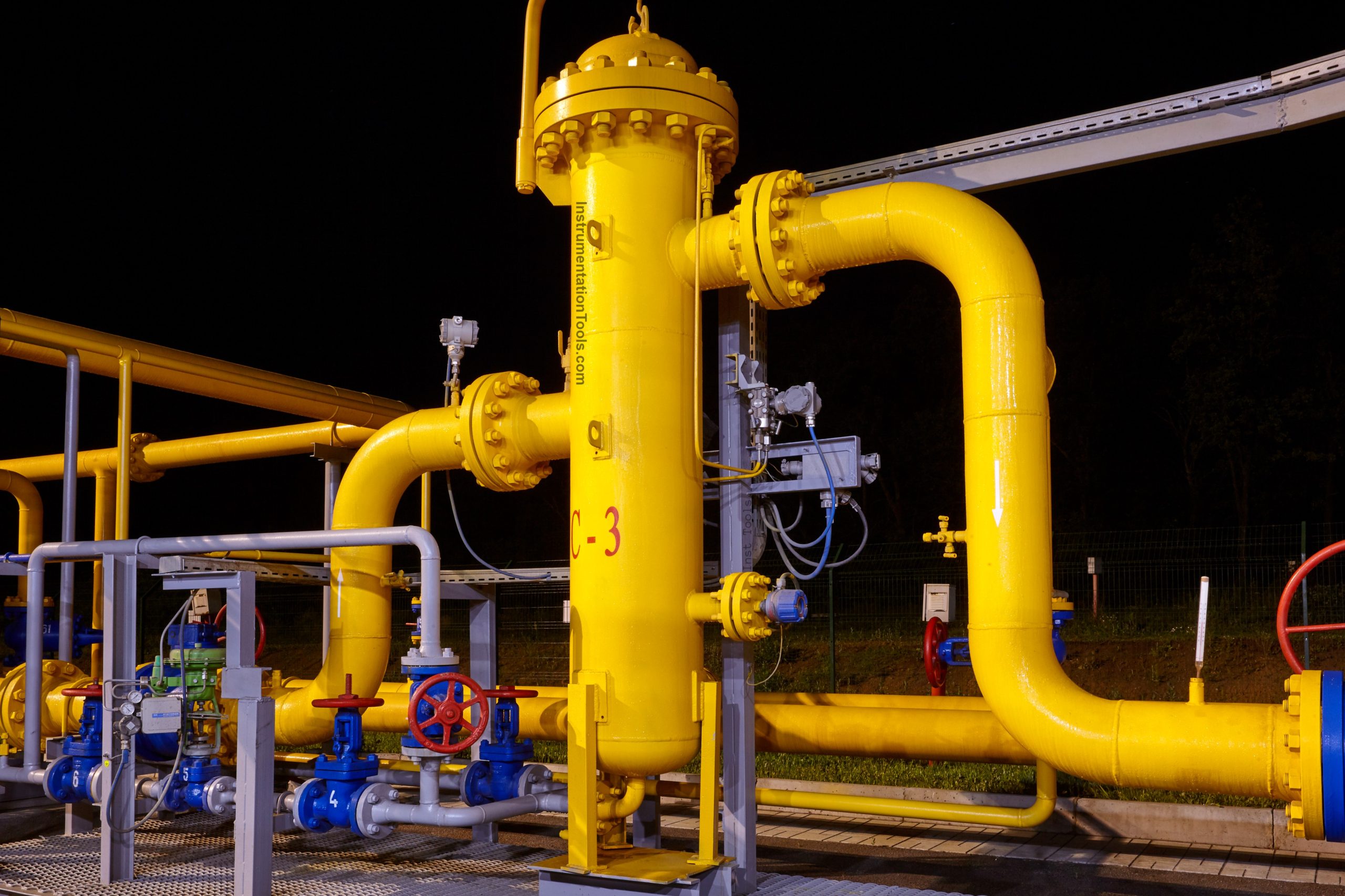
Crucial factors include the properties of the respective mediums.
Mechanical and electronic measurement methods must account for these properties, yielding results of varying accuracy based on the method. Particularly in pressure and flow measurement, certain principles of fluid mechanics must also be considered. Measurement technology faces challenges such as:
- Wear and Tear Due to the Measured Medium: Aggressive chemical properties of liquids or gases can impact the lifespan of measuring devices.
- Potential Sources of Errors: Environmental factors like temperature and humidity, in addition to the inherent accuracy of the measurement method, can influence results.
- Viscosity: The viscosity of a liquid, indicating its thickness, can be crucial for flow measurement.
- Explosion Protection: Safety precautions are vital when operating in environments containing combustible gases, vapors, or liquids. Explosion-proof devices are specially designed for use in hazardous areas, preventing sparks or heated surfaces from directly contacting the medium.
Flow Measurement
Monitoring processes necessitates measuring the flow rate over a specific period of time. Users have access to a broad range of measurement methods, each with distinct advantages and disadvantages.
Fundamentally, mechanical and electronic methods of measurement can be differentiated. Electronic flow meters measure the flow of liquids or gases electronically and display the results on a digital screen. They can utilize various principles such as ultrasound or electromagnetic measurement. Compared to mechanical devices, electronic flow meters offer high accuracy and cover a wider measurement range.
Mechanical flow meters, on the other hand, are based on the differential pressure principle by using orifice plates, Venturi nozzles/tubes, throttle valves, or flow nozzles. They are highly robust and independent of power supply, making them ideal for challenging environments with high temperatures or corrosive media.
For electrically conductive liquids, electromagnetic flow measurement is suitable. It employs a weak magnetic field generated perpendicular to the flow direction to measure the induced voltage. This forms the basis for an accurate calculation of the volumetric flow rate.
Other variants include Coriolis and ultrasonic flow measurements. Measurement technology experts like WIKA offer a comprehensive portfolio, enabling businesses to choose the technology best suited for their application. The range includes products such as primary flow elements, flow switches and air flow sensors.
Flow Measurement as the Foundation for the Energy Transition
Production and Storage of Hydrogen: Sensitive measurement technology monitors and controls production, distribution, and storage in extreme conditions, enduring temperatures of -235 °C.
Carbon Dioxide Capture and Storage: In carbon dioxide capture and storage, flow measurement ensures the safe and effective storage of carbon dioxide in geological formations.
Level Measurement
Determining the level of a medium in a tank is a classic application for level measurement. When handling liquids, measuring the level is indispensable.
Methods such as the reed chain technique, magnetostrictive level measurement, or hydrostatic level measurement are suitable for continuous level measurement. Floats, level probes, or level sensors are used in these methods.
For measuring limit levels, however, level limit switches are employed. Also, a proven method in level measurement is capacitive level measurement.
In recent years, however, ultrasonic measurement technology has gained in importance, as it enables non-contact measurement and is suitable for various media.
Pressure Measurement
The industrial process monitoring and control relies on precise monitoring of pressure conditions in liquid and gas containers. Even in closed systems, pressure losses must be promptly detected to ensure desired process quality and safety.
Pressure measurement differentiates between mechanical and electronic methods. Mechanical pressure measurement uses gauges with bourdon tube, capsule, or diaphragm as sensing element.
Pressure is measured through the elastic deformation of the sensing element proportional to the pressure, which is then read directly from a scale with a mechanically operated pointer.
For situations requiring more precision or automated regulation, pressure sensors come into play. These sensors convert pressure into an electrical signal, which is digitally processed and utilized for monitoring pressure and pressure changes.
In electronic pressure measurement, on the other hand, resistive, piezoresistive, capacitive, and piezoelectric methods are common. Resistive and piezoresistive methods employ pressure-dependent resistance changes for measurement, while capacitive pressure measurement relies on changes in distance between two parallel electrically conductive plates.
Piezoelectric pressure measurement utilizes a physical phenomenon wherein certain materials like quartz or piezoceramic emit electric charges when mechanically deformed, allowing their measurement.
Temperature Measurement
In addition to pressure, flow, and level, temperature constitutes one of the most crucial parameters in many processes.
Temperature measurement devices differ as follows:
- Mechanical Temperature Measurement Devices:
Measurement based on expansion of temperature-dependent materials, e.g., tension thermometers, gas actuated thermometers, bimetal thermometers.
- Electronic Temperature Measurement Devices:
Measurement using a sensor converting temperature into an electrical signal, e.g., thermocouples, resistance thermometers (RTD), infrared technology. In an RTD, the sensor is made of a material whose resistance changes with temperature.
Thermocouples, on the other hand, exploit the conductive properties of two different metals or alloys. The thermocouple wire measures the temperature difference between the junctions through an applied electrical voltage
- Mechatronic Temperature Measurement Devices:
Mechanical Thermometer with integrated electrical switch contacts triggering the switching process at a specific measurement value, e.g., bimetal thermometers with electrical output signal, gas actuated thermometers with electrical output signal, bimetal thermometers with switching contacts.
Invasive vs. Non-Invasive Measurement Methods
In the measurement of liquids and gases, both invasive and non-invasive methods are common depending on the location and medium used.
Invasive methods involve direct interaction with the medium, whereas non-invasive methods do not come into contact with the sensor unit, avoiding potential contamination or influence on the test results by the sensors.
Optical methods are an example of non-invasive measurement techniques.
Criteria for Choosing the Right Measurement Method
The optimal measurement method depends primarily on the specific case of application. Generally, existing alternatives can be categorized into invasive and non-invasive, as well as mechanical and electronic methods.
The following criteria should be considered when selecting the measurement technology:
Measurement Accuracy: The accuracy of the measurement range should match the application requirements.
Measured medium: Verify if the measuring device is suitable for the type of medium (liquid or gas) and its chemical properties.
Environmental Conditions: Consider the ambient conditions in which the device will be used, including temperature, pressure, and potential interactions with chemicals.
Budget: The budget for the measuring device and its maintenance should influence the decision.
Certifications and Standards: Many industries and applications have specific certification and standard requirements. The chosen measurement method must comply with applicable regulations and quality standards.
Connectivity: To integrate with a control system, a specific signal is typically required, which can be an analogue voltage or current signal or a digital signal, depending on the system. The sensor technology must provide the required type of signal output.
Sources: (1) (2) (3) (4) (5) (6) (7) (8) (9) (10) (11)
nice post