WDS system is known as Wet Dust Suppression system which is frequently used to suppress dust and other harmful toxic gases from fertilizer Plants.
In the case of the Urea Plant Unit, it is mostly used in Urea and bagging Plant Material Transfer Point i.e. Urea Material Transfer Bulk Conveyor (BC-01_For reference only) to Bagging Plant Product Transfer Bulk Conveyor BC-02.
WDS system is designed to remove the unwanted Urea Dust particles present during the transfer of Urea from the Urea Plant after prilling. Also during the transfer of Urea through different Bulk Conveyor systems Urea Dust is generated.
It serves as an essential component within the bagging plant, ensuring a cleaner and safer environment during the bagging operation.
Wet Dust Suppression System
The primary function of the WDS system is to remove Urea & Free Ammonia from Urea. WDS system’s basic working is explained below.
- WDS system consists 3-inch (Pipe size may vary) Flexible Plastic Pipe Assembly connected through a 3-inch SS Pipe (SS pipe size may vary, Here SS is used to prevent the Pipe from Corrosion) and this assembly is directly connected with the Blower system.
- WDS Pipe is connected at 3 main points i.e. at the Bagging Machine Spout assembly Front side at both edges i.e. Left and Right side.
- At the second point, WDS system pipes are connected at the rear side of the Bagging Machine Spout Assembly to suck free ammonia and Urea Dust.
- At the third point WDS system pipe is installed at the Bagging Machine Weigh Pan i.e. Pandoor Assembly Upper side.
- Also WDS system suction point is given at BC-01 and BC-02 material transfer point where Concentration of Free ammonia is high also dust percentage is also high. This point is initial suction point of the WDS system.
When we take Bagging machines in line before that we start WDS system so that Bag Filing operator can work at bag filling dust easily before any problem.
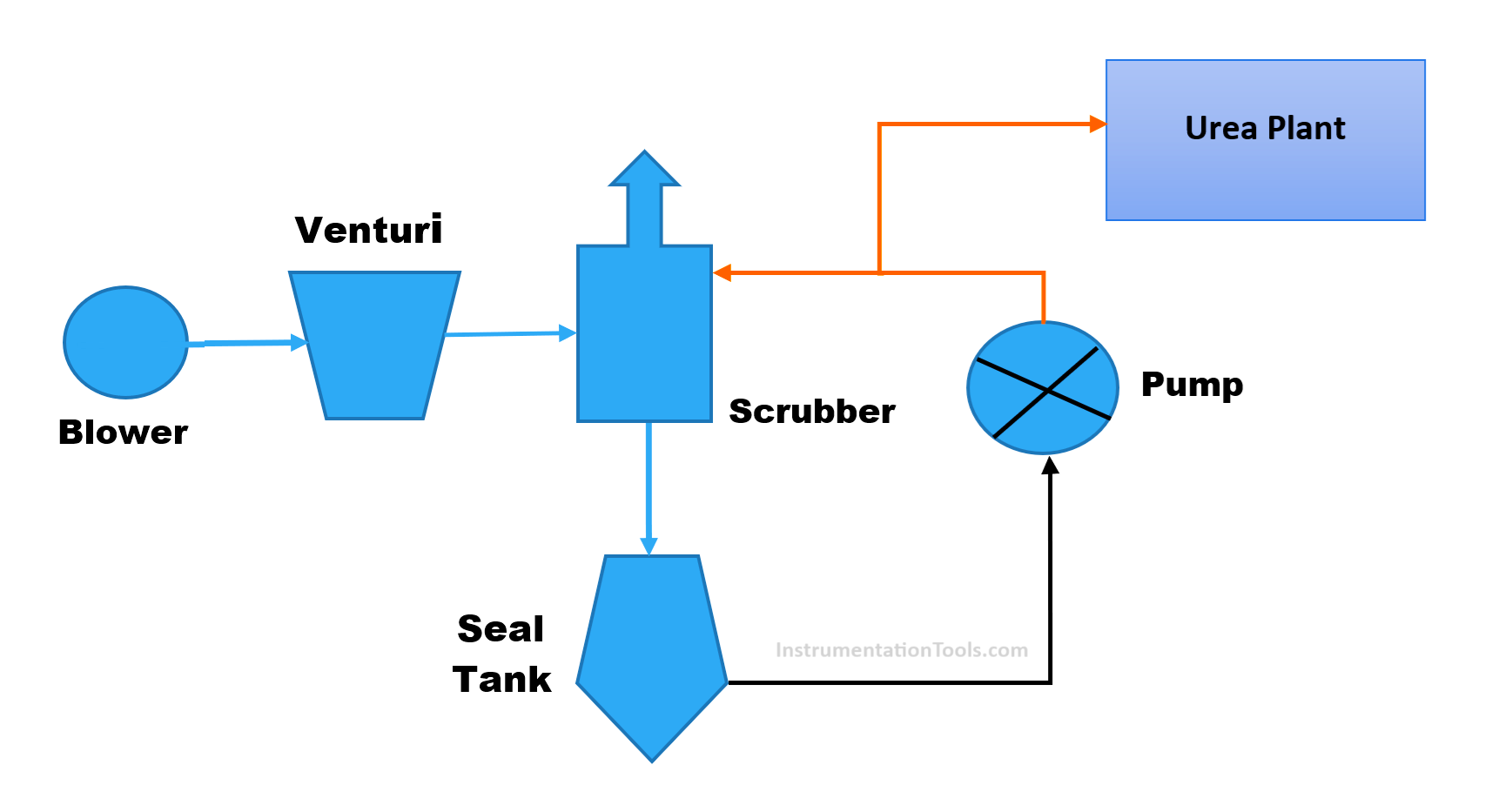
Components of Wet Dust Suppression System
All Important component and their working is listed below:-
- Suction Blower
- Wet Scrubber
- Pump
- Seal tank etc.
Suction Blower
A blower is provided between the duct network and wet scrubber. Blower forces the Dust laden air into Wet Venturi Scrubber.
In general practice Blower Suck 55-60% volume of Dust and Ammonia From all Bagging Machine Spout assembly.
And 30-35% volume of Urea dust and ammonia from Bagging Machine body cum Discharge Hopper.
And it sucks 5-10 % Volume of Urea Dust and ammonia from Bulk conveyor BC-02 aka Urea Material Transfer Main Bulk Conveyor.
Generally Blower Discharge Pressure is 450-500 mmWC and Motor Power rating is 60-70 Kw (motor power rating may vary according to our system need0.
Wet Scrubber
Wet scrubber is provided between Pump and Blower. Blower forces dust laden air into Venturi scrubber and Pump circulates the urea solution through the wet Scrubber. The relative velocity between Urea dust laden air and liquid droplets make for high efficiency by impingement Urea dust is highly soluble in water.
The Urea solution and water droplets are separated from the air with a chevron type mist eliminator located inside the separator of wet scrubber.
Clean air flows to atmosphere through the stack positioned separator and solution flows to Seal tank to provide suction to the pump for recirculation.
An important parameter for wet Scrubber
All the most important parameters range is listed below
- Differential Pressure across the Venturi – 230-250 mmWC
- Inlet Dust Concentration – 10g/m3
- Outlet Dust Concentration – 100mg/m3
- Scrubber Liquid Pressure – 0.35 kg/cm2
- Inlet Air Pressure – 500 mmWC
Pump
WDS Pump recirculates the Urea solution for wet scrubbing unit. A part of solution is discharged to Urea Plant when concentration of Urea solution becomes more than 10 %.Pump takes suction from Seal tank at scrubber outlet and discharge the solution at four points of Venturi scrubber.
Important Parameters for Pump –
- Urea Solution concentration: 10 %
- Specific Gravity of Urea Solution: 1.15
- Discharge Pressure: 2 kg/cm2
Seal Tank
In Wet dust suppression (WDS) system seal tank play very crucial role in management of Dust and Ammonia very efficiently. Seal tank is integral component of WDS system designed to improve the Dust Control of Urea. Seal Tank also ensures that dust control process must be operate efficiently according to dust volume quantity.
Seal tank work as water storage system for the wet dust suppression system. As per requirement it provides the water to wet dust suppression system to work effectively.
The Seal tank tends to maintain a consistent water level so that a constant water supply can we provided for dust suppression.
Seal tank also work as to controller of the water pressure, and provide plenty of water pressure to ensure efficient operation of nozzles and spray systems.
The seal tank designing done in such way that it has self-cleaning property by which it prevent lime, salts, and chalk buildup inside Spray system.Â
Important points to note:
- Free ammonia present in Urea dust laden air and it reacts with Air Moisture and form Ammonium hydroxide (NH₄OH), also known as solution of ammonia (NH₃) in water.
- NH3 + H2O =NH4OH
- Ammonium hydroxide is alkaline in nature and responsible for corrosion of internals pipe line of Blower. Also Urea dust deposited inside the pipeline and forms Lumps in long time which reduces the cross sectional area of pipeline.
- Lumps formation takes place inside the blower & discharge pipe line also.
Advantages of Wet Dust Suppression (WDS) System
In Urea Manufacturing Plant or in Other Fertilizer Plant Dust Control is very important factor to prevent Human, Atmosphere and society from harmful affects.
A few Points are listed below:
Urea dust inhalation can be harmful to workers’ health, nearby area animals, birds leading to fatal respiratory issues for short and long time duration.
Urea dust accumulation on surrounding equipment can cause adverse effect in their efficiency also it can lead to corrosion of Bulk Conveyor, Flat Conveyor, Slat Conveyor, Discharge Hopper and Building Ferrous structure which can lead to financial loss of company.
Dust accumulation on different component of Bagging machine can decrease the efficiency of Bagging Machine.
Dust Mixture Urea Bags have most change to get damage during the transfer of bags from one place to another i.e. from Urea Plant two end user.
Dust Mixture user have more chance to form lumps before bagging and even after bagging.
Controlling dust prevents it from spreading into the surrounding environment and by this way we save our nature and its valuable assets.
How to effective the WDS system in bagging Plant.