When a venturi flow meter is placed in a pipe carrying the fluid whose flow rate is to be measured, a pressure drop occurs between the entrance and throat of the venturi meter.
This pressure drop is measured using a differential pressure sensor and when calibrated this pressure drop becomes a measure of flow rate.
Venturi Flow Meter
The below animations shows the working of venturi flow meter.
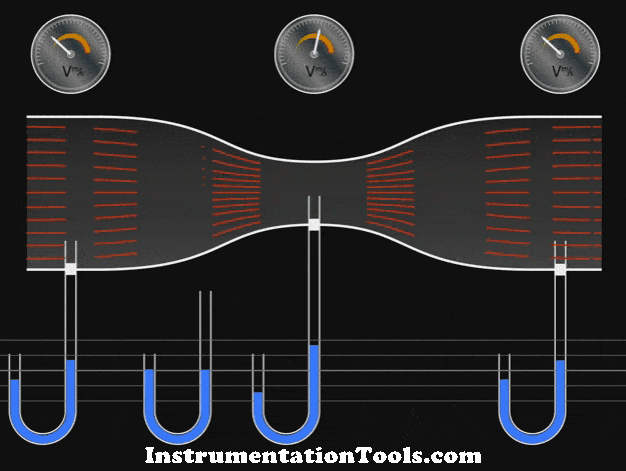
Construction of Venturi meter
The following are the main parts and areas of the venturi meter:
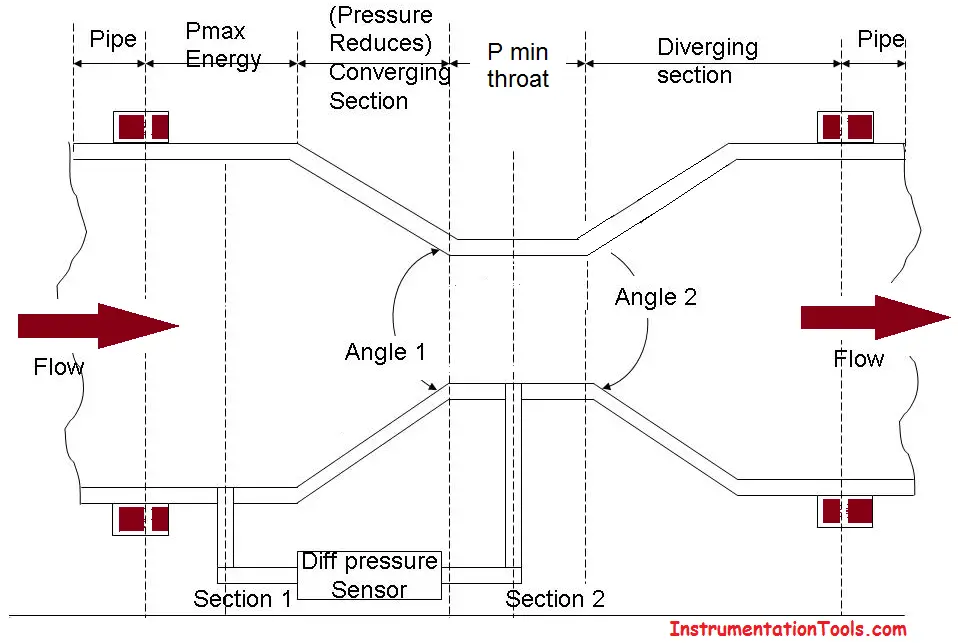
The entry of the venture is cylindrical in shape to match the size of the pipe through which fluid flows. This enables the venture to be fitted to the pipe.
After the entry, there is a converging conical section with an included angle of 19’ to 23’.
Following the converging section, there is a cylindrical section with a minimum area called as the throat.
After the throat, there is a diverging conical section with an included angle of 5’ to 15’.
Openings are provided at the entry and throat (at sections 1 and 2 in the diagram) of the venture meter for attaching a differential pressure sensor (u-tube manometer, differential pressure gauge, etc) as shown in the diagram.
Operation of Venturi Meter
The fluid whose flow rate is to be measured enters the entry section of the venturi meter with a pressure P1.
As the fluid from the entry section of venturi meter flows into the converging section, its pressure keeps on reducing and attains a minimum value P2 when it enters the throat. That is, in the throat, the fluid pressure P2 will be minimal.
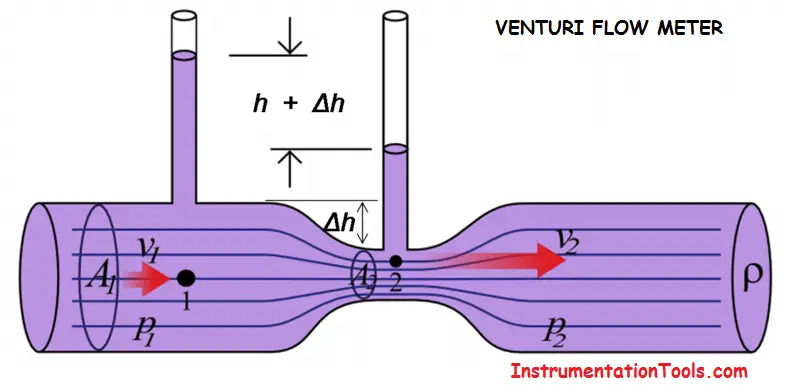
The differential pressure sensor attached between the entry and throat section of the venturi meter records the pressure difference(P1-P2) which becomes an indication of the flow rate of the fluid through the pipe when calibrated.
The diverging section has been provided to enable the fluid to regain its pressure and hence its kinetic energy. The lower the angle of the diverging section, the greater the recovery.
Applications of Venturi Meters
- It is used where high-pressure recovery is required.
- Can be used for measuring flow rates of water, gases, suspended solids, slurries, and dirty liquids.
- Can be used to measure high flow rates in pipes having diameters in a few meters.
Advantages of Venturi Meters
- Fewer changes of getting clogged with sediments
- The coefficient of discharge is high.
- Its behavior can be predicted perfectly.
- Can be installed vertically, horizontally, or inclined.
- Low-pressure drop (around 10% of Δp)
- Lower sensitivity to installation effects than orifice plates
- Less susceptibility to damage
- More suitable for gas flows with entrained liquid
- Comprehensive standards (ISO 5167)
Limitations of Venturi Meters
- They are large in size and hence where space is limited, they cannot be used.
- Expensive initial cost, installation, and maintenance.
- Require long laying length. That is, the venturi meter has to be proceeded by a straight pipe which is free from fittings and misalignments to avoid turbulence in flow, for satisfactory operation. Therefore, straightening vanes is a must.
- Low turndown (can be improved with dual range Δp cells)
- Greater cost to manufacture
- Greater susceptibility to “tapping errors” in high Reynolds number gas flows owing to the high-velocity fluid passing the pressure tapping at the throat.
- Less experimental data than orifice plates
If you liked this article, then please subscribe to our YouTube Channel for Instrumentation, Electrical, PLC, and SCADA video tutorials.
You can also follow us on Facebook and Twitter to receive daily updates.
Read Next:
- Basics of Venturi Flow Meter
- What is Averaging Pitot Tube
- Strain Gauge Pressure Sensor
- How Orifice Measures Flow
- 3-15 psi to 4-20mA Convert
Its educative.
Thanks,
From Emgr G.C. Achakpo