Learn the difference between rotary shaft valves and sliding stem type control valves.
To achieve the required control valve performance, proper shaft or stem travel is required. Insufficient valve travel cannot achieve desired control of any process variable.
Control valves are a primary method for regulating the flow of material and its associated energy into and out of a process.
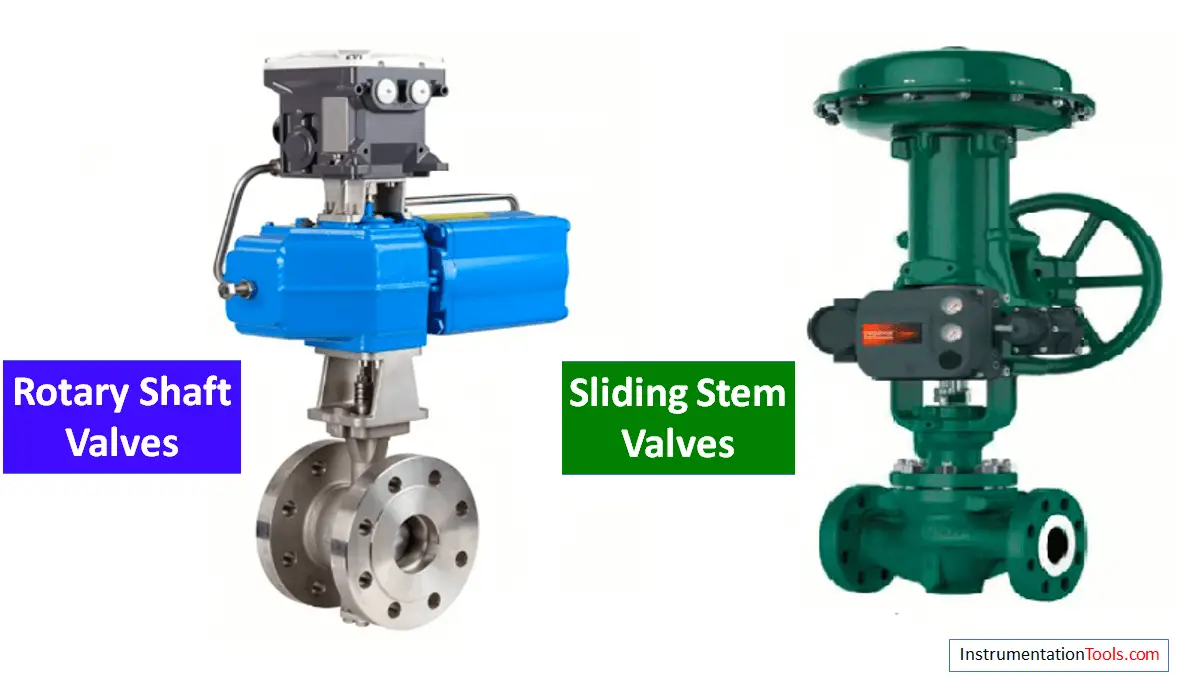
Control Valve Types
Valves are classified based on stem movement as Â
- Rotary shaft control valves.
- Sliding stem control valves.
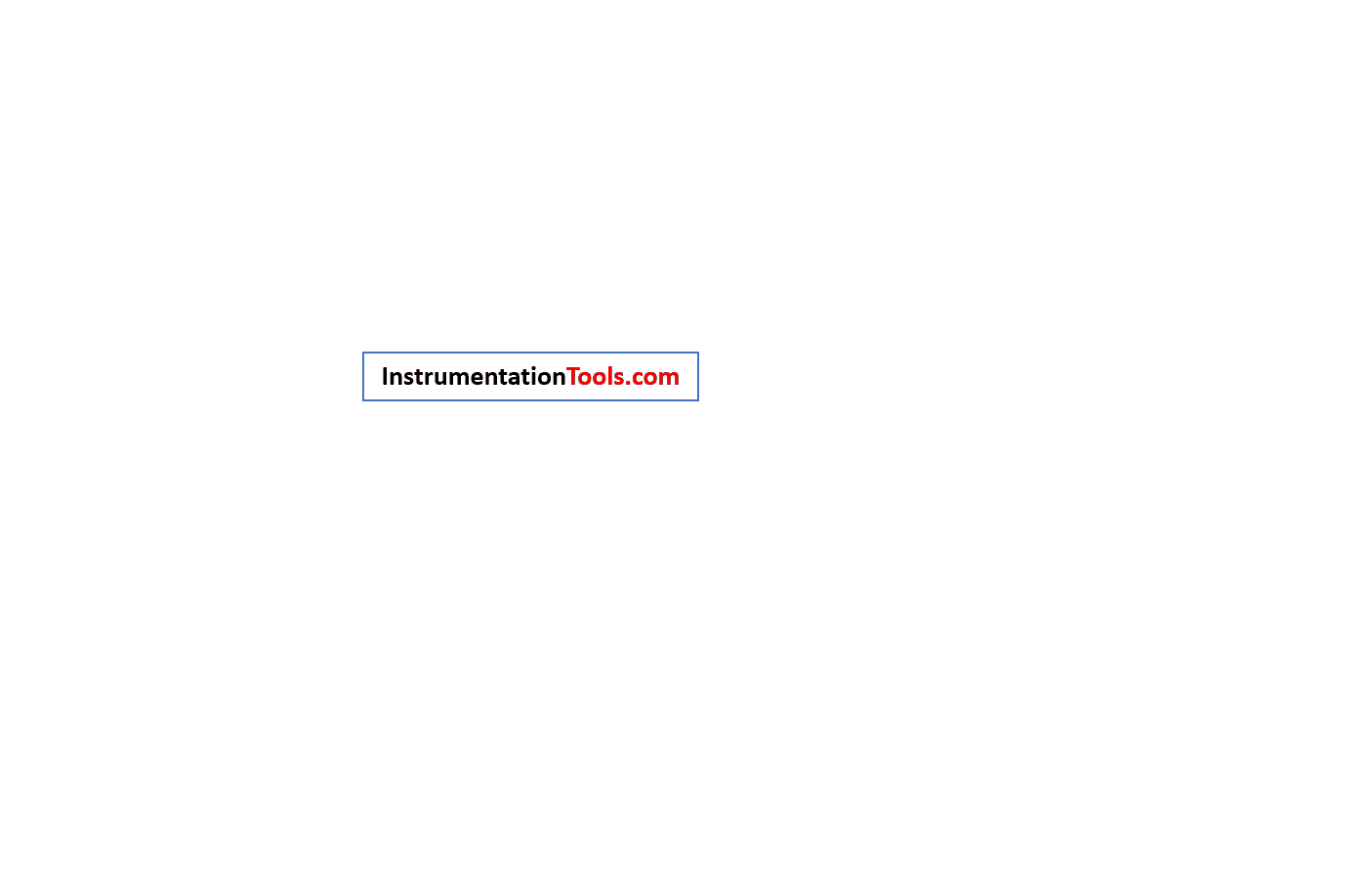
Rotary Shaft Valves
Rotary shaft control valves enjoy the advantages of being
- small in size,
- low weight,
- simplicity or design relatively high flow rates,
- more reliable,
- friction-free packing, and
- relatively low initial cost.
They are not usually found in sizes below one inch.
It is a type of valve with a closure member that moves with a rotary motion to correct the rate of flow through the valve.
Rotary valves are easier to seal than a sliding-stem valve because
1). Rotary valves have less packing to shaft travel distance for each stroke of the valve, thus decreasing the loss of packing material due to friction.
2). Dust and other abrasives from the environment do not have an effect as the shaft slides in and out of the packing.
Rotary valves rotate a shaft that turns a plug or a ball. They are less prone to clogging in services like dirt applications.
Rotary valves are also called quarter-turn valves as they use a closure element that rotates through a quarter turn or 90 degrees range to stop the flow.
A rotary motion valve in almost all cases rotates 90 degrees completely closed with an indication at 0 degrees, open position, and 90 degrees.  Â
The most commonly used rotary valve is the butterfly valve. Butterfly valves are range in size from 2 inches through 36 inches, or even large. They are generally used in applications involving large flows, high static pressures, and limited pressure drop availability.
Another type of rotating shaft control valve of particular usefulness is the eccentric cylindrical plug valve. Its cost is low, relative capacity is high. It is especially useful on services involving fluids with suspended solids, corrosive fluids, and viscous liquids.
There are two distinctly different types of ball control valves, one involves a ball with a passageway through it. This is generally specified as the full ball type. Ball valve that modifies flow rates with the rotary motion of the closure member, which is either a sphere with an internal passage or a segment of a spherical surface.
The second type is developed along the lines of the concentric plug valve and utilizes a hollowed-out spherical segment, which is supported by a shaft. Both types of these ball valves are quarter-turned rotary valves.
Ball valves have the highest flow capacity of any commonly used control valve. They are useful whenever slurry is involved and also provide tight shift off.Â
Advantages of rotary ball or butterfly over traditional globe valve are
- Lower cost, and weight
- Higher flow capacity
- Tight shut-off
- Lower leakages.
Sliding Stem Control Valves
Sliding stem valves are more resistant to cavitation compared to a rotary valve.
Sliding stem valves have the smallest amount of dead band because it offers low trim friction as a direct connection between the actuator shafts and trim stems.
Sliding stem valve linearly moves a stem that moves a plug, presses a diaphragm, or pinches a boot. In a sliding motion valve, the stem and valve movement is up and down, a common control valve is the gate valve.
In sliding stem control valves, the valve plug is positioned by a stem that slides through a stem gland packing.
Sliding stem linear motion control valves may be single-seated, double-seated. They have various body types and most common being in the form of a gate or globe.
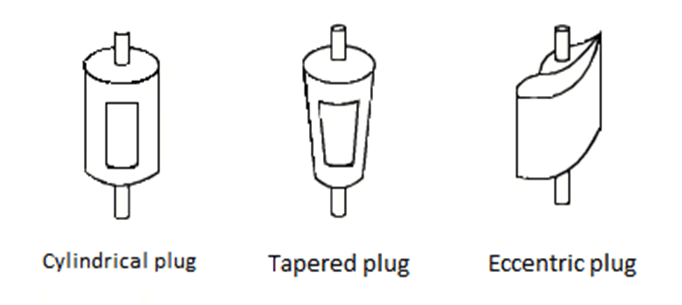
The sliding stem single-seated valves are commonly employed for situations in which tight shut-off is required in small-sized valves. Â
Double seated valves generally have leakage through the valve that is a bit higher than in single-seated valves because it is virtually not possible to close the two ports simultaneously, but the advantage of double-seated bodies is that the hydrostatic effect of the fluid pressure acting on each of the two seats will tend to cancel out and little actuator force is necessary to move the valve.
Sliding stem linear motion valves are also used in three-way valve bodies where the control valve may be used to divert a stream or to combine streams.
Packing friction is the major cause of dead-band in sliding stem control valves, the measured friction can vary remarkably between various valve styles and stem packing arrangements.
If you liked this article, then please subscribe to our YouTube Channel for Instrumentation, Electrical, PLC, and SCADA video tutorials.
You can also follow us on Facebook and Twitter to receive daily updates.
Read Next:
- Valve Commissioning
- What is a Pilot Valve?
- What is a Spool Valve?
- Sliding Stem Valve Principle
- Types of Failures in Valves