What is Corrosion?
Corrosion is a natural destructive phenomenon where metal in presence of moisture and air (oxygen) form its metallic oxide, hydroxide, or sulfide form.
For e.g. when iron comes in contact with air and moisture it forms iron oxide.
The reddish-brown color which forms on the metal surfaces is known as rust while the phenomena of chemical reactions happening on the metal surface are known as corrosion. So, corrosion is a process while rust is the end result.
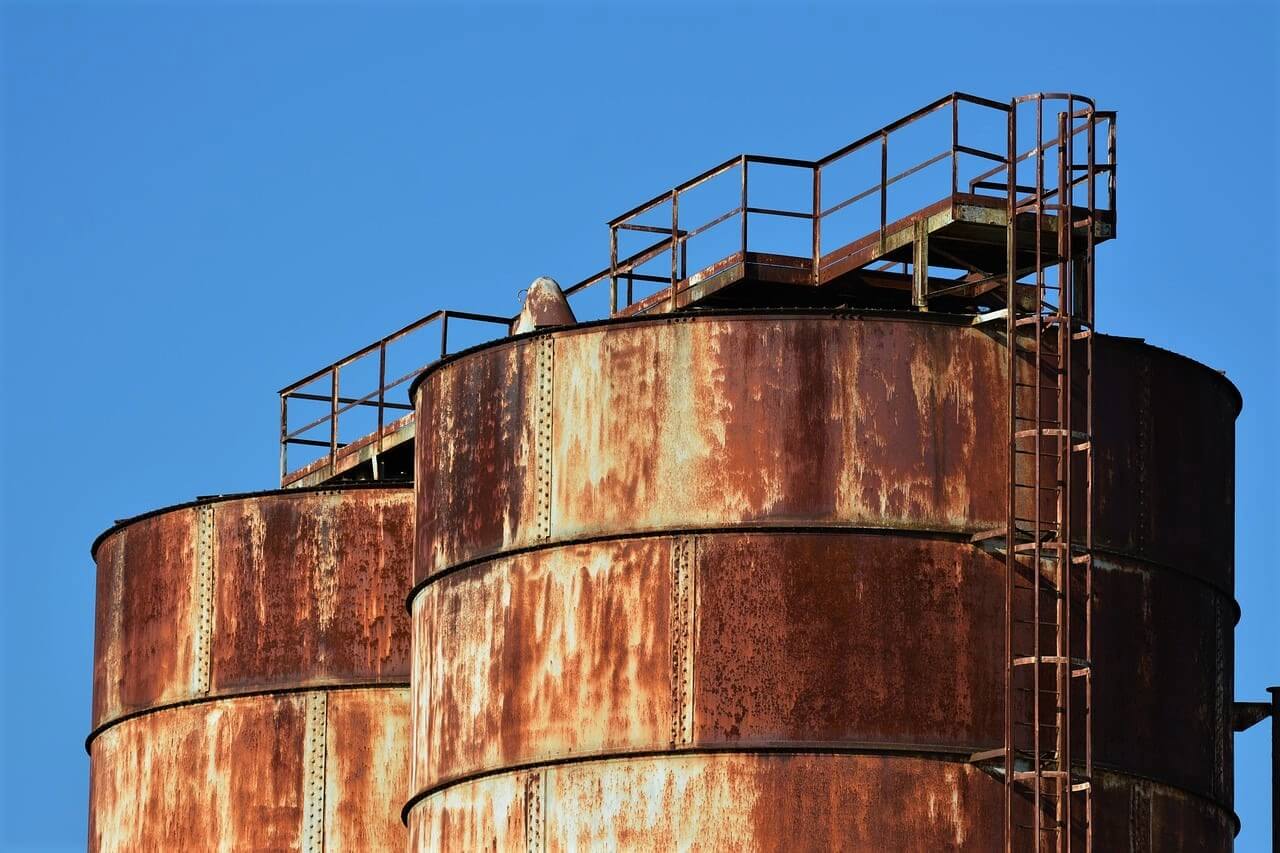
Rusting is a Redox reaction that is a combination of Reduction and Oxidation. The reduction reaction is a process where an element gains an electron while the oxidation reaction is a process where an element loses an electron.
Most metals are easily oxidized, they tend to lose electrons to oxygen. As oxygen is reduced (gains electron), it forms an oxide with the metal.
Types of Corrosion
- Galvanic Corrosion – When reduction and oxidation takes place on different kinds of metal in contact with one another, the process is called galvanic corrosion.
- Electrochemical Corrosion – it occurs commonly in electronic equipment, water or other moisture becomes trapped between two electrical contacts that have an electrical voltage applied between them. This result in an unintended electrolytic cell.
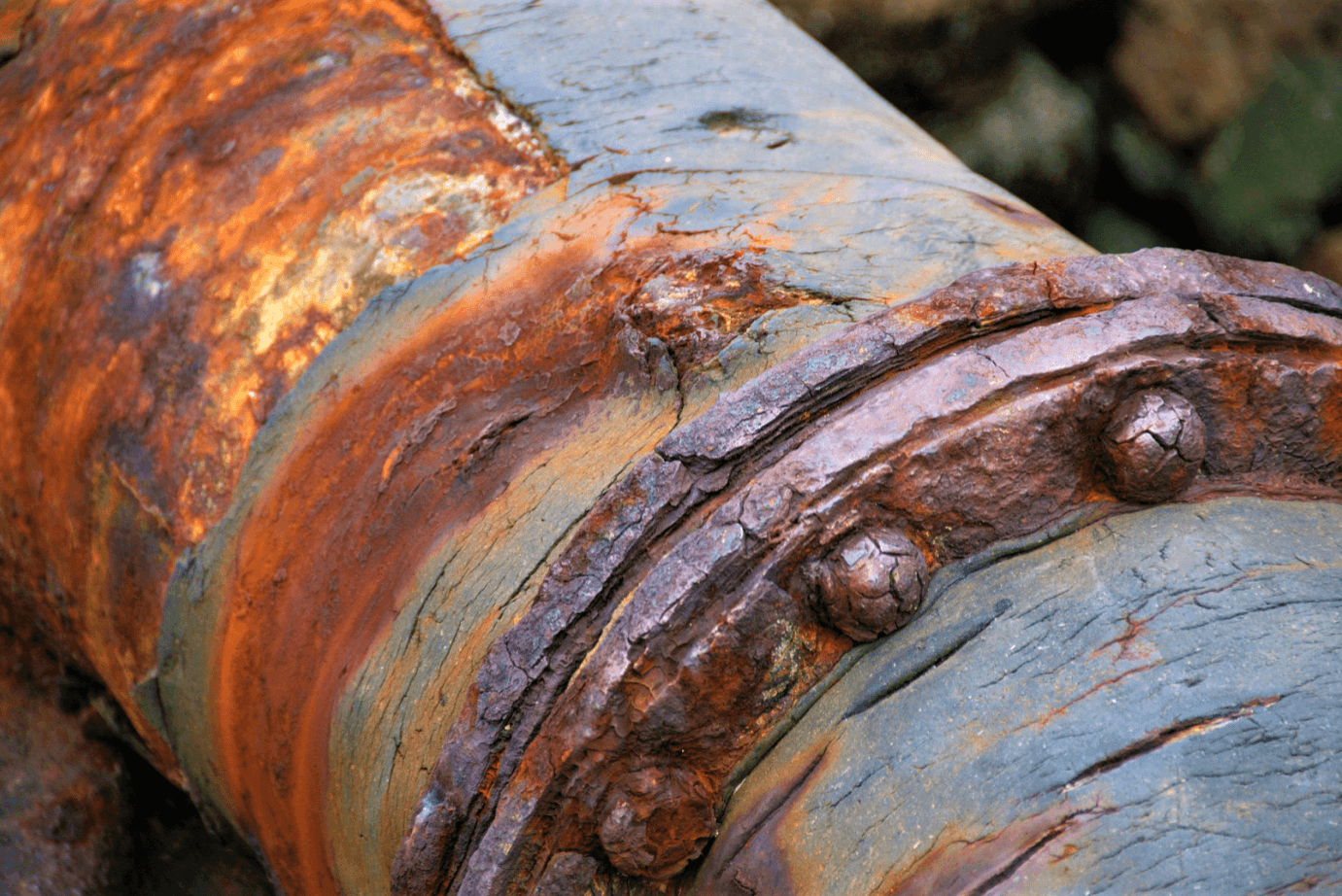
Ways to Prevent Corrosion
Corrosion causes huge losses to any organisation. To prevent corrosion we use a Cathodic Protection system.
Cathodic protection is a process of providing protection to the buried and submerged or above ground metallic parts against corrosion it is also used to prevent corrosion in a bridge, an oil rig and other metallic structures.
It increases the lifespan of metallic structures thus increasing productivity & safety. Here the metal to be protected acts as a cathode, therefore the term cathodic protection.
Now we will discuss about cathodic protection and its different types.
Types of Cathodic Protection
Here we will discuss about the two types of cathodic protection methods.
They are
- Sacrificial Anodic Protection and
- Impressed Current Protection
Sacrificial Anodic Protection
Sacrificial Anodic Protection used in underground pipelines, crude tanks.
In sacrificial anodic protection a more reactive metal (such as Zinc, Aluminium, and Magnesium) is used as an anode because they have low electrochemical potential as compared to steel) while the metal to be protected acts as a cathode.
When two metals are electrically connected to each other in an electrolyte e.g. seawater, electrons will flow from the more active metal to the other, due to the difference in the electrical potential.
When the most active metal (anode) supplies current, it will gradually dissolve into ions in the electrolyte, and at the same time produce electrons, which the least active (cathode) will receive through the metallic connection with the anode.
The result is that the cathode will be negatively polarized and hence be protected against corrosion.
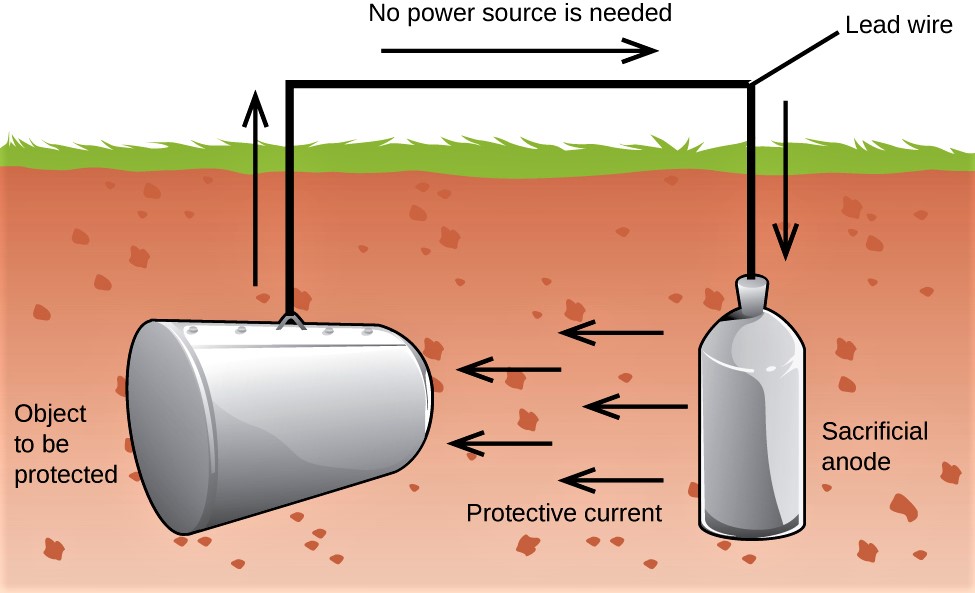
It is temporary Cathodic protection. Its minimum Lifespan is 25 years. In a year, if 2ma current is sent continuously, then 3gm of zinc anode will corrode.
Impressed Current Protection
Impressed Current Protection used in storage tanks and mounded bullets.
The impressed current method is used for the protection of large underground structures like the tank bottom and bullets.
Here the anode is an MMO anode (Mixed metal oxide) with small proportions of titanium and indium. The number of MMO anode rings varies according to the diameter of the tank/structure.
Three loops are taken out from MMO anodes and are connected to the Anode junction box. When DC potential is applied current starts to flow from anode to cathode (the structure to be protected).
HDP sheet is provided such that electrons can flow from anode to cathode. The CuSO4 electrodes are installed in different locations to monitor the pipe to soil potential. 60% of sand in the bitumen layer to ensure continuity of electron flow.
Two drain points are provided to complete the circuit. One measuring point is given to measure the current. If corrosion occurs on the tank bottom then at that part the resistance will be high.
So there will be a voltage drop and the reference electrode at that part will show a drop in potential. Future monitoring pipelines to monitor the pipe to soil potential manually.
Factors affecting corrosion rate
Some factors which affect the rate of corrosion are-
- Temperature – Steel and other metals corrode faster in high temperatures. So, metallic structures exposed to higher temperature will corrode much faster.
- Conductivity – For Corrosion to occur there has to be conductivity between two parts of corrosion reaction. Corrosion will not happen in distilled water, however it will be maximum in saline water.Therefore corrosion happens more in coastal & humid areas.