When you work in industrial automation, one key aspect to understand is the communication protocol. Beyond hardwired I/Os, modern systems rely heavily on communication protocols for transferring large volumes of data. One such protocol widely used in factory automation is DeviceNet. It is robust, efficient, and often misunderstood. Let’s dive into some important facts about DeviceNet through a simple question-and-answer format.
1. What is DeviceNet?
DeviceNet is an industrial communication protocol developed by Rockwell Automation and now maintained by the ODVA (Open DeviceNet Vendors Association). It is based on the CAN (Controller Area Network) physical and data link layers and utilizes CIP (Common Industrial Protocol) at the application layer. Unlike Ethernet/IP, DeviceNet supports deterministic control and is ideal for low-level device communications.
2. What is the physical connection method used in DeviceNet?
DeviceNet typically operates using a scanner-slave architecture. A DeviceNet scanner module communicates with multiple slave devices (like sensors or I/O modules). The physical topology is usually trunk-line/drop-line, where 5 wires are used:
- V+
- V-
- CAN-H
- CAN-L
- Shield (Drain)
Power and data share the same cable, simplifying the wiring. The trunk line supplies power, and drop lines connect to devices. The network requires terminating resistors (121 Ω) at both ends of the trunk line to prevent signal reflections.
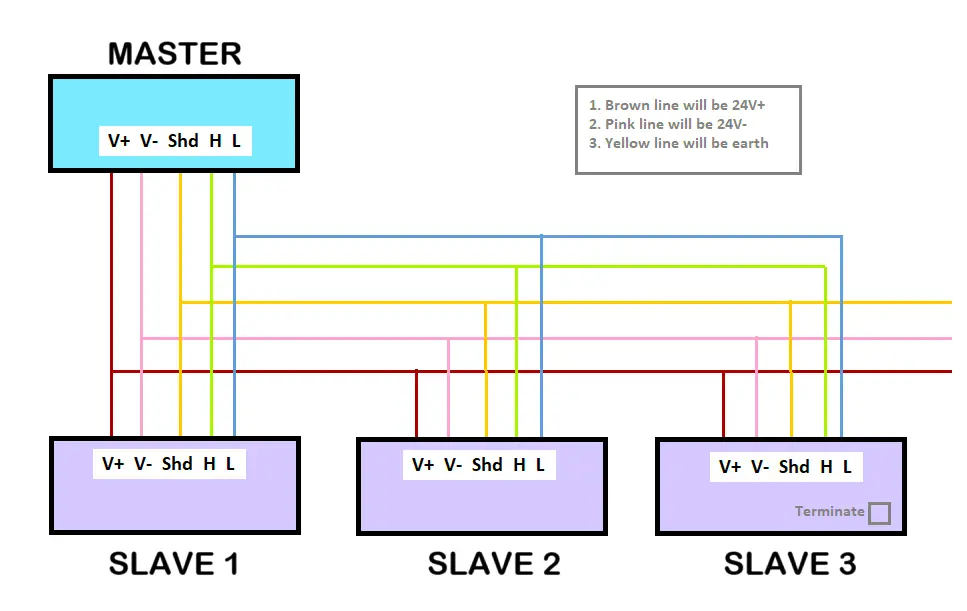
3. How are devices identified?
Each DeviceNet device is assigned a unique MAC ID (Node Address) between 0 to 63, usually configured via DIP or rotary switches. Duplicate node IDs are not allowed and will cause a communication fault. Note that the MAC ID in DeviceNet is not the same as an Ethernet MAC address.
4. How is data communicated?
DeviceNet uses CIP object models to exchange data. Communication types include:
- Implicit Messaging: For time-critical I/O data
- Explicit Messaging: For configuration and diagnostics
Devices exchange data using the CIP structure of classes, instances, and attributes. To configure devices in a PLC, an EDS (Electronic Data Sheet) file is used to define how to interpret device data.
5. Is polarity important in wiring?
Yes, absolutely. Reversing CAN-H and CAN-L or misconnecting power lines can cause complete communication failure and potential hardware damage. Double-check wiring against documentation during installation.
6. Does cable length matter?
Yes. Cable length affects speed and network stability. Here’s a quick reference:
Baud Rate | Max Trunk Length |
---|---|
125 kbps | 500 meters |
250 kbps | 250 meters |
500 kbps | 100 meters |
Also:
- Drop line length: Max 6 meters (20 ft)
- Total drop length: Must not exceed 156 meters
7. What are the power limits in DeviceNet?
- Trunk line current: Max 8 Amps
- Drop line current: Max 3 Amps
- Overloading the network can cause voltage drops and data loss
- Multiple power supplies can be used only with diode isolation circuits to prevent short circuits
Always plan power budgeting carefully, especially with high-power slave devices.
Summary
DeviceNet is a highly reliable protocol when used correctly. Understanding the roles of MAC ID, proper termination, correct topology, and power limitations ensures a healthy network. With strong vendor support and a robust object-based communication model, DeviceNet remains relevant in many automation applications.
Read Next:
- Difference Between Ethernet IP and EtherCAT
- BACNet IP vs. BACNet MS/TP Comparison
- Difference Between Modbus TCP IP and Profinet
- Basic Industrial Communication Networks
- Difference Between Ethernet IP and Profinet