In the world of industrial automation, a variable frequency drive (VFD) is a motor controller that changes the frequency and voltage of an electric motor in order to control the speed of the motor.
Controlling motor speed has been one of the main requirements in process control industries.
Other names for a VFD are:
- variable speed drive,
- variable frequency drive,
- AC drive,
- microdrive, and inverter.
An electronic speed regulator is made up of circuits that incorporate power transistors such as Insulated Gate Bipolar transistors (IGBTs) or thyristors.
The basic operating principle is to transform industrial frequency electrical energy into variable frequency electrical energy.
The frequency variation is achieved by two stages in series.
- A rectifier stage that transforms AC (alternating current) into DC (direct current), with all the power in the so-called intermediate circuit.
- Another inverter stage transforms direct current into alternating current, with adjustable frequency and voltage, which will depend on the set-point values. This second stage is also often called an undulator.
The entire frequency converter assembly is called an inverter.
What is a VFD?
Variable frequency drives are systems that are located between the electrical power supply and the electric motors.
VFDs are used to regulate the speed of motors by varying the alternating current (AC).
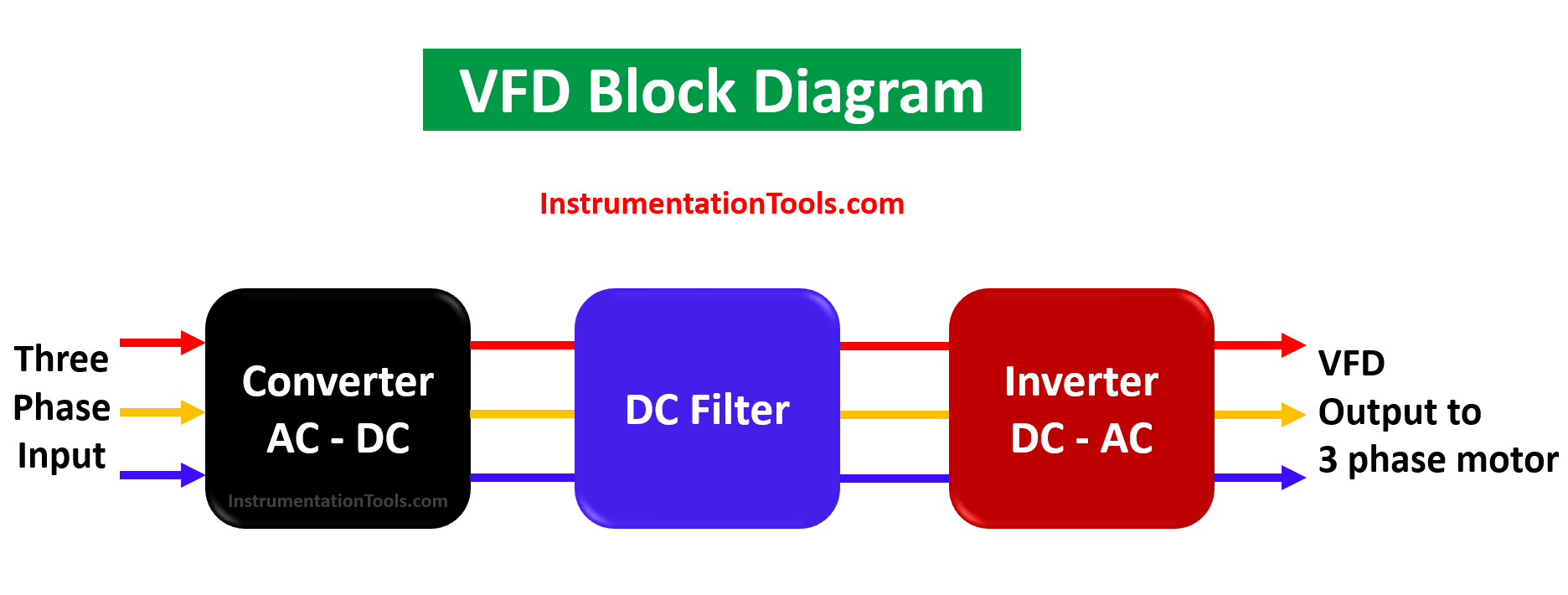
The frequency converter also has the ability to control the ramp-up and ramp-down of the motor when starting or stopping, respectively, even though the drive controls the frequency and voltage of the motor for regulating its speed.
Also Read: VFD Working Principle
By regulating the frequency of the electricity received by the motor, the frequency inverter manages to offer this motor the demanded electricity. Thus avoiding energy loss, or what is the same, optimizing consumption.
Variable Frequency Drive
In an AC motor, the mechanical speed of the rotor is related to the frequency of the currents in the stator. It is possible to control the speed of the rotor by controlling the frequency of the current to the stator.
There is a direct relationship between the control of the frequency of the current at the stator and the mechanical speed, to fix the corresponding stator frequency.
It is on this principle that the operation of the VFD is based – for controlling a mechanical rotation speed by controlling the frequency of the stator current.
What are the basic principles by which a frequency variation is governed?
We know that any motor connected to the electrical power network has a certain torque and certain speed. In the event that they do not meet the requirements of a specific system, we can count on a frequency variation to adjust it to our needs.
Also Read: VFD and PLC Programming
In short, it is about controlling the speed of the motor. Frequency converters “convert”
(hence their name) the alternating current (AC) converted into direct current (DC).
The beginning steps in the process are carried out by an essential part of the drive, called the rectifier. Afterward, the drive’s capacitors take care of the next phase. The capacitors are charged with the direct current transformed by the rectifier and smooth the waveform of the resulting electrical current.
Finally, the last stage is that of the inverter, which converts the direct current into alternating current, again. This is how the motor actually receives the supply adjusted to the needs of adequate frequency and voltage.
How to Choose the right VFD for a motor?
Despite the wide variety of VFD models and manufacturers, the basic selection process is the same.
The following are the details that will help in choosing the right VFD.
- This includes parameters such as voltage, frequency, current, and kW rating
- In the event that more than one motor is to be controlled by one VFD, the ratings of each motor must be considered
- Variable speed drives are not recommended for high starting loads.
Advantages of Variable Frequency Drives (VFD)
The variable speed drives have several advantages:
- The progressive motor starting method reduces the voltage drops in the power network and limits starting currents.
- Reduction in electrical energy consumption due to the effects of reducing the starting torque peak.
- Increased precision of motor speed regulation.
- Possibility of increasing production capacity by increasing the speed of the process.
- The longer useful life for the motor by reducing mechanical impacts through the assignment of acceleration and deceleration ramps for start-up and stop events.
- Savings in maintenance, as there are no mechanical parts that can suffer aging due to mechanical wear.
- Extension of the service life of the driven equipment
- Possibility of creating control loops and interacting with the process. Presently many variable speed drives have inbuilt PID control functions, in addition to activating alarm signals in cases of a process failure, among many other possibilities.
- Have the possibility of basic PLC functions and dynamic braking.
- Improvement of the power factor.
- Have accessibility and control from any point of the plant through the RS485 Modbus port that allows linking with main control systems such as DCS or PLC.
Disadvantages of Variable Frequency Drives (VFD)
Some disadvantages of VFD drives are mentioned below.
- Only qualified technical personnel can carry out the installation, programming, and maintenance of the drives.
- May affect the noise and interference in the electrical network, which could affect other nearby electronic elements.
- For simple applications, it may require a higher investment than a simple system (contactor-protector) although in the long run the supplementary cost is get paid off. This is due to the energy and reactive power savings provided by the drive.
- Inverter faults cannot be repaired on-site (they must be sent to the vendor or technical service shop). In the meantime, another equivalent drive must be available, or the installation must be left out of operation.
Applications of VFD
- VFD can be used in refrigeration and air conditioning.
- Used in lifts, and escalators.
- Speed control of AC motors (induction motors)
- Speed control of conveyors, large exhaust motors.
If you liked this article, then please subscribe to our YouTube Channel for Instrumentation, Electrical, PLC, and SCADA video tutorials.
You can also follow us on Facebook and Twitter to receive daily updates.
Read Next: