In this article, you will learn the Response Time test of RTD and thermocouple.
The Process Parameters in the Industry or Power Plant must be continuously Monitored and Controlled.
The Temperature is one of the most important parameters that need to be controlled. RTD and Thermocouples are used to measure the Temperature.
Response Time Test
The Response Time of Temperature Element is tested in all Power Plants and other industries.
- Measure the sensor’s In-service Response Time to meet the Technical specification requirements
- Verify that the sensing element is at their thermowell and test for air gaps, dirt, and flying Bagasse particles inside the thermowell.
- Distinguish between Sensor Problem and Cable Connectivity Problem.
- Diagnose the sensor or process irregularity.
Temperature Element Tests
Methods of Response Time Test of Temperature Element are:
- Self-Heating Index (SHI),
- Loop Current Step Response (LCSR).
Generally, the Response Time of the Temperature Element has been characterized by a single parameter called Plunge Time (T).
Plunge Time
It is the time taken by the Temperature Element to produce an output of 65% to 66% of its actual Range value, even after the step change in temperature.
Self-Heating Index (SHI)
It is defined as the ratio of change in Resistance to the Electric Power generated in RTD’s Sensing Element.
It applies only to RTDs and is performed to detect the gross change in the Response Time of RTDs.
The Self-Heating Index is performed using Wheatstone’s bridge Circuit.
The unit is expressed in ohms/watt.
The Procedure for Self-Heating Index for RTD is as follows
- The Wheatstone’s Bridge needs to be Balanced,
- Check the Resistance of RTD, the current should be within 2 mA
- Switch the current to “HIGH” The High current must be 5 mA.
- Now hold the RTD to reach a steady state.
- Again the Wheatstone’s bridge must be balanced to the new value of the RTD.
- The RTD’s output Value must be Recorded in the Data Chart. The value maybe Resistance in ohms, Current in mA, and Power in mW.
- Keep on raising the current to its Range Value and note down the display values for about 5 Repetitions.
- Plot the “Self-Heating Curve” graph data on rectangular coordinates in terms of RTD Resistance (R), versus Power (P).
- Calculate the slope of the line. The straight-line path is observed through the Self-Heating Data, and
- Finally, the slope observed is the Self-Heating Index.
Loop Current Step Response (LCSR)
This method was developed to measure the Response Time of RTD and Thermocouple remotely when the sensor is installed in the Process Field.
- This test involves the application of Electric Current at the end of sensor extension leads.
- The Electric Current causes the Sensor to heat and results in a change in temperature transient inside the sensor.
- The time plot, of sensor heating and cooling, is recorded during the LCSR test.
- LCSR transformation represents the sensor response time.
- The LCSR test holds good for all the effects of installation and process conditions.
- The LCSR test provides a sensor’s actual “In-Service” Response time.
The Loop Current Step Response (LCSR) Test Procedure differs for RTDs and Thermocouples
RTD Loop Current Step Response Test Procedure
The Loop Current Step Response (LCSR) Test Procedure for RTD:
- Wheatstone bridge is used to perform the LCSR test for RTD.
- The bridge must be balanced with RTD at a current of 1 to 2 mA DC.
- Switch the current to “HIGH.” For 30mA to 50 mA.
- Wait for the RTD sensing element to heat up gradually and settle at a few degrees above the ambient temperature.
- The rise in RTD Temperature depends on the magnitude of the heating current used and its Surrounding medium.
- Normally during LCSR, the RTD gets heated up to 5 oC to 15 oC
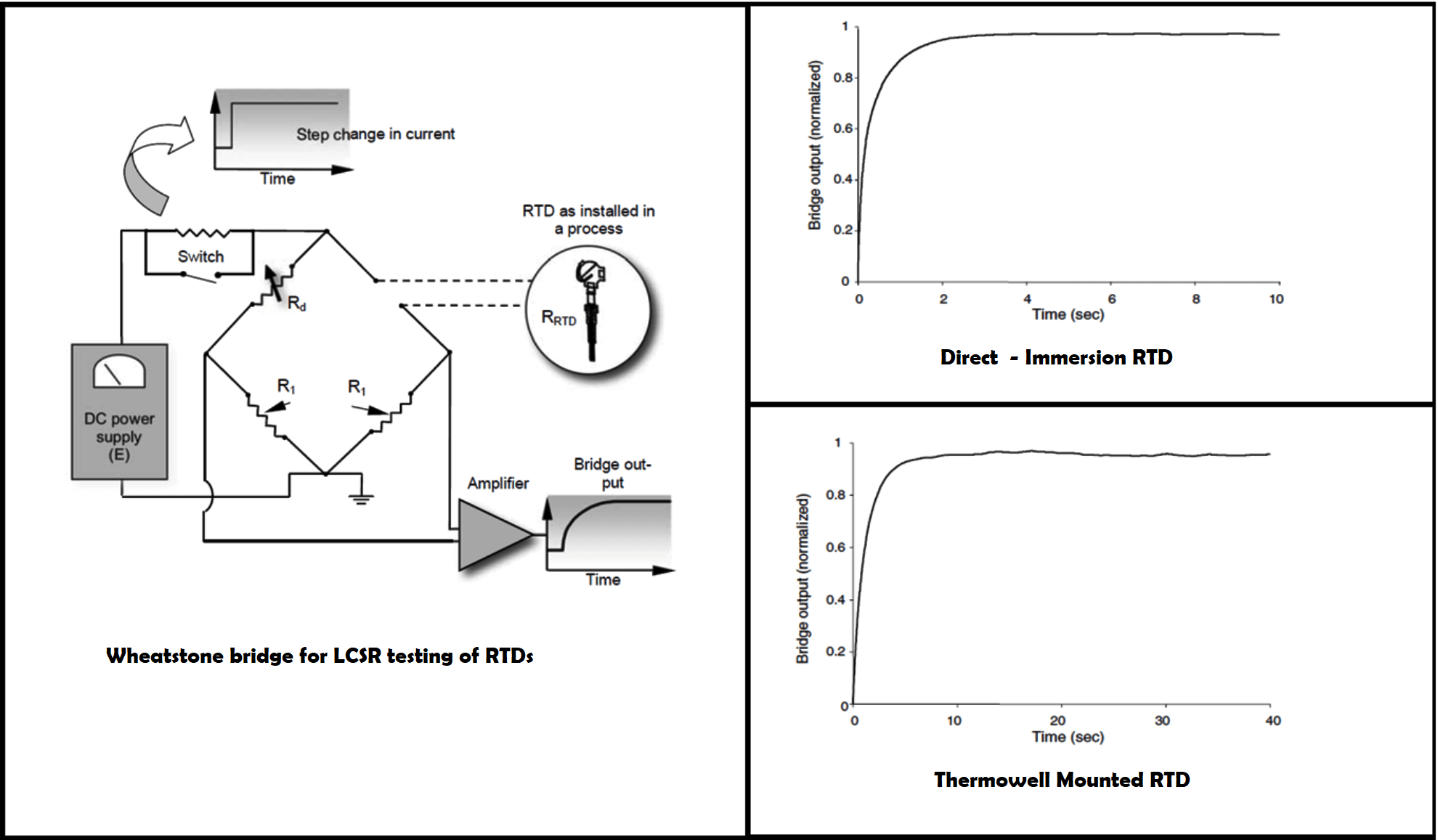
The above diagram shows the graph of 2 LCSR test transients:
- Direct-Immersion RTD and
- Thermowell-Mounted RTD.
But these transients are from the LCSR testing of the RTDs in power plants using a heating current of about 40 mA.
The Direct-Immersion RTD has a faster Response Time that heats up faster than the Thermowell-mounted RTD.
And these transients are caused by internal heating and cannot provide the RTD’s response time until after the data is transformed.
To provide the necessary current for the LCSR test, the Power Supply in the Wheatstone bridge is adjusted so the high current must lie between 30 and 50 mA, depending on the RTD and the process in which it is installed.
If the RTD is in a stable process, then only 30 mA is enough. On the other hand, if the RTD is in a process that has large temperature fluctuations, a higher current of 50 mA is required to improve the Signal to Noise (S/N) ratio.
To adjust the amplitude of the LCSR signal an amplifier can be used at the output of the Wheatstone bridge.
The Wheatstone bridge’s output voltage (V) changes almost linearly with changes in RTD resistance (δR) during the LCSR test.
Thermocouple Loop Current Step Response Test Procedure
The LCSR test procedure for Thermocouple and RTD is different although the principle of the test and data analysis is the same for Both RTD and Thermocouple.
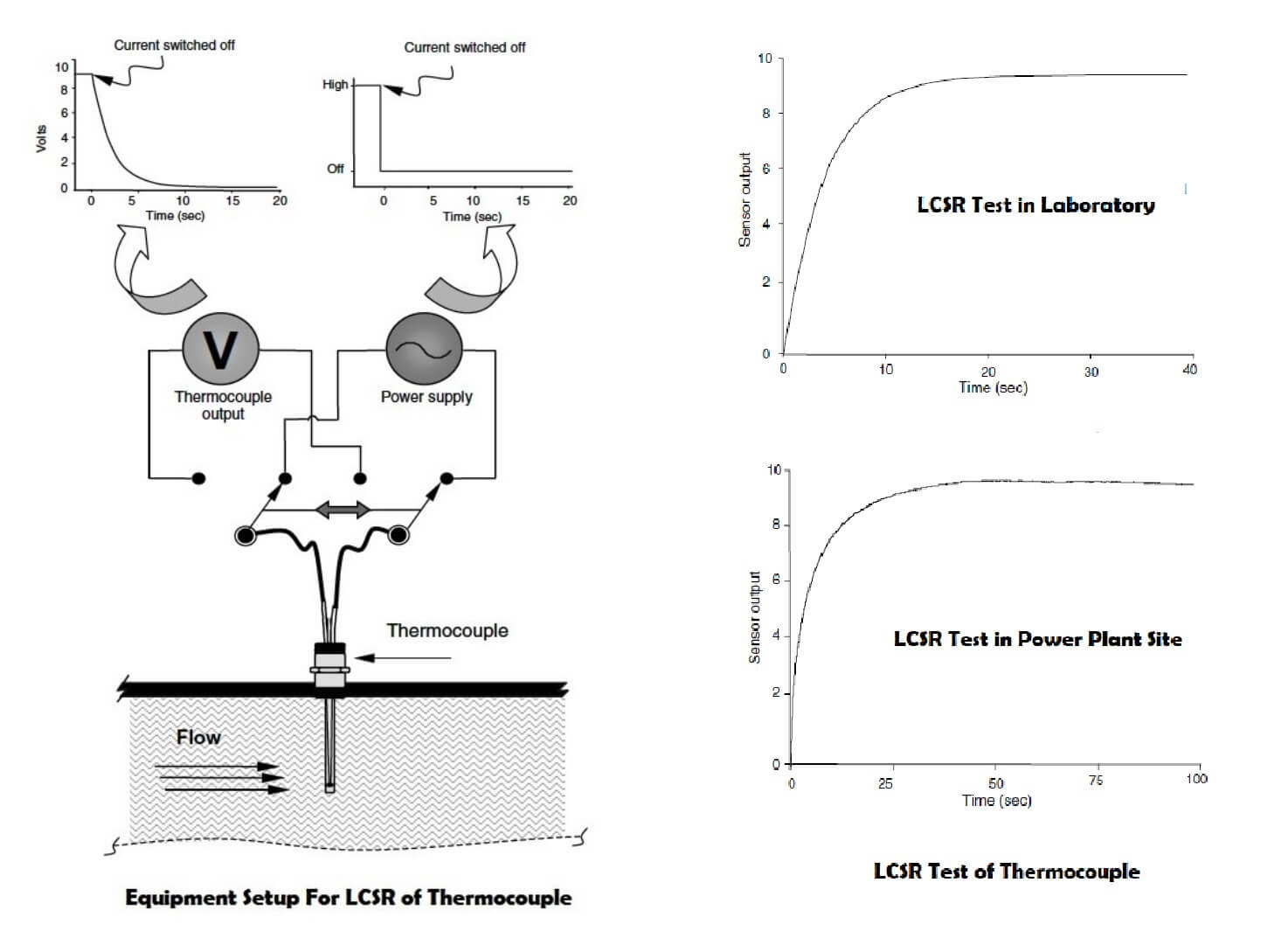
For LCSR testing of thermocouples, to heat the sensor an AC signal is required instead of a DC signal. This is because AC cancels the Peltier effect at the thermocouple junction.
The Higher current of 500mA is also required because the thermocouples circuit resistance is distributed along the length of the Thermocouple. And the whole Thermocouple unit is heated on applying the LCSR test current
Peltier effect: It is defined as the change in heat content when 1 coulomb of charge crosses the junction. If current flows in the same direction heat are liberated in the hot junction and heat is absorbed in the cold junction. And if the current flows in the opposite direction heat are liberated in the cold junction and heat is absorbed in the hot junction.
The difference between the LCSR testing of RTD and Thermocouple is that
In LCSR testing of RTDs, the data is collected as current is running through the circuit and the RTD is heating up.
In LCSR testing of Thermocouples, the data is collected after the current is switched off and while the thermocouple is cooling down to the ambient temperature
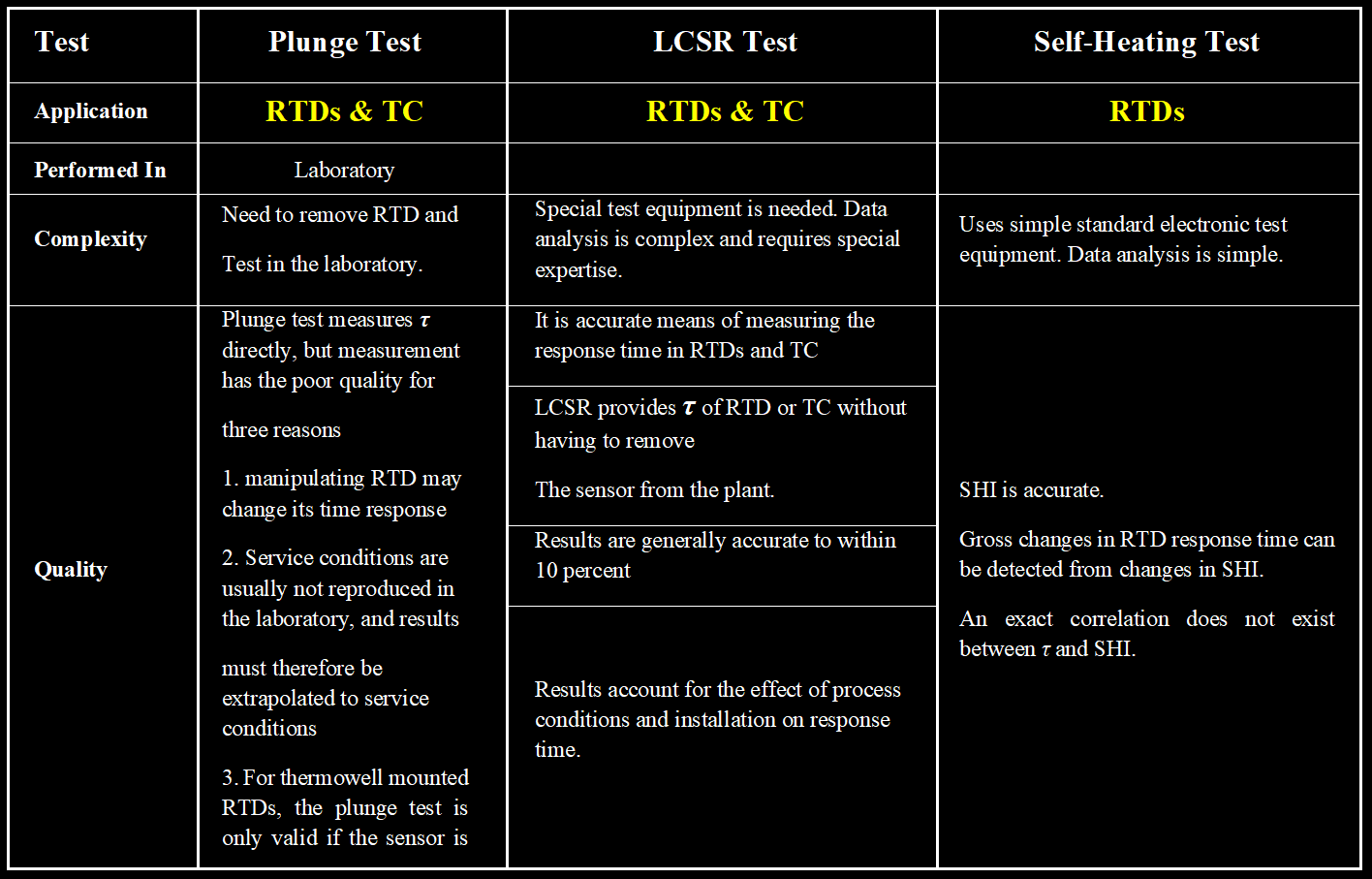
To obtain the Thermocouple response time, the LCSR transient must be analyzed using the same procedure as RTDs. Therefore, the LCSR cooling transient for thermocouples is often inverted when presenting the plot of the raw data.
Reference: Maintenance of Process Instrumentation in Power Plants H.M. Hashemian