This is a PLC Program for the automatic water separation process. Learn ladder logic with the example problems.
Oil and Water Separation Process
Problem Description
Implement oil and water separation process in PLC using ladder diagram programming language.
Problem Diagram
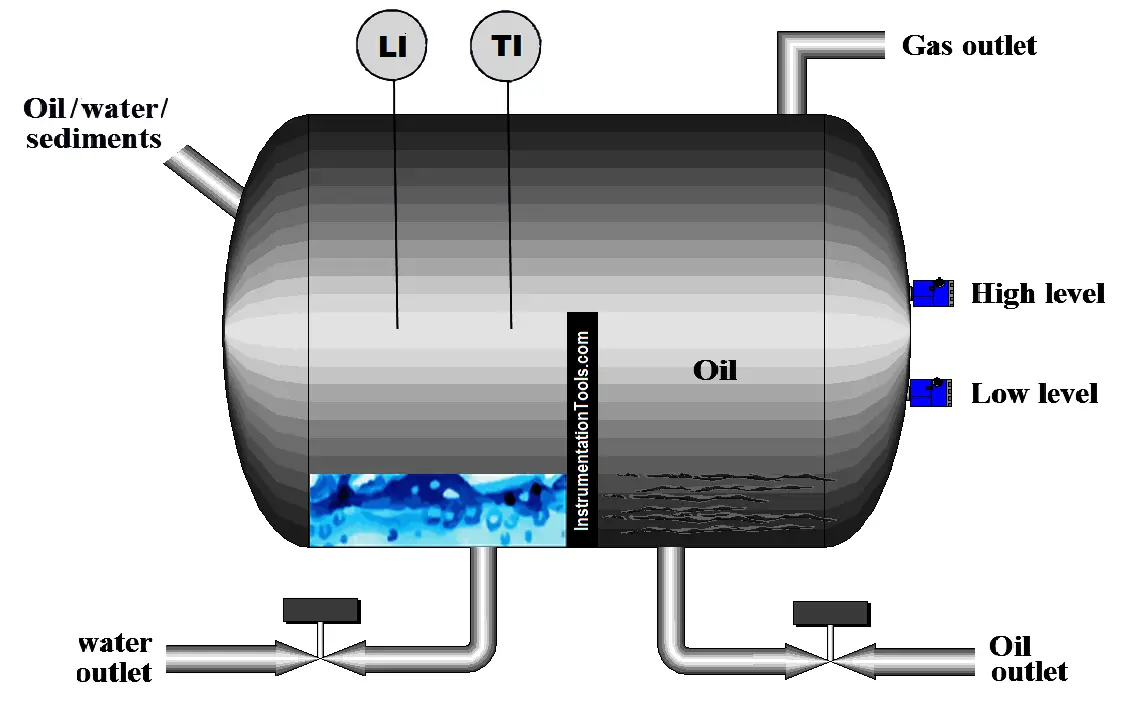
Problem Solution
We will use PLC S7-300 for this application. We will use scaling for programming purpose.
Due to the gravitational force and density of water and oil, when oil and water both are present in liquid, oil always resides on the top of the water. By using this concept we have made one arrangement for oil and water separation as shown in figure.
However, this system is not completely removing water particles from the mixed liquid but only less than 10% of water contents are presents after this process.
Temperature transmitter is used to control the temperature in the tank and level transmitter is used to control or display the level of the tank.
Here, for monitoring purpose it is considered that level is 200cm and temperature is 50 degree centigrade.
Level sensors are used for controlling the oil control valve.
I/O List
List of inputs
- Cycle START :- I0.0
- Cycle STOP :- I0.1
- High level :- I1.1
- Low level :- I1.0
- Level transmitter input :- IW64 (analog)
- Temperature transmitter :- IW66 (analog)
List of outputs
- Oil outlet valve :- Q0.0
M memory
- Master coil :- M0.0
- LT_input DINT : – MD100 (DINT)
- Multiplication value :- MD104
- Actual level :- MD108
- TT_input DINT :- MD112
- Multiplication value :- MD116
- Actual temperature :- MD120
PLC Ladder Diagram
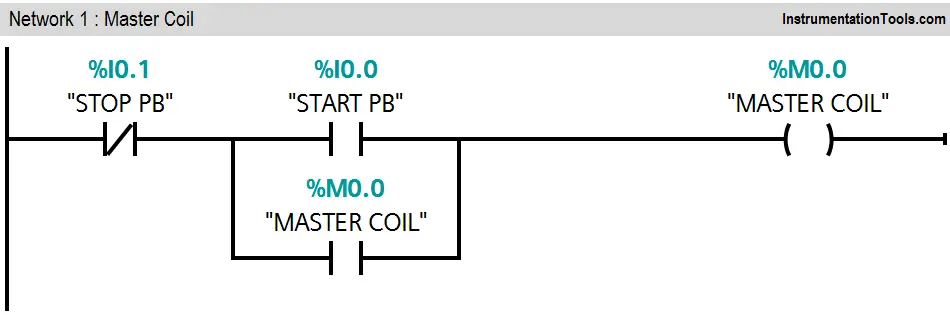
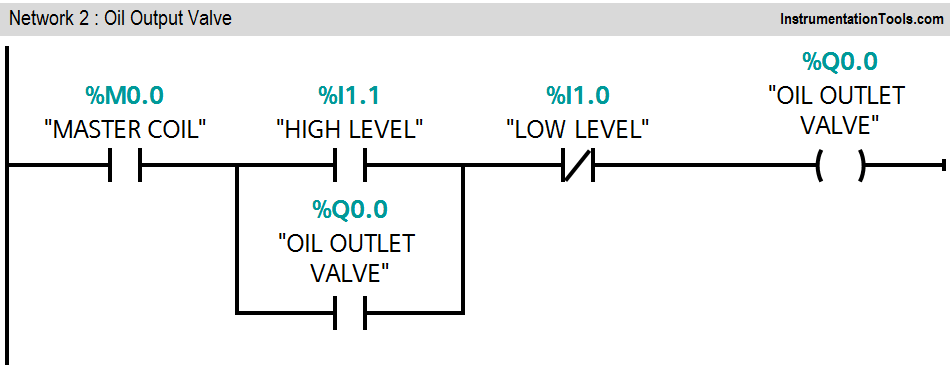
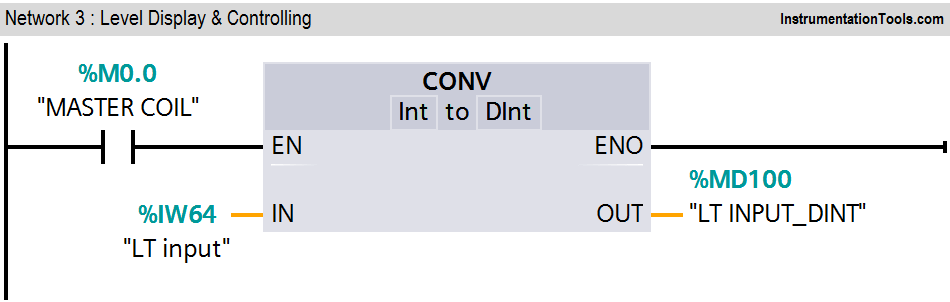
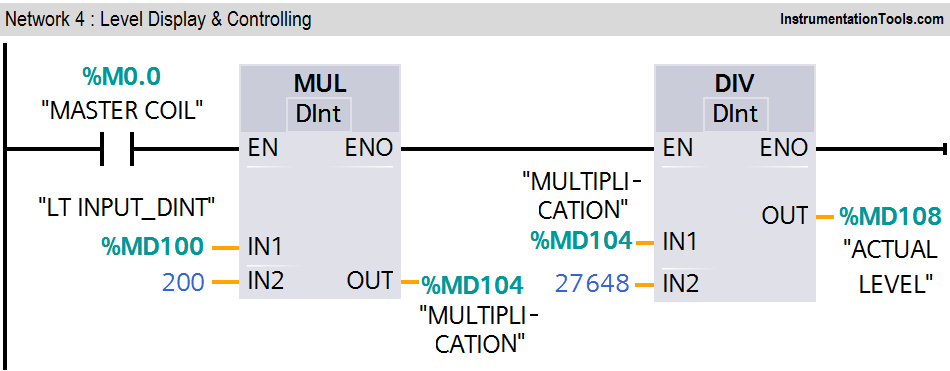
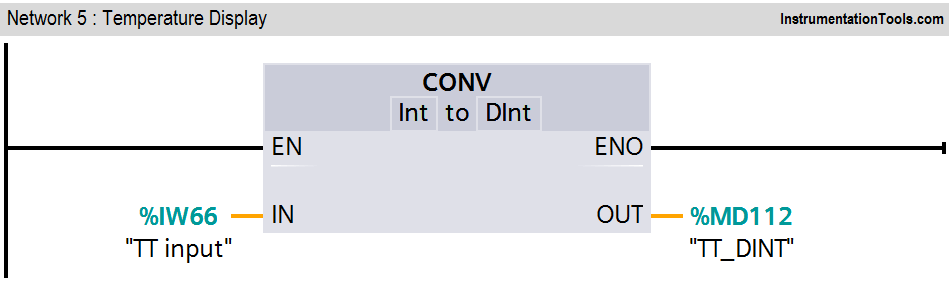
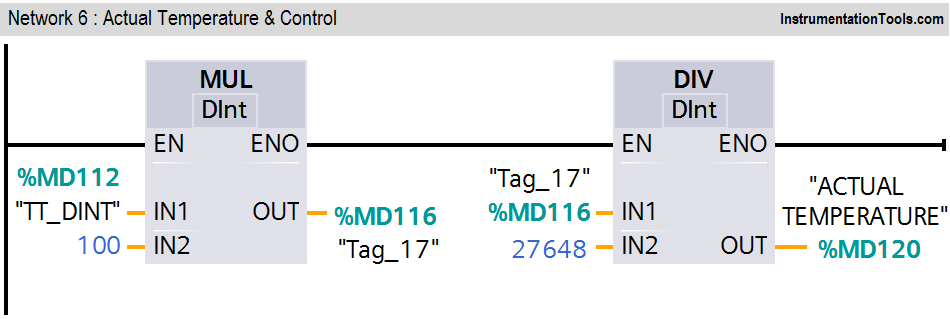
PLC Program Description
For this application, we used S7-1200 PLC and TIA portal software for programming.
Network 1:
we used latching circuit for master coil (M0.0) output. It can be started by pressing START PB (I0.0) and stop by pressing STOP PB (I0.1).
Network 2:
When high level (I1.1) is detected and low level (I1.0) is not detected, oil outlet valve (Q0.0) will be ON.
Network 3:
Here actual count or value coming from the level transmitter is current (4 to 20mA) so by using analog input channel in the PLC we can convert it into digital count.
This digit is in INT (IW64) format so we need to convert it into DINT (MD100) for calculation or multiplication.
Network 4:
DINT value (MD100) is multiplied with max height (200cm) of the tank for calculation purpose.
The multiplied value (MD104) is divided by max count of the analog module (27648).And final actual level is stored in MD108.
Network 5:
Here actual count or value coming from the temperature transmitter is current (4 to 20mA) so by using analog input channel in the PLC we can convert it into digital count.
This digit is in INT (IW66) format so we need to convert it into DINT (MD112) for calculation or multiplication.
Network 6:
DINT value (MD112) is multiplied with max temp (100 degree) of the tank for calculation purpose. The multiplied value (MD116) is divided by max count of the analog module (27648).And final actual temperature is stored in MD120.
Note:- Above application may be different from actual application. This example is only for explanation purpose only. We can implement this logic in other PLC also. This is the simple concept of oil and water separation process, we can use this concept in other examples also.
All parameters considered in example are for explanation purpose only, parameters may be different in actual applications. Also all interlocks are not considered in the application.
Result
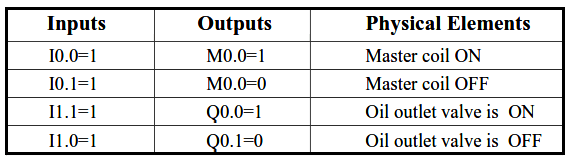
If you liked this article, then please subscribe to our YouTube Channel for PLC and SCADA video tutorials.
You can also follow us on Facebook and Twitter to receive daily updates.
Read Next:
- PLC Problems Troubleshooting
- Failsafe Wiring Practices
- PLC Sinking and Sourcing
- Digital Signals Wiring Techniques
- PLC Program Examples
What is TIA portal software?
super explanation for basics