PLC Programming for Controlling Conveyor Direction: Facilitating Forward or Reverse Movement Based on Detected Part Size. Identify Each Part’s Size and Ensure its Distribution to the Designated Location.
Advanced PLC Conveyor Control
The hopper provides different size objects when the operator presses the pushbutton then the conveyors and sensors are used to separate the objects based on their size.
A pusher is used to separate two different object sizes. The conveyor can move forward and in reverse directions to place the objects as per their dedicated storage trays.
A robot is used to pick and place the objects in medium size boxes.
The below simulation shows the PLC conveyor simulation with different box sizes.
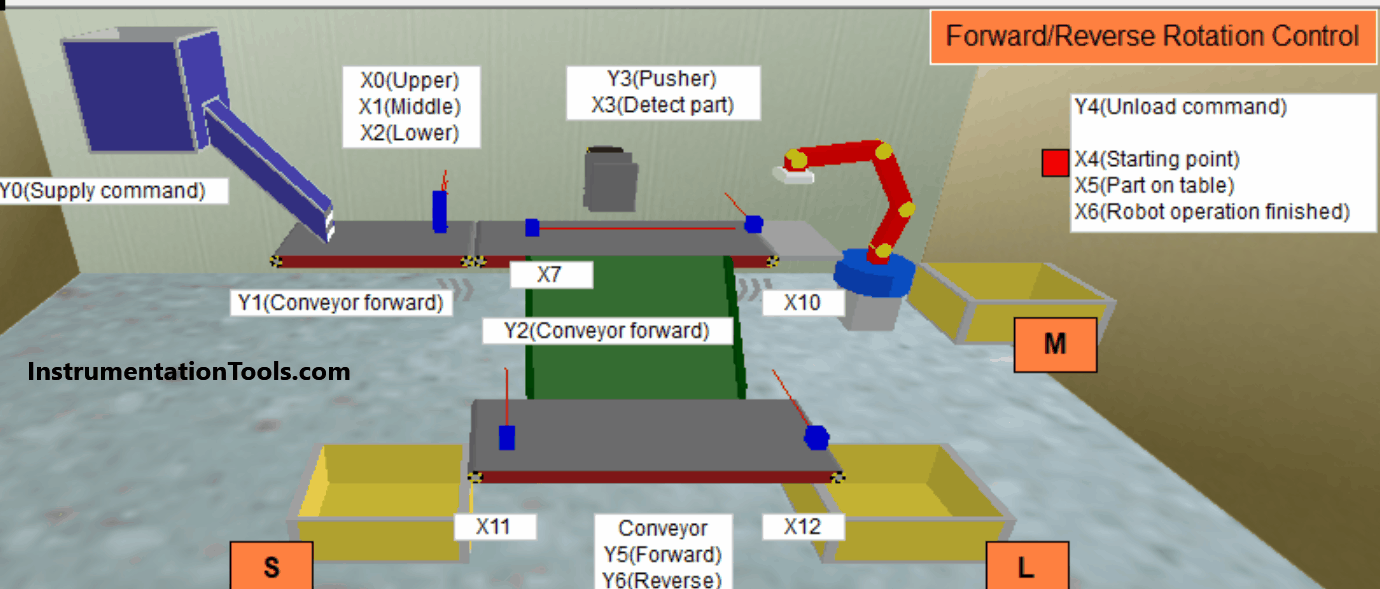
PLC Inputs and Outputs
The below table lists the inputs and outputs of this PLC project.
Type | Device No. | Device name | Operation |
Input | X0 | Upper | ON when the part is detected. |
Input | X1 | Middle | ON when the part is detected. |
Input | X2 | Lower | ON when the robot is at starting point. |
Input | X3 | Detect part | ON when the part is detected in front of the pusher. |
Input | X4 | Starting point | The conveyor moves forward when Y1 is ON. |
Input | X5 | Part on table | ON when the part is on the table. |
Input | X6 | Robot operation finished | ON when the part is detected on the incline. |
Input | X7 | Sensor | ON when the part is detected at the right end. |
Input | X10 | Sensor | ON when the part is detected at the left end. |
Input | X11 | Sensor | ON when the part is detected at the right end. |
Input | X12 | Sensor | ON when the robot operation is finished. |
Output | Y0 | Supply command | One part is supplied when Y0 is ON: Wooden part repeats in order L, M, S, M, S, L. |
Output | Y1 | Conveyor forward | The conveyor moves forward when Y2 is ON. |
Output | Y2 | Conveyor forward | Extends when Y3 is ON and retracts when Y3 is OFF. The pusher cannot be stopped in the mid-stroke. |
Output | Y3 | Pusher | The robot moves part to tray when Y4 is ON. A process cycle begins. |
Output | Y4 | Unload command | The conveyor moves forward when Y5 is ON. |
Output | Y5 | Conveyor forward | The conveyor moves backward when Y6 is ON. |
Output | Y6 | Conveyor reverse | Conveyor moves backward when Y6 is ON. |
Program Description
When the pushbutton PB1 (X20) on the control panel is pressed, it activates the Supply command (Y0) for the hopper. Once you release pushbutton PB1, the Supply command is deactivated. Whenever the Supply command is engaged, the robot dispenses a part.
When the switch SW1 (X24) on the control panel is activated, the conveyors start moving forward. As soon as you deactivate SW1, the conveyors halt.
The conveyors transport large, medium, and small parts, which are sorted by the Upper (X0), Middle (X1), and Lower (X2) sensors respectively, to designated trays.
- Large part: Directed to the lower conveyor and delivered to the tray on the right.
- Medium part: Transferred to the tray by the robot.
- Small part: Directed to the lower conveyor and delivered to the tray on the left.
When the Detect part sensor (X3) is activated, the conveyor stops, and a large or small part is directed to the lower conveyor.
Note: When the actuating command for the pusher is turned ON, it fully extends. When the actuating command is turned OFF, the pusher fully retracts.
When the Part on the table (X5) sensor in the robot is activated, the Unload command (Y4) is engaged. When the Robot operation is finished (X6) sensor is activated (it activates when a part is placed on the tray), and the Unload command (Y4) is deactivated.
As long as the switch SW2 (X25) on the control panel is ON, a new part is automatically supplied in the following scenarios:
- When the robot starts to handle a medium part
- When a small or large part is deposited into a tray
PLC Programming Conveyor Forward and Reverse Rotation Control
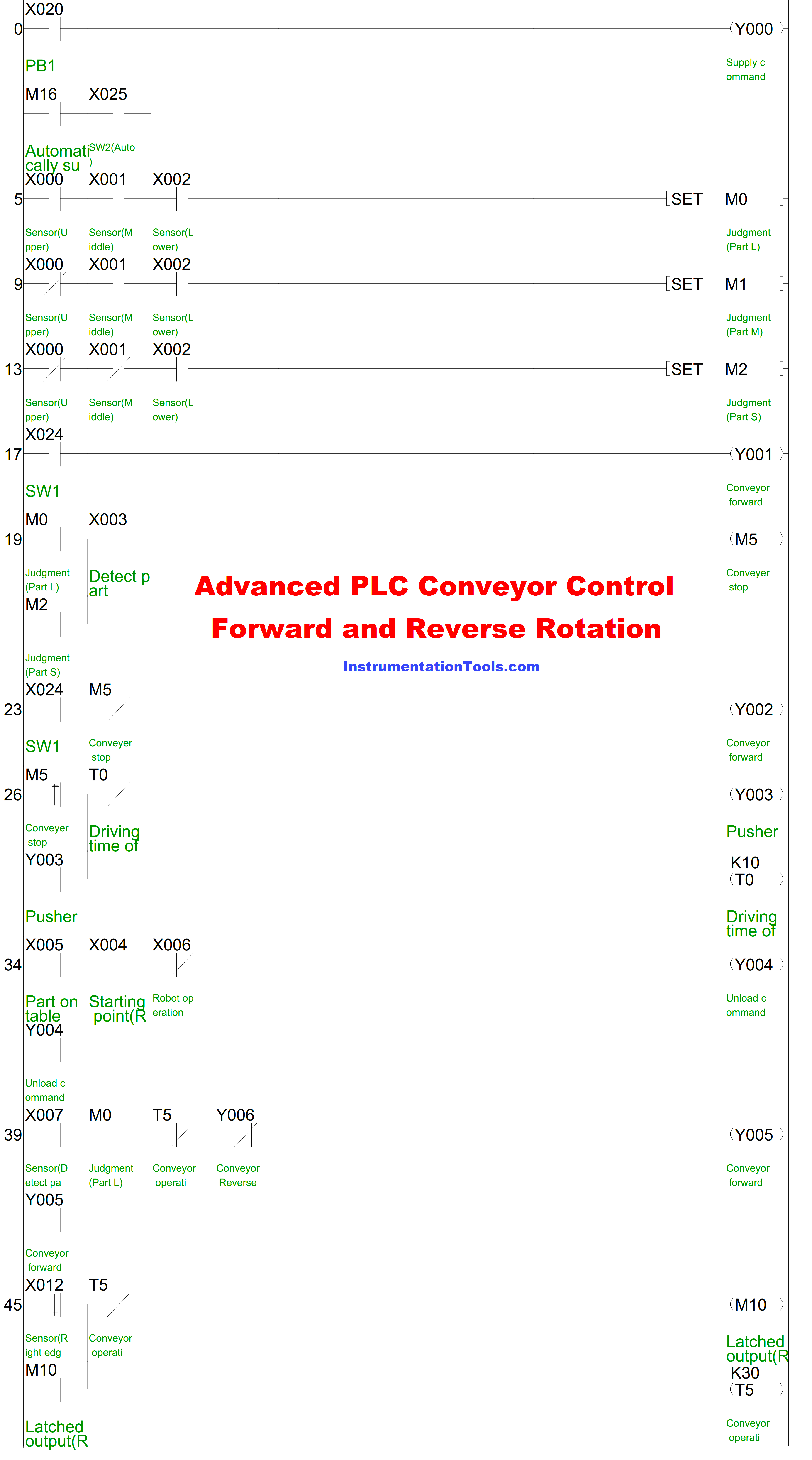
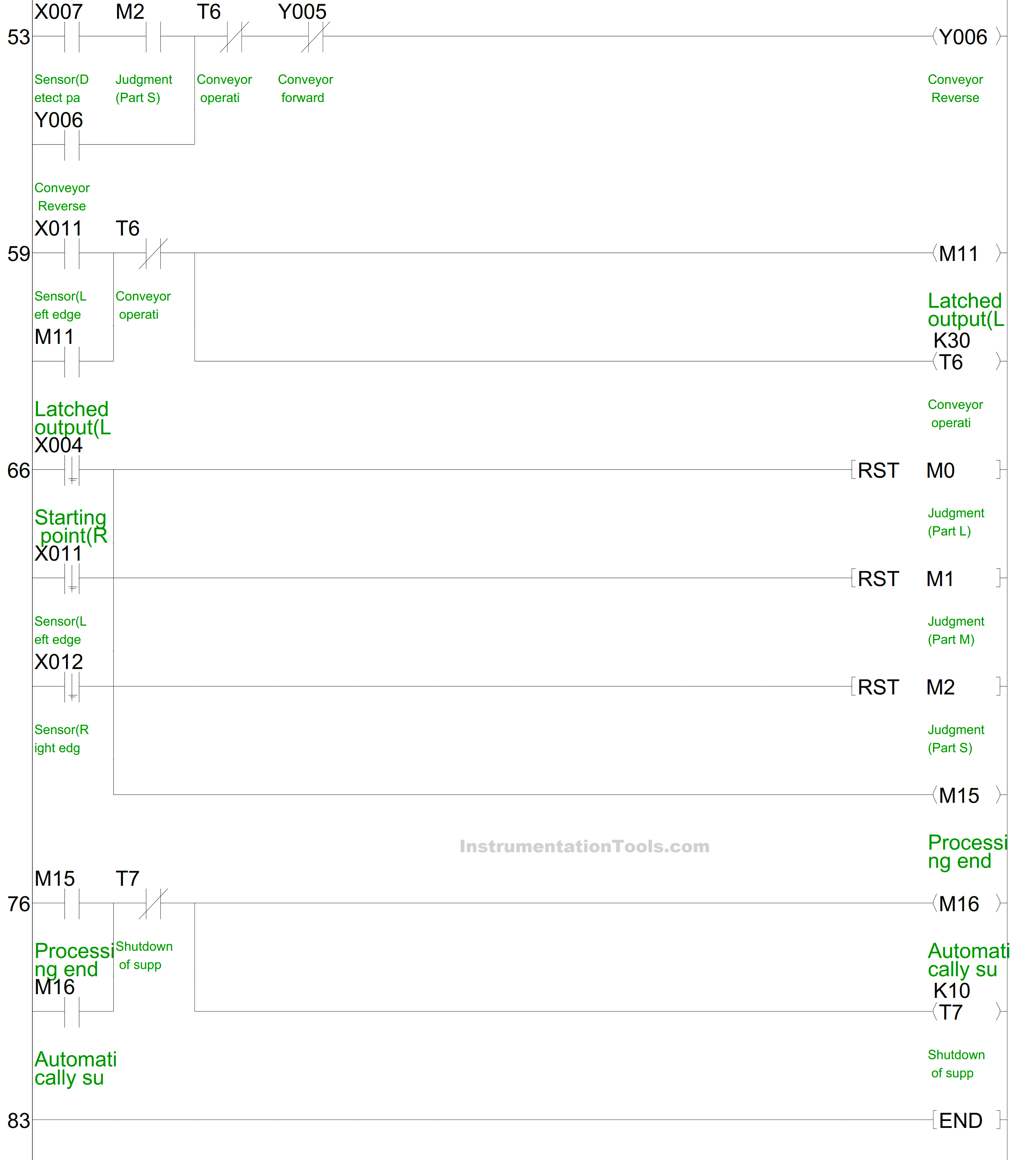
Source: Mitsubishi Electric
If you liked this article, then please subscribe to our YouTube Channel for Instrumentation, Electrical, PLC, and SCADA video tutorials.
You can also follow us on Facebook and Twitter to receive daily updates.
Read Next:
- Overview of SIEMENS PLC
- HMI and VFD Control System
- Sequential PLC Pneumatic Valves
- HMI Screen Design for Hazardous
- S7-1200 Hardware Configuration