Aluminum comes with immense uses, especially in the manufacturing sector. Its properties like machinability, high strength, and workability, and lightweight nature. No wonder it is counted among the top in most commonly used materials for machining.
The industries for example use the material; the automotive sector, etc. The statistics here show aluminum as the manufacturing material.
- The market size of the Aluminum manufacturing industry in Canada will increase 13.1% in 2021.
- m
- The industry in Canada is the 9th ranked manufacturing industry.
Here’s a look at the complete guide about aluminum machining in this article.
Aluminum as a Material and Properties
Aluminum is one of the best raw materials because of its fundamental properties.
Here are some of the properties that make aluminum an ideal fit for machining:
- It carries high strength and less density. Thus making it easier for the machine shop owners.
- Since aluminum is corrosion-resistant. Therefore it is ideal for creating parts for the marine industry.
- Aluminum retains all its main properties. These are ductility, softness, and strength even at the lowest temperatures.
- It offers the effective machinability required for CNC machining. Due to its soft nature, aluminum gets cut and requires less power to get machined.
- Aluminum as a material is recyclable.
Aluminum CNC Machining Process
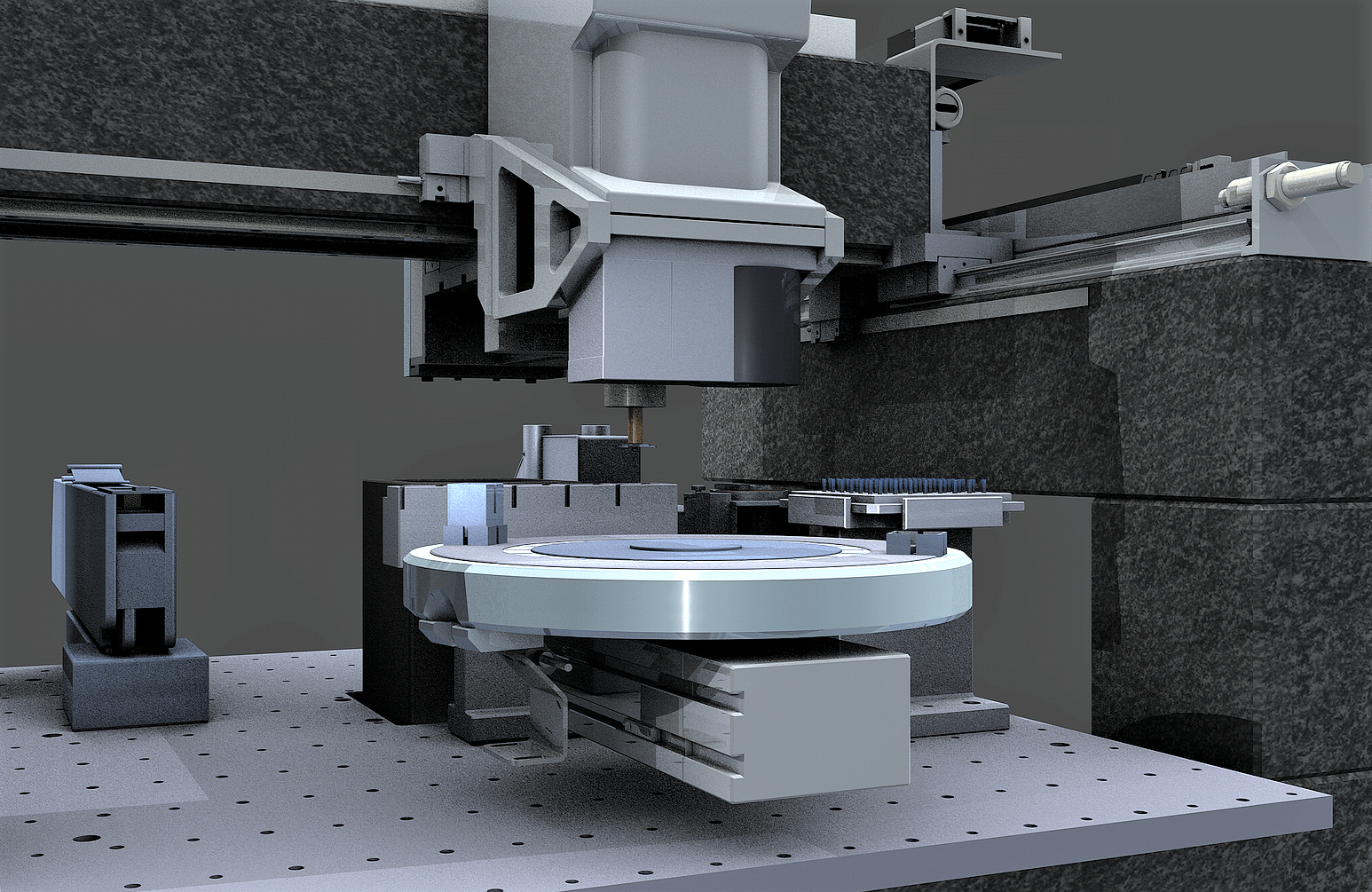
We can machine aluminum with machining processes available. Here are some of the processes are as follows:
Turning
The workpiece rotates while the single-point cutting tool remains stationary. It stays along its axis in CNC turning operations. The workpiece performs an outfeed motion thus removing the material.
Milling
In CNC machining aluminum, milling operations are common. A multi-point cutting gets rotated along its axis. While the workpiece remains ideal in these operations.
The feed motion with the cutting tool combined achieves cutting action as a result of material removal. Therefore, it uses many axes to carry out this motion.
Drilling
Making a hole in a workpiece gets referred to as drilling. A multi-point rotating cutting tool of specific size drills a hole in a straight line perpendicular to the surface to get drilled.
Facing
In face turning or face milling creates a flat cross-sectional area on the surface of a workpiece.
What are the Grades of Aluminum Machining?
The below are the common grades of aluminum machining.
Grade 2011
It is the most machinable of aluminum grades. The low corrosion resistance of this grade is a drawback.
Grade 2024
This grade fits the military and aerospace industries because of its mechanical properties. It includes high strength. The disadvantages are poor welding properties and low corrosion resistance.
Grade 6061
This grade has weldability and mechanical properties. Therefore it is ideal for the extrusion process. It is ideal for five-axis machining.
Grade 6063
Like 6061, but more seen in extrusions. It is not quite as stiff, though because of this, 6063 is a little more difficult to machine; it is softer.
Grade 5052
Because of its softness, it gets used in forming applications. Because of its excellent corrosion resistance, ideal for marine applications.
CNC Machined Aluminum Parts
Many parts and components made from CNC machined aluminum are an ideal fit for various services. In the engineering world, well-machined CNC aluminum parts are gaining popularity.
Some of the CNC machined aluminum parts are as follows:
- Front panels
- Dowels Pins
- EMI-Housings
- Spline Shafts
- Medical Devices
- Lighting Fixtures
Tool Factors to keep in mind for CNC Machining Aluminum
When it comes to creating custom machine parts, having the right tools is crucial. During the process of aluminum machining, a few tools are to consider for the desired machined equipment.
Flutes
Solid carbide end mills have 3 flutes 98 percent of the time. Therefore, three flutes provide the ideal balance of tool strength and chip clearance.
Using two flutes is an option for the machine shop owners as the cutting forces are lower. It is suitable when the tool is very long and prone to vibration.
As a result, three flutes are the industry standard for CNC machining aluminum.
Helix angle
The angle formed between the tool’s centerline and a straight line. It is tangent to the cutting edge resulting in the helix angle of the tool.
Standard end mills have lower helix angles than aluminum cutting tools. Thus, aluminum specialized helix angles are 35°, 40°, or 45°.
Clearance angle
In CNC machining aluminum for proper tool, the operation is clearance angle.
Therefore, the tool will dig if the angle is large however, a tiny angle will cause friction between the tool and the work.
Feeds and speeds
The faster the cutting speed, the softer the material gets machined. During the CNC aluminum machining, high spindle speed gets needed.
In fact, the tool will spend more time rubbing against the aluminum than cutting it. Therefore, it can increase the working temperature and reduce the tool life.
Carbide
As aluminum is soft cutting meaning the tool cannot have a hard impact on the surface. Additionally, the machine shop owners need to choose hardness over toughness.
In the case of aluminum machining, you need to maintain the edge sharpness. As a result, small grain size is best for the largest edge retention. The other factor is the binder ratio resulting in better CNC aluminum machining.
Industrial Applications of Aluminum CNC Machining
Some industries leverage aluminum CNC machining, therefore, making it easier to manufacture precision machined parts. Some of the sectors are as follows:
Aerospace industry
Those in the aerospace industry know the importance of precision machined parts.
While even a tiny error in the machined part leads to the loss of thousands of dollars resulting in precision machining.
CNC aluminum machining can make several components in the aerospace industry includes:
- Airfoils
- Landing gear parts
- Plane fittings
- Bushings
- Electrical connectors
Electrical industry
Consumer electronics are becoming smaller and powerful while remaining lightweight. The smaller the parts, the tighter is the tolerance.
CNC aluminum machined parts in the electronics industry are:
- Semiconductors
- Printed circuit boards
- Hardware components
- Metal slats
- Heat sinks
Medical industry
Precision machining is necessary in the medical industry as it is the case of life and death. Also, any machine part failure can increase the margin of error.
Thus, aluminum machining can meet and exceed these needs in various parts that include:
- Medical instruments
- Surgical implants
- MRI machines
- Research equipment
- Orthotic devices
Automotive industry
Aluminum can withstand the weight. This property comes in handy when manufacturing parts for wheels. Thus, it can take the pressure. Aluminum helps to achieve emission reduction, therefore resulting in energy saving.
Here are the areas where aluminum machined parts get used in the automotive industry:
- Interior panels
- Starter motors
- Drive axles
- Gearboxes
- Custom parts
In conclusion, these are the industries that take leverage of aluminum machining. Thus, it helps to produce precision high-volume machined parts in less time.
Author: Norm