Remote I/O and Distributed I/O are the two most common I/O architectures used in industrial automation and control systems.
Although often used interchangeably, these two systems follow distinctly different design philosophies and technological implementations.
In this article, learn what remote and distributed I/O systems are, how they differ, and when to use each to maximize efficiency, reliability, and scalability in industrial environments.
What Is Remote I/O?
Remote I/O (Input/Output) refers to a system configuration where I/O modules are located away from the central control unit (like a PLC – Programmable Logic Controller) but are still managed and controlled by it. These remote modules are typically connected via a single communication link, such as Ethernet/IP, PROFIBUS, or Modbus.
Remote I/O systems key characteristics and benefits:
- Control logic is centralized: All intelligence and decision-making always remain with the central PLC or controller.
- Focused on communications: The remote I/O acts as an extension of the central system, essentially providing extra input/output points.
- Simpler troubleshooting: Because both the logic and maintenance are often centralized, isolating issues and acting upon them is easier.Â
Example: In a packaging facility, the central PLC communicates with remote I/O stations positioned at various stages of the conveyor line. These stations are still dependent on the central PLC for all logic and decision-making based on their inputs.
What Is Distributed I/O?
Distributed I/O systems, in a nutshell, are more decentralized relative to Remote I/O’s centralization.
In distributed I/O setups, modulators are placed closer to field devices. Typically coming with their own processing power or microcontrollers, they can carry out tasks independently without the central controller. Typically, they are tasked with preprocessing data before relaying it to the central controller.
Distributed I/O systems key characteristics and benefits:
- Decentralized control: Each module can process independently with its own processing capabilities.
- Modularity and scalability: Can be easily expanded by simply adding more nodes.
- Faster response time: Since data can be pre-processed, minimal bottlenecks occur at the central controller, leading to decreased latency.
Use Case Example: In a smart manufacturing line using Industry 4.0 principles, distributed I/O nodes might independently monitor equipment health. They can then initiate local alarms by themselves, or even perform minor corrective actions, without waiting for instructions from a central system.
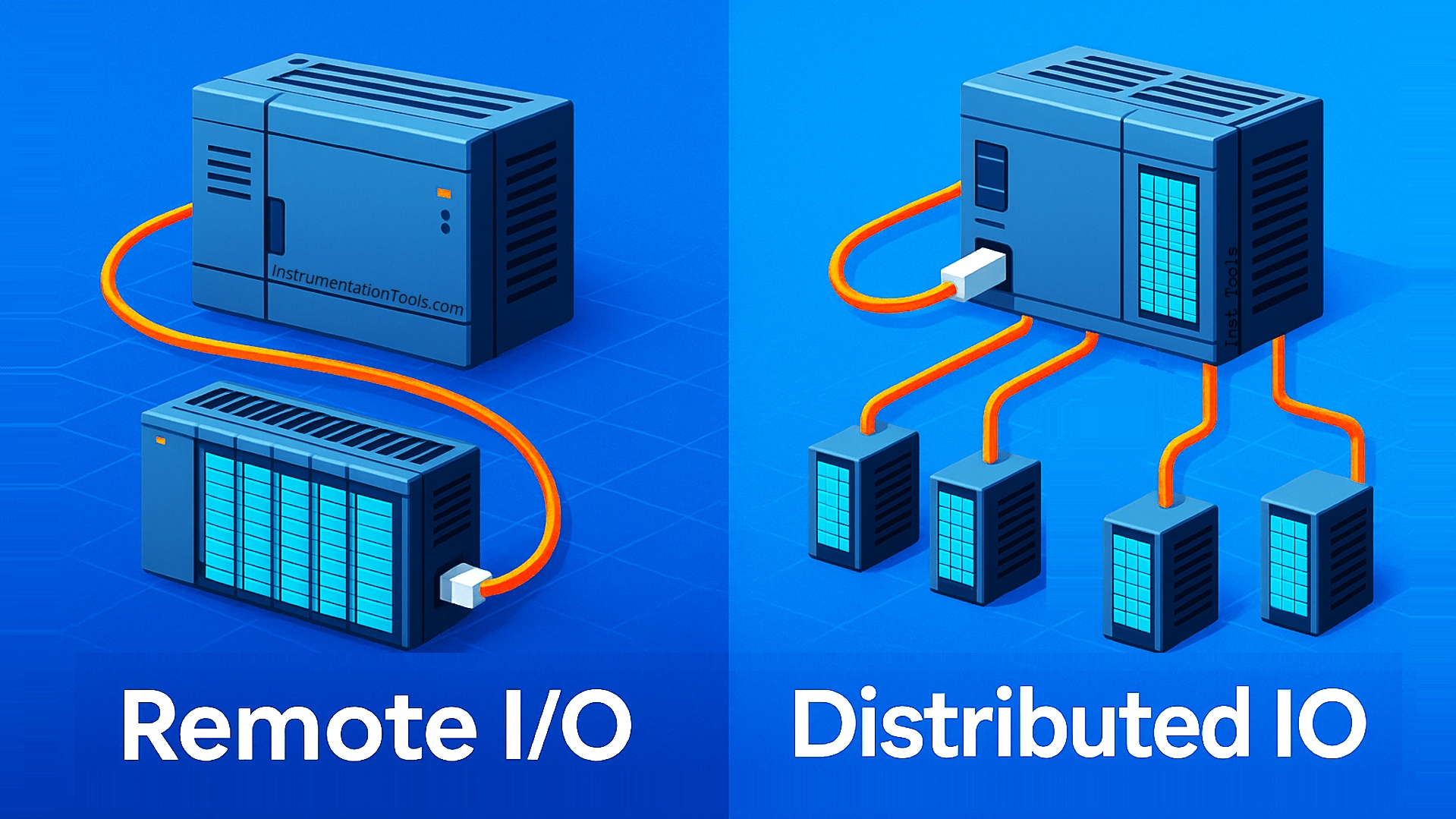
How the Architectures Differ: At a Glance
Understanding the differences between these two architectures is essential for choosing the right one for your application.Â
You may refer to the side-by-side comparison below for a summary of differences:
Feature | Remote I/O | Distributed I/O |
---|---|---|
Control Logic Location | Centralized in the PLC/controller | Decentralized or shared |
Processing Capability | Minimal to none at the I/O level | Smart I/O with local processing |
Communication Load | Higher network dependency | Reduced due to local decision-making |
Scalability | Moderate | High |
Fault Isolation | More difficult | Easier and localized |
Setup Complexity | Simpler to install and configure | More complex but flexible |
Why the Distinction Matters
Remote and distributed I/O systems can differ greatly in system performance, cost, and even future scalability.Â
Performance
With local control and data processing, distributed I/O systems tend to perform better with lower latency. This can be vital in fast-moving applications (such as robotic assembly lines).
Reliability and Maintenance
Distributed systems tend to be more resilient than remote systems, as a node failing does not affect the rest of the system. In remote I/O systems, the whole network also fails should the central PLC goes down.
Cost Considerations
With these benefits, however, come increased costs. Remote I/O is typically cheaper compared to distributed I/O. In fact, according to research, the market for distributed systems may reach $26.7 billion by 2028.
However, remote systems may be more costly in the long term due to lower reliability, performance bottlenecks, and scalability limits.Â
Learning When to Use Each System
Choose Remote I/O:
- For small to mid-sized installations.
- If centralized control logic is desired.
- On tighter budgets.Â
- If simplicity and ease of integration are important.
Choose Distributed I/O if:
- Fast local processing or high reliability are critical.
- The installation spans a large physical area.
- You need future-proof scalability.
- You aim to reduce network traffic and improve modularity.
Combining Both Approaches
In truth, modern industrial systems often use a hybrid of remote and distributed I/O based on use case. Â
In a factory, for example, distributed I/O might be used at critical control points (like robotic arms) and remote I/O for less demanding ones (like simple switches and sensors).Â
By knowing where to use distributed I/O systems and where to use remote I/O systems, companies can maximize their budgets and leverage the benefits of both.
Integration with Today’s Technologies
As industrial automation moves towards more advanced connectivity and data handling (edge computing, IoT, etc.), distributed I/O systems are becoming increasingly important.Â
More and more systems are prioritizing compatibility with things like smart sensors, cloud platforms, and secure communication protocols.
In some advanced control systems, such as those where remote diagnostics or configuration may be accessed over wireless or mobile networks, even consumer-level software is being used with these I/O systems. For example, VPNs like Surfshark for iOS or Windows allow remote diagnostics or configuration to be accessed over wireless or mobile networks.
Conclusion
Remote I/O systems and distributed I/O systems are two different I/O approaches, even if they may appear similar at a glance.Â
What’s better – remote I/O’s simplicity and cost-efficiency or distributed I/O’s performance and modularity – will depend highly on the needs of the system. And in fact, the smartest solution is often some hybrid of both.